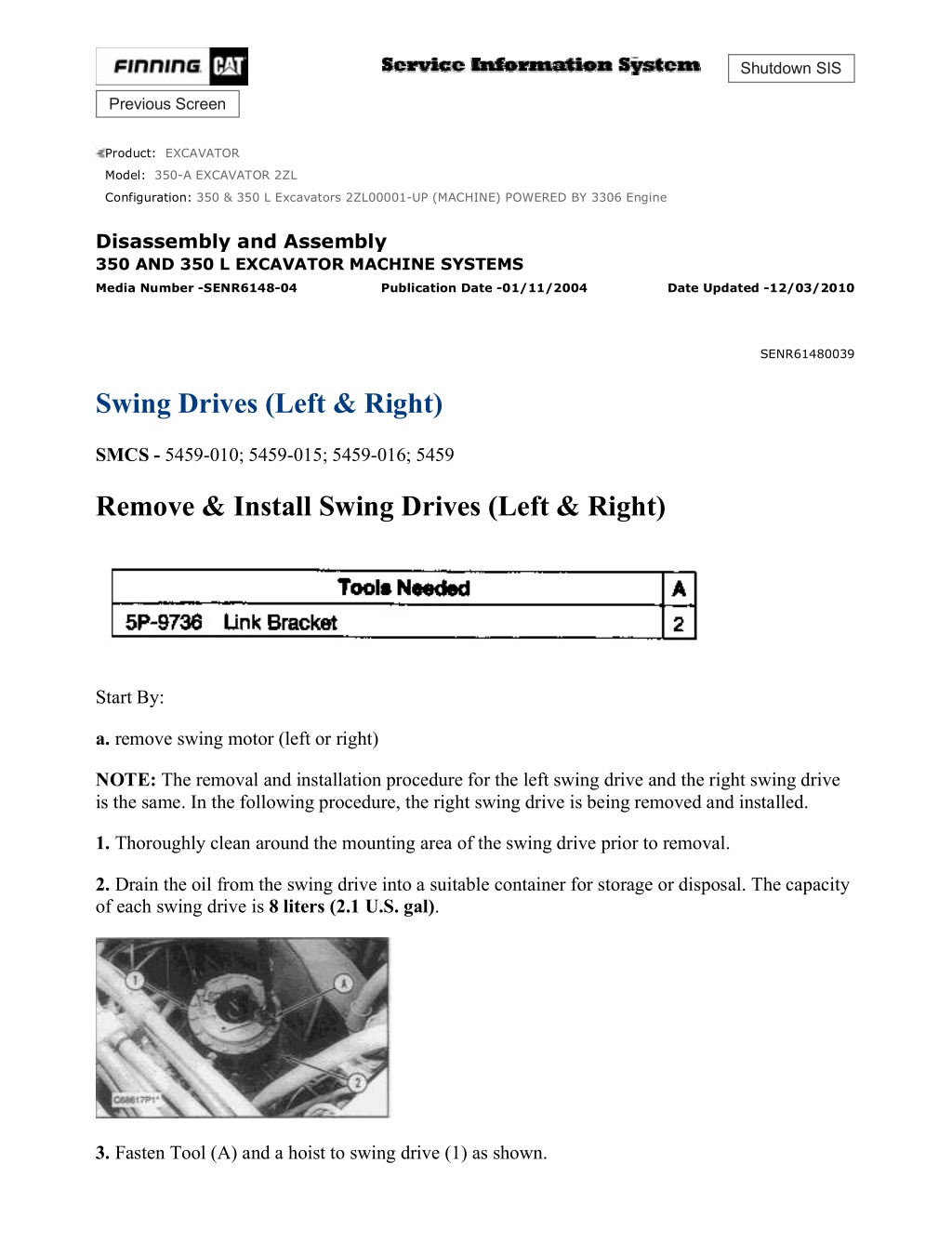
Caterpillar Cat 350 and 350 L Excavator (Prefix 2ZL) Service Repair Manual Instant Download
Please open the website below to get the complete manualnn//
Download Presentation

Please find below an Image/Link to download the presentation.
The content on the website is provided AS IS for your information and personal use only. It may not be sold, licensed, or shared on other websites without obtaining consent from the author. Download presentation by click this link. If you encounter any issues during the download, it is possible that the publisher has removed the file from their server.
E N D
Presentation Transcript
w 1/13(W) Shutdown SIS Previous Screen Product: EXCAVATOR Model: 350-A EXCAVATOR 2ZL Configuration: 350 & 350 L Excavators 2ZL00001-UP (MACHINE) POWERED BY 3306 Engine Disassembly and Assembly 350 AND 350 L EXCAVATOR MACHINE SYSTEMS Media Number -SENR6148-04 Publication Date -01/11/2004 Date Updated -12/03/2010 SENR61480039 Swing Drives (Left & Right) SMCS - 5459-010; 5459-015; 5459-016; 5459 Remove & Install Swing Drives (Left & Right) Start By: a. remove swing motor (left or right) NOTE: The removal and installation procedure for the left swing drive and the right swing drive is the same. In the following procedure, the right swing drive is being removed and installed. 1. Thoroughly clean around the mounting area of the swing drive prior to removal. 2. Drain the oil from the swing drive into a suitable container for storage or disposal. The capacity of each swing drive is 8 liters (2.1 U.S. gal). 3. Fasten Tool (A) and a hoist to swing drive (1) as shown. https://127.0.0.1/sisweb/sisweb/techdoc/techdoc_print_page.jsp?returnurl=/sisweb/siswe... 2022/3/7
w 2/13(W) 4. Remove 20 bolts (2) and the washers that hold the swing drive in position. Remove the two corks from the forcing screw holes in the swing drive housing. Install suitable size forcing screws in the threaded forcing screw holes. Tighten the forcing screws evenly to separate the swing drive from the main frame. 5. Remove swing drive (1) from the machine. The weight of the swing drive is 308 kg (680 lb). NOTE: The following steps are for the installation of the swing drive. 6. Thoroughly clean the mating surfaces of the main frame and the swing drive housing. 7. Put 5P-3931 Anti-Seize Compound on the locating dowel in the main frame. 8. Put 1U-8846 Gasket Maker on the mating surface of the main frame and the swing drive housing. NOTE: During installation, the locating dowel for the swing drive may come out of the swing drive housing. 9. Fasten Tool (A) and a hoist to swing drive (1). Put the swing drive in its original position in the main frame. If the locating dowel comes out of the swing drive housing, it can be reinstalled with a hammer after the swing drive is in place. 10. Put 9S-3263 Thread Lock on the threads of 20 bolts (2). Install the 20 bolts and washers that hold the swing drive in position. Reinstall the two corks in the forcing screw holes in the swing drive housing. 11. After installation of the swing motor, fill the hydraulic oil tank and the swing drive with oil to the correct level. Refer to the 350 & 350 L Excavators Operation & Maintenance Manual for the correct filling procedures. End By; a. install swing motor (left or right) Disassemble Swing Drive (Left & Right) Start By: a. remove swing drive (left or right) https://127.0.0.1/sisweb/sisweb/techdoc/techdoc_print_page.jsp?returnurl=/sisweb/siswe... 2022/3/7
w 3/13(W) NOTE: The disassembly procedure which follows is for both the left and right swing drives. 1. Fasten the swing drive to Tool (A) as shown. The weight of the swing drive is 308 kg (680 lb). 2. Put an alignment mark on the cover, ring gear and main housing of the swing drive for assembly purposes. 3. Remove 16 bolts (1) and the washers that hold cover (2) to the ring gear and housing of the swing drive. 4. Fasten Tool (B) and a hoist to cover (2). Remove the cover. The weight of the cover is 16 kg (35 lb). 5. Remove sun gear (3) from the carrier assembly. 6. Remove carrier assembly (4). 7. Disassemble carrier assembly (4) as follows: https://127.0.0.1/sisweb/sisweb/techdoc/techdoc_print_page.jsp?returnurl=/sisweb/siswe... 2022/3/7
https://www.ebooklibonline.com Hello dear friend! Thank you very much for reading. Enter the link into your browser. The full manual is available for immediate download. https://www.ebooklibonline.com
w 4/13(W) a. Drive spring pin (6) into planetary shaft (5) with a hammer and punch. b. Remove planetary shaft (5), two thrust washers (9) and planetary gear (7) from the carrier. c. Remove bearing (8) from planetary gear (7). d. Remove spring pin (6) from planetary shaft (5) with a hammer and punch. e. Remove the other three planetary gears from the carrier as in Steps 7a through 7d. f. Remove retaining ring (10) with a screwdriver. Remove gear (11) from carrier (4). g. Remove retaining ring (12) from gear (11). https://127.0.0.1/sisweb/sisweb/techdoc/techdoc_print_page.jsp?returnurl=/sisweb/siswe... 2022/3/7
w 5/13(W) 8. Spacer (14) has been discontinued and is no longer part of the assembly. 9. Slide a piece of steel bar stock in between the planetary gears in carrier assembly (13) as shown. Make sure the bar stock is centered in the carrier assembly. Fasten a lifting sling and a hoist to the steel bar stock as shown. Slowly lift carrier assembly (13) from the swing drive. The weight of the carrier assembly is 39 kg (85 lb). 10. Disassemble carrier assembly (13) as follows: a. Drive spring pin (16) into planetary shaft (15) with a hammer and punch. b. Remove planetary shaft (15), two thrust washers (19) and planetary gear (17) from the carrier. c. Remove two bearings (18) from planetary gear (17). d. Remove spring pin (16) from planetary shaft (15) with a hammer and punch. e. Remove the other three planetary gears from the carrier as in Steps 10a through 10d. https://127.0.0.1/sisweb/sisweb/techdoc/techdoc_print_page.jsp?returnurl=/sisweb/siswe... 2022/3/7
w 6/13(W) 11. Fasten Tool (C) and a hoist to ring gear (20) as shown. Remove the ring gear. The weight of the ring gear is 36 kg (80 lb). 12. Bend the tab down on the locking washer used under bolt (21). Loosen bolt (21) approximately 12.7 mm (.50 in). Do not remove the bolt at this time. Use Tool (D) to loosen coupling (23) from the end of the pinion shaft. Remove Tool (D) from the coupling. 13. Remove bolt (21), the locking washer, retainer (22) and coupling (23) from the main housing. 14. Remove shims (24) from the end of the pinion shaft. If necessary, remove the two locating pins from the end of the pinion shaft. 15. Loosen eight bolts (25) that hold the cage to the main housing. Do not remove bolts (25) until the main housing has been position in a press for removal of the pinion shaft. https://127.0.0.1/sisweb/sisweb/techdoc/techdoc_print_page.jsp?returnurl=/sisweb/siswe... 2022/3/7
w 7/13(W) 16. Put main housing (26) in a press as shown. The combined weight of the main housing, pinion shaft, cage and bearings is approximately 136 kg (300 lb). 17. Install Tool (E) on the end of the pinion shaft. Put and alignment mark on the cage and main housing for assembly purposes. Put a wood block under the pinion shaft as shown. Remove eight bolts (25) and the washers. 18. Using the press, remove the pinion shaft, bearings and cage, as a unit, from main housing (26). Remove the O-ring seal from the cage. 19. Using the press and Tool (E), remove pinion shaft (28) from bearing (27), spacer (29) and bearing (30). 20. Using a press, remove bearing (30) from cage (31). 21. Remove lip-type seal (32) from cage (31). https://127.0.0.1/sisweb/sisweb/techdoc/techdoc_print_page.jsp?returnurl=/sisweb/siswe... 2022/3/7
w 8/13(W) Assemble Swing Drive (Left & Right) NOTE: The assembly procedure which follows is for both the left and right swing drives. 1. Make sure all parts of the swing drive are thoroughly clean and free of dirt and debris prior to assembly. Check the condition of the O-ring seal used in cage (31). If the seal is damaged, use a new part for replacement. Reassemble the swing drive on Tool (A). 2. Put 5P-3413 Pipe Sealant on the inner surface of cage (31) where lip-type seal (32) fits. Install lip-type seal (32) in cage (31) with Tool (D). Install the seal with the lip facing toward the outside of the cage and until it makes contact with the counterbore in the cage. Lubricate the lip of the seal with 5P-0960 Multipurpose Grease. 3. Put 5P-3931 Anti-Seize Compound on the outside diameter of bearing (30) and the inside diameter of cage (31) where bearing (30) fits. Install bearing (30) in cage (31) with a press. Install the bearing until it makes contact with the counterbore in the cage. NOTICE Do not damage lip-type seal (32) during installation of pinion shaft (28) in the cage. Also, make sure to support bearing (30) during installation of the pinion shaft in the cage. https://127.0.0.1/sisweb/sisweb/techdoc/techdoc_print_page.jsp?returnurl=/sisweb/siswe... 2022/3/7
w 9/13(W) 4. Put a thin coat of 5P-0960 Multipurpose Grease on the surface of the pinion shaft that makes contact with seals (32). Install pinion shaft (28) in cage (31) and bearing (30) with a press. Install the pinion shaft until it seats against the bearing in the cage. 5. Install spacer (29) over the pinion shaft. 6. Install bearing (27) on pinion shaft (28) with a press. Install the bearing until it makes contact with spacer (29). 7. Make sure the mating surfaces of the cage (31) and main housing (26) are clean and free of dirt and debris. Put 1U-8846 Gasket Maker on the mating surfaces of the cage and main housing. Install the O-ring seal in cage (31). Using a press, install the cage with the pinion shaft in the main housing. Make sure the alignment marks made on the components during disassembly line up with each other. Put a thin coat of 9S-3263 Thread Lock on the threads of eight bolts (25). Install eight bolts (25) and the washers that hold the cage to the main housing. 8. Adjust the end play of the coupling as follows: a. Install coupling (23) on the pinion shaft without shims (24). Install retainer (22), the locking washer and bolt (21). Tighten the bolt, but do not bend the tab on the locking washer over the head of the bolt at this time. b. Support the pinion shaft so the coupling can be moved up and down. Using a dial indicator, measure the end play of the coupling. Record this dimension. c. Add shims (24) between coupling (23) and retainer (22) until the end play of the coupling is .175 .125 mm (.007 .005 in). d. Remove bolt (21), the locking washer, retainer (22) and coupling (23) from the pinion shaft. 9. If the two locating pins in the end of the pinion shaft were removed, reinstall them. Prior to installing the locating pins, put 5P-3931 Anti-Seize Compound in the locating pin holes in the end of the pinion shaft and on the outside of the two locating pins. https://127.0.0.1/sisweb/sisweb/techdoc/techdoc_print_page.jsp?returnurl=/sisweb/siswe... 2022/3/7
w 10/13(W) 10. Install shim (24), that was determined in Steps 8a through 8d, on the end of the pinion shaft as shown. NOTICE Do not damage retainer (24) when the tab of the locking washer is bent against the head of bolt (21). 11. Put 9S-3263 Thread Lock on the threads of bolt (21). Install coupling (23), retainer (22), the locking washer and bolt (21). Tighten bolt (21) to a torque of 181 24.5 N m (135 18 lb ft). Sharply bend the tab of the locking washer against the flat on the head of bolt (21). 12. Put 1U-8846 Gasket Maker on the mating surface of ring gear (20) and main housing (26). 13. Fasten Tool (C) and a hoist to ring gear (20). Put the ring gear in its original position on the main housing. 14. Assemble carrier assembly (13) as follows: a. Put clean SAE 30 oil on bearings (18). Install two bearings (18) in planetary gear (17). https://127.0.0.1/sisweb/sisweb/techdoc/techdoc_print_page.jsp?returnurl=/sisweb/siswe... 2022/3/7
w 11/13(W) b. Install a thrust washer (19) on each side of the planetary gear. Install the planetary gear and the thrust washers in the carrier. Install planetary shaft (15) in the carrier and through planetary gear (17). Make sure the spring pin hole in the planetary shaft is in alignment with the spring pin hole in the carrier. c. Install spring pin (16) in the carrier and into the planetary shaft. Install the spring pin until it is slightly below the outside surface of the carrier and with the split in the spring pin facing toward the top or bottom of the carrier. To prevent the spring pin from falling out, make a stake mark on each side of the spring pin hole in the carrier. Each stake mark should be approximately 1.5 mm (.059 in) from the spring pin hole. 15. Install the other three planetary gears (17) in the carrier as in Steps 14a through 14c. 16. Spacer (14) has been discontinued and is no longer part of the assembly. 17. Install carrier assembly (13) in ring gear (20). Slide a piece of steel bar stock in between the planetary gears in carrier assembly (13) as shown. Make sure the bar stock is centered in the carrier assembly. Fasten a lifting sling and a hoist to the steel bar stock as shown. Lower the carrier assembly into position in the ring gear. It may be necessary to move the carrier assembly back and forth to allow all gears to line up and mesh correctly. 18. Assemble carrier assembly (4) as follows: a. Install retaining ring (12) in gear (11). b. Put gear (11) in carrier (4). Install retaining ring (10) with a screwdriver. https://127.0.0.1/sisweb/sisweb/techdoc/techdoc_print_page.jsp?returnurl=/sisweb/siswe... 2022/3/7
w 12/13(W) c. Put clean SAE 30 oil on bearing (8). Install bearing (8) in planetary gear (7). d. Install a thrust washer (9) on each side of the planetary gear. Install the planetary gear and thrust washers in the carrier. Install planetary shaft (5) in the carrier and through planetary gear (7). Make sure the spring pin hole in planetary shaft (5) is in alignment with the spring pin hole in the carrier. e. Install spring pin (6) in the carrier and into the planetary shaft. Install the spring pin until it is slightly below the outside surface of the carrier, and with the split in the spring pin facing toward the top or bottom of the carrier. To prevent the spring pin from falling out, make a stake mark on each side of the spring pin hole in the carrier. Each stake mark should be approximately 1.5 mm (.059 in) from the spring pin hole. f. Install the other three planetary gears in the carrier as in Steps 18c through 18e. 19. Install carrier assembly (4) in the swing drive. Lower the carrier assembly into position in the swing drive. It may be necessary to move the carrier assembly back and forth to allow all gears to line up and mesh correctly. https://127.0.0.1/sisweb/sisweb/techdoc/techdoc_print_page.jsp?returnurl=/sisweb/siswe... 2022/3/7
w 13/13(W) 20. Install sun gear (3) in carrier assembly (4). 21. Put a bead of 1U-8846 Gasket Maker on the mating surface of ring gear (20) and cover (2). 22. Fasten Tool (B) and a hoist to cover (2) as shown. Put the cover in its original position on ring gear (20). 23. Put 9S-3263 Thread Lock on the threads of 16 bolts (1). Install bolts (1) and the washers that hold cover (2). Tighten bolts (1) to a torque of 270 40 N m (200 30 lb ft). End By: a. install swing drive (left or right) Copyright 1993 - 2022 Caterpillar Inc. Mon Mar 7 13:25:19 UTC+0800 2022 All Rights Reserved. Private Network For SIS Licensees. https://127.0.0.1/sisweb/sisweb/techdoc/techdoc_print_page.jsp?returnurl=/sisweb/siswe... 2022/3/7
w 1/2(W) Shutdown SIS Previous Screen Product: EXCAVATOR Model: 350-A EXCAVATOR 2ZL Configuration: 350 & 350 L Excavators 2ZL00001-UP (MACHINE) POWERED BY 3306 Engine Disassembly and Assembly 350 AND 350 L EXCAVATOR MACHINE SYSTEMS Media Number -SENR6148-04 Publication Date -01/11/2004 Date Updated -12/03/2010 SENR61480040 Shuttle Valve (Swing Park Brake Release) SMCS - 5079-010 Remove & Install Shuttle valve (Swing Park Brake Release) NOTE: The shuttle valve (swing park brake release) is mounted on the inside of the main frame, directly behind the fuel tank. The purpose of this valve is to direct implement pilot pressure and/or swing pilot pressure to release the swing park brake. At operating temperature, the hydraulic oil tank is hot and under pressure. Hot oil can cause burns. To prevent possible personal injury, release the pressure in the implement hydraulic circuits (boom, stick and bucket) before any hydraulic lines or components are disconnected or removed. 1. Release the pressure in the hydraulic system as follows: a. Fully retract the rod in the stick cylinder. b. Adjust the position of the bucket so it will be flat on the ground when the boom is lowered. c. Lower the boom until the bucket is flat on the ground. d. Shut off the engine, and put the hydraulic activation control lever in the "Lock" position. e. Move the control levers for the boom, bucket, stick and swing through their full travel strokes. This will relieve any pressure that may be present in the pilot system. f. Slowly loosen the air breather cap on the hydraulic oil tank to release the pressure. https://127.0.0.1/sisweb/sisweb/techdoc/techdoc_print_page.jsp?returnurl=/sisweb/siswe... 2022/3/7
w 2/2(W) g. Tighten the air breather cap on the hydraulic oil tank. h. The pressure in the hydraulic system has now been released. Lines and components can now be removed. 2. Disconnect three hose assemblies (1) from the shuttle valve. Put plugs in the hose assemblies to prevent oil loss and to keep dirt and debris out of the hydraulic system. 3. Remove two socket head bolts (2) and shuttle valve (3). NOTE: Install the shuttle valve (swing park brake release) in the reverse order of removal. 4. Check the oil level in the hydraulic oil tank. If necessary, fill the hydraulic oil tank to the correct level with oil. Refer to the 350 & 350 L Excavators Operation & Maintenance Manual for the correct filling procedure. Copyright 1993 - 2022 Caterpillar Inc. Mon Mar 7 13:26:14 UTC+0800 2022 All Rights Reserved. Private Network For SIS Licensees. https://127.0.0.1/sisweb/sisweb/techdoc/techdoc_print_page.jsp?returnurl=/sisweb/siswe... 2022/3/7
w 1/10(W) Shutdown SIS Previous Screen Product: EXCAVATOR Model: 350-A EXCAVATOR 2ZL Configuration: 350 & 350 L Excavators 2ZL00001-UP (MACHINE) POWERED BY 3306 Engine Disassembly and Assembly 350 AND 350 L EXCAVATOR MACHINE SYSTEMS Media Number -SENR6148-04 Publication Date -01/11/2004 Date Updated -12/03/2010 SENR61480041 Undercarriage Frame Assembly SMCS - 4150-010 Remove & Install Undercarriage Frame Assembly Start By: a. remove bucket https://127.0.0.1/sisweb/sisweb/techdoc/techdoc_print_page.jsp?returnurl=/sisweb/siswe... 2022/3/7
w 2/10(W) 1. Start the machine, and move it onto a level surface. Position drain plug (2) for each final drive in the position shown. Drain the oil from each final drive into a suitable container for storage or disposal. The capacity of each final drive is 16 liters (4.2 U.S. gal). 2. Put wood blocks in front of and behind each track assembly. 3. Remove two cover assembly bolts (1) from the final drive. 4. Install two suitable size threaded rods (3) in the final drive, in place of two bolts (1). The threaded rods will prevent the ring gear and carrier assemblies from falling out of position when cover assembly (5) is removed. 5. Remove remaining bolts (4) that hold cover assembly (5) in position. 6. It may be necessary to use a soft faced hammer to break the seal between the cover assembly and ring gear of the final drive. Using two persons, remove cover assembly (5) from the final drive. The weight of the cover assembly 52 kg (115 lb). When ring gear (7) is removed from cover assembly (5) in each final drive, and the covers assemblies are reinstalled on the machine, the brakes for the machine are inoperable. The machine is free to move. To prevent movement of the machine, put wood blocks in front of and behind each track assembly. https://127.0.0.1/sisweb/sisweb/techdoc/techdoc_print_page.jsp?returnurl=/sisweb/siswe... 2022/3/7
w 3/10(W) 7. Remove 10 socket head bolts (6) and ring gear (7) from cover assembly (5). 8. Temporarily reinstall cover assembly (5) back on the final drive. Remove the two threaded rods from the final drive. 9. Repeat Steps 3 through 8 for the other final drive. 10. Loosen, but do not remove all bolts (8) that hold the upper structure to the undercarriage frame assembly. 11. Remove right hand boom cylinder (9) from the machine. See the topic "Remove & Install Boom Cylinders" in this module. Put caps in the hydraulic lines that connect to the right hand boom cylinder. 12. Start the machine, and rotate the upper structure 90 degrees to the right or left. Raise the boom, and fully extend the stick cylinder. https://127.0.0.1/sisweb/sisweb/techdoc/techdoc_print_page.jsp?returnurl=/sisweb/siswe... 2022/3/7
w 4/10(W) 13. With the engine still running, position the end of the stick so the distance between the end of the stick and the floor is the same as the distance between the floor and the bottom of the counterweight. This distance is approximately 1460 mm (57.5 in). NOTICE Do not lower the boom after Tool (A) has been installed in place of the right hand boom cylinder. 14. Adjust the length of Tool (A), and install it in place of the right hand boom cylinder. Make sure to use six bolts, washers and nuts to hold the link group [Tool (A)] together. 15. Adjust the height of Tooling (B) so it can be installed under the end of the stick as shown. Install Tooling (B) under the stick. Make sure the tooling is centered. 16. Install Tooling (C) under the main frame at the rear of the machine as shown. 17. Disconnect lubrication tube assemblies (10) from the block on the front of the main frame. 18. Remove all bolts (8) that hold the upper structure to the undercarriage frame assembly. https://127.0.0.1/sisweb/sisweb/techdoc/techdoc_print_page.jsp?returnurl=/sisweb/siswe... 2022/3/7
w 5/10(W) 19. Install a suitable size guide bolt (11) in the upper structure at the front of the upper structure and the rear of the upper structure as shown. At operating temperature, the hydraulic oil tank is hot and under pressure. Hot oil can cause burns. To prevent possible personal injury, release the pressure in the implement hydraulic circuits (boom, stick and bucket) before any hydraulic lines or components are disconnected or removed. 20. Release the pressure in the hydraulic system. 21. Drain the oil from the hydraulic oil tank into a suitable container for storage or disposal. The capacity of the hydraulic oil tank is 240 liters (63.3 U.S. gal). View From Under Machine 22. Remove six bolts (12) and the washers that hold cover (13) in position under the swivel group. Remove the cover. View From Under Machine https://127.0.0.1/sisweb/sisweb/techdoc/techdoc_print_page.jsp?returnurl=/sisweb/siswe... 2022/3/7
w 6/10(W) 23. Put identification marks on all hose and tube assemblies that are connected to the bottom of the swivel group. 24. Disconnect two hose assemblies (14). 25. Disconnect four hose assemblies (18) from the swivel group. 26. Disconnect two hose assemblies (16). Remove coupling (15). 27. Remove five bolts (17) and the washers from the swivel group. NOTICE It is important to keep the upper structure level when it is being removed or installed from the undercarriage frame assembly. If the upper structure is not kept level, binding of the pinion shaft in the left and right hand swing drives, with the swing gear and bearing, will result. The clearance between the gears is minimal. NOTE: The weight of the upper structure and undercarriage frame assembly will vary depending on the attachments. The weights which are listed below are only approximate weights. 28. Carefully raise upper structure (18) off of the undercarriage frame assembly with Tooling (B) and (C) in 6.4 mm (.25 in) increments. Raise the upper structure until pinion shafts (19) of the left and right swing drives are clear of swing gear and bearing (20). The weight of the upper structure is approximately 25946 kg (57200 lb). 29. Check the clearance between the pinion shafts of the left and right swing drives and the swing gear and bearing. Make sure they will not interfere with each other during removal of the undercarriage frame assembly. https://127.0.0.1/sisweb/sisweb/techdoc/techdoc_print_page.jsp?returnurl=/sisweb/siswe... 2022/3/7
w 7/10(W) NOTE: The weight of the upper structure should only be concentrated on Tooling (C). Tooling (D) is only used as additional support. 30. Install Tooling (D) under the rear of the machine as shown. 31. Remove the wood blocks from the front and rear of the track assemblies. 32. Fasten a chain to the undercarriage frame assembly as shown. Slowly pull undercarriage frame assembly (21) out from under the upper structure with a lift truck. The weight of the undercarriage frame assembly is approximately 25260 kg (55690 lb). 33. If the undercarriage frame assembly is to be serviced, use wood blocks to support the upper structure of the machine. Support the upper structure under the main frame and sub frame. NOTE: The following steps are for the installation of the undercarriage frame assembly. 34. Make sure the mating surfaces of the upper structure and undercarriage frame assembly are thoroughly clean and free of dirt and debris. 35. Make sure two guide bolts (11) in the upper structure are in position and not bent. NOTE: Two locating dowels are used to align the upper structure with the undercarriage frame assembly. Make sure these dowels are in position. 36. Put 4C-5593 Thread Lubricant in the bores in the swing gear and bearing for the locating dowels in the upper structure. 37. Put 1U-8846 Gasket Maker on the mating surfaces of the upper structure and the undercarriage frame assembly. 38. Remove the wood blocks from under the main frame and sub frame of the machine. 39. Using a lift truck, move undercarriage frame assembly (21) in position under the upper structure. NOTICE Because of the minimal amount of clearance between pinion shafts (19) in the left and right swing drives and swing gear and bearing (20), careful alignment of the upper structure with the undercarriage frame assembly is required. Make sure guide bolts (11) do not bend during installation of the upper structure. If the guide bolts bend, it is an indication that correct alignment between the upper structure and the https://127.0.0.1/sisweb/sisweb/techdoc/techdoc_print_page.jsp?returnurl=/sisweb/siswe... 2022/3/7
w 8/10(W) undercarriage frame assembly has not been obtained. Keep the upper structure level during installation. 40. Remove Tooling (D) from under the rear of the machine. Slowly lower upper structure (18) down with Tooling (B) and (C) in 6.4 mm (.25 in) increments. As the upper structure is being lowered, make sure two guide bolts (11) in the upper structure are in alignment with their respective bolt holes in the undercarriage frame assembly. 41. Put 4C-5593 Thread Lubricant on the threads of some of the bolts (8) that hold the upper structure and the undercarriage frame assembly together. At this time, only install the bolts that have easy access. Tighten the bolts evenly. Remove two guide bolts (11) from the upper structure. View From Under Machine 42. Install five bolts (17) and the washers in the bottom of the swivel group. 43. Reinstall coupling (15). 44. Check the condition of the O-ring seals used in the ends of the hose assemblies that are connected to the bottom of the swivel group. If any of the seals are damaged, use new parts for replacement. 45. Connect two hose assemblies (16) to the bottom of the swivel group. 46. Connect four tube assemblies (18) to the bottom of the swivel group. 47. Connect two hose assemblies (14) to the swivel group. View From Under Machine 48. Reinstall cover (13) with bolts (12) and the washers. https://127.0.0.1/sisweb/sisweb/techdoc/techdoc_print_page.jsp?returnurl=/sisweb/siswe... 2022/3/7
w 9/10(W) 49. Connect two lubrication tube assemblies (10) to the block on the front of the upper structure. 50. Remove Tool (A) from the machine. 51. Fill the hydraulic oil tank with oil to the correct level. See the 350 & 350 L Excavators Operation & Maintenance Manual, Form No. SEBU6725 for the correct filling procedure. 52. Start the machine, and straighten it out. 53. Reinstall right hand boom cylinder (9). See the topic "Remove & Install Boom Cylinders" in this module. 54. Remove Tooling (C) from under the rear of the machine. 55. Remove Tooling (B) from under the stick. https://127.0.0.1/sisweb/sisweb/techdoc/techdoc_print_page.jsp?returnurl=/sisweb/siswe... 2022/3/7
w 10/10(W) 56. Put 4C-5593 Thread Lubricant on the threads of the remainder of the bolts (8) that hold the upper structure and the undercarriage frame assembly together. Install the remainder of the bolts and tighten them. The machine can be rotated to the left or right to make access to all bolts (8) easier. Tighten all bolts (8) to a final torque of 1000 125 N m (750 90 lb ft). 57. Reinstall two threaded rods (3) in the final drive. 58. Remove cover assembly (5) from each final drive. 59. Put ring gear (7) in position in cover assembly (5). Make sure all of the mounting holes in both components are in alignment with each other. Put 9S-3263 Thread Lock on the threads of 10 socket head bolts (6) that hold the ring gear in place. Install the socket head bolts, and tighten them evenly. 60. Make sure the machined surface of the ring gear on the final drive is thoroughly clean, free of dirt and debris and is dry. Put 1U-8846 Gasket Maker around the machined surface of the ring gear. Using two persons, put cover assembly (5) in its original position on the ring gear. It will be necessary to rotate the cover back and forth to engage to planetary gears of the outer carrier assembly in the final drive with the ring gear in cover assembly (5). 61. Put a thin coat of 9S-3263 Thread Lock on the threads of 20 bolts (4) that hold cover assembly (5) in position. Install the 20 washers and bolts. Tighten the bolts evenly to a torque of 570 79 N m (420 60 lb ft). 62. Repeat Steps 51 through 55 for the other final drive. 63. Fill each final drive with oil to the correct level. See the 350 & 350 L Operation & Maintenance Manual for the correct filling procedure. End By: a. install bucket Copyright 1993 - 2022 Caterpillar Inc. Mon Mar 7 13:27:10 UTC+0800 2022 All Rights Reserved. Private Network For SIS Licensees. https://127.0.0.1/sisweb/sisweb/techdoc/techdoc_print_page.jsp?returnurl=/sisweb/siswe... 2022/3/7
w 1/3(W) Shutdown SIS Previous Screen Product: EXCAVATOR Model: 350-A EXCAVATOR 2ZL Configuration: 350 & 350 L Excavators 2ZL00001-UP (MACHINE) POWERED BY 3306 Engine Disassembly and Assembly 350 AND 350 L EXCAVATOR MACHINE SYSTEMS Media Number -SENR6148-04 Publication Date -01/11/2004 Date Updated -12/03/2010 SENR61480042 Swing Gear & Bearing SMCS - 7063-010 Remove & Install Swing Gear & Bearing Start By: a. remove undercarriage frame assembly Typical Example 1. Put an alignment mark on the swing gear and bearing and the undercarriage frame assembly for assembly purposes. 2. Remove 67 bolts (2) that hold swing gear and bearing (1) to the undercarriage frame assembly. https://127.0.0.1/sisweb/sisweb/techdoc/techdoc_print_page.jsp?returnurl=/sisweb/siswe... 2022/3/7
w 2/3(W) Typical Example 3. Fasten Tool (A) to the swing gear and bearing with suitable size bolts, washers and nuts as shown. Remove swing gear and bearing (1) from the undercarriage frame assembly. The weight of the swing gear and bearing is approximately 816 kg (1800 lb). Typical Example 4. Tape over the sealing surfaces of the dust seals, the inner race and the outer race. This will prevent cleaning solvent from entering the cross sections of the dust seals. Thoroughly clean the swing gear and bearing. 5. Remove dust seals (3) and (4) from the outer and inner races of the swing gear and bearing. 6. Clean the sealing grooves of the inner and outer races with fine grift sandpaper; then use a cleaning solvent to clean the seal grooves. Make sure the seal grooves are thoroughly clean and dry prior to installing new dust seals. NOTE: The following steps are for the installation of the swing gear and bearing. 7. Lay a new dust seal (3) around the outer race to determine the required length. Cut the new seal approximately 1 cm (0.3937 in) shorter than the required length. Cut the seal at a 90 degree angle. Use a file to smoothen the cross section cut of the seal. https://127.0.0.1/sisweb/sisweb/techdoc/techdoc_print_page.jsp?returnurl=/sisweb/siswe... 2022/3/7
w 3/3(W) 8. Install new dust seal (3) in the outer race using 8T-9021 Adhesive. Make sure to put adhesive on the cross section cut in the seal. Install the seal with the lip facing as shown in illustration C30014P1. 9. Install a new dust seal (4) in the inner race. Follow the same procedure as in Steps 7 and 8. 10. Lubricate the swing gear and bearing with grease. 11. Clean the mating surface for the swing gear and bearing on the undercarriage frame assembly. Put 1U-8846 Gasket Maker on the mating surface. Fasten Tool (A) and a hoist to swing gear and bearing (1), and put it in its original position on the undercarriage frame assembly. Make sure the stamp mark "S" on the inner race is positioned as shown, relative to the undercarriage frame assembly and the stopper on the outer race. 12. Put a thin coat of Loctite 277 on the threads of 67 bolts (2). Install bolts (2) that hold the swing gear and bearing to the undercarriage frame assembly. Tighten the bolts to a torque of 900 100 N m (660 75 lb ft). 13. Add 5P-0960 Multipurpose Grease to the swing gear and bearing. Refer to the 350 & 350 L Excavators Operation & Maintenance Manual for lubricating the swing gear and bearing at specific service intervals. End By: a. install undercarriage frame assembly Copyright 1993 - 2022 Caterpillar Inc. Mon Mar 7 13:28:06 UTC+0800 2022 All Rights Reserved. Private Network For SIS Licensees. https://127.0.0.1/sisweb/sisweb/techdoc/techdoc_print_page.jsp?returnurl=/sisweb/siswe... 2022/3/7
w 1/6(W) Shutdown SIS Previous Screen Product: EXCAVATOR Model: 350-A EXCAVATOR 2ZL Configuration: 350 & 350 L Excavators 2ZL00001-UP (MACHINE) POWERED BY 3306 Engine Disassembly and Assembly 350 AND 350 L EXCAVATOR MACHINE SYSTEMS Media Number -SENR6148-04 Publication Date -01/11/2004 Date Updated -12/03/2010 SENR61480043 Hydraulic Oil Tank SMCS - 5056-010 Remove & Install Hydraulic Oil Tank NOTE: Access to the cover assemblies under the hydraulic oil tank and the mounting hardware on the underside of the hydraulic oil tank is easier if the machine is swung 90 degrees to the right or left. At operating temperature, the hydraulic oil tank is hot and under pressure. Hot oil can cause burns. To prevent possible personal injury, release the pressure in the implement hydraulic circuits (boom, stick and bucket) before any hydraulic lines or components are disconnected or removed. https://127.0.0.1/sisweb/sisweb/techdoc/techdoc_print_page.jsp?returnurl=/sisweb/siswe... 2022/3/7
w 2/6(W) 1. Release the pressure in the hydraulic system as follows: a. Fully retract the rod in the stick cylinder. b. Adjust the position of the bucket so it will be flat on the ground when the boom is lowered. c. Lower the boom until the bucket is flat on the ground. d. Shut off the engine, and put the hydraulic activation control lever in the "Lock" position. e. Move the control levers for the boom, bucket, stick and swing through their full travel strokes. This will relieve any pressure that may be present in the pilot system. f. Slowly loosen the air breather cap on the hydraulic oil tank to release the pressure. g. Tighten the air breather cap on the hydraulic oil tank. h. The pressure in the hydraulic system has now been released. Lines and components can now be removed. 2. Remove 10 bolts (1), the washers and spacers that hold two cover assemblies (2) in position. Remove the two cover assemblies from under the hydraulic oil tank. View From Under Hydraulic Oil Tank 3. Remove drain plug (3) to drain the oil from the hydraulic oil tank into a suitable container for storage or disposal. The capacity of the hydraulic oil tank is 240 liters (63.3 U.S. gal). https://127.0.0.1/sisweb/sisweb/techdoc/techdoc_print_page.jsp?returnurl=/sisweb/siswe... 2022/3/7
Suggest: If the above button click is invalid. Please download this document first, and then click the above link to download the complete manual. Thank you so much for reading
w 3/6(W) View From Under Hydraulic Oil Tank 4. Remove four bolts (4) and the washers that hold the tube assembly to the bottom of the hydraulic oil tank. 5. Remove four bolts (5), the washers and hydraulic oil filter (6) from the side of the hydraulic oil tank. Position the hydraulic oil filter out of the way of the hydraulic oil tank. 6. Put identification marks on two hose assemblies (7). Disconnect the two hose assemblies from the side of the hydraulic oil tank. View From Back Side Of Hydraulic Oil Tank 7. Put identification marks on two wires (8) as to their location on the sending unit. Disconnect the two wires from the sending unit. https://127.0.0.1/sisweb/sisweb/techdoc/techdoc_print_page.jsp?returnurl=/sisweb/siswe... 2022/3/7
w 4/6(W) 8. Remove four bolts (9), and disconnect tube assembly (10) from the side of the hydraulic oil tank. 9. Disconnect hose assemblies (11) and (12) from the back side of the hydraulic oil tank. 10. Remove six bolts (13) and the washers that hold cover assembly (14) in position above the hydraulic oil tank. Remove the cover assembly. View From Under Hydraulic Oil Tank 11. Remove four bolts (15) and the spacers that hold the hydraulic oil tank to the frame of the machine. https://127.0.0.1/sisweb/sisweb/techdoc/techdoc_print_page.jsp?returnurl=/sisweb/siswe... 2022/3/7
https://www.ebooklibonline.com Hello dear friend! Thank you very much for reading. Enter the link into your browser. The full manual is available for immediate download. https://www.ebooklibonline.com