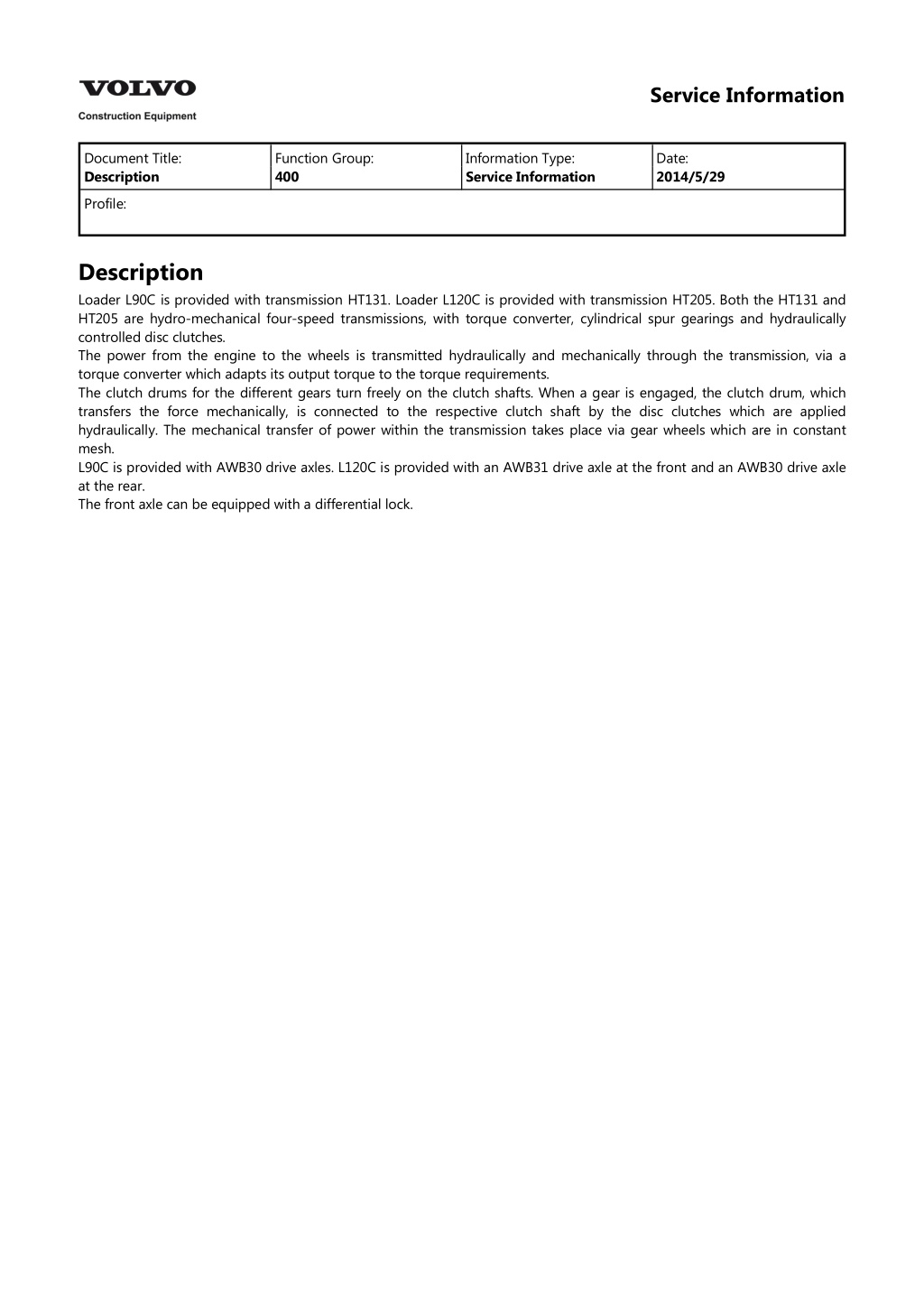
Volvo BM L90C OR Wheel Loader Service Repair Manual Instant Download
Please open the website below to get the complete manualnn// n
Download Presentation

Please find below an Image/Link to download the presentation.
The content on the website is provided AS IS for your information and personal use only. It may not be sold, licensed, or shared on other websites without obtaining consent from the author. Download presentation by click this link. If you encounter any issues during the download, it is possible that the publisher has removed the file from their server.
E N D
Presentation Transcript
Service Information Document Title: Description Function Group: 400 Information Type: Service Information Date: 2014/5/29 Profile: Description Loader L90C is provided with transmission HT131. Loader L120C is provided with transmission HT205. Both the HT131 and HT205 are hydro-mechanical four-speed transmissions, with torque converter, cylindrical spur gearings and hydraulically controlled disc clutches. The power from the engine to the wheels is transmitted hydraulically and mechanically through the transmission, via a torque converter which adapts its output torque to the torque requirements. The clutch drums for the different gears turn freely on the clutch shafts. When a gear is engaged, the clutch drum, which transfers the force mechanically, is connected to the respective clutch shaft by the disc clutches which are applied hydraulically. The mechanical transfer of power within the transmission takes place via gear wheels which are in constant mesh. L90C is provided with AWB30 drive axles. L120C is provided with an AWB31 drive axle at the front and an AWB30 drive axle at the rear. The front axle can be equipped with a differential lock.
Service Information Document Title: APS II (Automatic Power Shift with Mode Selector) Function Group: 420 Information Type: Service Information Date: 2014/5/29 Profile: APS II (Automatic Power Shift with Mode Selector) Description L90C and L120C are, as standard, provided with APS II (Automatic Power Shift with shift Mode Selector [ 1] included in the Contronic System control unit. The following positions are available: LIGHT: (first position) The machine shifts at low engine speed, suitable for transport operations without load. LIGHT: (second position) The machine shifts at a slightly higher speed than the first position, suitable for transport operations and lighter loading / carrying work. NORMAL: Is used for "normal handling" and operation. HEAVY: The machine shifts at higher engine speeds, suitable for heavier work. MAN: Gear shifting is operated manually by the operator using the gear selector. , which is Figure 1 Shift Mode Selector SW143 positioned on the front panel Description of function during manual gear shifting Mode Selector SW143 placed in position "MAN" Gears are selected manually by turning the gear selector to the required gear position. Changing travelling direction After changing travelling direction, the machine starts off in the previously selected gear. NOTE!
As a safety precaution, upshifting to a higher gear takes place if a certain critical travelling speed and/or engine speed is exceeded. Description of function during automatic gear shifting Mode selector SW143 placed within the "AUTOMATIC" range The gear selector placed in the 3rd or 4th gear position. When starting from stationary this takes place in 2nd gear and, if the machine is rolling, it will start off in 3rd gear. The gear shifting is automatic. Conditions required to cause gear shifting is a combination of the setting of the Mode Selector, travelling speed and engine speed. Gear shifting between gears, Forward: 2nd - 3rd - 4th, Reverse: 2nd - 3rd For gear shifting down to 1st gear, see "Kick-down function". Changing travelling direction Changing travelling direction at low speed takes place in 2nd gear. If the speed is too high, 3rd gear will first be engaged and then, when the speed has dropped, 2nd gear will be engaged. Engine braking / downshifting 2nd gear is the basic gear and the gear which the machine always starts off in when operating with the selector set in 3rd or 4th gear position. During engine retarding, the accelerator control should be let up fully and the engine braking / down-shift button SW105, should be pressed in. Downshifting then takes place in stages, with one gear for each time the button is pressed, from 4th to 3rd and from 3rd to 2nd, if the travelling speed is then below 22 km/h (13.7 mph). For a further downshifting to 1st gear, see "Kick-down function". If engine braking / down-shift button, SW105, is kept pressed in while the accelerator is actuated, upshifting is prevented. Over-speeding protection When downshifting, the control programme always first checks that the travelling speed is not too high for the selected gear. If it is too high, the engaged gear will be retained until the travelling speed has dropped to a permissible level. Kick-down function Kick-down means shifting down to 1st gear by activating the kick-down function with SW90 on the selector control, or SW105 on the control lever carrier. The timing of the downshift to 1st gear depends on the setting of the shift Mode Selector, the engine speed and the travelling speed. 1st gear will be engaged if the travelling speed of the machine is sufficiently low or if the travelling speed, within 8 seconds from that kick-down has been activated, becomes sufficiently low. When 1st gear is engaged, this is indicated by a pip from the buzzer. In order to shift up to 2nd gear, the kick-down button must again be actuated. NOTE! As a safety precaution, upshifting to a higher gear takes place if a certain critical travelling speed and/or engine speed is exceeded. [ 1]*) APS II with Mode Selector SW143 on the front panel is a gear-shifting programme which is adjustable for different operating and working conditions.
https://www.ebooklibonline.com Hello dear friend! Thank you very much for reading. Enter the link into your browser. The full manual is available for immediate download. https://www.ebooklibonline.com
Service Information Document Title: Gear selector valve Function Group: 420 Information Type: Service Information Date: 2014/5/29 Profile: Gear selector valve Figure 1 1. 2. 3. Pressure connection from transmission pump Connection to valve spool Return to tank When the solenoid is not activated, the valve spool control side is connected to tank via the solenoid (connection 2 - 3). The return spring, which is positioned on the opposite side, presses the valve spool toward the solenoid, see fig. [Invalid linktarget] . When the solenoid is activated, the solenoid core closes connection 3 to tank, the connection from the pump to the valve spool is opened (connection 1 - 2), the valve spool is pressed over to the opposite side, see fig. 4.
Service Information Document Title: Operating with the ecu disconnected Function Group: 420 Information Type: Service Information Date: 2014/5/29 Profile: Operating with the ecu disconnected Op nbr Nipple, part no. 957030, 2 pcs for operating forward, 4 pcs for operating rearward Hose, part no. 13932807, 1 pcs for operating forward, 2 pcs for operating rearward WARNING when operating with the ecu disconnected, the gear will be applied immediately the engine is started, therefore keep the service brakes applied when starting the engine. Operating forward with the ecu disconnected 1. Remove the pressure checking point for the main pressure, fig. [Invalid linktarget] for l90c and fig. [Invalid linktarget] for l120c respectively and plug n/d on the gear selector valve fig. [Invalid linktarget] . Fit nipples part no. 957030. 2. Connect a hose part no. 13932807 between the nipples. 3. Keep the selector control in neutral position and start the engine.3rd gear forward will now be applied. 4. When operating with the ecu disconnected is no longer required, restore the check point and plugs.
Figure 1 Gear selector valve N/d valve spool, neutral - drive F/r valve spool, forward - reverse Operating rearward with the ecu disconnected 5. Remove the pressure checking points for the main pressure and the 3rd clutch pressure on the checking panel, fig. [Invalid linktarget] and fig. [Invalid linktarget] for l90c and fig [Invalid linktarget] for l120c respectively as well as plugs n/d and f/r on the gear selector valve fig. [Invalid linktarget] . Fit nipples part no. 957030. 6. Connect a hose part no. 13932807 between the outlet for the main pressure on the checking panel and the outlet n/d on the gear selector valve. Connect the other hose between the pressure outlet for the 3rd clutch on the checking panel and outlet f/r on the gear selector valve. 7. Keep the selector control in neutral position and start the engine.3rd gear reverse will now be applied. 8. When operating with the ecu disconnected is no longer required, restore the check points and the plugs.
Service Information Document Title: Symbol diagram HT131 Function Group: 420 Information Type: Service Information Date: 2014/5/29 Profile: Symbol diagram HT131 Figure 1 Symbol diagram HT131 A PM PC PL N/D F/R H/L 1/2 3/4 R1 R2 S1 S2 Pressure-reducing valve, input torque converter pressure Check point, main pressure Check point, torque converter pressure Check point, lubricating oil pressure Selector spool, neutral - drive Selector spool, forward - reverse Selector spool, high - low Selector spool, 1st - 2nd Selector spool, 3rd - 4th Damping valve, forward gear Damping valve, reverse gear Solenoid, neutral - drive Solenoid, forward - reverse
S3 S4 S5 1 2 3 4 F R Solenoid, high - low gear Solenoid, 1st - 2nd gear Solenoid, 3rd - 4th gear 1st disc clutch 2nd disc clutch 3rd disc clutch 4th disc clutch Forward gear disc clutch Reverse gear disc clutch The gear-shifting diagram shows the solenoids which areactivated for the respective gears. For instance, for 1F, solenoids S1, S3 and S4 are activated.
Service Information Document Title: Symbol diagram HT205 Function Group: 420 Information Type: Service Information Date: 2014/5/29 Profile: Symbol diagram HT205 Figure 1 Symbol diagram HT205 PM PC PL N/D F/R H/L 1/2 3/4 R1 R2 S1 S2 Check point, main pressure Check point, torque converter pressure Check point, lubricating oil pressure Selector spool, neutral - drive Selector spool, forward - reverse Selector spool, high - low Selector spool, 1st - 2nd Selector spool, 3rd - 4th Damping valve, forward gear Damping valve, reverse gear Solenoid, neutral - drive Solenoid, forward - reverse gear
S3 S4 S5 1 2 3 4 F R Solenoid, high - low gear Solenoid, 1st - 2nd gear Solenoid, 3rd - 4th gear 1st disc clutch 2nd disc clutch 3rd disc clutch 4th disc clutch Forward gear disc clutch Reverse gear disc clutch The gear-shifting diagram shows the solenoids which areactivated for the respective gears. For instance, for 1F, solenoids S1, S3 and S4 are activated.
Service Information Document Title: Checking transmission Function Group: 421 Information Type: Service Information Date: 2014/5/29 oil pressures, Profile: Checking oil pressures, transmission Op nbr 42102 11 666 017 Pressure gauge, range 0 - 0.6 MPa (0 - 87 psi) 11 666 018 Pressure gauge, range 0 - 2.5 MPa (0 - 363 psi) 11 666 035 Hose 999 3721 Service display unit 930032 Measuring nipple L90C Main pressure (neutral): 1.45 - 1.68 MPa (210 - 244 psi) Clutch pressure, 1st - 4th 1.35 - 1.58 MPa (196 - 229 psi) Clutch pressure, Forward - Reverse: 1.35 - 1.58 MPa (196 - 229 psi) Torque converter pressure, (out, neutral): 0.57 - 0.69 MPa (83 - 100 psi) Lubricating oil pressure, (neutral): 0.35 - 0.45 MPa (51 - 65 psi) L120C Main pressure (neutral): 1.37 - 1.58 MPa (199 - 229 psi) Clutch pressure, 1st - 4th 1.37 - 1.58 MPa (199 - 229 psi) Clutch pressure, Forward - Reverse: 1.37 - 1.58 MPa (199 - 229 psi) Torque converter pressure, (out, neutral): 0.20 - 0.50 MPa (29 - 73 psi) Lubricating oil pressure, (neutral): 0.16 - 0.22 MPa (23 - 32 psi) The following applies when checking: Temperature: Normal operating temperature Speed: High idling speed Use measuring nipple 930032 where it is not already mounted. NOTE! When checking the pressures, apply service brakes and parking brake. Also make sure that the transmission disengagement function is not activated. NOTE! To be able to check the clutch pressure for the 4th gear, without activating the automatic shifting, the ECU must be disconnected, see Fig. [Invalid linktarget] .
1. Figure 1 Disconnecting ECU 1. 2. Connector EY should be disconnected from the circuit board Connector EA should be disconnected from ECU and connected on the circuit board, to connector EZ 2. Remove the lining from the rear cab wall so that the electrical distribution box is accessible. 3. Disconnect the ECU by removing connector EY (blue leads) from the circuit board. 4. Disconnect connector EA (yellow) from the control unit and connect it to connector EZ (yellow) on the circuit board. L90C Main pressure (alternative 1) 5. The main pressure can be read off with the aid of the service display unit. 6. Connect service display unit 3721 to connector IA on the steering wheel column. 7. The gear selector should be in neutral position, and the engine running at high idling speed. Main pressure (alternative 2)
8. Figure 2 Gear selector valve 1. Pressure outlet main pressure Connect pressure gauge 11 666 018 to the pressure outlet on the gear selector valve, positioned behind the cover door on the left side, see Fig. [Invalid linktarget] 9. The gear selector should be in neutral position, and the engine running at high idling speed. Clutch pressure, 1st - 4th gear 10. Connect pressure gauge 11 666 018 to pressure outlets items 1, 2, 3, or 4, see Fig. [Invalid linktarget] 11. With the gear selector in the position for the respective gears, check in both forward and reverse gear at high idling speed. Clutch pressure, forward and reverse gear 12. Connect pressure gauge 11 666 018 to pressure outlet items F or R, see Fig. [Invalid linktarget] 13. With the gear selector in forward or reverse position respectively, with 3rd gear engaged and engine running at
high idling speed. Lubricating oil pressure 14. Figure 3 Under the entry step on the left side of the machine R F 1 2 3 Pressure outlet reverse gear Pressure outlet forward gear Pressure outlet 1st gear Pressure outlet 2nd gear Pressure outlet 3rd gear (provided with quick-action coupling) Pressure outlet 4th gear Pressure outlet, lubricating oil pressure (provided with quick-action coupling) 4 5 Connect pressure gauge 11 666 017 to pressure outlet item 5 Fig. [Invalid linktarget] . High idling speed. Torque converter pressure
15. Figure 4 1 Pressure outlet, torque converter valve Connect pressure gauge 11 666 017 to the pressure outlet on the torque converter delivery valve, positioned behind the cover door on the right side, see Fig. [Invalid linktarget] . 16. The gear selector in neutral position, high idling speed. 17. After the pressure checks have been completed, reconnect the connectors in the electrical distribution box and re- fit the wall lining. 18. Clutch pressure diagram Lubricati ng oil Torque converte r Main pressure Clutch pressure F B 1 2 3 4 N 1F 2F X X X X X X X X X 0 X X 0 0 0 0 X 0 0 0 X X 0 0 0 0 0
3F 4F 1R 2R 3R 4R X X X X X X X X X X X X X X X X X X X X 0 0 0 0 0 0 X X X X 0 0 X 0 0 0 0 0 0 X 0 0 X 0 0 0 X 0 0 X 0 0 0 X X = Pressure 0 = Without pressure Any operating problems caused by internal leakage in the gear selector valve or between clutch shaft and oil distributor, can be determined if all the different pressures for the transmission are checked at the same time as described above. L120C Main pressure (alternative 1) 19. The main pressure can be read off with the aid of the service display unit. 20. Connect service display unit 3721 to connector IA on the steering wheel column. 21. The gear selector should be in neutral position and the engine running at high idling speed. Main pressure (alternative 2) 22. Figure 5 Under the entry step on the right side of the machine 1 2 3 Pressure outlet 1st gear Pressure outlet 2nd gear Pressure outlet 3rd gear (provided with quick-action coupling) Pressure outlet 4th gear Pressure outlet reverse gear Pressure outlet forward gear Pressure outlet main pressure (provided with quick- action coupling) 4 R F H Connect pressure gauge 11 666 018 to the pressure outlet item 7, see Fig. [Invalid linktarget] . 23. The gear selector should be in neutral position and the engine running at high idling speed. Clutch pressure, 1st - 4th gear
24. Connect pressure gauge 11 666 018 to the pressure outlets items 1, 2, 3 or 4 (certain markets only 3) see Fig. [Invalid linktarget] . 25. The gear selector should be in the position for the respective gears. Check in both forward and reverse position with the engine running at high idling speed. Clutch pressure, forward and reverse gear 26. Connect pressure gauge 11 666 018 to items F or R, see Fig. [Invalid linktarget] . 27. The gear selector should be in forward or reverse position respectively with 3rd gear engaged and the engine running at high idling speed. Torque converter pressure and lubricating oil pressure 28. Figure 6 1. 2. Lubricating oil pressure Torque converter pressure Connect pressure gauge 11 666 017 on the left side of the transmission, item 1 lubricating oil pressure, or item 2 torque converter pressure, see Fig. [Invalid linktarget] . 29. The gear selector should be in neutral position and the engine running at high idling speed. 30. NOTE! The torque converter pressure depends on temperature, speed and the resistance in the system which varies, but is limited at its lowest by the lubricating oil pressure and at its highest by the safety valve which opens at 0.8 MPa (116 psi). 31. After the pressure checks have been completed, reconnect the connectors to the electrical distribution box and re- fit the wall lining. 32. Clutch pressure diagram Lubricating oil Torque converter Main pressure Clutch pressure F B 1 2 3 4 N 1F 2F 3F 4F 1R 2R 3R 4R X X X X X X X X X X X X X X X X X X X X X X X X X X X 0 X X X X 0 0 0 0 0 0 0 0 0 X X X X 0 X 0 0 0 X 0 0 0 0 0 X 0 0 0 X 0 0 X 0 0 X 0 0 0 X 0 0 0 0 0 X 0 0 0 X X = Pressure 0 = Without pressure
Any operating problems caused by internal leakage in the gear selector valve or between clutch shaft and oil distributor, can be determined if all the different pressures for the transmission are checked at the same time as described above.
Suggest: If the above button click is invalid. Please download this document first, and then click the above link to download the complete manual. Thank you so much for reading
Service Information Document Title: Differential lock, adjusting Function Group: 468 Information Type: Service Information Date: 2014/5/29 Profile: Differential lock, adjusting Op nbr 46805 E 1370 support 1. Lift both front wheels so that they can be turned freely off the ground. Support the front axle. 2. Figure 1 1. 2. E1370 Axle stands Position support (e 1370) under the lifting frame, see fig. [Invalid linktarget] . 3. Remove protective cover (17) over microswitch (18) for the differential lock, see fig. [Invalid linktarget] . 4. Remove cover (13), thrust washer (22) and diaphragm (15) above the differential lock diaphragm sleeve (7). Remove push rod (5) lock screw (8) with the aid of a 5 mm allen key. 5. Screw the diaphragm sleeve counter-clockwise until the differential lock is fully engaged, but without any pre- tension. Check by rotating one of the wheels of the machine forwards and backwards. 6. Then screw the diaphragm sleeve clockwise 4 revolutions so that the differential lock is disengaged and then lock pushrod (5) with lock screw (8). Fit diaphragm (15). 7. Fix thrust washer (22) with petroleum jelly in cover (13). Then re-fit the cover. Check that the differential lock is disengaged by rotating a wheel. 8. Adjust the differential lock microswitch as follows: loosen the lock nut (19) and screw in microswitch (18) until it just closes the circuit, the control lamp on the instrument panel lights up. Then screw out the microswitch a 1/4 of a turn, tighten down the lock nut. Re-fit the protective cover (17). 9. Remove the support under the lifting frame and remove any other supports.
Figure 2 1. 2. 3. 4. 5. 6. 7. 8. 9. Locking clamp Stud Bolt Cotter pin Pushrod Lock nut Diaphragm sleeve (thrust sleeve) Lock screw Return spring Filter Piston O-ring Cover Pressure connection Diaphragm Support washe Protective casing Microswitch Lock nut Shifter shaft Engaging sleeve Thrust washer 10. 11. 12. 13. 14. 15. 16. 17. 18. 19. 20. 21. 22.
https://www.ebooklibonline.com Hello dear friend! Thank you very much for reading. Enter the link into your browser. The full manual is available for immediate download. https://www.ebooklibonline.com