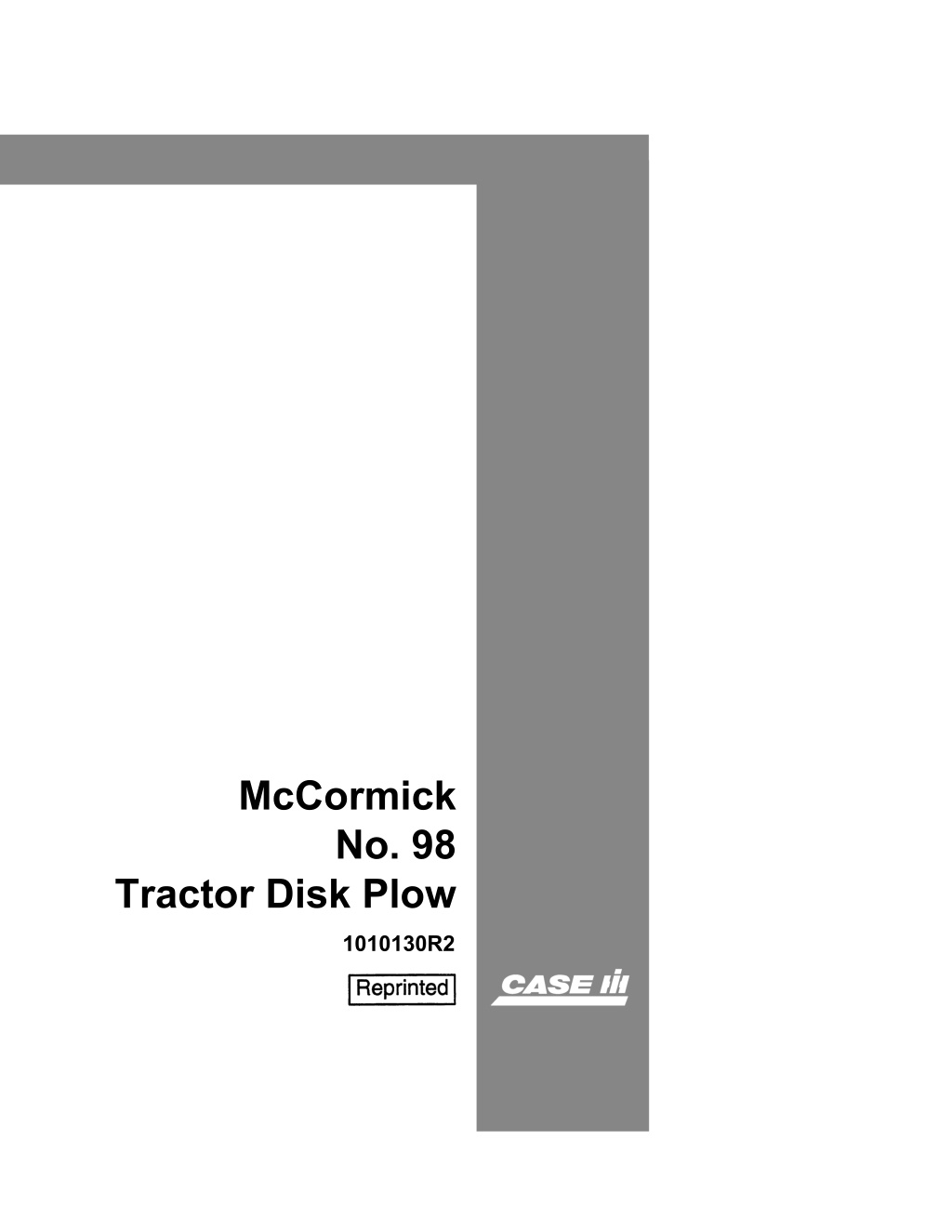
Case IH McCormick No.98 Tractor Disk Plow Operator’s Manual Instant Download (Publication No.1010130R2)
Please open the website below to get the complete manualnn//
Download Presentation

Please find below an Image/Link to download the presentation.
The content on the website is provided AS IS for your information and personal use only. It may not be sold, licensed, or shared on other websites without obtaining consent from the author. Download presentation by click this link. If you encounter any issues during the download, it is possible that the publisher has removed the file from their server.
E N D
Presentation Transcript
McCormick No. 98 Tractor Disk Plow 1010130R2
THIS SAFETY ALERT SYMBOL INDICATES IMPORTANT SAFETY it ALERT TO THE POSSIBILITY OF PERSONAL INJURY OR DEA TH. MESSAGES IN THIS MANUAL. WHEN YOU SEE THIS SYMBOL, , CAREFULL Y READ THE MESSAGE THA T FOLLOWS AND BE M171B If Safety Decals on this machine use the words Danger, Warning or Caution, which are defined as follows: DANGER: Indicates an immediate hazardous situation which if not avoided, will result in death or serious injury. The color associated with Danger is RED. WARNING: Indicates an potentially hazardous situation which if not avoided, will result in serious injury. The color associated with Warning is ORANGE. CAUTION: Indicates an potentially hazardous situation which if not avoided, may result in minor or moderate injury. It may also be used to alert against unsafe practices. The color associated with Caution is YELLOW. If Safety Decals on this machine are ISO two panel Pictorial, decals are defined as follows: The first panel indicates the nature of the hazard. The second panel indicates the appropriate avoidance of the hazard. Background color is YELLOW.I\:\ it WARNING IMPROPER OPERATION OF THIS MACHINE CAN CAUSE INJURY OR DEATH. BEFORE USING THIS MACHINE, MAKE CERTAIN THAT EVERY OPERATOR: Prohibition symbols such as \::::I X and e if used, are RED. Is instructed in safe and proper use of the machine. Reads and understands the Manual(s) pertaining to the machine. Reads and understands ALL Safety Decals on the machine. Clears the area of other persons. Learns and practices safe use of machine controls in a safe, clear area before operating this machine on a job site. It is your responsibility to observe pertinent laws and regulations and follow Case Corporation instructions on machine operation and maintenance. Bur 0-00000 2001 Case Corporation March, 1995 (Revised October, 1997) CASE and IH are registered trade marks of Case Corporation
SETTING UP INSTRUCTIONS tH 14 VUJI. 11 nl- ..,tltMAl McCORMICK No. 98 Tractor Disle . Plow
https://www.ebooklibonline.com Hello dear friend! Thank you very much for reading. Enter the link into your browser. The full manual is available for immediate download. https://www.ebooklibonline.com
Accidents can he prevented with your help No accident-prevention program can be successful without the wholehearted co-operation of the person who is directly respon- sible for the operation of equipment. To read accident reports from allover the country is to be convinced that a large number of accidents can be prevented only by the operator anticipating the result before the accident is caused and doing something about it. No power-driven equip- ment, whether it be transportation or processing. whether it be on the highway, in the harvest field or in the industrial plant, can be safer than the man who is at the controls. If accidents are to be prevented-and they can be prevented-it will be done by the operators who accept a full measure of their responsibility. It is true that the designer, the manufacturer, the safety engineer can help; and they will help, but their combined efforts can be wiped out by a single careless act of the operator. It is said that "'he be.t kind oj" Mj_ty _we i. fJ cMeJul operator:' We ask you to be that kind of an operator. NATIONAL SAFETY COUNCIL
110. 98 Tractor lliak Plows ara bu i It In the following sizu: Three-Furrow, No. 98 3 Ho. 98-1l3 Four-furrow Bdjll,table to Three-Furrow. 110. 98-53 rive-Furrow adjustable to Three or four-Furrow. No. 96-5 Five-Furrow. No. Six-furrow adjustable to five-Furrow. 9 8 ~ 6 5 No. 96-75 Seven-Furrow adjustable to Five-Furrow. It lust. I No. 98-5 Five-furrow 910101. All illustr,tlona and descriptive matter in thl. publica- tion a9ply to International Karvester products sold under the McCormick, MeCorlllc:k-lnternational. MeCoralick..oeerlnll, McCormick-Deering International trade n .... or
INSTRUCTIONS FOR ADJUSTING AND OPERATING (Setting Up Instructiona are on page a) LUBRICATION Lubrication fittings should be screwed into place and the parts well lubricated before putting the plow into operation. Use the pressure lubri- cating gun furnished with the tractor, using good quality lubricant. All parts with lubrication fittings ahould be filled with lubricant, that is, force the lubricant in until it shows on the outside of the part. Moving parts which do not have tittings should be lubricated daily with oil. for special care of disk bearings, see page 7. When operating the plow, fittings located in the tollowing parts Should be lubricated at least as often as designated below: LUBRICATE IfAl LY Rear axle bracket (2). Raising gear (2). Raising clutch (1). Land wheel box, inside (2). Land wheel box, outside (+). Front axle bracket (1). Clutch wheel (1). Raising arm swivel (2). Depth adjusting pipe (1). Rear raising arm knuokle (2). Frant adjusting lever quadrant bracket (1). Front furrow wheel boxes (2). Rotary scraper bracket on bearing (Speoial) (1) . LUBRICATE TWICE DAILY Rear furrow wheel boxes (2). Disk bearing brackets (1 in each disk). REMOVE THE VARNISH BEFORE STARTING PLOW Disks and scrapers are finished to give them a high polish and are varnished before leaving the factory to prevent them from rusting. Good work cannot be accolllPUehed until the varnish is removed. VARMISH REMOVER: The method recommended is to USe a regular prepared varnish remover whieh ean be obtained frOil almost any store handling a line of paints. CONCENTRATED LYE: Another method is to procure ordinary concentrated lye and mix it with water, making the liquid strong enough to remove the varnish. One small can of ordinary lye to one quart of water will be suffioient to remove the varnish from one disk. The lye may be applied by cloth or waste attached on the end of a stick. After applying the lye, let it stand for a few minutes, and if necessary, repeat the operation. CAUTION! Lye is poisonous and should be kept away fro. the face, hands and clothing. The plow should be used immediately, or the finished surfaces should be thoroughly covered with lubricant to prevent them trom rusting. ~ ~ i c h e v e r method 1s followed, be sure that all varnish is removed beJ fore trying to plow.
5 G IIEUL Nuts on all bolts must be kept perfectly tight. Spread all cotters to keep them from falling out. OPEN IHG UP hen opening up, raise front lever to top of ratchet and adjust rear adjusting screw to whatever depth is desired. Atter the first round has been ~ d e , level with the previous furrow. lower the front lever to such posItion that the disks will cut RAISING AND LOWERIKG To lower the plow into the ground, pull the trip rope; to raise the plow pull the same rope. Do not hold the rope atter the clutch begins to operate or the clutch may repeat its operation. Regulate tension on lifting springs so that the plow will lift out of the ground without the wheel sliding. If the wheel slips when enter- ing the ground, there is too much tension. SPRIIfGS Do not forget to properly tension the lift springs. The proper ten- sion on the lift spring will make it easy to operate the depth regulating lever, will balance the plow when being raised, and w111 prevent the wheel "rom slipping or sliding. LUERS An adjusting lever is provided for raising and lowering the front end of the plow. An adjusting screw crank is provided for the rear furrow wheel to regulate the penetration in hard or soft ground. HITCHIKG Move hitch in and out on the drawbar untU the .front disk is cutting the deSIred width. If a finer adjustment is desired than can be obtained on the drawbar, swing the drawbar bracket by removing the top belt in the hitch plate. Adjust the front furrow connecting link until the front furroVi wheel runs straight.
DI Sit SCRAPERS Three types of sorapers are provided for use on the plow. They are the Moldboard Type. Rotary Type, and Oscillating Type. Til. Moldboard TYII' Scra"er. (Htusts. 20 and 28J are intended for average oonditions where the soil is not very stiCky. When plowing in wet or in sticky conditions be sure to set this type of scraper up close to tne face of the disk. It this is not done the so11 w111 gradually force the scraper away frOll\ the disk. This type of scraper is especially de- signed to do a good covering Job. In setting the Moldboard scraper, it Is well to have the end of the scraper extend neerly to the oenter of the disk. The lower edge of the scraper should be set nearly touching the disk on the inside edge, and ex- tend out to give l/Sft to 3/16" clearance at the outside edge of the disk. Th, Rotary Type Scraperl (Illust. 31) are intended for certain kinds of soil which w111 build up on the disk face and foroe stationary scrapers away from the disk. These scrapers also reduce friction to a lIt1nuum. The O,clll.tlns Type Serape" daDIp, sticky Boll and tor use under damp, sticky conditions, as they clean readily in damp soll. (IlZuat. 22) are intended for use in a Ad.Just scrapn blades to fit disks olosely but not tIght enough to cause friction. It scrapers are too close, loosen large nut on eyebolt slightly, turn rear set serew back and screw down a little on front set sorew. If soraper blades do not fit olose enough to the disks, turn front set screw back and tighten rear set screw, Arter scrapers are adjusted, tighten nuts on eye- bolts. The SpecIal Moldboard Type Scraper. fIt lust. 28) may be a.dJusted in or out on the scraper arm by loosening or tightening the lerge nut on the scraper arm. By loosening or tightening the set screws in the scraper arm braoket, the scraper may be adjusted out or in toward the oenter 01' the disk.
Suggest: If the above button click is invalid. Please download this document first, and then click the above link to download the complete manual. Thank you so much for reading
7 DISK BEARINGS The angle of the disk can be changed to .eet the varying soil conditions by changing the location of the top bolt in the disk bearing. For ordinary plowing conditions, the bolt should be placed in hole "An as shown ill Iltust. 2. Where the ground is very hard and difficult to penetrate, the top bolt in the disk bearing should be placed in hole "B" 111ust. 2 ROLLER BEARINGS These bearings are double race TImken bearings, protected by a felt washer and steel dust ring. An adjustable castle nut 1s provided inside the rear cap, whereby the slack may be taken out of the bearing. These bearings should be kept snuk but not tight. Keep these roller bearings packed with lubricant and they will last indefinitely. VERY IMPOnAHl CARE OF DISK BEARINGS Ha{ore the start of every plowlnc scason each dlsR beartn, should be taken apart and all old lubricant r oved and the enttre b e a r t n ~ chorauthlu leaned as f o l l o ~ s : The felt washer should be removed and then all parts of the b o a r t n ~ 8 . that is, the dIsk bearing bracket disk SPindle, roller bearings, castle nut, washer. etc. ahould be thorouihlV'washed with RerOStl'lll to remove all of the old lubr!cant and dtrt. It is very important to clean out all of the old lubricant as it is full of firt and grit Which, if allowed to remain in the bearing, Vl11l cauae the parts to wear rapIdly. The {cIt dust washer s/lould be washed cteon tn kerosene and worked until BortanGd Gnd ,luffed up. 80 that It will seal the baartne well wilen replaced. This is very important, as the felt washer is apt to become dry and hardened and, if left in this condition; will allow dirt and grit to work into the bearing. After thoroughly cleaning all parts of the bearing, the parts should all be packed well with new lubricant and reassembled. The castle nut on the disk spindle should be tightened as tight as possible and still allow the spindle to turn, as the bearing parts will wear rapidly if left too loose. Be sure to replace the cotter through castle nut and disk spindle before replacing bearing cap. After reassembling the bearing, use the pressure lubricating gun on the fitting and force the lubricant into the bearing until the new lubri- cant starts to ~ o m e out of the bearing.
https://www.ebooklibonline.com Hello dear friend! Thank you very much for reading. Enter the link into your browser. The full manual is available for immediate download. https://www.ebooklibonline.com