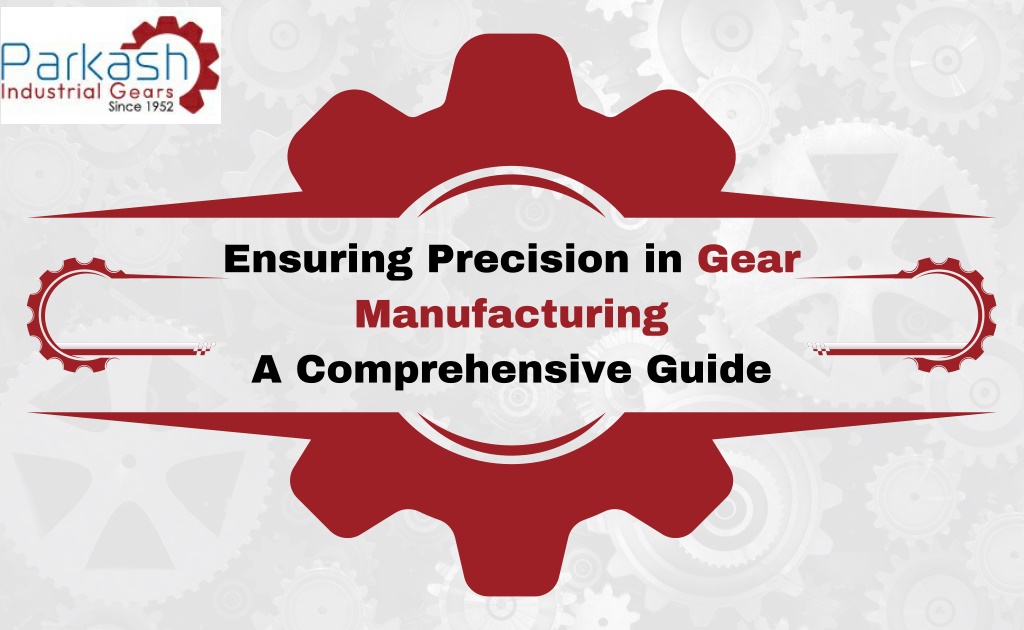
Comprehensive Guide to Precision Gear Manufacturing Processes
This comprehensive guide by Parkash Industrial Gears explores the manufacturing processes of worm gear manufacturing, bevel gears, spur gears, and helical gears. Learn about the precision crafting techniques and materials used to ensure durability and efficiency in these essential mechanical components. Understand the unique characteristics and applications of each gear type to help select the right solution for your needs. Discover the importance of partnering with experienced manufacturers who prioritize quality and accuracy in gear production. This article provides valuable insights for ind
Download Presentation

Please find below an Image/Link to download the presentation.
The content on the website is provided AS IS for your information and personal use only. It may not be sold, licensed, or shared on other websites without obtaining consent from the author. Download presentation by click this link. If you encounter any issues during the download, it is possible that the publisher has removed the file from their server.
E N D
Presentation Transcript
Ensuring Precision in Gear Manufacturing A Comprehensive Guide
Introduction Gears are fundamental components in countless mechanical systems, enabling efficient power transmission and precise motion control. Among the most commonly used gears are worm gears, bevel gears, spur gears, and helical gears. Understanding the manufacturing processes of these gears can help industries select the right gear type for their applications. This article, provided by Parkash Industrial Gears, delves into the intricacies of worm gear manufacturing, bevel gear manufacturer, spur gear manufacturers, and helical gear manufacturers, providing a detailed overview of each process.
The Process of Worm Gear Manufacturing Design and Material Selection: The first step in worm gear manufacturing is designing the gear according to the application requirements. Materials such as hardened steel, bronze, and cast iron are commonly used due to their strength and wear resistance. Cutting the Worm: The worm is typically machined using a thread milling or thread grinding process. Precision is crucial here to ensure the worm s threads mesh perfectly with the worm wheel. Manufacturing the Worm Wheel: The worm wheel is usually cut using a gear hobbing machine. The process involves a hob that gradually cuts the teeth into the wheel, ensuring accurate tooth profile and spacing. Heat Treatment: Both the worm and the worm wheel often undergo heat treatment to enhance their hardness and durability. Finishing and Inspection: The gears are finished to remove any burrs or imperfections. They are then inspected for accuracy and quality, ensuring they meet the required specifications.
The Role of a Bevel Gear Manufacturer Design and Material Selection: Bevel gears are designed based on their application. Common materials include alloy steel, carbon steel, and cast iron. Gear Cutting: The cutting process involves a gear- cutting machine that shapes the teeth. The method used can vary, including straight bevel gear cutting and spiral bevel gear cutting. Heat Treatment: Like worm gears, bevel gears often undergo heat treatment to improve their hardness and performance. Finishing and Quality Control: Finishing processes such as grinding and lapping achieve the desired surface finish. Rigorous quality control ensures the gears meet strict tolerances.
Spur Gear Manufacturing Process Design and Material Selection:Spur gear manufacturing designs are tailored to specific needs, with materials such as steel, brass, and nylon being commonly used. Gear Cutting: Gear cutting involves a hobbing machine or a shaping machine. The process ensures that the teeth are evenly spaced and accurately shaped. Heat Treatment: To enhance strength and wear resistance, spur gears often undergo heat treatment. Finishing and Inspection: The gears are finished to achieve a smooth surface and precise tooth profiles. Inspection processes ensure the gears conform to required specifications.
Helical Gear Manufacturing Design and Material Selection: Helical gears are designed for specific applications, with materials such as steel, aluminum, and cast iron being commonly used. Gear Cutting: The gear cutting process for helical gear manufacturing involves a hobbing machine or a milling machine. The angled teeth require precise cutting to ensure smooth operation. Heat Treatment: Heat treatment processes enhance the hardness and durability of helical gears. Finishing and Quality Control: Finishing processes such as grinding and honing are used to achieve the desired surface finish. Quality control ensures the gears meet precise specifications.
Conclusion Worm gear manufacturing, bevel gear manufacturers, spur gear manufacturers, and helical gear manufacturers all play crucial roles in producing gears essential for various mechanical systems. Each type of gear has unique characteristics and applications, making them indispensable in their respective fields. Understanding the manufacturing processes and applications of these gears can help industries select the right gear type for their needs. For reliable and precise gear solutions, it is essential to partner with experienced manufacturers like Parkash Industrial Gears, who prioritize quality and accuracy.