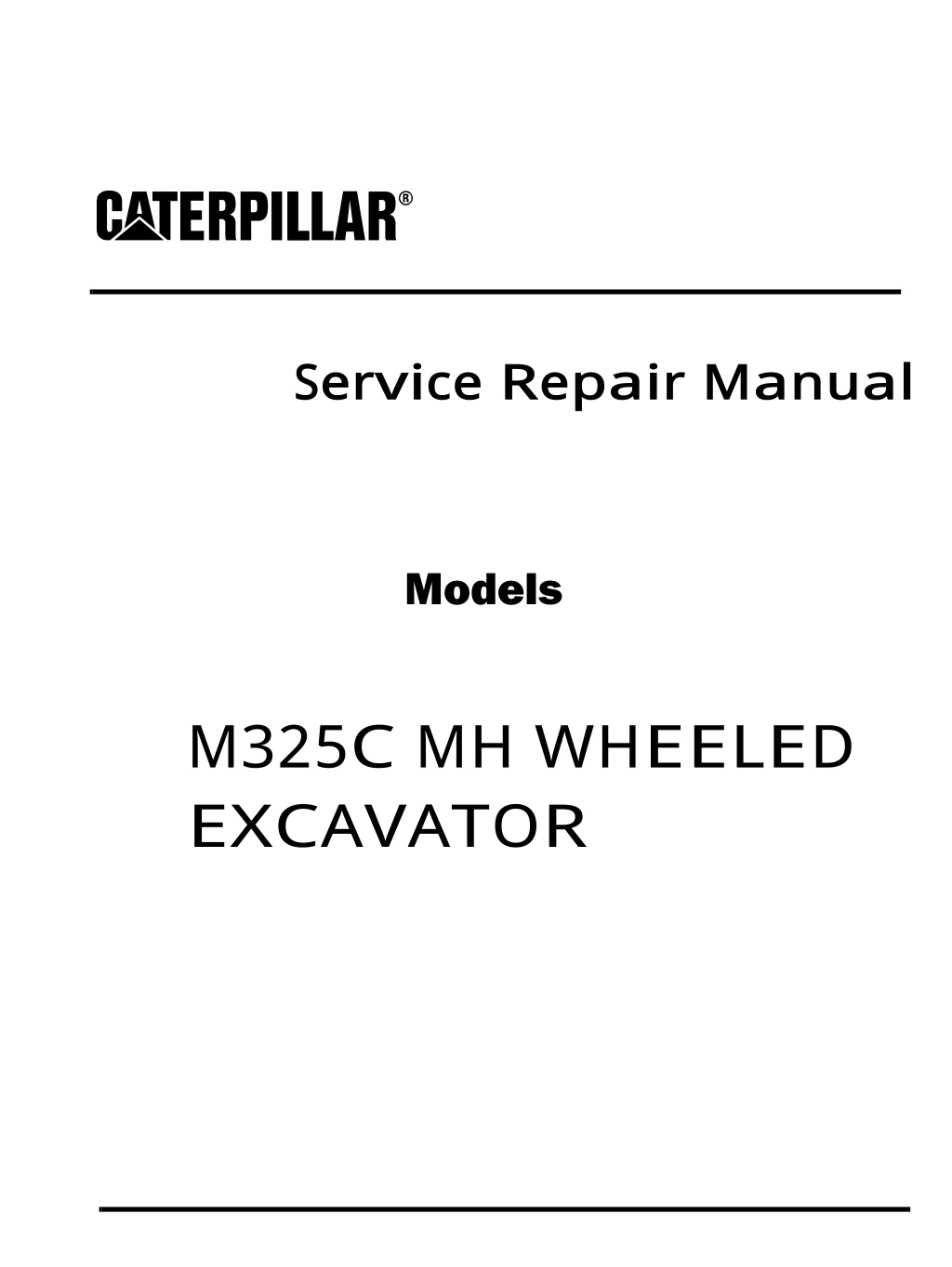
Caterpillar Cat M325C MH WHEELED EXCAVATOR (Prefix XJA) Service Repair Manual Instant Download
Please open the website below to get the complete manualnn// n
Download Presentation

Please find below an Image/Link to download the presentation.
The content on the website is provided AS IS for your information and personal use only. It may not be sold, licensed, or shared on other websites without obtaining consent from the author. Download presentation by click this link. If you encounter any issues during the download, it is possible that the publisher has removed the file from their server.
E N D
Presentation Transcript
Service Repair Manual Models M 325C M H WHEELED EXCAVATOR
w 1/10(W) Shutdown SIS Previous Screen Product: WHEELED EXCAVATOR Model: M325C MH WHEELED EXCAVATOR XJA Configuration: M325C Material Handler XJA00001-UP (MACHINE) POWERED BY 3126B Engine Disassembly and Assembly M325C Material Handler Machine Systems Media Number -RENR7163-01 Publication Date -01/10/2007 Date Updated -24/10/2007 i02233131 Swing Drive - Assemble SMCS - 5459-016 Assembly Procedure Table 1 Required Tools Tool Part Number Part Description Qty A 138-7573 Link Bracket 2 B 5P-5197 Pliers 1 E 138-7574 Link Bracket 2 F 138-7575 Link Bracket 3 G 5P-3931 Anti-Seize Compound 1 H 1U-8846 Gasket Sealant 1 J 9S-3263 Thread Lock Compound 1 K 1P-0520 Driver Gp 1 Note: Cleanliness is an important factor. Before assembly, all parts should be thoroughly cleaned in cleaning fluid. Allow the parts to air dry. Wiping cloths or rags should not be used to dry parts. Lint may be deposited on the parts which may cause later trouble. Inspect all parts. If any parts are worn or damaged, use new parts for replacement. https://127.0.0.1/sisweb/sisweb/techdoc/techdoc_print_page.jsp?returnurl=/sisweb/sisw... 2020/5/17
w 2/10(W) Illustration 1 g01126093 1. Use Tooling (K) to install lip seals (28) and O-ring seal (29) in bearing cage (27) . Illustration 2 g01126367 Note: Lubricate the seals and the seal surface of the shaft with the lubricant that is being sealed prior to installation of bearing cage (27) . 2. Install bearing cage (27) on pinion shaft (24) . https://127.0.0.1/sisweb/sisweb/techdoc/techdoc_print_page.jsp?returnurl=/sisweb/sisw... 2020/5/17
https://www.ebooklibonline.com Hello dear friend! Thank you very much for reading. Enter the link into your browser. The full manual is available for immediate download. https://www.ebooklibonline.com
w 3/10(W) Illustration 3 g01126373 3. Raise the temperature of bearing (30). Install bearing (30) on pinion shaft (24) . 4. Install spacer (31) . Illustration 4 g01126447 5. Raise the temperature of bearing (32). Install bearing (32) on pinion shaft (24) . Illustration 5 g01126490 6. Use Tooling (B ) to install retaining ring (23) on pinion shaft (24) and against bearing (32) . https://127.0.0.1/sisweb/sisweb/techdoc/techdoc_print_page.jsp?returnurl=/sisweb/sisw... 2020/5/17
w 4/10(W) Illustration 6 g01126507 Note: Ensure that bearings (30) and (32) are aligned while pinion shaft (24) is positioned. 7. Apply Tooling (G) to the inside diameter of swing drive housing (25) . 8. Attach Tooling (F) and a suitable lifting device to pinion shaft (24) . 9. Lower the temperature of pinion shaft (24) . 10. Install pinion shaft (24) in swing drive housing (25). The weight of pinion shaft (24) is approximately 50 kg (110 lb). 11. Remove Tooling (F) and the lifting device from pinion shaft (24). Attach Tooling (E) and a suitable lifting device to swing drive housing (25). The combined weight of swing drive housing (25), pinion shaft (24), and bearing cage (27) is approximately 151 kg (333 lb). 12. Lift the swing drive vertically. Use a hammer and a drift to align bearing (30) in the lower bore of swing drive housing (25). When the bearing is properly aligned in the bore, pinion shaft (24) will drop into the proper position within swing drive housing (25) . Illustration 7 g01126601 13. ApplyTooling (H) on the threads of bolts (26) . 14. Install bolts (26) . https://127.0.0.1/sisweb/sisweb/techdoc/techdoc_print_page.jsp?returnurl=/sisweb/sisw... 2020/5/17
w 5/10(W) Illustration 8 g01125682 15. Use two people or a suitable lifting device to install ring gear (22). The weight of ring gear (22) is approximately 46 kg (102 lb). Illustration 9 g01125627 Illustration 10 g01125625 https://127.0.0.1/sisweb/sisweb/techdoc/techdoc_print_page.jsp?returnurl=/sisweb/sisw... 2020/5/17
w 6/10(W) 16. Install bearings (20) in gear (19) . 17. Position thrust washers (21) on each side of gear (19). Install gear (19) in carrier assembly (14). Install shaft (18) in carrier assembly (14) and through gear (19). Make sure that the pin hole in shaft (18) is aligned with the pin hole in the carrier. 18. Install pin (17) in carrier assembly (14) and into shaft (18). Install pin (17) until pin (17) is even with the outside surface of carrier assembly (14). Orient the split in the pin horizontally to the carrier assembly. Align the split in the pin to the left or to the right. Illustration 11 g00513451 19. Make a stake mark on each side of the hole for pin (17). This will prevent pin (17) from falling out of the pin hole. Each stake mark should be approximately 1.5 mm (0.06 inch) from the outside diameter of the pin hole. 20. Repeat Steps 16 through 19 in order to install the remaining three gears (19) . https://127.0.0.1/sisweb/sisweb/techdoc/techdoc_print_page.jsp?returnurl=/sisweb/sisw... 2020/5/17
w 7/10(W) Illustration 12 g01125623 21. Use a suitable lifting device to install carrier assembly (14) in ring gear (22). The weight of carrier assembly (14) is approximately 39 kg (86 lb). Illustration 13 g01125545 22. Install retaining ring (16) in carrier assembly (14) . 23. Install spacer (15) . Illustration 14 g01125491 24. Install retaining ring (13) in gear (12) . https://127.0.0.1/sisweb/sisweb/techdoc/techdoc_print_page.jsp?returnurl=/sisweb/sisw... 2020/5/17
w 8/10(W) Illustration 15 g01125481 25. Install gear (12). Install retaining ring (11) . Illustration 16 g01125464 Illustration 17 g01125347 26. Install bearing (9) in gear (8) . https://127.0.0.1/sisweb/sisweb/techdoc/techdoc_print_page.jsp?returnurl=/sisweb/sisw... 2020/5/17
w 9/10(W) 27. Position thrust washers (10) on each side of gear (8). Install gear (8) and thrust washers (10) in carrier assembly (4). Install shaft (6) in carrier assembly (4) and through gear (8). Make sure that the pin hole in shaft (6) is aligned with the pin hole in carrier assembly (4) . 28. Install pin (7) in carrier assembly (4) and into shaft (6). Install pin (7) until pin (7) is even with the outside surface of carrier assembly (4). Orient the split in pin (7) horizontally to carrier assembly (4). Align the split in pin (7) to the left or to the right. Illustration 18 g00513451 29. Make a stake mark on each side of the pin hole in carrier assembly (4). This will prevent spring (7) from falling out of the pin hole. Each stake mark should be approximately 1.5 mm (0.06 inch) from the outside diameter of the pin hole. 30. Repeat Steps 24 through 29 in order to install the remaining three planetary gears in the carrier assembly. 31. Install sun gear (5) in carrier assembly (4) . https://127.0.0.1/sisweb/sisweb/techdoc/techdoc_print_page.jsp?returnurl=/sisweb/sisw... 2020/5/17
w 10/10(W) Illustration 19 g01125227 32. Use a suitable lifting device or two people to install carrier assembly (4). The weight of carrier assembly (4) is approximately 23 kg (50 lb). Illustration 20 g01125185 33. Apply Tooling (H) on the flange surfaces of the ring gear and cover (2) . 34. Use Tooling (A) and a suitable lifting device to position cover (2) on the swing drive. Illustration 21 g01126965 35. Apply Tooling (J) on the thread of bolts (1). Install bolts (1). Tighten bolts (1) to a torque of 270 40 N m (200 30 lb ft). End By: Install the swing drive. Refer to Disassembly and Assembly, "Swing Drive - Install". Copyright 1993 - 2020 Caterpillar Inc. Sun May 17 11:15:09 UTC+0800 2020 All Rights Reserved. Private Network For SIS Licensees. https://127.0.0.1/sisweb/sisweb/techdoc/techdoc_print_page.jsp?returnurl=/sisweb/sisw... 2020/5/17
w 1/2(W) Shutdown SIS Previous Screen Product: WHEELED EXCAVATOR Model: M325C MH WHEELED EXCAVATOR XJA Configuration: M325C Material Handler XJA00001-UP (MACHINE) POWERED BY 3126B Engine Disassembly and Assembly M325C Material Handler Machine Systems Media Number -RENR7163-01 Publication Date -01/10/2007 Date Updated -24/10/2007 i02229749 Swing Drive - Install SMCS - 5459-012 Installation Procedure Table 1 Required Tools Tool Part Number Part Description Qty 132-8223 Hydraulic Pump and Motor Gp 1 A 1U-6221 Hydraulic Torque Wrench Gp 1 132-8143 Wrench Link 1 B 138-7573 Link Bracket 2 D 5P-3931 Anti-Seize Compound 1 E 1U-8846 Gasket Sealant 1 F 9S-3263 Thread Lock Compound 1 1. Apply Tooling (D) on the locating pin in the main frame. Also, apply Tooling (D) in the pin bore in the main frame. 2. Apply Tooling (E) on the mating surface of the main frame and the swing drive housing. https://127.0.0.1/sisweb/sisweb/techdoc/techdoc_print_page.jsp?returnurl=/sisweb/sisw... 2020/5/17
w 2/2(W) Illustration 1 g00900976 Illustration 2 g00518158 3. Attach Tooling (B) and a suitable lifting device to swing drive (2). The weight of swing drive (2) is approximately 310 kg (683 lb). Use Tooling (B) and the suitable lifting device to position swing drive (2) on the machine. 4. Apply Tooling (F) on the threads of bolts (1). Install bolts (1). Tighten bolts (1) with Tooling (A) . 5. Fill swing drive (2) with oil. Refer to Operation and Maintenance Manual, "Swing Drive Oil - Check". End By: Install the swing motor. Refer to Disassembly and Assembly, "Swing Motor - Install". Copyright 1993 - 2020 Caterpillar Inc. Sun May 17 11:16:05 UTC+0800 2020 All Rights Reserved. Private Network For SIS Licensees. https://127.0.0.1/sisweb/sisweb/techdoc/techdoc_print_page.jsp?returnurl=/sisweb/sisw... 2020/5/17
w 1/6(W) Shutdown SIS Previous Screen Product: WHEELED EXCAVATOR Model: M325C MH WHEELED EXCAVATOR XJA Configuration: M325C Material Handler XJA00001-UP (MACHINE) POWERED BY 3126B Engine Disassembly and Assembly M325C Material Handler Machine Systems Media Number -RENR7163-01 Publication Date -01/10/2007 Date Updated -24/10/2007 i02291905 Upper Frame and Undercarriage Frame - Separate SMCS - 4150-076; 7051-076 Separation Procedure Table 1 Required Tools Tool Part Number Part Description Qty 8S-7641 Tube 2 8S-8048 Saddle 2 8S-7615 Pin 4 A 8S-7625 Collar 2 4C-6486 Stand 2 8S-7650 Cylinder As 2 4C-5809 Electric Hydraulic Pump Gp 1 B FT-3013 Link Assembly 1 C FT-2765 Support Beam As 1 D 8S-7641 Tube 2 8S-8048 Saddle 2 8S-7615 Pin 4 4C-5809 Electric Hydraulic Pump Gp 1 8S-7625 Collar 2 4C-6486 Stand 2 https://127.0.0.1/sisweb/sisweb/techdoc/techdoc_print_page.jsp?returnurl=/sisweb/sisw... 2020/5/17
w 2/6(W) 8S-7650 Cylinder As 2 132-8112 Torque Wrench Gp 1 E 132-8223 Hydraulic Pump and Motor Gp 1 Start By: A. Remove the stick. Refer to Disassembly and Assembly, "Stick - Remove". Note: Put identification marks on all hose assemblies and on all tube assemblies for installation purposes. 1. Park the machine on level ground. Turn the upper frame to a 90 degree angle from the undercarriage. 2. Remove the front drive shaft and the rear drive shaft. Refer to Disassembly and Assembly, "Drive Shaft - Remove and Install". Illustration 1 g01147594 3. Use the hydraulics of the machine to retract cylinders (1). Use a suitable lifting device to reposition stick cylinder pin (4) in boom (2). The weight of stick cylinder pin (4) is approximately 54 kg (120 lb). Install plates (3) . 4. Remove the swivel. Refer to Disassembly and Assembly, "Swivel - Remove". https://127.0.0.1/sisweb/sisweb/techdoc/techdoc_print_page.jsp?returnurl=/sisweb/sisw... 2020/5/17
w 3/6(W) Illustration 2 g01147596 5. Position Tooling (A) below stick cylinder pin (4) . 6. Remove the left side boom cylinder. Refer to Disassembly and Assembly, "Boom Cylinder - Remove and Install". Illustration 3 g01147597 7. Use a suitable lifting device to position Tooling (B). The weight of Tooling (B) is approximately 227 kg (500 lb). Install pin (5). Reposition pin (7) and install plate (6) . https://127.0.0.1/sisweb/sisweb/techdoc/techdoc_print_page.jsp?returnurl=/sisweb/sisw... 2020/5/17
w 4/6(W) Illustration 4 g01147599 8. Use a suitable lifting device to position Tooling (C) onto Tooling (D). The weight of Tooling (C) is approximately 227 kg (500 lb). Illustration 5 g01147598 9. Position Tooling (C) and Tooling (D) beneath counterweight (8) in order to support counterweight (8) during the separation procedure. https://127.0.0.1/sisweb/sisweb/techdoc/techdoc_print_page.jsp?returnurl=/sisweb/sisw... 2020/5/17
w 5/6(W) Illustration 6 g01147600 10. Disconnect tube assembly (9) . Illustration 7 g01147601 Note: Note the orientation of bolts (10) for installation purposes. 11. Use Tooling (E) to remove bolts (10) . Illustration 8 g01147772 https://127.0.0.1/sisweb/sisweb/techdoc/techdoc_print_page.jsp?returnurl=/sisweb/sisw... 2020/5/17
w 6/6(W) 12. Use Tooling (C) and Tooling (D) to raise upper frame (11) in 6.4 mm (0.25 inch) increments. Raise upper frame (11) enough for pinion gear (12) to clear swing bearing (13) . 13. Use a properly rated machine to pull undercarriage frame (14) from underneath upper frame (11) . Copyright 1993 - 2020 Caterpillar Inc. Sun May 17 11:17:01 UTC+0800 2020 All Rights Reserved. Private Network For SIS Licensees. https://127.0.0.1/sisweb/sisweb/techdoc/techdoc_print_page.jsp?returnurl=/sisweb/sisw... 2020/5/17
w 1/6(W) Shutdown SIS Previous Screen Product: WHEELED EXCAVATOR Model: M325C MH WHEELED EXCAVATOR XJA Configuration: M325C Material Handler XJA00001-UP (MACHINE) POWERED BY 3126B Engine Disassembly and Assembly M325C Material Handler Machine Systems Media Number -RENR7163-01 Publication Date -01/10/2007 Date Updated -24/10/2007 i02292929 Upper Frame and Undercarriage Frame - Connect SMCS - 4150-077; 7051-077 Connection Procedure Table 1 Required Tools Tool Part Number Part Description Qty 8S-7641 Tube 2 8S-8048 Saddle 2 8S-7615 Pin 4 A 8S-7625 Collar 2 4C-6486 Stand 2 8S-7650 Cylinder As 2 4C-5809 Electric Hydraulic Pump Gp 1 B FT-3013 Link Assembly 1 C FT-2765 Support Beam As 1 D 8S-7641 Tube 2 8S-8048 Saddle 2 8S-7615 Pin 4 4C-5809 Electric Hydraulic Pump Gp 1 8S-7625 Collar 2 4C-6486 Stand 2 https://127.0.0.1/sisweb/sisweb/techdoc/techdoc_print_page.jsp?returnurl=/sisweb/sisw... 2020/5/17
w 2/6(W) 8S-7650 Cylinder As 2 132-8112 Torque Wrench Gp 1 E 132-8223 Hydraulic Pump and Motor Gp 1 F 1U-8846 Gasket Sealant 3 G 5P-3931 Anti-Seize Compound 1 Illustration 1 g01147825 1. Apply Tooling (F) to gear and bearing (16). Apply Tooling (G) to dowel hole (15) . Illustration 2 g01147772 Note: A locating dowel is used to align the upper frame with the undercarriage frame. Make sure that the dowel is in position in the undercarriage frame prior to installation. Make sure that pinion gear (12) is properly aligned with swing bearing (13) prior to installation. 2. Use a properly rated machine to pull undercarriage frame (14) under upper frame (11). 3. Use Tooling (C) and Tooling (D) to lower upper frame (11) onto undercarriage frame (14). Lower upper frame (11) in 6.4 mm (0.25 inch) increments. https://127.0.0.1/sisweb/sisweb/techdoc/techdoc_print_page.jsp?returnurl=/sisweb/sisw... 2020/5/17
w 3/6(W) Illustration 3 g01147601 4. Use Tooling (E) to install bolts (10). Tighten bolts (10) to a torque of 900 100 N m (664 74 lb ft). Illustration 4 g01147600 5. Connect tube assembly (9) . https://127.0.0.1/sisweb/sisweb/techdoc/techdoc_print_page.jsp?returnurl=/sisweb/sisw... 2020/5/17
w 4/6(W) Illustration 5 g01147599 6. Attach a suitable lifting device to Tooling (C). The weight of Tooling (C) is approximately 227 kg (500 lb). Illustration 6 g01147597 7. Remove pin (5). Remove plate (6). Reposition pin (7). Remove Tooling (B) . 8. Install the right side boom cylinder. Refer to Disassembly and Assembly, "Boom Cylinder - Remove and Install". https://127.0.0.1/sisweb/sisweb/techdoc/techdoc_print_page.jsp?returnurl=/sisweb/sisw... 2020/5/17
Suggest: If the above button click is invalid. Please download this document first, and then click the above link to download the complete manual. Thank you so much for reading
w 5/6(W) Illustration 7 g01147596 9. Remove Tooling (A) from stick cylinder pin (4) . Illustration 8 g01147594 Note: Cylinders (1) were retracted during the separation procedure. 10. Attach a suitable lifting device to stick cylinder pin (4). The weight of stick cylinder pin (4) is approximately 54 kg (120 lb). Remove stick cylinder pin (4) from boom (2) . 11. Install the swivel. Refer to Disassembly and Assembly, "Swivel - Install". End By: a. Install the front drive shaft and the rear drive shaft. Refer to Disassembly and Assembly, "Drive Shaft - Remove and Install". b. Install the stick. Refer to Disassembly and Assembly, "Stick - Install". Sun May 17 11:17:57 UTC+0800 2020 https://127.0.0.1/sisweb/sisweb/techdoc/techdoc_print_page.jsp?returnurl=/sisweb/sisw... 2020/5/17
https://www.ebooklibonline.com Hello dear friend! Thank you very much for reading. Enter the link into your browser. The full manual is available for immediate download. https://www.ebooklibonline.com