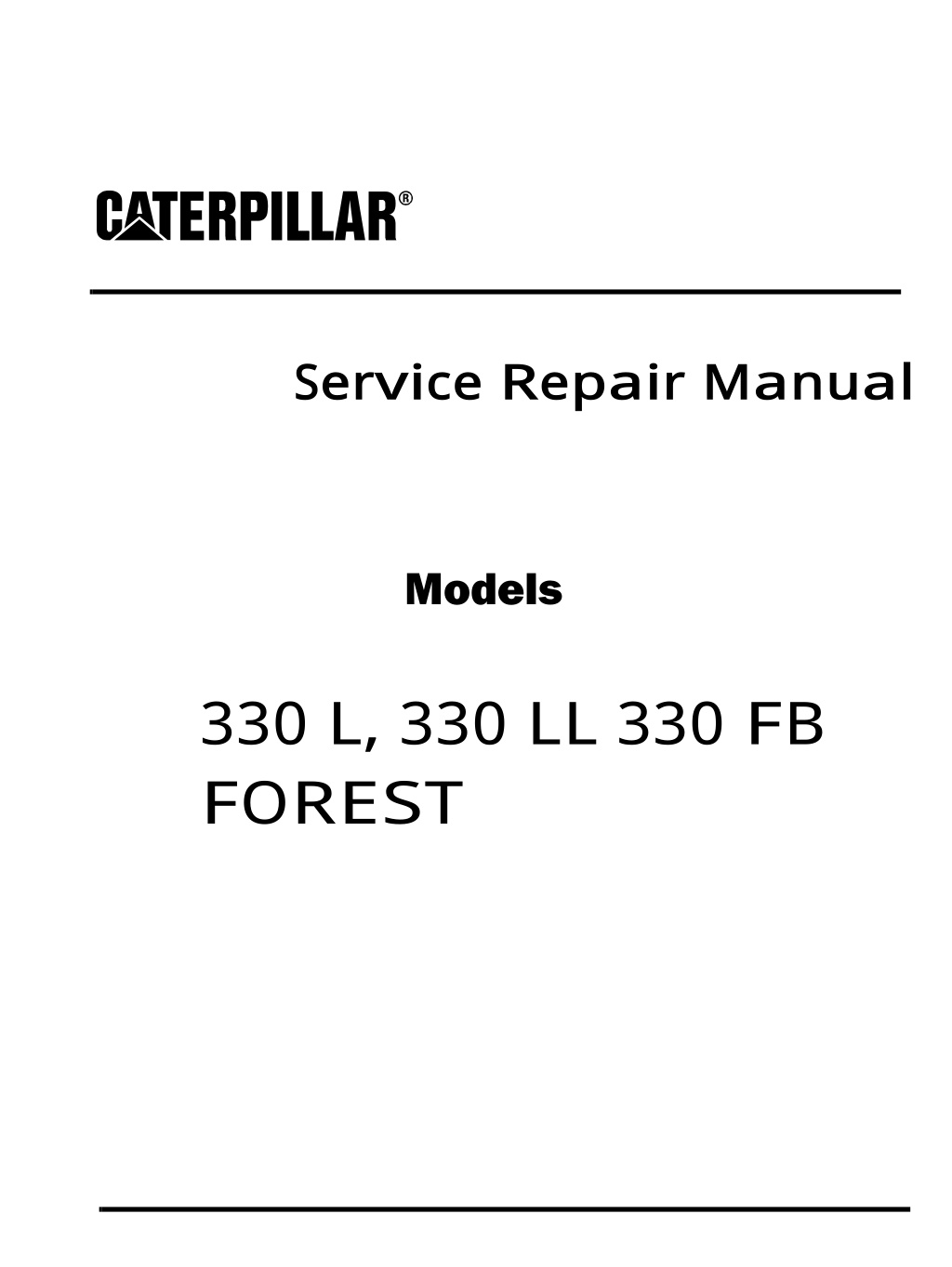
Caterpillar Cat 330 FB FOREST SWING MACHINES (Prefix 8FK) Service Repair Manual Instant Download
Please open the website below to get the complete manualnn//
Download Presentation

Please find below an Image/Link to download the presentation.
The content on the website is provided AS IS for your information and personal use only. It may not be sold, licensed, or shared on other websites without obtaining consent from the author. Download presentation by click this link. If you encounter any issues during the download, it is possible that the publisher has removed the file from their server.
E N D
Presentation Transcript
Service Repair Manual Models 330L, 330LL 330 FB FOREST
w 1/3(W) Shutdown SIS Previous Screen Product: EXCAVATOR Model: 330 L EXCAVATOR 8FK Configuration: 330 L, 330 LL & 330 FB FOREST SWING MACHINES 8FK00001-UP (MACHINE) Disassembly and Assembly 3304B and 3306B Engines for Caterpillar Built Machines Media Number -SENR5598-09 Publication Date -01/01/2013 Date Updated -25/01/2013 i01111802 Engine Balancer Shaft - Remove and Install SMCS - 1220-010-JF Removal Procedure Start By: A. Remove the front housing cover. Refer to Disassembly and Assembly, "Front Housing Cover - Remove". B. Remove the engine oil pump. Refer to Disassembly and Assembly, "Engine Oil Pump - Remove". NOTICE Keep all parts clean from contaminants. Contaminants may cause rapid wear and shortened component life. NOTICE Care must be taken to ensure that fluids are contained during performance of inspection, maintenance, testing, adjusting and repair of the product. Be prepared to collect the fluid with suitable containers before opening any compartment or disassembling any component containing fluids. Refer to Special Publication, NENG2500, "Caterpillar Tools and Shop Products Guide" for tools and supplies suitable to collect and contain fluids on Caterpillar products. https://127.0.0.1/sisweb/sisweb/techdoc/techdoc_print_page.jsp?returnurl=/sisweb/sis... 2020/10/17
w 2/3(W) Dispose of all fluids according to local regulations and mandates. Note: The oil pan plate has been removed for photo purposes only. Illustration 1 g00590442 1. Remove plates (2) that hold the balancer shaft in the cylinder block. 2. Remove balancer shafts (1) from the cylinder block. Installation Procedure Illustration 2 g00590449 NOTICE Keep all parts clean from contaminants. Contaminants may cause rapid wear and shortened component life. https://127.0.0.1/sisweb/sisweb/techdoc/techdoc_print_page.jsp?returnurl=/sisweb/sis... 2020/10/17
https://www.ebooklibonline.com Hello dear friend! Thank you very much for reading. Enter the link into your browser. The full manual is available for immediate download. https://www.ebooklibonline.com
w 3/3(W) 1. Install the balancer shafts in each side of the cylinder block. 2. Install plates (2) and the bolts that hold the balancer shafts in position in the cylinder block. Note: Ensure that the balancer shafts are in time before the oil pump is installed. End By: a. Install the engine oil pump. Refer to Disassembly and Assembly, "Engine Oil Pump - Install". b. Install the front housing cover. Refer to Disassembly and Assembly, "Front Housing Cover - Install". Copyright 1993 - 2020 Caterpillar Inc. Sat Oct 17 00:05:33 UTC+0800 2020 All Rights Reserved. Private Network For SIS Licensees. https://127.0.0.1/sisweb/sisweb/techdoc/techdoc_print_page.jsp?returnurl=/sisweb/sis... 2020/10/17
w 1/4(W) Shutdown SIS Previous Screen Product: EXCAVATOR Model: 330 L EXCAVATOR 8FK Configuration: 330 L, 330 LL & 330 FB FOREST SWING MACHINES 8FK00001-UP (MACHINE) Disassembly and Assembly 3304B and 3306B Engines for Caterpillar Built Machines Media Number -SENR5598-09 Publication Date -01/01/2013 Date Updated -25/01/2013 i01135419 Engine Balancer Shaft Bearings - Remove and Install SMCS - 1220-010-BD Removal Procedure Table 1 Required Tools Tool Part Number Part Description Qty 8S-2241 Camshaft Bearing Tool Group 1 A 8H-0684 Ratchet Wrench 1 Start By: A. Remove the engine oil pan. Refer to Disassembly and Assembly, "Engine Oil Pan - Remove". B. Remove the balancer shaft. Refer toDisassembly and Assembly, "Balancer Shaft - Remove". C. Remove the flywheel housing. Refer to Disassembly and Assembly, "Flywheel Housing Remove" . NOTICE Keep all parts clean from contaminants. Contaminants may cause rapid wear and shortened component life. NOTICE https://127.0.0.1/sisweb/sisweb/techdoc/techdoc_print_page.jsp?returnurl=/sisweb/sis... 2020/10/17
w 2/4(W) Care must be taken to ensure that fluids are contained during performance of inspection, maintenance, testing, adjusting and repair of the product. Be prepared to collect the fluid with suitable containers before opening any compartment or disassembling any component containing fluids. Refer to Special Publication, NENG2500, "Caterpillar Tools and Shop Products Guide" for tools and supplies suitable to collect and contain fluids on Caterpillar products. Dispose of all fluids according to local regulations and mandates. Illustration 1 g00602186 Use Tool (A) to remove the six balancer shaft bearing. Pull the balancer shaft bearings toward the flywheel end of the engine. Installation Procedure Illustration 2 g00602186 https://127.0.0.1/sisweb/sisweb/techdoc/techdoc_print_page.jsp?returnurl=/sisweb/sis... 2020/10/17
w 3/4(W) Illustration 3 g00602205 (A) The front bearing depth is 0.8 0.5 mm (0.03 0.02 inch). (B) The center bearing depth is 290.6 0.5 mm (11.44 0.02 inch). (C) The rear bearing depth is 601.0 0.5 mm (23.66 0.02 inch). NOTICE Keep all parts clean from contaminants. Contaminants may cause rapid wear and shortened component life. NOTICE Care must be taken to ensure that fluids are contained during performance of inspection, maintenance, testing, adjusting and repair of the product. Be prepared to collect the fluid with suitable containers before opening any compartment or disassembling any component containing fluids. Refer to Special Publication, NENG2500, "Caterpillar Tools and Shop Products Guide" for tools and supplies suitable to collect and contain fluids on Caterpillar products. Dispose of all fluids according to local regulations and mandates. https://127.0.0.1/sisweb/sisweb/techdoc/techdoc_print_page.jsp?returnurl=/sisweb/sis... 2020/10/17
w 4/4(W) 1. Install the balancer shaft front bearing with Tool (A). Ensure that the holes in the bearings are aligned with the holes in the cylinder block. The bearing must be 0.8 0.5 mm (0.03 0.02 inch) inside the front face of the cylinder block after installation. 2. Install the balancer shaft center bearing with Tool (A). Ensure that the holes in the bearings are aligned with the holes in the cylinder block. The bearing must be 290.6 0.5 mm (11.44 0.02 inch) inside the front face of the cylinder block after installation. 3. Install the balancer shaft rear bearing with Tool (A). Ensure that the holes in the bearings are aligned with the holes in the cylinder block. The bearing must be 601.0 0.5 mm (23.66 0.02 inch) inside the front face of the cylinder block after installation. 4. Check the bore of the bearings. The balancer shaft bearing bore must be 53.05 0.06 mm (2.089 0.002 inch) after installation. End By: a. Install the flywheel housing. Refer to Disassembly and Assembly, "Flywheel Housing - Install" . b. Install the balancer shaft. Refer to Disassembly and Assembly, "Balancer Shaft - Remove and Install". c. Install the engine oil pan. Refer to Disassembly and Assembly, "Engine Oil Pan - Remove and Install". Copyright 1993 - 2020 Caterpillar Inc. Sat Oct 17 00:06:29 UTC+0800 2020 All Rights Reserved. Private Network For SIS Licensees. https://127.0.0.1/sisweb/sisweb/techdoc/techdoc_print_page.jsp?returnurl=/sisweb/sis... 2020/10/17
w 1/2(W) Shutdown SIS Previous Screen Product: EXCAVATOR Model: 330 L EXCAVATOR 8FK Configuration: 330 L, 330 LL & 330 FB FOREST SWING MACHINES 8FK00001-UP (MACHINE) Disassembly and Assembly 3304B and 3306B Engines for Caterpillar Built Machines Media Number -SENR5598-09 Publication Date -01/01/2013 Date Updated -25/01/2013 i00912474 Cylinder Liner - Remove SMCS - 1216-011 Removal Procedure Table 1 Required Tools Tool Part Number Part Description Qty 8T-0812 Cylinder Liner Puller 1 A 1U-6317 Bridge 1 1U-6319 Socket 1 Start By: A. Remove the spacer plate. Refer to Disassembly and Assembly, "Spacer Plate - Remove and Install". B. Remove the engine oil pump. Refer to Disassembly and Assembly, "Engine Oil Pump - Remove". NOTICE Keep all parts clean from contaminants. Contaminants may cause rapid wear and shortened component life. https://127.0.0.1/sisweb/sisweb/techdoc/techdoc_print_page.jsp?returnurl=/sisweb/sis... 2020/10/17
w 2/2(W) Illustration 1 g00474523 1. Turn the crankshaft until two of the pistons are at the bottom center. Remove two connecting rod cap bolts (2) from each rod. Remove connecting rod caps (4) . 2. Tap connecting rod (3) away from the crankshaft with a soft hammer. Remove bearing half (1) . Illustration 2 g00474623 3. Use tool (A) to remove cylinder liners (5) . 4. Remove the pistons and connecting rods from the cylinder liners. Copyright 1993 - 2020 Caterpillar Inc. Sat Oct 17 00:07:24 UTC+0800 2020 All Rights Reserved. Private Network For SIS Licensees. https://127.0.0.1/sisweb/sisweb/techdoc/techdoc_print_page.jsp?returnurl=/sisweb/sis... 2020/10/17
w 1/5(W) Shutdown SIS Previous Screen Product: EXCAVATOR Model: 330 L EXCAVATOR 8FK Configuration: 330 L, 330 LL & 330 FB FOREST SWING MACHINES 8FK00001-UP (MACHINE) Disassembly and Assembly 3304B and 3306B Engines for Caterpillar Built Machines Media Number -SENR5598-09 Publication Date -01/01/2013 Date Updated -25/01/2013 i01048841 Cylinder Liner - Install SMCS - 1216-012 Installation Procedure Table 1 Required Tools Tool Part Number Part Description Qty A 8T-0455 Liner Projection Tool 1 B 2P-8260 Cylinder Liner Installation Tool 1 Note: The following procedure alleviates the need for the crossbar to hold the cylinder liners during cylinder liner projection measurements. 1. Clean the cylinder liner flange and the cylinder block surface. Remove any nicks on the top of the cylinder block. 2. Install clean cylinder liners without the rubber seals or the filler band. Install a new spacer plate gasket and the clean spacer plate. Table 2 Required Components Item Part Part Quantity For One Cylinder Quantity For Six Cylinders Number Description 1 0S-1589 Bolt 6 36 2 2S-0736 Washer 6 36 3 8F-1484 Washer 6 36 4 7K-1977 Washer 6 36 https://127.0.0.1/sisweb/sisweb/techdoc/techdoc_print_page.jsp?returnurl=/sisweb/sis... 2020/10/17
w 2/5(W) Illustration 1 g00544054 3. Install the bolts and washers in the order that is shown in Illustration 1 in order to seat the cylinder liner in the block. Tighten bolts (1) evenly to a torque of 95 N m (70 lb ft). Illustration 2 g00544478 (5) Bolt (6) Dial Indicator (7) Gauge Body (8) Gauge https://127.0.0.1/sisweb/sisweb/techdoc/techdoc_print_page.jsp?returnurl=/sisweb/sis... 2020/10/17
w 3/5(W) 4. Loosen bolt (5) until dial indicator (6) can be moved. Place gauge body (7) and dial indicator (6) on the long side of gauge (8) . 5. Slide dial indicator (6) into position until the point contacts gauge (8). Slide dial indicator (6) until the needle of the dial indicator makes a quarter of a revolution clockwise. The needle should be in a vertical position. Tighten bolt (5) and zero dial indicator (6) . 6. Place gauge body (7) on the spacer plate with the dial indicator point on the cylinder liner flange. Read the dial indicator in order to find the amount of liner projection. Check the liner projection at four locations (every 90 degrees) around each cylinder liner. Table 3 Specifications Liner Projection 0.033 mm (.0013 inch) to 0.175 mm (.0069 inch) Maximum Variation in Each Cylinder 0.051 mm (.0020 inch) Maximum Average Variation Between Adjacent Cylinders 0.051 mm (.0020 inch) Maximum Variation Between All Cylinders 0.102 mm (.0040 inch) 7. If the cylinder liner projection is out of specification, rotate the cylinder liner in the bore and repeat the procedure. If the cylinder liner projection measurements are again out of specification, try installing the cylinder liner in a different cylinder bore to improve the measurements. Note: Do not exceed the maximum liner projection of 0.175 mm (0.0069 inch). Cracking in the flange of the cylinder liner results from excessive cylinder liner projection measurements. 8. If the maximum variation between cylinder liners is greater than the recommended specification, shims must be used in order to reach the correct specification. 9. When the cylinder liner projection for each cylinder liner is within the recommended specification, mark each cylinder liner for the proper location in the bore and remove the cylinder liners. 10. Lubricate the O-ring seals, the cylinder liner, and the upper filler band before installation. Note: If the lower O-ring seals are black in color, apply liquid soap on the lower O-ring seals and the cylinder block. Use clean engine oil on the upper filler band. Note: If the lower O-rings are brown in color, apply engine oil on the lower O-ring seals, the cylinder block, and the upper filler band. NOTICE https://127.0.0.1/sisweb/sisweb/techdoc/techdoc_print_page.jsp?returnurl=/sisweb/sis... 2020/10/17
w 4/5(W) Apply 5P-3975 Rubber Lubricant and/or clean engine oil immediately before assembly. If the 5P-3975 Rubber Lubricant or engine oil is applied too early, the filler bands and/or O-ring seals may swell and the filler bands and/or O-ring seals may be pinched under the cylinder liner during installation. Illustration 3 g00544889 11. Apply liquid soap on the bottom cylinder liner bore in the cylinder block. Apply liquid soap on the grooves of the cylinder liner and on O-ring seals (4). Install O-ring seals (4) on the cylinder liner. 12. Lubricate filler band (5) with clean engine oil and install filler band (5) on cylinder liner (6). Install cylinder liner (6) into the engine block immediately after you lubricate the cylinder liner. This helps to prevent swelling of the filler band. Illustration 4 g00478920 13. Ensure that the mark on the cylinder liner is in alignment with the mark on the cylinder block. Use Tool (B) to press each of the cylinder liners into position. End By: https://127.0.0.1/sisweb/sisweb/techdoc/techdoc_print_page.jsp?returnurl=/sisweb/sis... 2020/10/17
w 5/5(W) a. Install the Pistons and Connecting Rods. Refer to Disassembly and Assembly, "Pistons and Connecting Rods - Install". b. Install the cylinder head. Refer to Disassembly and Assembly, "Spacer Plate - Remove and Install". Copyright 1993 - 2020 Caterpillar Inc. Sat Oct 17 00:08:20 UTC+0800 2020 All Rights Reserved. Private Network For SIS Licensees. https://127.0.0.1/sisweb/sisweb/techdoc/techdoc_print_page.jsp?returnurl=/sisweb/sis... 2020/10/17
w 1/3(W) Shutdown SIS Previous Screen Product: EXCAVATOR Model: 330 L EXCAVATOR 8FK Configuration: 330 L, 330 LL & 330 FB FOREST SWING MACHINES 8FK00001-UP (MACHINE) Disassembly and Assembly 3304B and 3306B Engines for Caterpillar Built Machines Media Number -SENR5598-09 Publication Date -01/01/2013 Date Updated -25/01/2013 i01112806 Piston Cooling Jets - Remove and Install SMCS - 1331-010 Removal Procedure Start By: A. Remove the crankshaft. Refer to Disassembly and Assembly, "Crankshaft - Remove". NOTICE Keep all parts clean from contaminants. Contaminants may cause rapid wear and shortened component life. Illustration 1 g00473474 https://127.0.0.1/sisweb/sisweb/techdoc/techdoc_print_page.jsp?returnurl=/sisweb/sis... 2020/10/17
w 2/3(W) 1. Use a soft punch to remove piston cooling jet (1) from the cylinder block. Installation Procedure Table 1 Required Tools Tool Part Number Part Description Qty A 6V-7772 Driver 1 NOTICE Keep all parts clean from contaminants. Contaminants may cause rapid wear and shortened component life. Note: On the 3304B, the piston cooling jets are installed in the No. 2 and the No. 4 main bosses. On the 3306B, the No. 2 and the No. 6 bosses for the main bearings have two jets. The No. 3 and No. 5 bosses for the main bearings have one jet. A replacement is necessary if the jets are damaged. Normally, it will only be necessary to ensure that the jets are clean. Illustration 2 g00473474 1. Use Tool (A) to install piston cooling jet (1) with the small end first. Install the jets in the bosses for the main bearing until the jets are against the counterbore. 2. Ensure that the passage is open after piston cooling jet (1) is installed. End By: Install the crankshaft. Refer to Disassembly and Assembly, "Crankshaft - Install". Copyright 1993 - 2020 Caterpillar Inc. Sat Oct 17 00:09:16 UTC+0800 2020 All Rights Reserved. https://127.0.0.1/sisweb/sisweb/techdoc/techdoc_print_page.jsp?returnurl=/sisweb/sis... 2020/10/17
w 1/3(W) Shutdown SIS Previous Screen Product: EXCAVATOR Model: 330 L EXCAVATOR 8FK Configuration: 330 L, 330 LL & 330 FB FOREST SWING MACHINES 8FK00001-UP (MACHINE) Disassembly and Assembly 3304B and 3306B Engines for Caterpillar Built Machines Media Number -SENR5598-09 Publication Date -01/01/2013 Date Updated -25/01/2013 i00976049 Pistons and Connecting Rods - Remove SMCS - 1225-011 Removal Procedure Table 1 Required Tools Tool Part Number Part Description Qty A 8S-2269 Ridge Reamer 1 Start By: A. Remove the spacer plate. Refer to Disassembly and Assembly, "Spacer Plate - Remove and Install". B. Remove the engine oil pan plate. Refer to Disassembly and Assembly, "Engine Oil Pan Plate - Remove and Install". C. Remove the engine oil pump. Refer to Disassembly and Assembly, "Engine Oil Pump - Remove". NOTICE Keep all parts clean from contaminants. Contaminants may cause rapid wear and shortened component life. 1. Use Tool (A) to remove the liner wear ridge from the inner surface of the cylinder liner. https://127.0.0.1/sisweb/sisweb/techdoc/techdoc_print_page.jsp?returnurl=/sisweb/sis... 2020/10/17
w 2/3(W) Illustration 1 g00483120 2. Turn the crankshaft until two of the pistons are at the bottom center. Remove connecting rod nuts (1) from the connecting rod. Remove connecting rod cap (2). Put identification marks on the connecting rod and connecting rod cap. The identification marks must be on the bearing tab side for installation purposes. Illustration 2 g00483180 Illustration 3 g00496980 https://127.0.0.1/sisweb/sisweb/techdoc/techdoc_print_page.jsp?returnurl=/sisweb/sis... 2020/10/17
w 3/3(W) 3. After connecting rod cap (2) is removed, push connecting rod (3) away from the crankshaft until the piston rings are out of the cylinder liners. Remove piston (4) from the cylinder block. 4. Ensure that the connecting rod and the connecting rod cap are kept as a set. Put an identification mark on each piston in order to locate the piston in the cylinder block. 5. Repeat Steps 1 through 4 for the remaining piston and connecting rods. Copyright 1993 - 2020 Caterpillar Inc. Sat Oct 17 00:10:11 UTC+0800 2020 All Rights Reserved. Private Network For SIS Licensees. https://127.0.0.1/sisweb/sisweb/techdoc/techdoc_print_page.jsp?returnurl=/sisweb/sis... 2020/10/17
w 1/4(W) Shutdown SIS Previous Screen Product: EXCAVATOR Model: 330 L EXCAVATOR 8FK Configuration: 330 L, 330 LL & 330 FB FOREST SWING MACHINES 8FK00001-UP (MACHINE) Disassembly and Assembly 3304B and 3306B Engines for Caterpillar Built Machines Media Number -SENR5598-09 Publication Date -01/01/2013 Date Updated -25/01/2013 i00977166 Pistons and Connecting Rods - Disassemble SMCS - 1225-015 Disassembly Procedure Table 1 Required Tools Tool Part Number Part Description Qty A 7S-9470 Piston Ring Expander 1 5P-8639 Press Group 1 5P-8645 Adapter 1 6V-3029 Spacer 1 6V-2049 Adapter 1 B 1U-5230 Hand Hydraulic Pump 1 8F-0024 Hose 1 1P-2375 Connecting Coupler 1 1P-2376 Connecting Coupler 1 Start By: A. Remove the pistons and connecting rods. Refer to Disassembly and Assembly, "Pistons and Connecting Rods - Remove". NOTICE https://127.0.0.1/sisweb/sisweb/techdoc/techdoc_print_page.jsp?returnurl=/sisweb/sis... 2020/10/17
w 2/4(W) Keep all parts clean from contaminants. Contaminants may cause rapid wear and shortened component life. Illustration 1 g00484932 1. Remove the piston rings from the pistons with Tool (A) . Illustration 2 g00484980 2. Remove retaining ring (3), piston pin (1) and connecting rod (2) . 3. Remove the connecting rod bearing. 4. Heat the connecting rod in an oven to a temperature of 176 to 260 C (350 to 500 F). Do not use a direct flame to heat a connecting rod. https://127.0.0.1/sisweb/sisweb/techdoc/techdoc_print_page.jsp?returnurl=/sisweb/sis... 2020/10/17
w 3/4(W) Illustration 3 g00485038 Hot oil and hot components can cause personal injury. Do not allow hot oil or hot components to contact the skin. 5. Put 6V-3029 Spacer (11) into the base plate. Put the connecting rod on the base plate of Tool (B) . 6. Put the connecting rod piston pin bearing end in the center of the port assembly of Tool (B). Install pin (5) in the center of the bore for the connecting rod bearing. 7. Install 6V-2049 Adapter (9). Align the hole in the adapter with the hole in the base plate of Tool (B) . 8. Install clamp bar (10) and clamp pin (4) . Note: The old piston pin bearing is removed while the new piston pin bearing is installed. 9. Put the new piston pin bearing on the connecting rod. Install 5P-8645 Adapter (8) with the tapered end of the adapter toward the piston pin bearing. The piston pin bearing joint must be in alignment with the hole in 6V-2049 Adapter (9) and the base plate of Tool (B) . 10. Install adapter (7) from the press group on adapter (11) . 11. Use Tool (B) to push the new piston pin bearing (6) into the connecting rod. Press piston pin bearing (6) into position until adapter (8) makes contact with the connecting rod surface. 12. Remove the connecting rod and the old piston pin bearing from Tool (B) . 13. Check the piston pin bearing bore diameter after the bearing is installed. The correct inside diameter is 43.210 0.008 mm (1.7012 0.0003 inch). The clearance between the bearing and the piston pin must not be more than 0.08 mm (0.003 inch). Refer to Special Instruction, SMHS7295 for additional information on removing the piston pin bearings. Sat Oct 17 00:11:07 UTC+0800 2020 https://127.0.0.1/sisweb/sisweb/techdoc/techdoc_print_page.jsp?returnurl=/sisweb/sis... 2020/10/17
w 1/3(W) Shutdown SIS Previous Screen Product: EXCAVATOR Model: 330 L EXCAVATOR 8FK Configuration: 330 L, 330 LL & 330 FB FOREST SWING MACHINES 8FK00001-UP (MACHINE) Disassembly and Assembly 3304B and 3306B Engines for Caterpillar Built Machines Media Number -SENR5598-09 Publication Date -01/01/2013 Date Updated -25/01/2013 i00977179 Pistons and Connecting Rods - Assemble SMCS - 1225-016 Assembly Procedure Table 1 Required Tools Tool Part Number Part Description Qty A 7S-9470 Piston Ring Expander 1 NOTICE Keep all parts clean from contaminants. Contaminants may cause rapid wear and shortened component life. 1. Clean the grooves of the used pistons with an acceptable tool or 1U-8811 Cleaner . 2. Install the connecting rod bearings. Ensure that the tabs on the back side of the connecting rod bearings are in the tab grooves of the connecting rod and the connecting rod cap. https://127.0.0.1/sisweb/sisweb/techdoc/techdoc_print_page.jsp?returnurl=/sisweb/sis... 2020/10/17
Suggest: If the above button click is invalid. Please download this document first, and then click the above link to download the complete manual. Thank you so much for reading
w 2/3(W) Illustration 1 g00486509 3. Install connecting rod (2) into the piston. Ensure that bearing tab slot (3) and the identification marks are on the same side as the "V" mark on the top of the piston. 4. Lubricate piston pin (1) with clean engine oil and install piston pin (1) through the piston and connecting rod. Install retaining ring (4) on the end of the piston pin. Illustration 2 g00484932 5. Install the oil control ring on the piston with Tool (A) . Note: The spring ends of the oil control ring should be assembled 180 degrees from the ring end gap. The blue colored portion of the spring must be visible at the ring end gap. 6. Use Tool (A) to install the intermediate piston ring with the side marked "UP-2" toward the top of the piston. 7. Use Tool (A) to install the top piston ring with the side marked "UP-1" toward the top of the piston. Note: The gaps in the intermediate piston ring and the top piston ring should be separated by 120 degrees. End By: Install the pistons and connecting rods. Refer to Disassembly and Assembly, "Pistons and Connecting Rods - Install". https://127.0.0.1/sisweb/sisweb/techdoc/techdoc_print_page.jsp?returnurl=/sisweb/sis... 2020/10/17
https://www.ebooklibonline.com Hello dear friend! Thank you very much for reading. Enter the link into your browser. The full manual is available for immediate download. https://www.ebooklibonline.com