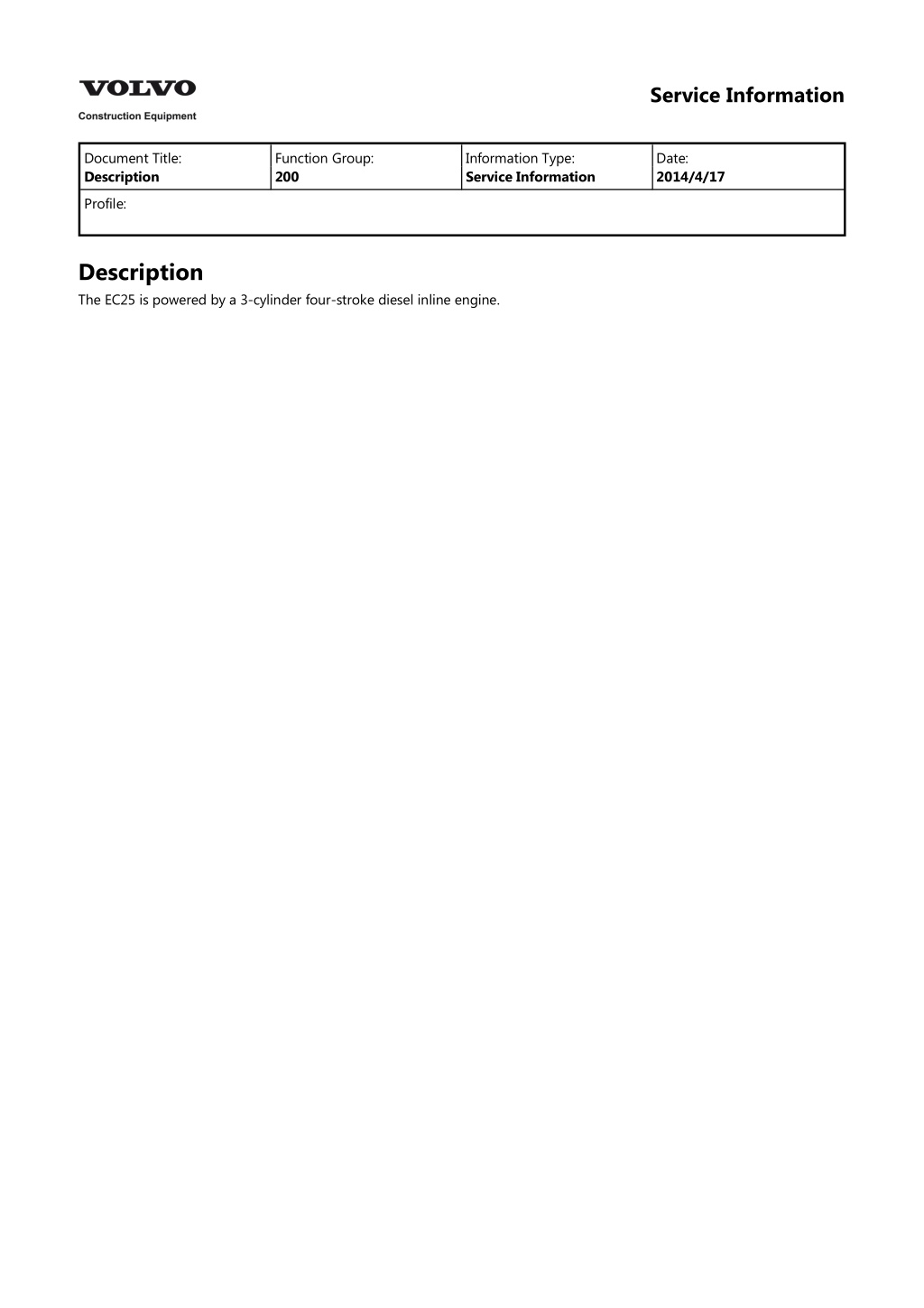
Volvo EC25 Compact Excavator Service Repair Manual Instant Download
Please open the website below to get the complete manualnn// n
Download Presentation

Please find below an Image/Link to download the presentation.
The content on the website is provided AS IS for your information and personal use only. It may not be sold, licensed, or shared on other websites without obtaining consent from the author. Download presentation by click this link. If you encounter any issues during the download, it is possible that the publisher has removed the file from their server.
E N D
Presentation Transcript
Service Information Document Title: Description Function Group: 200 Information Type: Service Information Date: 2014/4/17 Profile: Description The EC25 is powered by a 3-cylinder four-stroke diesel inline engine.
Service Information Document Title: Installing the engine Function Group: 200 Information Type: Service Information Date: 2014/4/17 Profile: Installing the engine Op nbr 2101 Lifting sling 1 m Shackle 3/8"" Figure 1 1. Attach the lifting tackle to the engine. Weight approx. 125 kg. 2. Lift the engine into the machine. NOTE! Take care not to damage the hydraulic hoses. 3. Assemble the front left hand engine mounting. Cover the screws slightly with Loctite and tighten with 55 Nm. 4. Turn in the screws between engine mountings and rubber elements and tighten with 105 Nm. 5. Remove the lifting tackle to the engine. Figure 2 1. Bracket
2. Hydraulic pump 6. Install compensation tank bracket and engine hood lock. 7. Mount the hydraulic pump and tighten the screws with 105 Nm. 8. Fasten both brackets with hydraulic hoses to the rear engine mounts. 9. Assemble fan grid and heating hose bracket to the engine mounting. 10. Install heating and coolant hoses with new hose clamps. 11. Fasten the throttle control to the injection pump. Figure 3 1. 2. 3. 4. Engine block fastening screws Fastening screw Exhaust muffler bracket Traverse 12. Install the engine wiring loom and connect the following components: Oil pressure switch Injection pump Glow plug Temperature sensor Generator Starter Ground cable Fasten the cables with cable straps. 13. Assemble the exhaust muffler traverse. 14. Install the exhaust system, attach bracket (3) and tighten screw (2) with 85 Nm. 15. Fasten the exhaust bracket on the engine block and tighten screws (1) with 25 Nm.
https://www.ebooklibonline.com Hello dear friend! Thank you very much for reading. Enter the link into your browser. The full manual is available for immediate download. https://www.ebooklibonline.com
Figure 4 16. Install the air filter with bracket and tighten the screws with 24 Nm. 17. Connect the electrical cables and terminals to the following components: Socket Fuel pump Air filter vacuum gauge Fasten the cables with cable straps. 18. Reconnect the fuel pipes. 19. Set the valve lever on the fuel pre-cleaner to position OPEN. Figure 5 20. Fill in coolant. Filling capacity: approx. 6 litres. 21. Connect the ground cable to the battery. 22. Fold the lateral weight back in and fasten with screws. 23. Assemble engine hood and floor plate. 24. Start the engine and make sure that there are no leaks.
Service Information Document Title: Operator side Function Group: 200 Information Type: Service Information Date: 2014/4/17 Profile: Operator side Figure 1 Engine, side view 1. 2. 3. 4. 5. 6. 7. 8. 9. Oil filler neck Injection pump Water pump Oil filler neck Crankshaft pulley Oil filter Oil drain plug Oil dipstick Flywheel Coolant drain plug Intake manifold Injection nozzle 10. 11. 12.
Service Information Document Title: Performance characteristics (measuring values for one hour with fan) Function Group: 200 Information Type: Service Information Date: 2014/4/17 Profile: Performance characteristics (measuring values for one hour with fan) Engine performance diagram Figure 1 Engine power Engine (hp/kW) Power S3L S3L2 With fan With fan rpm 1500 1800 2000 2200 2500 1500 12.0 / 8.8 15.0 / 11.0 17.0 / 12.5 19.0 / 14.0 21.5 / 15.8 11.4 / 8.4 14.5 / 10.7 18.0 / 13.2 20.0 / 14.7 22.0 / 16.2 24.5 / 18.0 13.8 / 10.1 1 hour (without overload) Continuous
1800 2000 2200 2500 14.3 / 10.5 16.2 / 12 18.1 / 13.3 20.4 / 15 17.1 / 12.6 19.0 / 14.0 20.9 / 15.4 23.3 / 17.1
Service Information Document Title: Removing the engine Function Group: 200 Information Type: Service Information Date: 2014/4/17 Profile: Removing the engine Op nbr 2101 Lifting sling 1 m Shackle 3/8"" Figure 1 1. Disassemble engine hood and floor plate. 2. Unscrew the bolts from the lateral weights and pull the weights out. 3. Disconnect the ground cable from the battery. WARNING When opening the lid of the compensation tank (radiator cap) there is a risk of scalding because of the overpressure in the cooling system. 4. Unscrew the drain plug, open the radiator cap and drain of all coolant. Filling quantity approx. 6 litres. Figure 2 5. Set the valve lever on the fuel pre-cleaner to position CLOSED.
6. Disassemble the fuel pipes. 7. Disconnect all necessary electrical cables and terminals from the following components: Socket Fuel pump Air filter vacuum gauge 8. Unscrew the top and bottom fastening screws from the bracket and remove the complete air filter. Figure 3 1. 2. 3. 4. Engine block fastening screws Fastening screw Exhaust muffler bracket Traverse 9. Remove the exhaust silencer from the exhaust tube. 10. Unscrew the fastening screws from bracket and engine block and remove the exhaust system. 11. Disassemble the exhaust muffler traverse. 12. Disconnect all necessary electrical cables and terminals from the following components: Oil pressure switch Injection pump Glow plug Temperature sensor Generator Starter Ground cable Figure 4 1. 2. Bracket Hydraulic pump
13. Lay the engine wiring loom to the side. 14. Disconnect the throttle control from the injection pump. 15. Remove the heating hose bracket from the engine mounting. 16. Disassemble heating and coolant hoses. 17. Remove the fan grid. 18. Disassemble both brackets for hydraulic hoses from the rear engine mounts. 19. Remove the hydraulic pump from the engine. 20. Unscrew the screws between engine mounts and rubber elements. 21. Remove front left hand engine mounting, compensation tank bracket and engine hood lock. Figure 5 Attach the lifting tackle 1. 2. Lifting sling 1 m Shackle 3/8"" 22. Attach the lifting tackle to the engine. 23. Lift the engine out. Weight: approx. 125 kg
Service Information Document Title: Specification, engine Function Group: 200 Information Type: Service Information Date: 2014/4/17 Profile: Specification, engine Engine Type designation Firing sequence (injection sequence) Compression ratio Type of combustion chamber Number of cylinders Bore x stroke, mm Displacement, litres Compression pressure Max. permissible pressure deviation between cylinders Idle speed Full speed Installed net power (ISO 9249) Maximum torque Cooling Air filter S3L -61A S3L2-61A 1 - 3 - 2 22:1 Swirl chamber 3 78 x 78.5 1.125 78 x 92 1.318 32 bar 3 bar 900 + 100 rpm 2400 + 20 rpm 17.1 kW at 2200 rpm 77 kW at 1600 rpm Centrifugal water pump with temperature control Dry
Service Information Document Title: Specification, capacities Function Group: 200 Information Type: Service Information Date: 2014/4/17 filling Profile: Specification, filling capacities Engine, oil change incl. filter 5.7 l
Service Information Document Title: Specification, weight Function Group: 200 Information Type: Service Information Date: 2014/4/17 Profile: Specification, weight Engine, standard 125 kg
Service Information Document Title: Starter side Function Group: 200 Information Type: Service Information Date: 2014/4/17 Profile: Starter side Figure 1 Engine, side view 1. 2. 3. 4. 5. 6. 7. 8. Exhaust manifold Starter Oil sump V-belt Fan Generator Lifting eye Thermostat
Service Information Document Title: Tightening torque Function Group: 200 Information Type: Service Information Date: 2014/4/17 Profile: Tightening torque Tightening torques engine S3L-S3L2 Tightening torques Cylinder head bolt Rocker cover bolt Rocker shaft bracket bolt Thermoswitch Crankshaft pulley nut Main bearing cap bolt Connecting rod cap nut Rear plate bolt (tractor engine) Rear plate bolt (standard) Rear plate bolt (stamping) Flywheel bolt Oil pan bolt (tractor motor) Oil pan drain plug Pressure relief valve Oil filter Oil pressure switch Fuel injection pipe nut Fuel leak-off pipe nut Delivery valve holder Fuel injection nozzle holder Retaining nut for delivery valve holder body Sliding sleeve shaft Special nut for torque spring set Glow plug Glow plug connection plate Stop solenoid nut Starter B terminal Nm 88 5 11.3 1.5 14.7 5 22.6 4 172 25 51.5 2.5 34.8 2.5 93 10 64 10 11.3 1.5 132 5 27.5 3 39 5 49 5 12 1 10 2 29 5 27 2.5 49 5 54 5 37 2.5 35 6 20 5 17.2 2.5 1.2 0.2 44 5 10.8 1
Service Information Document Title: Valve timing Function Group: 200 Information Type: Service Information Date: 2014/4/17 Profile: Valve timing Technical data, general Valve system Valve clearance (warm or cold engine) Intake valve Exhaust valve 0.25 mm 0.25 mm
Service Information Document Title: Checking the compression pressure Function Group: 211 Information Type: Service Information Date: 2014/4/17 Profile: Checking the compression pressure Op nbr ST332270 Adapter for pressure gauge Figure 1 1. Set the control lever to a position in which the fuel supply is interrupted. 2. Disassemble all glow plugs and install adapter (1) ST332270 with pressure gauge (2) to one of the cylinders. 3. Crank the engine with the starter. Compression pressure, see table [Invalid linktarget] The measured compression pressure depends on the starter speed during the measuring process and the altitude of the engine location. Limit values can therefore not be specified precisely. The compression pressure measurement is only recommended as a comparison measurement for all cylinders of an engine. If a deviation of more than 10% is found the respective cylinders should be disassembled in order to detect the cause. 4. Insert all glow plugs and tighten with 17.2 2.5 Nm.
Service Information Document Title: Adjusting the valves Function Group: 214 Information Type: Service Information Date: 2014/4/17 Profile: Adjusting the valves Figure 1 Op nbr 21412 NOTE! Before starting adjustment work clean the area around the rocker cover. 1. Pull off the crankcase ventilation hose. 2. Remove the rocker cover. 3. Crank the engine until the valves are overlapping. NOTE! Overlapping of valves means: Exhaust valve not yet closed, intake valve starts to open. Both push rods cannot be turned. Figure 2 4. Adjust the valve clearance on the respective cylinder with a feeler gauge ( [Invalid linktarget] ) 5. Tighten the counter nut. Check the adjustment once again with a feeler gauge.
Suggest: If the above button click is invalid. Please download this document first, and then click the above link to download the complete manual. Thank you so much for reading
6. Attach the gasket to the rocker cover. 7. Fasten the rocker cover. Tighten the screws with a torque of 11.3 Nm. 8. Plug on the crankcase ventilation hose.
https://www.ebooklibonline.com Hello dear friend! Thank you very much for reading. Enter the link into your browser. The full manual is available for immediate download. https://www.ebooklibonline.com