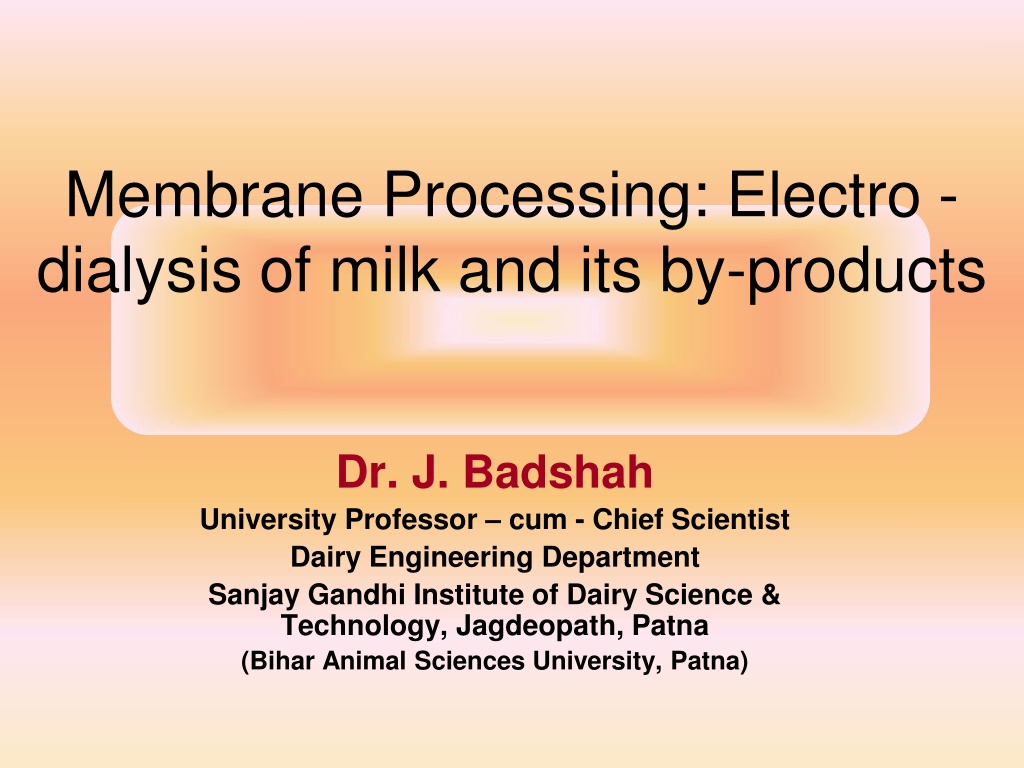
Electrodialysis in Dairy Industry: Applications and Benefits
Learn about the uses of electrodialysis (ED) in milk processing, its applications in producing various dairy products, and the benefits it offers such as demineralization, acidity adjustment, and cost savings. Discover how ED can improve the efficiency and quality of dairy manufacturing processes.
Download Presentation

Please find below an Image/Link to download the presentation.
The content on the website is provided AS IS for your information and personal use only. It may not be sold, licensed, or shared on other websites without obtaining consent from the author. Download presentation by click this link. If you encounter any issues during the download, it is possible that the publisher has removed the file from their server.
E N D
Presentation Transcript
Membrane Processing: Electro - dialysis of milk and its by-products Dr. J. Badshah University Professor cum - Chief Scientist Dairy Engineering Department Sanjay Gandhi Institute of Dairy Science & Technology, Jagdeopath, Patna (Bihar Animal Sciences University, Patna)
Applications of Electro dialysis (ED) ED of milk ingredients like Whey, UF and other Dairy Products resulted in demineralised products, which are extensively used for the production of following products: a. Infant Formula b. Breast milk Substitutes c. Nurse and Sport Nutrition products d. Ice creams e. Yoghurts f. Partial milk substitutes in own manufacturing process Low processing temperatures of 8-15 C can save ingredients
What does ED doApplications Desired demineralization level can be reached Ash can be adjusted/decreased Adjustment of Acidity Standardisation and improvement of organolettic properties such as taste of Acid whey Saving the additional cost of eco disposal of unused by-products Saving additional cost of crystallization and drying process i.e. additional profits Design Flexibility to develop usable products from by-products Reversibility of the whole ED unit provide automatic cleaning of fouling products Fully automatic process including CIP results in high efficiency
Electrodialytic Phenomena and their Applications in Dairy Industry Electrodialysis (ED) is an electrochemical separation process by which electrically-charged species are transported from one solution to another. ED is a combined method of dialysis and electrolysis and can be performed with two main cell types: i. Multi-membrane cells for dilution-concentration and water dissociation applications (membrane phenomena), ii. Electrolysis cells for redox reactions (electrode phenomena). Demineralization of milk and milk products is done by dilution- concentration method The use of ED with monopolar membrane and acid caseinate production is studied in dairy industry. for protein separation ED with bipolar membranes was applied very recently for lactic acid production from whey products fermentation, production of castion of whey proteins.
Electrodialytic Phenomena and their Applications Industry Two principle applications of electrode reactions were published: electrochemical coagulation (EC) to precipitate milk proteins, and electroreduction for the reduction of disulfide bonds in the proteins. This is the composition of milk and the lack of knowledge of redox reactions of the different food compounds that limit the applications and the development of electrolytic phenomena. Electrodialytic phenomena present a great potential for application in the dairy industry, and more generally, in the food industry; many of these applications have to be discovered.
Electrodialysis- A membrane Process Electrodialysis is a separation process that uses ion-exchange membranes under the action of an electric field (driving force) for the separation of ionic species from aqueous solutions or other neutral solutes. ED use electrical power (DC voltage) to transfer dissociated ions and other charged compounds through ions selective membranes and forming two different loops i.e. diluate and concentrate (brine) loop. Each type of membrane is permeable to only one type of ion depending upon the charge, allowing both types of ions to be removed or transferred. The compartments that have a cation-exchange membrane on one side and an anion-exchange membrane on the other. feed solution containing ions flows through several
Electrodialysis- A membrane Process Under the action of an electric field that is established between the anode and the cathode, the cations migrate into the cathode, permeating selectively through the cation-exchange membrane, while the anions migrate toward the anode permeating selectively through the anion-exchange membrane. The ionic mobility is directly proportional to specific conductivity and inversely proportional to number of molecules in solution. Anion exchange membranes carry cations groups which repel cations and are permeable to anions and vice versa. Each type of membrane is permeable to one type of ions. Thus the anions leave the gap in the direction of anode and cations leave in the direction of cathode. Both are taken up by a concentrate streams.
Electrodialysis- A membrane Process In this way, there is the transport of the salt from the feed compartment, designated also by the diluate compartment, to the concentrate under the action of the electric field, which is the driving force. The salt is retained in the adjacent compartments, also designated by concentrate compartment membranes retain the cations that are migrating towards the cathode under the electric field action while the cation-exchange membranes block the anion transport that is moving toward the anode. The ions that reach the electrodes suffer redox reactions and there is the formation of chemical compounds, which are removed by the electrodes cleaning solution. An electrodialysis cell has a diluate compartment and a concentrate compartment, that together with a pair of ion-exchange membranes, one anionic and other cationic, constitute the basic unit of this separation process. because the anion-exchange
Characterization of Ion-Exchange Membranes The ion-exchange commercial membranes are films of ion- exchange resins with thicknesses between 0.1 and 1.5 mm, with exchange capacities ranging from 1 to 3.5 eq-mol/kg of dry resin equilibrated with sodium and water content that varies between 30% and 50%. For produced from reticulated polystyrene (i.e. polymer chains- styrene divinyl benzene) that is further sulfonated to produce sulphonic groups ( SO3 ) to make cationic exchange membranes or quaternized to produce quaternary ammonium groups ( NR3+) to make anionic exchange membranes in the polymeric matrix. conventional applications, the membranes are generally Due to the low mechanical resistance of these membranes it is necessary to add a fabric support layer (Strathmann, 1992).
Membrane characteristics and operation Membrane characteristics like electric resistance ( cm2), burst strength (MPa), and thickness (mm) are provided by the ion- exchange membrane manufacturers. Process Operation The principle of operation of an electrodialysis stack with n membrane pairs is shown in diagram. At a large scale an electrodialysis unit can comprise several stacks and each one may have from 20 to 500 pairs of membranes per electrode pair, with surface areas ranging from 0.02 to 2 m2. The diluate and concentrate compartments are delimited by the membranes, which have in between spacers that prevent the membranes from contacting each other and at the same time promote mass transfer. The spacers have usually a thickness ranging from 0.5 to 2 mm depending on the application and on the manufacturer.
Membrane characteristics and operation An electrodialysis plant in addition to the membrane stacks comprises power supply, pumps, tanks, process control devices, feed solution pretreatment unit, etc. After MF the feed solution is circulated into the electrodialysis stacks through the diluate channels. The deionized solution and the concentrated brine streams leaving the last stack are collected in storage tanks when the desired deionization is reached. In case of salt precipitation risk the pH in the concentrate tank may be adjusted. In order to prevent the formation of free chlorine the electrodes are often rinsed with a separate chloride-free solution.