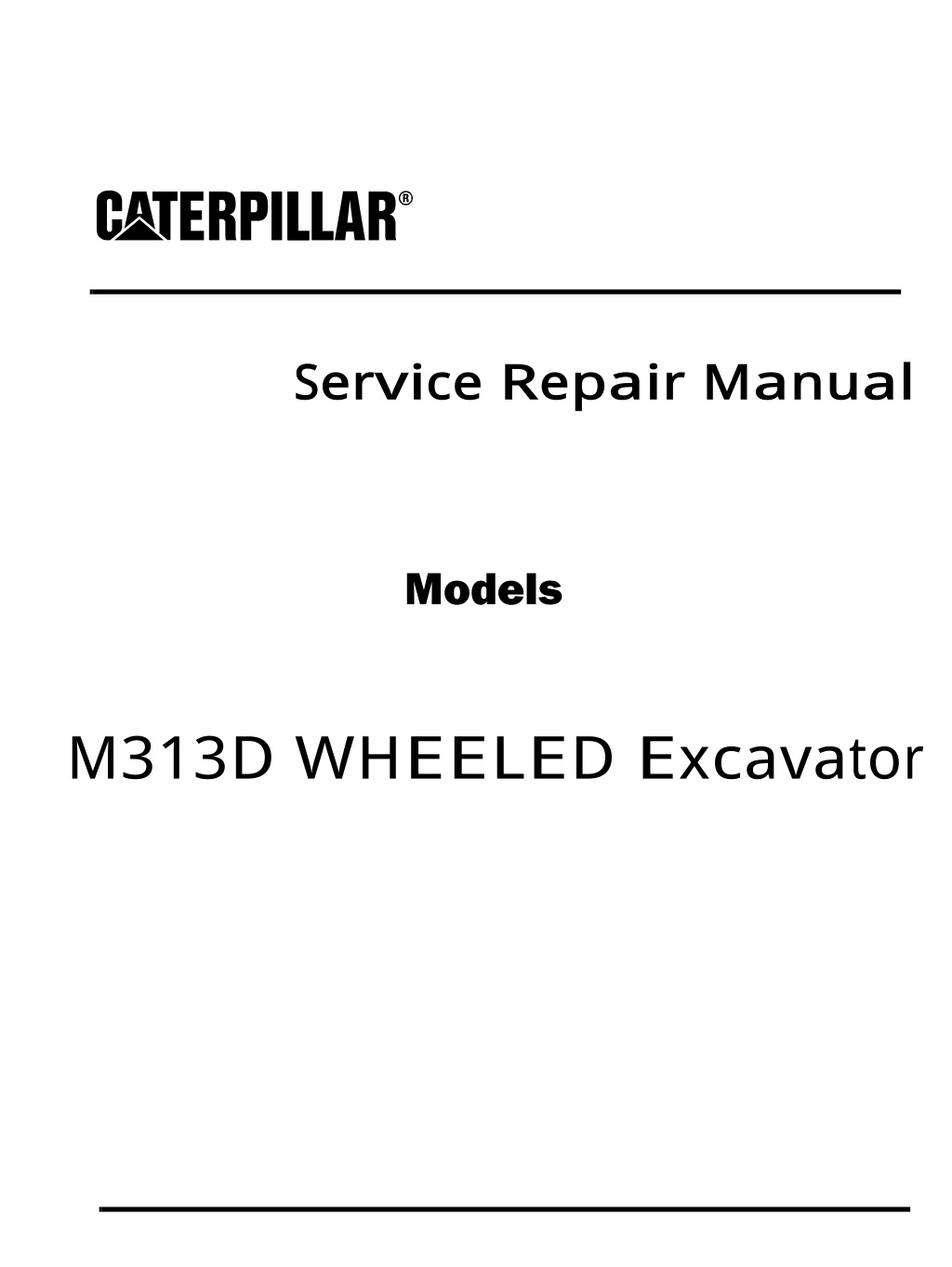
Caterpillar Cat M313D WHEELED Excavator (Prefix J3A) Service Repair Manual Instant Download
Please open the website below to get the complete manualnn//
Download Presentation

Please find below an Image/Link to download the presentation.
The content on the website is provided AS IS for your information and personal use only. It may not be sold, licensed, or shared on other websites without obtaining consent from the author. Download presentation by click this link. If you encounter any issues during the download, it is possible that the publisher has removed the file from their server.
E N D
Presentation Transcript
Service Repair Manual Models M 313D WHEELEDExcavator
w 1/30(W) Shutdown SIS Previous Screen Product: WHEELED EXCAVATOR Model: M313D WHEELED EXCAVATOR J3A Configuration: M313D Excavator J3A00001-UP (MACHINE) POWERED BY C4.4 Engine Disassembly and Assembly M313D Wheeled Excavator Power Train Media Number -KENR6026-02 Publication Date -01/10/2013 Date Updated -17/10/2013 i07308038 Transmission - Assemble SMCS - 3150-016 Assembly Procedure Table 1 Required Tools Tool Part Number Part Description Qty B 5P-4758 Retaining Ring Pliers As 1 C 5P-5197 Retaining Ring Pliers As 1 D 1P-1863 Retaining Ring Pliers 1 H 9U-7289 Ruler 1 J 1P-0520 Driver Gp 1 K 8T-0984 Pinion Flange Holder 1 L 9U-5017 Torque Wrench 1 M 267-3844 Seal Installer 1 N 267-3845 Guard Installer 1 P 6V-2055 Grease 1 Q 1P-0775 Seal Guide 1 R 267-3850 Clearance Gauge 1 https://127.0.0.1/sisweb/sisweb/techdoc/techdoc_print_page.jsp?returnurl=/sisweb/sisw... 2020/4/25
w 2/30(W) Illustration 1 g01150633 1. Install spring pin (86) if it is necessary. Illustration 2 g01150630 2. Install shroud (85). Illustration 3 g01150629 3. Install gear (84). https://127.0.0.1/sisweb/sisweb/techdoc/techdoc_print_page.jsp?returnurl=/sisweb/sisw... 2020/4/25
https://www.ebooklibonline.com Hello dear friend! Thank you very much for reading. Enter the link into your browser. The full manual is available for immediate download. https://www.ebooklibonline.com
w 3/30(W) Illustration 4 g01150626 4. Install O-ring seals (82) to cover (80). Illustration 5 g01150746 Illustration 6 g01150623 5. Use Tooling (J) to install seal (81) to cover (80). Use Tooling (H) to measure the depth of seal (81). Install seal (81) to the depth that was recorded during disassembly. https://127.0.0.1/sisweb/sisweb/techdoc/techdoc_print_page.jsp?returnurl=/sisweb/sisw... 2020/4/25
w 4/30(W) Illustration 7 g01150757 Illustration 8 g01150627 6. Position deflector plate (83). Install deflector plate (83). Illustration 9 g01150772 7. Position new bearing cone (74) and new bearing cup (78) together on a flat surface. Rotate bearing cone (74) in both directions. Use a suitable depth gauge to measure dimension (A). Subtract 0.10 mm (0.004 inch) from Dimension (A) for bearing preload. https://127.0.0.1/sisweb/sisweb/techdoc/techdoc_print_page.jsp?returnurl=/sisweb/sisw... 2020/4/25
w 5/30(W) Illustration 10 g06278522 8. Use a suitable depth gauge to measure Dimension (B) of cover (80). Illustration 11 g01150921 9. Use the number that is stamped on pinion (71) as Dimension (C), this number is in millimeters. Use 189.0 mm (7.44 inch) as Dimension (D). Dimension (D) is the constant value for the desired pinion depth. Illustration 12 g01150964 https://127.0.0.1/sisweb/sisweb/techdoc/techdoc_print_page.jsp?returnurl=/sisweb/sisw... 2020/4/25
w 6/30(W) 10. Subtract Dimension (C) from Dimension (D) to obtain Dimension (E). Add Dimension (A) to Dimension (B) to obtain Dimension (F). Subtract Dimension (E) from Dimension (F) to obtain the required thickness for shim (79). 11. Install shim (79) to cover (80). Illustration 13 g01150971 12. Use Tooling (J) to install bearing cup (78) to cover (80). Illustration 14 g01151014 13. Install cover (80). https://127.0.0.1/sisweb/sisweb/techdoc/techdoc_print_page.jsp?returnurl=/sisweb/sisw... 2020/4/25
w 7/30(W) Illustration 15 g01151015 14. Use Tooling (J) to install bearing cup (77). Illustration 16 g01150614 15. Raise the temperature of bearing cone (74) and install bearing cone (74) onto pinion (71). Install bushing (73) and O-ring seal (72) onto pinion (71). Illustration 17 g01151025 16. Install pinion (71). Illustration 18 g01151028 https://127.0.0.1/sisweb/sisweb/techdoc/techdoc_print_page.jsp?returnurl=/sisweb/sisw... 2020/4/25
w 8/30(W) 17. Position the transmission housing so that the weight of the housing is on pinion (71). Install shim (76). Illustration 19 g01151035 18. Raise the temperature of bearing cone (75) and install bearing cone (75) to pinion (71). Illustration 20 g01151051 Illustration 21 g01151056 19. If necessary, install studs (69) to gear (67). Tighten studs (69) to a torque of 20 N m (15 lb ft). https://127.0.0.1/sisweb/sisweb/techdoc/techdoc_print_page.jsp?returnurl=/sisweb/sisw... 2020/4/25
w 9/30(W) 20. Install gear (67) and plate (65). Install Tooling (K). Install bolts (63) and (64). Tighten bolts (63) and (64) to a torque of 46 N m (34 lb ft). 21. Remove Tooling (K). Use Tooling (L) to check the rolling torque. The rolling torque should measure 1.5 to 3.0 N m (13.30 to 27.00 lb in). Change shim (76) to adjust the rolling torque. 22. Install Tooling (K). Remove bolts (63) and (64). Remove gear (67) and plate (65). Illustration 22 g01151060 23. Use Tooling (M) to install seal (70). Illustration 23 g01151064 24. Use a suitable press and Tooling (N) to install plate (68) to gear (67). https://127.0.0.1/sisweb/sisweb/techdoc/techdoc_print_page.jsp?returnurl=/sisweb/sisw... 2020/4/25
w 10/30(W) Illustration 24 g01151068 25. Install gear (67). Install O-ring seal (66). Illustration 25 g01151072 26. Install plate (65). Install Tooling (K). Install bolts (63) and (64). Install bolts (63) and (64) to a torque of 46 N m (34 lb ft). Illustration 26 g01151077 Illustration 27 g01151085 https://127.0.0.1/sisweb/sisweb/techdoc/techdoc_print_page.jsp?returnurl=/sisweb/sisw... 2020/4/25
w 11/30(W) 27. Use Tooling (J) to install bearing cup (59) (not shown) and bearing cup (60) (not shown). Illustration 28 g01151088 28. Raise the temperature of inner race (58) and install inner race (58) to gear assembly (50). Illustration 29 g01151097 29. Use Tooling (P) to position rollers (57) to inner race (58). Illustration 30 g01151098 30. Install planetary pinion (55) and shim (56). Use Tooling (C) to install retaining ring (54). https://127.0.0.1/sisweb/sisweb/techdoc/techdoc_print_page.jsp?returnurl=/sisweb/sisw... 2020/4/25
w 12/30(W) Illustration 31 g01137229 Illustration 32 g01151103 31. Install spring pins (53) to gear assembly (50). Install spring pins (53) to a depth of 28 1.0 mm (1.1 0.04 inch). Use Tooling (H) to measure the depth of spring pins (53). Illustration 33 g01151106 32. Use a suitable press, Tooling (J), and Tooling (Q) to install bearing cone (52) to gear assembly (50). https://127.0.0.1/sisweb/sisweb/techdoc/techdoc_print_page.jsp?returnurl=/sisweb/sisw... 2020/4/25
w 13/30(W) Illustration 34 g01137187 33. Install gear assembly (50). Illustration 35 g01151110 34. Use suitable cribbing and position the transmission on gear assembly (50) (not shown) to keep gear assembly (50) in place. Illustration 36 g01151120 35. Raise the temperature of bearing cone (51) and install bearing cone (51) to gear assembly (50). Position washer (49) and install bolts (48). Tighten bolts (48) to a torque of 46 N m (34 lb ft). https://127.0.0.1/sisweb/sisweb/techdoc/techdoc_print_page.jsp?returnurl=/sisweb/sisw... 2020/4/25
w 14/30(W) Illustration 37 g01153935 36. Position lubrication pump (47) and install bolts (46). Install speed sensor (45) and bolts (45A). Tighten bolts (46) and (45A) to a torque of 23 N m (17 lb ft). Illustration 38 g01151139 37. Reposition the transmission. Position races (43) and (40). Position bearing (44). Illustration 39 g01151141 38. Install washer (42) to shaft assembly (31). https://127.0.0.1/sisweb/sisweb/techdoc/techdoc_print_page.jsp?returnurl=/sisweb/sisw... 2020/4/25
w 15/30(W) Illustration 40 g01151145 39. Install ball bearing (41) to shaft assembly (31). Illustration 41 g01151148 40. Position shaft assembly (31) to gear (32). Use Tooling (D) to install retaining ring (39). Use Tooling (C) to install retaining ring (38) and (37). Illustration 42 g01137136 https://127.0.0.1/sisweb/sisweb/techdoc/techdoc_print_page.jsp?returnurl=/sisweb/sisw... 2020/4/25
w 16/30(W) Illustration 43 g01137133 41. Install gear (32). Install discs (35) and clutch discs (36) alternately. Illustration 44 g01137130 42. Install shim (34) and retaining ring (33) to gear (32). Illustration 45 g01154987 43. Use Tooling (B) to install retaining ring (30) to gear (32). https://127.0.0.1/sisweb/sisweb/techdoc/techdoc_print_page.jsp?returnurl=/sisweb/sisw... 2020/4/25
w 17/30(W) Illustration 46 g01154279 44. Install washer (29). Illustration 47 g01154282 Illustration 48 g01154286 45. Install discs (27) and discs (28) alternately. https://127.0.0.1/sisweb/sisweb/techdoc/techdoc_print_page.jsp?returnurl=/sisweb/sisw... 2020/4/25
w 18/30(W) Illustration 49 g01137095 Illustration 50 g01154687 46. Install seal (26) to ring (25). Install ring (25). Illustration 51 g01137088 47. Install seals (22), (23), and (24) to ring (21). https://127.0.0.1/sisweb/sisweb/techdoc/techdoc_print_page.jsp?returnurl=/sisweb/sisw... 2020/4/25
w 19/30(W) Illustration 52 g01154289 48. Install ring (19) and (21). Illustration 53 g01154338 49. Install race (13), thrust bearing (12), and race (14). Illustration 54 g01151213 50. Install piston (15). https://127.0.0.1/sisweb/sisweb/techdoc/techdoc_print_page.jsp?returnurl=/sisweb/sisw... 2020/4/25
w 20/30(W) Illustration 55 g01151214 51. Install piston (11). Illustration 56 g01151216 52. Install springs (6). Illustration 57 g01151218 53. Install springs (5). https://127.0.0.1/sisweb/sisweb/techdoc/techdoc_print_page.jsp?returnurl=/sisweb/sisw... 2020/4/25
w 21/30(W) Illustration 58 g01151231 Improper assembly of parts that are spring loaded can cause bodily injury. To prevent possible injury, follow the established assembly procedure and wear protective equipment. 54. Position Tooling (R) and install bolts (2). Alternately tighten bolts (2) to a torque of 80 N m (59 lb ft). Illustration 59 g01151311 55. Use a suitable depth gauge to measure the distance from the face of Tooling (R) to piston (15). Record this dimension as Dimension (G). https://127.0.0.1/sisweb/sisweb/techdoc/techdoc_print_page.jsp?returnurl=/sisweb/sisw... 2020/4/25
w 22/30(W) Illustration 60 g01151316 56. Use a suitable depth gauge to measure the distance from the face of Tooling (R) to piston (11). Record this dimension as Dimension (H). Illustration 61 g01151231 Personal injury can result from being struck by parts propelled by a released spring force. Make sure to wear all necessary protective equipment. Follow the recommended procedure and use all recommended tooling to release the spring force. 57. Alternately loosen bolts (2). Remove Tooling (R). https://127.0.0.1/sisweb/sisweb/techdoc/techdoc_print_page.jsp?returnurl=/sisweb/sisw... 2020/4/25
w 23/30(W) Illustration 62 g01151321 58. Position Tooling (R) on a flat surface. Use a suitable depth gauge to measure the distance from the lower surface of Tooling (R). Record this dimension as Dimension (J). Illustration 63 g01151323 59. Use a suitable depth gauge to measure the distance from the upper surface of Tooling (R). Record this dimension as Dimension (K). Subtract Dimension (J) from Dimension (G) to obtain Dimension (L). Dimension (L) should measure 1.8 .30 mm (0.07 0.012 inch). 60. Subtract Dimension (K) from Dimension (H) to obtain Dimension (M). Dimension (M) should measure 2.4 .30 mm (0.09 0.012 inch). If Dimension (L) or Dimension (M) are not within the specification, adjust the thickness of the clutch packs. https://127.0.0.1/sisweb/sisweb/techdoc/techdoc_print_page.jsp?returnurl=/sisweb/sisw... 2020/4/25
w 24/30(W) Illustration 64 g01151218 61. Remove springs (5). Illustration 65 g01151216 62. Remove springs (6). Illustration 66 g01151214 63. Remove piston (11). Illustration 67 g01151213 https://127.0.0.1/sisweb/sisweb/techdoc/techdoc_print_page.jsp?returnurl=/sisweb/sisw... 2020/4/25
Suggest: If the above button click is invalid. Please download this document first, and then click the above link to download the complete manual. Thank you so much for reading
w 25/30(W) 64. Remove piston (15). Illustration 68 g01154338 65. Remove race (13), thrust bearing (12), and race (14). Illustration 69 g01154689 Improper assembly of parts that are spring loaded can cause bodily injury. To prevent possible injury, follow the established assembly procedure and wear protective equipment. 66. Remove ring (19). https://127.0.0.1/sisweb/sisweb/techdoc/techdoc_print_page.jsp?returnurl=/sisweb/sisw... 2020/4/25
https://www.ebooklibonline.com Hello dear friend! Thank you very much for reading. Enter the link into your browser. The full manual is available for immediate download. https://www.ebooklibonline.com