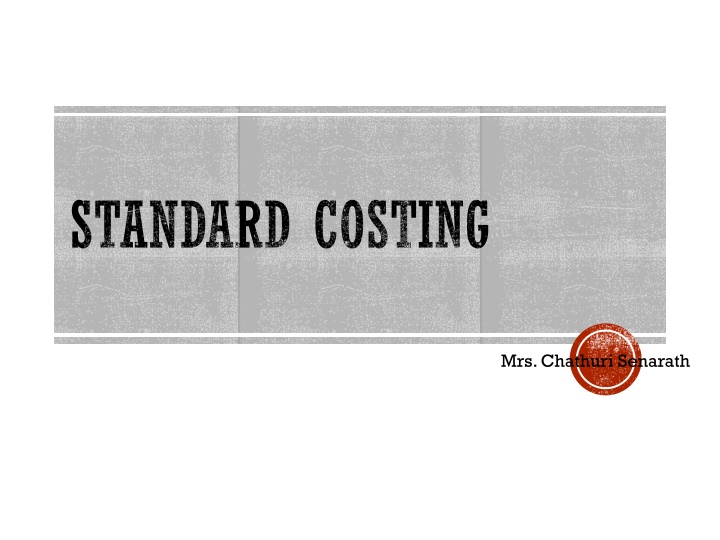
Understanding Standard Costing Principles
Learn all about standard costing, a control technique that compares actual costs to pre-set standards to manage exceptions effectively. Discover its benefits, uses, and implementation steps in modern organizations.
Download Presentation

Please find below an Image/Link to download the presentation.
The content on the website is provided AS IS for your information and personal use only. It may not be sold, licensed, or shared on other websites without obtaining consent from the author. If you encounter any issues during the download, it is possible that the publisher has removed the file from their server.
You are allowed to download the files provided on this website for personal or commercial use, subject to the condition that they are used lawfully. All files are the property of their respective owners.
The content on the website is provided AS IS for your information and personal use only. It may not be sold, licensed, or shared on other websites without obtaining consent from the author.
E N D
Presentation Transcript
STANDARD COSTING Mrs. Chathuri Senarath
STANDARD COSTING WHAT ? Control technique that reports variances by comparing actual costs to pre-set standards so facilitating action through management by exception.
WHEN STANDARD COSTING IS USED The greatest benefit from its use can be gained if there is a degree of repetition in the production process. It is therefore most suited to mass production and repetitive assembly work.
STANDARD COSTING 1. Developing standards 2. Compares standards with actual (variance) 3. Generate information (variance analysis) 4. Stimulate improved performance
01. DEVELOPING STANDARDS ? What is a standard ? The difference between a standard and a budget ? How to set the standards ? Manufacturing Vs Service Standards, is it suitable for modern organizations ?
WHAT IS A STANDARD ? A predetermined unit cost Pre-determine Estimate For future period Per unit
Standard cost card Product: A Cost Requirement Rs Rs Direct Materials X Y Z Others Rs 2.00 per kg Rs 3.00 per kg Rs 4.00 per liter 6 kgs 2kgs 1 lit 12.00 6.00 4.00 2.00 24.00 Direct labour Grade I Grade II Rs 4.00 per hour Rs 5.40 per hour 3 hrs 5 hrs 12.00 27.00 39.00 Variable production overheads Fixed production overheads Standard full cost of production Rs 1.00 per hour Rs 3.00 per hour 8 hrs 8 hrs 8.00 24.00 95.00
THE DIFFERENCE BETWEEN A STANDARD AND A BUDGET ? A budget usually refers to a department's or a company's projected revenues, costs, or expenses. A standard usually refers to a projected amount per unit of product,per unit of input (such as direct materials, factory overhead), or per unit of output. For example, a manufacturer will have budgets for its manufacturing or factory overhead departments. Let's assume that the budgeted manufacturing overhead for the upcoming year is expected to be $1,000,000 in order to produce the expected 100,000 identical units of product. The standard cost of manufacturing overhead per unit of product is $10 ($1,000,000 divided by 100,000 units)
HOW TO SET THE STANDARDS ? Depends on the type of organization
IF THE ORGANIZATION IS A MANUFACTURING ENTITY Normal items looked at are; Material Labour O/H Sales & we look at price/rate or volume/qty
FOR PRICE/RATE STANDARDS INFO: Past prices or rates (past trends) Estimates received from material or labour suppliers Level of quality planned (specifications: High or low quality material, high or low skilled workers). Agreements or possible agreements with trade unions National legislations (Ex: minimum wage rate acts, price controls) Types of overheads and the current methods used. Specific external factors [Competitors, Customers (level of demand, price elasticity), Suppliers] General external factors [Political / Economical (inflation and interest rates) / Social and Legal / Technical]
FOR QUANTITY/VOLUME STANDARDS INFO: Past performance Competitor performance Planned Performance Level of performance gives: Ideal standard Attainable standard Current standard Basic standard
IF THE ORGANIZATION IS A SERVICE PROVIDER Few issues Difficult to establish a measurable cost unit Every cost unit will be different / heterogeneous High levels of human involvement
STANDARD & SERVICE ORGANISATIONS Exceptional cases McDonaldization Diagnostic Reference Grouping
STANDARDS, IS IT SUITABLE FOR MODERN ORGANIZATIONS ? Stable Vs Dynamic environment Cost control or Cost management Labour centric or Realistic Aggregate Vs Individualistic Standards and Behavioral implications
2. COMPARES STANDARDS WITH ACTUAL (VARIANCE)
VARIANCE Standard items Actual items
AT THE END OF THE PERIOD THIS IS WHAT WE ARE LOOKING AT Actual Info. Standard Info. Per Unit Materials 1 5 kg@4 Labour 1 6 hrs@5 Variable 1 6 hrs@2.5 Fixed 1 6 hrs Total cost 30.00 Selling price 6.00 8.00 4.00 12.00 Materials 10,300 kgs Labour 11,420 hours Overhead: Variable Fixed Sales revenue 38,720 71,200 29,650 83,800 164,800 40 00 Budget Production Budget Sales = 5000 units Actual production = 6000 = 5000 units Actual sales = 4300 Important points to remember : Are we looking at per unit or a total comparison At what activity level We can break it down to
TYPES OF VARIANCE Direct Material variance Direct Labour variance Variable O/H variance Fixed O/H variance Sales variance
Total Direct Material Variances Price Variance Usage Variance
TOTAL DIRECT MATERIAL VARIANCE Std material x Actual no of - Cost per unit units produced Actual cost incurred
MATERIAL PRICE VARIANCE Std material Cost Per Kg Actual Material cost per Kg Actual material purchased or used* Material Usage variance Std material x Actual units Actual Raw Std raw material usage per units produced material used cost per Kg
Material price variance 4 38720/10300 X 10300 = 2480Fav Material usage variance 1.5X6000 10300 x 4 = 5200Adv
Total Direct Labour Variances Rate Variance Efficiency Variance Idle time Variance
TOTAL LABOUR COST VARIANCE Std labour x Actual No units Cost per unit - Actual labour cost incurred produced
LABOUR RATE VARIANCE Std labour Actual labour Actual hours worked rate Per hour rate per hour Labour efficiency Variance Std labour x Actual units Actual hours hrs per unit produced actively worked Std labour rate per hr. Labour : Idle time Variance Idle hrs X Std labour rate per hour
Labour rate variance 5 - 71200/11420 X 11420 = 14100Adv Labour efficiency variance 1.6 X 6000 9150 X 5 = 2250Fav Idle time variance 2270 X 5 = 11350 Adv
Total Variable O/H cost Variances Expenditure Variance Efficiency Variance
TOTAL VARIABLE O/H COST VARIANCE Std variable O/H x Actual units - Actual variable O/H Cost per unit produced cost incurred
VARIABLE O/H EXPENDITURE VARIANCE Std variable O/H - Actual variable O/H Actual active expenditure per expenditure per hrs worked hr active hrs * Variable O/H efficiency Variances Std hrs per x no of units - Actual active Std variable O/H Unit produced hrs per hour
Variable O/H expenditure variance 2.5 - 29650/9150 X 9150 = 6775 Adv Variable O/H efficiency variance 1.6 X 6000 9150 X 2.5 = 1125Fav
ONE VARIANCE NOT LOOKED AT IN FOUNDATION Fixed Overhead
THE FIXED O/H Fixed O/H is different to other items ? If the Fixed O/H is calculated in per unit terms We already have the name
TOTAL FIXED O/H COST VARIANCE Fixed O/H x Actual activity - Actual fixed O/H Absorption level cost incurred rate per unit
Total Fixed O/H cost Variances Expenditure Variance Volume Variance
FIXED O/H EXPENDITURE VARIANCE Bug. Fixed O/H cost - Actual fixed O/H cost Fixed O/H volume variance Bud units Actual units fixed O/H absorption rate per unit
Fixed O/H expenditure variance 12X5000 - 83800 = 23,800 Adv Fixed O/H volume variance 5000 6000 X 12 = 12,000Fav
Sales Variances Price Variance Volume Variance
SALES PRICE VARIANCE Std selling price - Actual price Actual no of units sold per unit per unit Sales Volume variance (Budgeted sales units - Actual sales units) Std profit per unit (Budgeted sales units Actual sales units) Std contribution per unit (Budgeted sales units - Actual sales units) Std revenue per unit
Sales price variance (40 - 164800/4300) 4300 = 7200 Adv Sales volume variance * (5000 4300) X 10 = 7,000 Adv * (5000 4300) X 22 = 15,400 Adv * (5000 4300) X 40 = 28,000 Adv
OPERATING STATEMENT (STATEMENT OF VARIANCES/RECONCILIATION)
Operating Statement Budgeted profit Sales volume variance xxx/(xxx) Standard profit xxxx Sales price variance xxx/(xxx) xxxx Cost Variances Adverse Favorable Material - price usage Labour - rate efficiency idle Variable O/H - expenditure efficiency Fixed O/H - expenditure volume Actual profitxxxx xxx/(xxx)
TYPES OF OPERATING STATEMENT Profit statement (Absorption costing) Profit statement (Marginal costing) Contribution statement Cost statement
PROFIT STATEMENT (ABSORPTION COSTING)
Profit statement (Absorption costing) Budgeted profit Sales volume variance Sales price variance xxxx xxx/(xxx) xxx/(xxx) Cost Variances Material - price usage Labour - rate efficiency idle Variable O/H - expenditure efficiency Fixed O/H - expenditure volume Actual profit Adverse Favorable xxx/(xxx) xxxx
A. BUDGETED PROFIT/LOSS Sales 200,000 Less Cost of sales Op. Stock - Production 150,000 -Cl. Stock - (150,000) Gross profit 50,000 Adj. Under or Over Absorbed Less- Non production cost Net profit 50,000
B. ACTUAL PROFIT/LOSS Sales 164,800 Less Cost of sales Op. Stock Production 223,370 -Cl. Stock (1700X30) (172,370) Gross profit (7,570) Adj. Under or Over Absorbed Less- Non production cost Net profit (7,570)
c. Operating Statement Budgeted profit 50,000 Sales volume variance (7000) Standard profit 43,000 Sales price variance (7200) Cost Variances Adverse Favorable Material - price 2480 usage 5200 Labour - rate 14100 efficiency 2250 idle 11350 Variable O/H - expenditure 6775 efficiency 1125 Fixed O/H - expenditure 23800 volume 12000 (43370) Actual profit(7570)