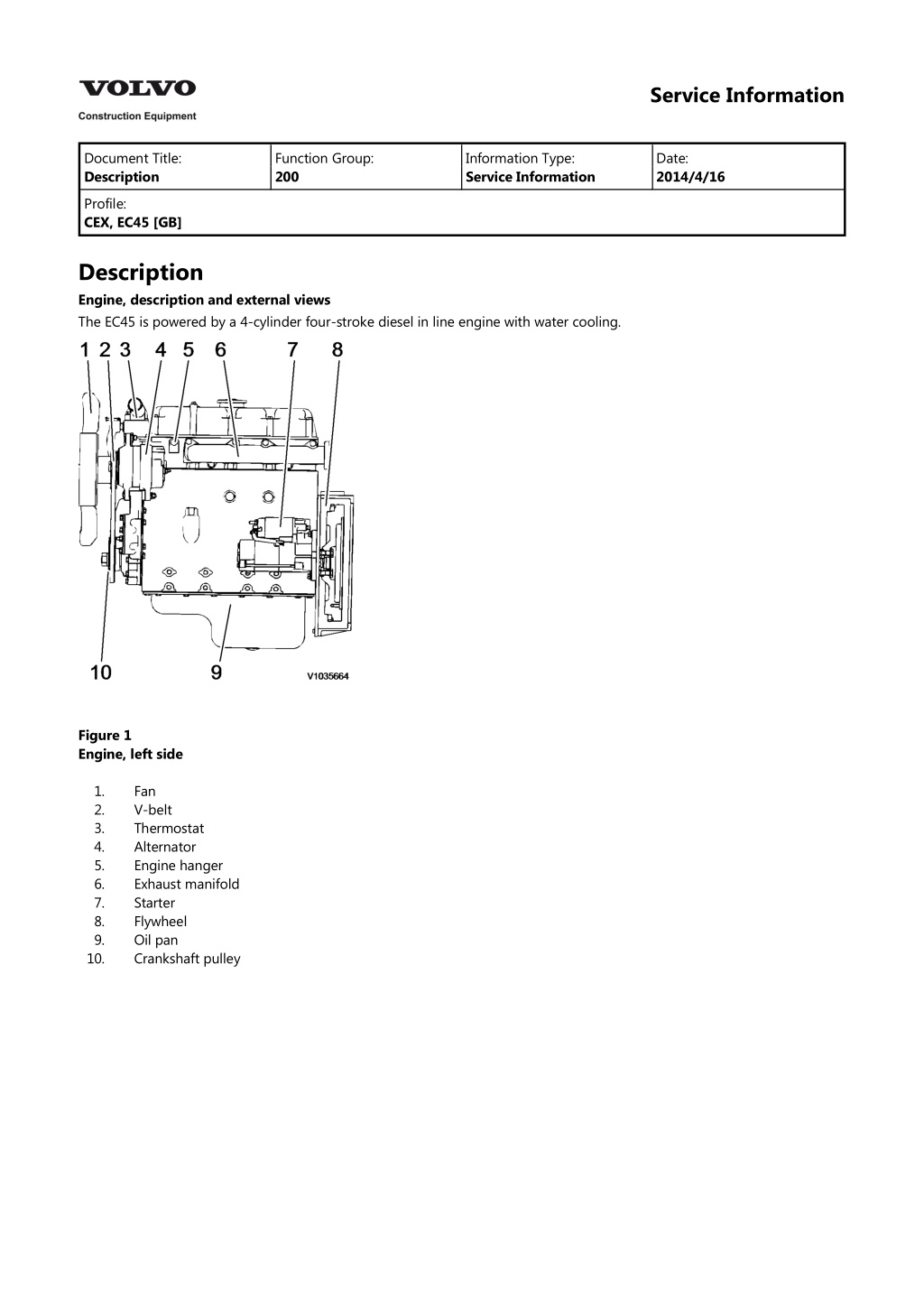
Volvo EC45 Compact Excavator Service Repair Manual Instant Download
Please open the website below to get the complete manualnn// n
Download Presentation

Please find below an Image/Link to download the presentation.
The content on the website is provided AS IS for your information and personal use only. It may not be sold, licensed, or shared on other websites without obtaining consent from the author. Download presentation by click this link. If you encounter any issues during the download, it is possible that the publisher has removed the file from their server.
E N D
Presentation Transcript
Service Information Document Title: Description Function Group: 200 Information Type: Service Information Date: 2014/4/16 Profile: CEX, EC45 [GB] Description Engine, description and external views The EC45 is powered by a 4-cylinder four-stroke diesel in line engine with water cooling. Figure 1 Engine, left side 1. 2. 3. 4. 5. 6. 7. 8. 9. Fan V-belt Thermostat Alternator Engine hanger Exhaust manifold Starter Flywheel Oil pan Crankshaft pulley 10.
Figure 2 Engine, right side 1. 2. 3. 4. 5. 6. 7. 8. 9. Fuel injection nozzle Fuel return Intake manifold Oil filler Oil filter Fuel inlet Injection pump Water pump Governor Oil drain plug Oil filter Disptick 10. 11. 12.
Service Information Document Title: Precautions Function Group: 200 Information Type: Service Information Date: 2014/4/16 Profile: CEX, EC45 [GB] Precautions Make preparation as follows before starting engine inspection and service. Fix the engine on a horizontal base. Remove the coolant hoses, fuel oil pipes, wire harness, control wires etc. connecting the driven machine and engine, and drain coolant, lubricating oil and fuel. Remove soil, oil, dust, etc. from the engine by washing with solvent, air, steam, etc. Carefully operate so as not to let any foreign matter enter the engine. Any part which is found defective as a result of inspection or any part whose measured value does not satisfy the standard or limit shall be replaced. Any part predicted to dissatisfy the standard or limit before the next service as estimated from the state of use should be replaced even when the measured value then satisfies the standard or limit.
https://www.ebooklibonline.com Hello dear friend! Thank you very much for reading. Enter the link into your browser. The full manual is available for immediate download. https://www.ebooklibonline.com
Service Information Document Title: Troubleshooting chart Function Group: 200 Information Type: Service Information Date: 2014/4/16 Profile: CEX, EC45 [GB] Troubleshooting chart The following table summarizes the general trouble symptoms and their causes. If any trouble symptom occurs, take corrective action before it develops into a serious problem so as not to shorten the engine service life. Engine troubleshooting chart Trouble symptoms Engine does not start Causes Improper clearance of inlet/exhaust valve Seizure of inlet/exhaust valve Seized or broken piston ring Worn piston ring, piston or cylinder Seized crankpin metal or bearing Foreign matter trapped in combustion chamber Improper open/close timing of intake/exhaust valves Improper properties of lubricating oil Water entrance in fuel system Clogged fuel filter Air entrance in fuel system Clogged or cracked fuel pipe Insufficient fuel supply to fuel injection pump Corrective actions Adjust the valve clearance Correct or replace Replace the piston ring Perform honing and use oversize parts Repair or replace Disassemble and repair Adjust the valve clearance Use proper lubricating oil Perform draining from the fuel filter Clean or replace Perform air bleeding Clean or replace Check the fuel tank cock, fuel tank, fuel pipe and fuel feed pump Disassemble and clean Priming failure (foreign matter trapped in the valve inside the priming pump) Starting motor defect Alternator defect Open circuit in wiring harness Battery voltage drop Improper clearance of inlet/exhaust valve Seized crankpin metal or bearing Improper arrangement of piston rings joint Defective governor Improper properties of lubricating oil Insufficient lubricating oil level Clogged fuel filter Air entrance in fuel system Clogged or cracked fuel pipe Insufficient fuel supply to fuel injection pump Repair or replace Repair or replace Repair Inspect and charge the battery Adjust the valve clearance Repair or replace Correct the ring joint positions Make adjustment Use proper lubricating oil Add proper lubricating oil Clean or replace Perform air bleeding Clean or replace Check the fuel tank cock, fuel tank, fuel pipe and fuel feed pump Correct or replace Replace the piston ring Perform honing and use oversize parts Perform draining from the fuel filter Engine starts, but stops soon. Exhaust smoke none. Engine starts, but stops soon. Exhaust smoke excessive. Seizure of inlet/exhaust valve Seized or broken piston ring Worn piston ring, piston or cylinder Water entrance in fuel system
Clogged air filter Improper clearance of inlet/exhaust valve Compression leakage from valve seat Seizure of inlet/exhaust valve Blowout from cylinder head gasket Worn crankpin and journal bearing Improper properties of lubricating oil Improper properties of fuel oil Clogged fuel filter Air entrance in fuel system Clogged or cracked fuel pipe Insufficient fuel supply to fuel injection pump Clean Adjust the valve clearance Lap the valve seat Correct or replace Replace the gasket Measure and replace Use proper lubricating oil Use proper fuel oil Clean or replace Perform air bleeding Clean or replace Check the fuel tank cock, fuel tank, fuel pipe and fuel feed pump Clean the strainer Replace the piston ring Perform honing and use oversize parts Correct the ring joint positions Reassemble correctly Measure and replace Adjust the valve clearance Insufficient engine output. Exhaust color : ordinary Clogged strainer at fuel feed pump inlet Seized or broken piston ring Worn piston ring, piston or cylinder Improper arrangement of piston rings joint Reverse assembly of piston ring Worn inlet/exhaust valve guide Improper open/close timing of intake/exhaust valves Timing of fuel injection pump too late Improper properties of fuel oil Water entrance in fuel system Uneven injection volume of fuel injection pump Poor spray pattern from fuel injection nozzle Compression leakage from valve seat Seizure of inlet/exhaust valve Improper open/close timing of intake/exhaust valves Insufficient cooling effect of radiator, Defective thermostat (kept opened) or slipping fan belt Insufficient coolant level Slackened fan belt Defective thermostat Timing of fuel injection pump too late Improper properties of fuel oil Uneven injection volume of fuel injection pump Poor spray pattern from fuel injection nozzle Clogged air filter Engine used at high temperature or at high altitude Clogged exhaust pipe Seized or broken piston ring Worn piston ring, piston or cylinder Reverse assembly of piston ring Improper open/close timing of intake/exhaust valves Excessive cooling effect of radiator, Insufficient engine output. (Exhaust color : white) Check and adjust Use proper fuel oil Perform draining from the fuel filter Check and adjust Check and adjust Lap the valve seat Correct or replace Adjust the valve clearance Insufficient engine output. (Exhaust color : black) Repair or replace thermostat and fan belt Check leakage from cooling system Adjust the belt tension Check or replace Check and adjust Use proper fuel oil Check and adjust Check and adjust Clean Study output drop and load matching Clean Replace the piston ring Perform honing and use oversize parts Reassemble correctly Adjust the valve clearance Poor exhaust color : white (During work) Repair or replace
Defective thermostat (kept closed) Defective thermostat Timing of fuel injection pump too early Timing of fuel injection pump too late Improper properties of fuel oil Water entrance in fuel system Uneven injection volume of fuel injection pump Poor spray pattern from fuel injection nozzle Compression leakage from valve seat Seizure of inlet/exhaust valve Improper open/close timing of intake/exhaust valves Timing of fuel injection pump too early Timing of fuel injection pump too late Improper properties of fuel oil Uneven injection volume of fuel injection pump Excessive fuel injection volume Poor spray pattern from fuel injection nozzle Clogged air filter Engine used at high temperature or at high altitude Clogged exhaust pipe Timing of fuel injection pump too early Check or replace Check and adjust Check and adjust Use proper fuel oil Perform draining from the fuel filter Check and adjust Check and adjust Lap the valve seat Correct or replace Adjust the valve clearance Poor exhaust color : black (During work) Check and adjust Check and adjust Use proper fuel oil Check and adjust Check and adjust Check and adjust Clean Study output drop and load matching Clean Check and adjust High knocking sound during compression Abnormal engine sound Improper clearance of inlet/exhaust valve Compression leakage from valve seat Seizure of inlet/exhaust valve Seized or broken piston ring Seized crankpin metal or bearing Worn crankpin and journal bearing Loosened connecting rod screw Foreign matter trapped in combustion chamber Excessive gear backlash Improper open/close timing of intake/exhaust valves Improper properties of fuel oil Water entrance in fuel system Uneven injection volume of fuel injection pump Poor spray pattern from fuel injection nozzle Clogged air filter Clogged exhaust pipe Seized or broken piston ring Seized crankpin metal or bearing Worn crankpin and journal bearing Defective governor Water entrance in fuel system Uneven injection volume of fuel injection pump Poor spray pattern from fuel injection nozzle Seizure of inlet/exhaust valve Adjust the valve clearance Lap the valve seat Correct or replace Replace the piston ring Repair or replace Measure and replace Tighten to specified torque Disassemble and repair Adjust gear and repair Adjust the valve clearance Uneven combustion sound Use proper fuel oil Perform draining from the fuel filter Check and adjust Check and adjust Clean Clean Replace the piston ring Repair or replace Measure and replace Make adjustment Perform draining from the fuel filter Check and adjust Check and adjust Correct or replace Hunting during idling Hunting during work
Seized crankpin metal or bearing Worn crankpin and journal bearing Defective governor Water entrance in fuel system Uneven injection volume of fuel injection pump Poor spray pattern from fuel injection nozzle Seizure of inlet/exhaust valve Seized or broken piston ring Seized crankpin metal or bearing Worn crankpin and journal bearing Loosened connecting rod screw Defective governor Timing of fuel injection pump too early Uneven injection volume of fuel injection pump Poor spray pattern from fuel injection nozzle Defective governor Repair or replace Measure and replace Make adjustment Perform draining from the fuel filter Check and adjust Check and adjust Correct or replace Replace the piston ring Repair or replace Measure and replace Tighten to specified torque Make adjustment Check and adjust Check and adjust Check and adjust Make adjustment Large engine vibration Difficulty in returning to low speed Excessive fuel consumption Compression leakage from valve seat Excessive cooling effect of radiator, Defective thermostat (kept closed) Timing of fuel injection pump too late Excessive fuel injection volume Poor spray pattern from fuel injection nozzle Engine used at high temperature or at high altitude Seized or broken piston ring Worn piston ring, piston or cylinder Improper arrangement of piston rings joint Reverse assembly of piston ring Foreign matter trapped in combustion chamber Worn inlet/exhaust valve guide Improper properties of lubricating oil Leakage from lubricating oil piping system Excessive fuel injection volume Seizure of inlet/exhaust valve Seized or broken piston ring Worn piston ring, piston or cylinder Blowout from cylinder head gasket Cracked water jacket Worn crankpin and journal bearing Loosened connecting rod screw Cracked water jacket Improper properties of lubricating oil Leakage from lubricating oil piping system Insufficient delivery capacity of trochoid pump Clogged lubricating oil filter Defective pressure regulating valve Insufficient lubricating oil level Compression leakage from valve seat Lap the valve seat Repair or replace Check and adjust Check and adjust Check and adjust Study output drop and load matching Excessive consumption lubricating oil Replace the piston ring Perform honing and use oversize parts Correct the ring joint positions Reassemble correctly Disassemble and repair Measure and replace Use proper lubricating oil Repair Check and adjust Correct or replace Replace the piston ring Perform honing and use oversize parts Replace the gasket Repair or replace Measure and replace Tighten to specified torque Repair or replace Use proper lubricating oil Repair Check and repair Clean or replace Check, adjust or replace Add proper lubricating oil Lap the valve seat Lubricating oil diluted by fuel Lubricating oil mixed with water Low lubricating oil pressure Excessive blow-by gas
Seizure of inlet/exhaust valve Seized or broken piston ring Worn piston ring, piston or cylinder Seized crankpin metal or bearing Improper arrangement of piston rings joint Reverse assembly of piston ring Foreign matter trapped in combustion chamber Worn inlet/exhaust valve guide Improper properties of lubricating oil Clogged lubricating oil filter Excessive fuel injection volume Blowout from cylinder head gasket Seized or broken piston ring Insufficient cooling effect of radiator, Defective thermostat (kept opened) or slipping fan belt Insufficient coolant level Cracked water jacket Slackened fan belt Defective thermostat Excessive fuel injection volume Engine used at high temperature or at high altitude Excessive cooling effect of radiator, Defective thermostat (kept closed) Defective thermostat Improper clearance of inlet/exhaust valve Compression leakage from valve seat Seizure of inlet/exhaust valve Clogged air filter Engine used at high temperature or at high altitude Excessive fuel injection volume Improper clearance of inlet/exhaust valve Compression leakage from valve seat Seized or broken piston ring Insufficient cooling effect of radiator, Defective thermostat (kept opened) or slipping fan belt Insufficient coolant level Slackened fan belt Timing of fuel injection pump too late Uneven injection volume of fuel injection pump Excessive fuel injection volume Clogged exhaust pipe Correct or replace Replace the piston ring Perform honing and use oversize parts Repair or replace Correct the ring joint positions Reassemble correctly Disassemble and repair Measure and replace Use proper lubricating oil Clean or replace Check and adjust Replace the gasket Replace the piston ring Repair or replace thermostat and fan belt Overheating of coolant Check leakage from cooling system Repair or replace Adjust the belt tension Check or replace Check and adjust Study output drop and load matching Low coolant temperature Repair or replace Check or replace Adjust the valve clearance Lap the valve seat Correct or replace Clean Study output drop and load matching Air inlet pressure drop Air inlet pressure rise Exhaust temperature rise Check and adjust Adjust the valve clearance Lap the valve seat Replace the piston ring Repair or replace thermostat and fan belt Check leakage from cooling system Adjust the belt tension Check and adjust Check and adjust Check and adjust Clean
Service Information Document Title: Engine trouble shooting Function Group: 210 Information Type: Service Information Date: 2014/4/16 Profile: CEX, EC45 [GB] Engine trouble shooting Engine faults must be detected and rectified as quickly as possible in order to avoid more expensive repairs. The following table summarizes the most important faults and their rectification. Problem/fault Engine does not start Possible cause of fault Starter switch defective Starter power too low Fault remedy Tighten connections. Replace the switch. If the starter is OK, check condition of battery and electric connections. Bleed the system. Replace the air filter. Check viscosity and fill in correct oil. Check the function of the preheater plug. Check and adjust the injection valves Replace defective valves. Adjust the injection timing. Check the valve clearance. Check condition of cylinder head gasket, valves and piston rings. Fill in fuel. Bleed the fuel system. Clean or replace the fuel filter. Check connection of fuel pump or replace fuel pump. Clear or replace the exhaust system. Replace the pump. Clean or replace the fuel filter. Bleed the fuel system. Clean the air filter. Check the intake air. Check and adjust the injection valves Replace defective valves. Check elements (water pump, radiator, thermostat, cylinder head gasket, coolant hoses). Check presence, tension and cleanliness of V-belt. Check elements (oil filter, oil pump, suction filter) and replace defective parts. Adjust the injection timing. Check the valve clearance. Fill in oil. Check whether the oil in the engine meets the operating conditions. Adjust the governor. Correct the coolant level. Check whether the coolant meets the operating conditions. Clean or replace the air filter. Check quality of fuel and suitability for climatic Air in fuel system Air filter dirty Wrong oil viscosity Engine too cold Injection valves defective Incorrect injection timing Compression pressure too low Engine shuts down automatically Fuel tank empty Air in fuel system Fuel filter dirty Fuel pump defective Exhaust system clogged Fuel pump defective Fuel filter dirty Erratic running of engine Air filter dirty Injection valves defective Engine overheating Cooling system elements defective Fan not running Lubrication system elements defective Engine overheating Incorrect injection timing Oil level too low Governor incorrectly adjusted Coolant level not correct Engine black smoke develops Air cleaner soiled Poor fuel quality
conditions. Adjust valve clearance and injection timing. Valve clearance and injection timing not correct Compression pressure not O.K. Check condition of cylinder head gasket, valves and piston rings. Check and adjust the injection valves Check injection pump, replace if necessary. Adjust the control cable. Fill in oil as required for the operating conditions. Check quality of fuel and suitability for climatic conditions. Adjust valve clearance and injection timing. Injection pressure not O.K. Injection pump defective Engine control cable incorrectly adjusted Poor engine oil quality Poor fuel quality Irregular idle speed Valve clearance and injection timing not correct Opening pressure of injection valves not correct Compression pressure not O.K. Check opening pressure and injection valves. Check condition of cylinder head gasket, valves and piston rings. Check injection pump, replace if necessary. Check quality of fuel and suitability for climatic conditions. Clean or replace the air filter. Adjust the injection timing. Check the engine shut-down solenoid. Adjust the injection valves. Check condition of cylinder head gasket, valves and piston rings. Replace the injection pump. Check oil level and oil quality and fill in specified oil. Check and replace the oil pressure switch. Tighten the V-belt or replace, if defective. Check and replace the generator. Replace the battery. Check correct connection of cables. Check regulator, replace if necessary. Tighten connections. Replace the switch. Check engine shut-down solenoid, replace if necessary. Injection pump defective Poor fuel quality Unusual noise engine Air cleaner soiled Incorrect injection timing Engine shut-down solenoid not O.K. Injection pressure not O.K. Compression pressure not O.K. Injection pump defective Oil level and oil quality not correct Oil low pressure too Oil pressure switch defective Fan V-belt too loose Generator defective Battery defective Wiring not O.K. Regulator defective Starter switch defective Engine shut-down solenoid not O.K. Battery condition too low charge Engine cannot be shut down
Service Information Document Title: Compression inspection Function Group: Information Type: Service Information Date: 2014/4/16 pressure Profile: CEX, EC45 [GB] Compression pressure inspection Compression pressure drop is one of major causes of increasing blow-by gas (lubricating oil contamination or increased lubricating oil consumption as a resultant phenomenon) or starting failure. The compression pressure is affected by the following factors: 1. 2. 3. Degree of clearance between piston and cylinder Degree of clearance at intake/exhaust valve seat Gas leak from nozzle gasket or cylinder head gasket In other words, the pressure drops due to increased parts wear and reduced durability resulting from long use of the engine. A pressure drop may also be caused by scratched cylinder or piston by dust entrance from the dirty air cleaner element or worn or broken piston ring. Measure the compression pressure to diagnose presence of any abnormality in the engine. Compression pressure measurement method Figure 1 Measurement, compression pressure 1. Compression gauge 1. 2. After warming up the engine, remove the fuel injection nozzle from the cylinder to be measured. Crank the engine before installing the compression gauge adapter. Perform cranking with the stop handle at the stop position (no injection state). 3. Install the compression gauge and compression gauge adapter at the cylinder to be measured. NOTE! Do not forget to install a gasket at the tip end of the adapter. 4. Crank the engine by the starting motor until the compression gage reading is stabilized. Standard compression pressure Standard: 30 kgf/cm2 (427 psi) Limit: 26 kgf/cm2 (370 psi) Dispersion among cylinders: 3 kgf/cm2 (43 psi)
Service Information Document Title: Valves, adjusting Function Group: Information Type: Service Information Date: 2014/4/16 Profile: CEX, EC45 [GB] Valves, adjusting Adjusting the valves Figure 1 Op nbr 21412 NOTE! Clean the area around the rocker cover before starting adjustment work. 1. Pull off the hose for crankcase ventilation. 2. Remove the cylinder head cover. 3. Crank the engine until the valves are overlapping. NOTE! Overlapping of valves means: Exhaust valve not yet closed, intake valve starts to open. In this situation the push rods cannot be turned.
Figure 2 4. Adjust the valve clearance on the respective cylinder using a feeler gauge. 5. Tighten the counter nut. Check the adjustment again with the feeler gauge. 6. Attach the gasket to the rocker cover. 7. Install the rocker cover. Tighten the screws with a torque of 11.3 Nm. 8. Push on the crankcase ventilation hose. Intake: 0.25 mm (0.01 in) Exhaust: 0.25 mm (0.01 in) Valve clearance values
Service Information Document Title: Lubricating description Function Group: 220 Information Type: Service Information Date: 2014/4/16 system, Profile: CEX, EC45 [GB] Lubricating system, description The oil pump delivers pressurized engine oil to lubricate the contact faces of moving parts, such as crankshaft, camshaft, intake/exhaust valves, rockers and engine timing gears. Schematic flow of lubrication oil Figure 1 1. 2. 3. 4. 5. 6. 7. Drain plug Oil screen Dipstick Oil pump Check valve Oil filter Oil pressure switch
8. 9. Rocker shaft Rocker arm Oil filler cap Camshaft Oil pan 10. 11. 12.
Service Information Document Title: Removing the oil filter Function Group: 222 Information Type: Service Information Date: 2014/4/16 Profile: CEX, EC45 [GB] Removing the oil filter Op nbr 22202 Filter wrench Figure 1 Remove oil filter 1. 2. 3. Oil filter Pressure switch Oil pump 1. Place a bowl under the oil filter to catch running out oil. 2. Unscrew the oil filter from the engine block using the filter wrench.
Service Information Document Title: Installing the oil filter Function Group: 222 Information Type: Service Information Date: 2014/4/16 Profile: CEX, EC45 [GB] Installing the oil filter Op nbr 22202 Figure 1 1. Slightly oil the seal on the new oil filter with engine oil. 2. Screw on the new filter cartridge by hand. When the seal touches the contact face turn further for another 1/2 of a turn. 3. Fill in 0.5 litres of oil. 4. Start the engine and check for leaks in the vicinity of the filter. 5. Shut the engine down. Check the oil level, fill up oil if necessary.
Service Information Document Title: Removing the oil pressure switch Function Group: 222 Information Type: Service Information Date: 2014/4/16 Profile: CEX, EC45 [GB] Removing the oil pressure switch Oil pressure switch Op nbr 22205 Socket wrench for oil pressure switch 1. Unscrew oil pressure switch using a socket wrench for oil pressure switch. Figure 1 remove oil pressure switch 1. 2. 3. Oil filter Pressure switch Oil pump Oil pressure test Op nbr Ohmmeter 1. Check the current flow between terminal and housing with an ohmmeter, as shown in the illustration. If this current flow is not assured replace the pressure switch.
Figure 2 Oil pressure test 2. Insert a small diameter rod into the oil bore of the pressure switch and push slightly in to check, whether current flow is applied (see illustration). If this is the case, replace the pressure switch. Figure 3 Oil pressure test 3. Blow with compressed air of 0.5 bar into the oil bore (arrow) to check whether current flow is present. If this is the case, replace the pressure switch. Check the switch also for air leaks. An air leak may be caused by a broken orifice. In this case the oil pressure switch must also be replaced.
Suggest: If the above button click is invalid. Please download this document first, and then click the above link to download the complete manual. Thank you so much for reading
Service Information Document Title: Installing the oil pressure switch Function Group: 222 Information Type: Service Information Date: 2014/4/16 Profile: CEX, EC45 [GB] Installing the oil pressure switch Op nbr 22205 Socket wrench for oil pressure switch 1. Cover the thread on the oil pressure switch with sealing compound. Turn in the oil pressure switch and tighten with the socket wrench to 10 2 Nm.
https://www.ebooklibonline.com Hello dear friend! Thank you very much for reading. Enter the link into your browser. The full manual is available for immediate download. https://www.ebooklibonline.com