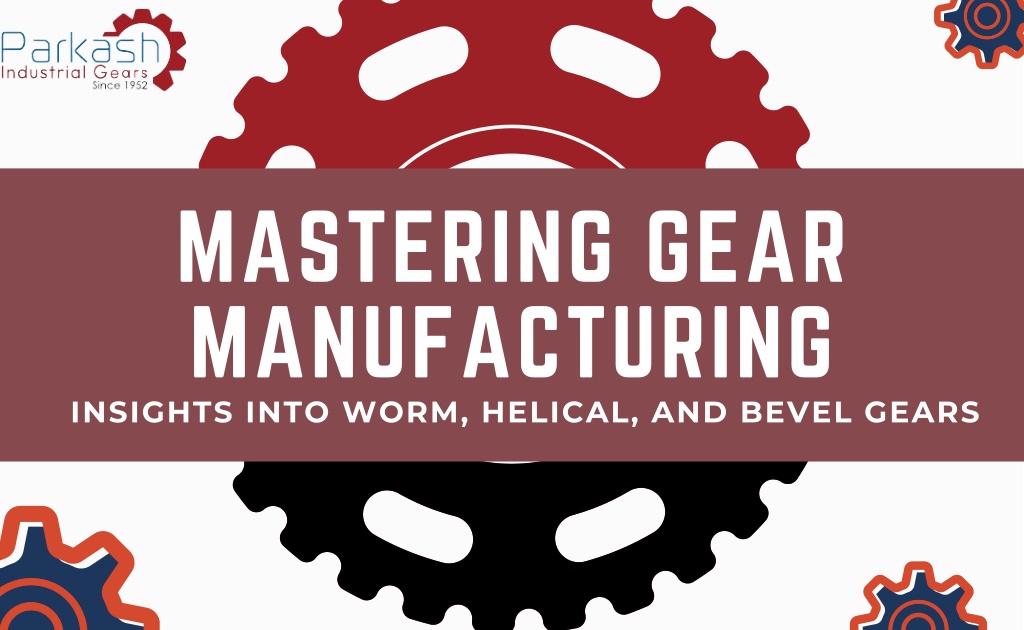
Worm Gear Manufacturing Unveiled: Driving Industries Forward with Precision
Explore the intricate world of gear manufacturing with our comprehensive guide. From the precision of worm gear manufacturing to the efficiency of helical gears and the versatility of bevel gears, discover how these components drive industries forwar
Download Presentation

Please find below an Image/Link to download the presentation.
The content on the website is provided AS IS for your information and personal use only. It may not be sold, licensed, or shared on other websites without obtaining consent from the author. Download presentation by click this link. If you encounter any issues during the download, it is possible that the publisher has removed the file from their server.
E N D
Presentation Transcript
MASTERING GEAR MANUFACTURING INSIGHTS INTO WORM, HELICAL, AND BEVEL GEARS
Introduction Parkash Industrial Gears recognizes the critical role worm gears play in various industrial applications, providing efficient power transmission and torque generation. Understanding the process of worm gear manufacturing, as well as the expertise of helical gear and bevel gear manufacturers, is essential for industries reliant on precision engineering and reliable mechanical components.
What is Worm Gear Manufacturing? Worm gears consist of a threaded cylindrical gear (the worm) meshing with a toothed gear (the worm wheel or worm gear). This setup allows for high torque transmission with a compact design, making them ideal for applications where space is limited but high gear reduction is required.
Key Steps in Worm Gear Manufacturing 1. Material Selection: High-quality metals such as bronze, steel, or aluminum are typically used due to their strength and wear resistance properties. Cutting and Shaping: The worm gear manufacturing process involves precision cutting and shaping of the worm and worm wheel. This can be done through various methods including hobbing, milling, or grinding. Heat Treatment: To enhance durability and strength, heat treatment processes like carburizing or nitriding are employed, ensuring the gears can withstand high loads and friction. Quality Control: Rigorous testing and inspection protocols ensure that the finished worm gears meet industry standards for accuracy, durability, and noise reduction. 2. 3. 4.
Helical Gear Manufacturer: Expertise in Precision Gears Helical gears, known for their smooth and quiet operation, are manufactured with precision to cater to industries where noise reduction and high efficiency are critical factors. A helical gear manufacturer employs advanced techniques such as CNC machining and gear grinding to achieve the required tooth profile accuracy and surface finish. Benefits of Helical Gears Quiet Operation: The helical tooth engagement reduces noise levels compared to spur gears. High Efficiency: They transmit power smoothly, minimizing energy loss due to friction. Versatility: Suitable for both parallel shaft and crossed axis applications.
Bevel Gear Manufacturer: Precision for Diverse Applications Bevel gears are conically shaped gears used to transmit power between intersecting shafts at right angles. A bevel gear manufacturer specializes in crafting these gears with tight tolerances to ensure smooth and efficient power transmission in various mechanical systems. Applications of Bevel Gears Automotive Industry: Differential gears in vehicles for torque distribution. Aerospace: Used in aircraft landing gear systems for reliable operation. Industrial Equipment: Machinery requiring precise torque transfer in tight spaces.
Choosing the Right Gear Manufacturer When selecting a gear manufacturer for worm gears, helical gears, or bevel gears, several factors should be considered: Experience and Expertise: Look for manufacturers with a proven track record in producing gears for your specific industry. Quality Standards: Ensure the manufacturer adheres to international quality standards such as ISO certifications. Customization Capabilities: Ability to customize gears according to your unique specifications and requirements. Technical Support: Manufacturers offering comprehensive technical support and post-sales service can be invaluable for troubleshooting and maintenance.
Conclusion Parkash Industrial Gears stand as a best gears manufacturers in India, trusted name in the field of gear manufacturing, offering expertise in worm gears, helical gears, and bevel gears. By implementing these insights and choosing keywords strategically throughout your content, you can enhance your visibility in search engine results while providing valuable information to your audience interested in gear manufacturing processes.