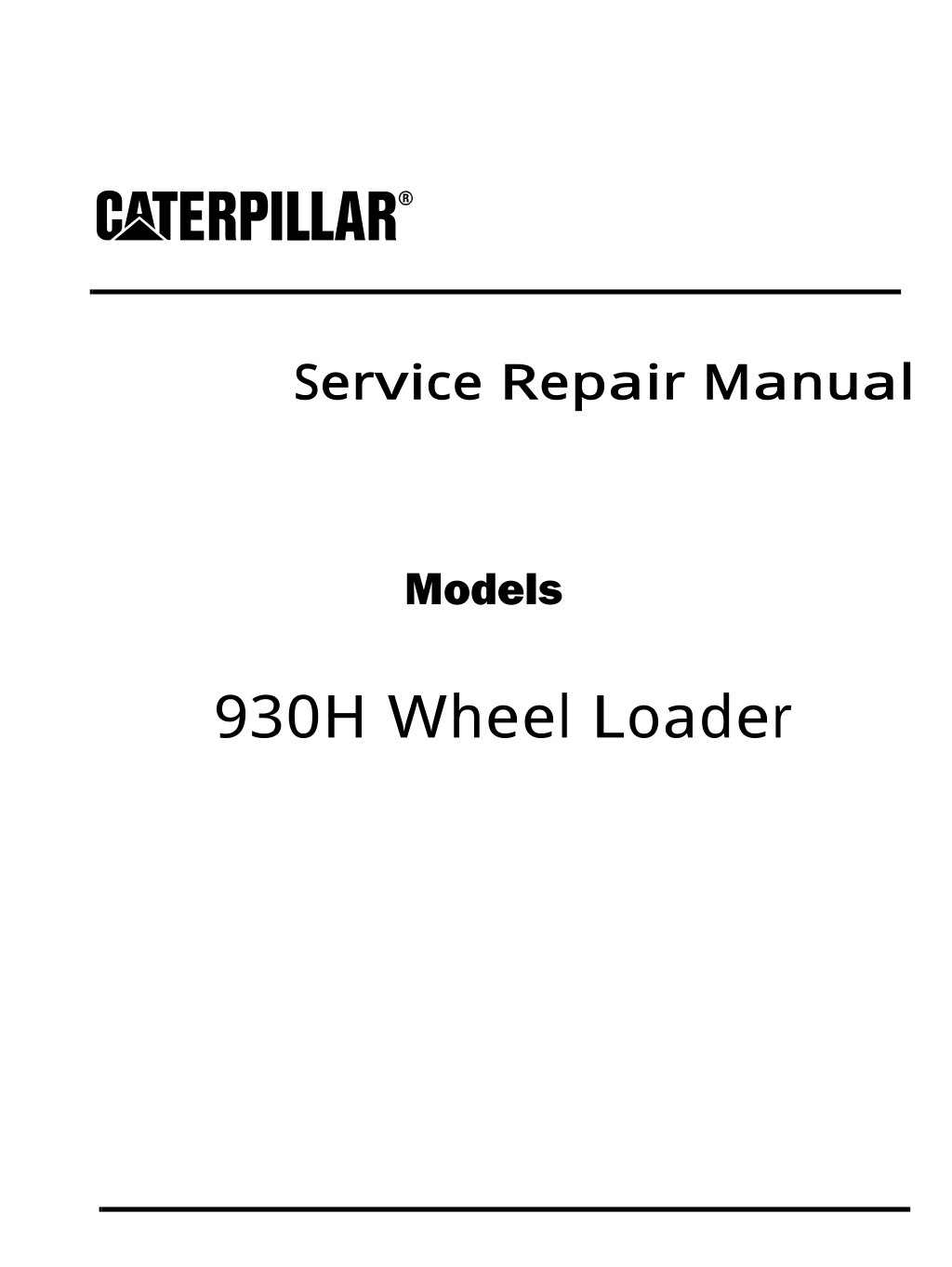
Caterpillar Cat 928HZ Wheel Loader (Prefix DHC) Service Repair Manual Instant Download
Please open the website below to get the complete manualnn// n
Download Presentation

Please find below an Image/Link to download the presentation.
The content on the website is provided AS IS for your information and personal use only. It may not be sold, licensed, or shared on other websites without obtaining consent from the author. Download presentation by click this link. If you encounter any issues during the download, it is possible that the publisher has removed the file from their server.
E N D
Presentation Transcript
Service Repair Manual Models 930H WheelLoader
928HZ 930H Wheel Loader DHC00001-04199 (MACHINE) POWERED BY C6.6 En... 1/19 Shutdown SIS Previous Screen Product: WHEEL LOADER Model: 930H WHEEL LOADER DHC Configuration: 928HZ 930H Wheel Loader DHC00001-04199 (MACHINE) POWERED BY C6.6 Engine Disassembly and Assembly 924H, 924HZ, 928HZ and 930H Wheel Loaders Machine Systems Media Number -KENR9440-02 Publication Date -01/08/2012 Date Updated -01/08/2012 i07528732 Loader Frame and Rear Frame - Connect SMCS - 7051-077; 7054-077 S/N - DHC1-UP S/N - HXC1-UP Connection Procedure Table 1 Required Tools Tool Part Number Part Description Qty A 1P-1863 Retaining Ring Pliers 1 284-5122 Stand 1 B 8S-7611 Tube 1 8S-7615 Pin 1 C 8T-5255 Hydraulic Jack 1 D 417-1324 Repair Stand Set 2 H 189-0412 Shackle 2 J 5P-0960 Grease Cartridge 1 K 1P-0510 Driver Gp 1 L - Loctite C5A Copper Anti-Seize - M 1P-0481 Drive Plate 2 N 1P-0495 Drive Plate 2 1B-2716 Bolt 1 P 6V-8185 Nut 1 https://127.0.0.1/sisweb/sisweb/techdoc/techdoc_print_page.jsp?returnurl=/sis... 2020/4/24
928HZ 930H Wheel Loader DHC00001-04199 (MACHINE) POWERED BY C6.6 En... 2/19 NOTICE Care must be taken to ensure that fluids are contained during performance of inspection, maintenance, testing, adjusting, and repair of the product. Be prepared to collect the fluid with suitable containers before opening any compartment or disassembling any component containing fluids. Refer to Special Publication, PERJ1017, "Dealer Service Tool Catalog" for tools and supplies suitable to collect and contain fluids on Cat products. Dispose of all fluids according to local regulations and mandates. Note: Apply Tooling (J) to all seals before installation. Lubricate all pin bores and all pins with Tooling (L) before installation of the pins. Illustration 1 g01118635 Note: Reference Illustration 4 for seal orientation. 1. Use Tooling (K) to install lip seal (39) into upper cap (35). Illustration 2 g01118634 Note: Reference Illustration 4 for seal orientation. 2. Use Tooling (K) to install lip seal (38) into lower cap (37). https://127.0.0.1/sisweb/sisweb/techdoc/techdoc_print_page.jsp?returnurl=/sis... 2020/4/24
https://www.ebooklibonline.com Hello dear friend! Thank you very much for reading. Enter the link into your browser. The full manual is available for immediate download. https://www.ebooklibonline.com
928HZ 930H Wheel Loader DHC00001-04199 (MACHINE) POWERED BY C6.6 En... 3/19 Illustration 3 g01120311 3. Position lower cap (37). 4. Install three bolts (34) in equal spacing. Illustration 4 g06351214 Lower Hitch 5. Lower the temperature of bearing cup (42). 6. Install bearing cup (42) so that bearing cup (42) contacts the lower cap. 7. Coat bearing cones (41) and (43) with oil. 8. Install bearing cones (41) and (43). 9. Lower the temperature of bearing cup (40) and install bearing cup (40). https://127.0.0.1/sisweb/sisweb/techdoc/techdoc_print_page.jsp?returnurl=/sis... 2020/4/24
928HZ 930H Wheel Loader DHC00001-04199 (MACHINE) POWERED BY C6.6 En... 4/19 Illustration 5 g01120311 10. Remove bolts (34) and lower cap (37). Illustration 6 g01120313 11. Install 1.5 mm (0.06 inch) of shims (36). Illustration 7 g01120315 12. Install upper cap (35), lower cap (37), and three of bolts (34), as shown. 13. Use Tooling (M) and Tooling (P) to check the rolling torques of the two bearing assemblies. 14. Add or remove shims (36) until the rolling torque of the bearing assemblies are between 1.7 N m to 5.6 N m (15 lb in to 50 lb in). https://127.0.0.1/sisweb/sisweb/techdoc/techdoc_print_page.jsp?returnurl=/sis... 2020/4/24
928HZ 930H Wheel Loader DHC00001-04199 (MACHINE) POWERED BY C6.6 En... 5/19 Illustration 8 g01118632 15. Install remaining bolts (34) onto upper cap (35). Illustration 9 g01118630 Note: Reference Illustration 12 for seal orientation. 16. Use Tooling (K) to install lip seal (33) into upper cap (28). Illustration 10 g01118528 Note: Reference Illustration 12 for seal orientation. 17. Use Tooling (K) to install lip seal (32) into lower cap (30). https://127.0.0.1/sisweb/sisweb/techdoc/techdoc_print_page.jsp?returnurl=/sis... 2020/4/24
928HZ 930H Wheel Loader DHC00001-04199 (MACHINE) POWERED BY C6.6 En... 6/19 Illustration 11 g01120480 18. Position lower cap (30). 19. Install three bolts (27). Illustration 12 g03741654 Upper Hitch 20. Lower the temperature of bearing cup (46). 21. Install bearing cup (46) so that bearing cup (46) contacts the lower cap. 22. Completely coat bearing cones (44) and (47) with oil. 23. Install bearing cones (44) and (47). 24. Lower the temperature of bearing cup (45) and install bearing cup (45). https://127.0.0.1/sisweb/sisweb/techdoc/techdoc_print_page.jsp?returnurl=/sis... 2020/4/24
928HZ 930H Wheel Loader DHC00001-04199 (MACHINE) POWERED BY C6.6 En... 7/19 Illustration 13 g01120480 25. Remove bolts (27) and lower cap (30). Illustration 14 g01121070 26. Install 2.0 mm (0.08 inch) of shims (29). Illustration 15 g01121074 27. Install upper cap (28), lower cap (30), and three of bolts (27), as shown. 28. Use Tooling (N) and Tooling (P) to check the rolling torques of the two bearings. 29. Add or remove shims (29) until the rolling torque of each bearing is between 2.8 N m to 11.2 N m (25 lb in to 99 lb in). https://127.0.0.1/sisweb/sisweb/techdoc/techdoc_print_page.jsp?returnurl=/sis... 2020/4/24
928HZ 930H Wheel Loader DHC00001-04199 (MACHINE) POWERED BY C6.6 En... 8/19 Illustration 16 g01118525 30. Install remaining bolts (27) into upper cap (28). Illustration 17 g06187594 31. Install spacer (31). https://127.0.0.1/sisweb/sisweb/techdoc/techdoc_print_page.jsp?returnurl=/sis... 2020/4/24
928HZ 930H Wheel Loader DHC00001-04199 (MACHINE) POWERED BY C6.6 En... 9/19 Illustration 18 g01118522 32. Use a suitable towing device and a suitable lifting device to reposition frame assembly (18). Illustration 19 g01131984 https://127.0.0.1/sisweb/sisweb/techdoc/techdoc_print_page.jsp?returnurl=/sis... 2020/4/24
928HZ 930H Wheel Loader DHC00001-04199 (MACHINE) POWERED BY C6.6 ... 10/19 33. Position frame assembly (18). Install pin assembly (19). Install bolt (20). Illustration 20 g01118430 34. Use Tooling (B) to support the rear end of the machine. Use Tooling (C) to adjust the alignment of the frames. Illustration 21 g06187596 Upper Hitch 35. Lower the temperature of pin assembly (25). Install pin assembly (25) into the bore of the upper hitch. https://127.0.0.1/sisweb/sisweb/techdoc/techdoc_print_page.jsp?returnurl=/sis... 2020/4/24
928HZ 930H Wheel Loader DHC00001-04199 (MACHINE) POWERED BY C6.6 ... 11/19 Illustration 22 g01131940 36. Install plate (22) and bolts (23), as shown. Illustration 23 g01131945 37. Use a feeler gauge to measure the gap between the flange of pin assembly (25) and the top of the hitch. Record the measurement. Illustration 24 g01131940 38. Remove plate (22) and bolts (23). Illustration 25 g01131952 39. Install shims (26) of the thickness that was recorded in Step 37 under pin assembly (25). https://127.0.0.1/sisweb/sisweb/techdoc/techdoc_print_page.jsp?returnurl=/sis... 2020/4/24
928HZ 930H Wheel Loader DHC00001-04199 (MACHINE) POWERED BY C6.6 ... 12/19 Illustration 26 g01131957 40. Install bolts (24) to pin assembly (25). Illustration 27 g01131960 41. Measure the gap between the bottom of pin assembly (25) and the bottom of the hitch. Record the measurement. https://127.0.0.1/sisweb/sisweb/techdoc/techdoc_print_page.jsp?returnurl=/sis... 2020/4/24
928HZ 930H Wheel Loader DHC00001-04199 (MACHINE) POWERED BY C6.6 ... 13/19 Illustration 28 g01118514 42. Install shims (21) with a thickness that is 0.25 mm (0.010 inch) less than the measured gap from Step 41. 43. Install plate (22) and bolts (23). Illustration 29 g01404160 https://127.0.0.1/sisweb/sisweb/techdoc/techdoc_print_page.jsp?returnurl=/sis... 2020/4/24
928HZ 930H Wheel Loader DHC00001-04199 (MACHINE) POWERED BY C6.6 ... 14/19 Illustration 30 g01118425 44. Position steering metering unit (17). Install bolts (16) onto both sides of the steering column. Position the floor mats into the cab. Illustration 31 g01118422 45. Reposition bracket (15). https://127.0.0.1/sisweb/sisweb/techdoc/techdoc_print_page.jsp?returnurl=/sis... 2020/4/24
928HZ 930H Wheel Loader DHC00001-04199 (MACHINE) POWERED BY C6.6 ... 15/19 Illustration 32 g01118420 46. Connect hose assembly (14) and install all mounting hardware. Illustration 33 g01118417 https://127.0.0.1/sisweb/sisweb/techdoc/techdoc_print_page.jsp?returnurl=/sis... 2020/4/24
928HZ 930H Wheel Loader DHC00001-04199 (MACHINE) POWERED BY C6.6 ... 16/19 47. Reposition harness assembly (13). Install all mounting hardware onto harness assembly (13). Connect harness assemblies (11) and (12). Connect harness assembly (10) onto both sides of the machine. Illustration 34 g01118201 48. Connect hose assemblies (8) and all mounting hardware. Connect hose assembly (9). https://127.0.0.1/sisweb/sisweb/techdoc/techdoc_print_page.jsp?returnurl=/sis... 2020/4/24
928HZ 930H Wheel Loader DHC00001-04199 (MACHINE) POWERED BY C6.6 ... 17/19 Illustration 35 g01118198 49. Position hose assemblies (6) and hose assemblies (7). Connect hose assemblies (6) and hose assemblies (7). Illustration 36 g01118197 50. Install pin (5). Use Tooling (A) to install retaining ring (4). 51. Repeat Step 50 to install the pin into the steering cylinder on the other side of the machine. https://127.0.0.1/sisweb/sisweb/techdoc/techdoc_print_page.jsp?returnurl=/sis... 2020/4/24
928HZ 930H Wheel Loader DHC00001-04199 (MACHINE) POWERED BY C6.6 ... 18/19 Illustration 37 g01118195 52. Install guard assemblies (3). Illustration 38 g01118194 53. Install guard assemblies (2). https://127.0.0.1/sisweb/sisweb/techdoc/techdoc_print_page.jsp?returnurl=/sis... 2020/4/24
928HZ 930H Wheel Loader DHC00001-04199 (MACHINE) POWERED BY C6.6 ... 19/19 Illustration 39 g01118191 54. Remove the suitable blocking from bucket (1). 55. Fill the hydraulic oil tank. The hydraulic tank capacity is approximately 73 L (19.3 US gal). Refer to Operation and Maintenance Manual for the proper procedure. End By: a. Install the center drive shaft. Refer to Disassembly and Assembly, "Drive Shaft (Center) - Install". Copyright 1993 - 2020 Caterpillar Inc. Fri Apr 24 10:51:08 UTC+0800 2020 All Rights Reserved. Private Network For SIS Licensees. https://127.0.0.1/sisweb/sisweb/techdoc/techdoc_print_page.jsp?returnurl=/sis... 2020/4/24
928HZ 930H Wheel Loader DHC00001-04199 (MACHINE) POWERED BY C6.6 En... 1/3 Shutdown SIS Previous Screen Product: WHEEL LOADER Model: 930H WHEEL LOADER DHC Configuration: 928HZ 930H Wheel Loader DHC00001-04199 (MACHINE) POWERED BY C6.6 Engine Disassembly and Assembly 924H, 924Hz, 928Hz and 930H Wheel Loaders Machine Systems Media Number -KENR7617-01 Publication Date -01/04/2010 Date Updated -21/04/2010 i02748684 Steering Frame Lock - Separate and Connect SMCS - 7506-029 Connection Procedure Personal injury or death can result from machine articulation or movement. Machine frames can move and a person can be crushed. Connect the steering frame lock link between the front and rear frames before working on machine. Secure clevis pin with locking pin. Before operating the machine, fasten the steering frame lock link into the stored position and secure the clevis pin with locking pin. Failure to lock into the stored position before operating can result in loss of steering. https://127.0.0.1/sisweb/sisweb/techdoc/techdoc_print_page.jsp?returnurl=/sis... 2020/4/24
928HZ 930H Wheel Loader DHC00001-04199 (MACHINE) POWERED BY C6.6 En... 2/3 Illustration 1 g01377068 1. Remove hitch pin (2) from pin (1). Illustration 2 g01377066 2. Move steering frame lock (3) in position to the front frame. Install pin (1) and hitch pin (2). Note: To align the pin bores, move the front loader frame. Separation Procedure Personal injury or death can result from machine articulation or movement. Machine frames can move and a person can be crushed. Connect the steering frame lock link between the front and rear frames before working on machine. Secure clevis pin with locking pin. Before operating the machine, fasten the steering frame lock link into the stored position and secure the clevis pin with locking pin. https://127.0.0.1/sisweb/sisweb/techdoc/techdoc_print_page.jsp?returnurl=/sis... 2020/4/24
928HZ 930H Wheel Loader DHC00001-04199 (MACHINE) POWERED BY C6.6 En... 3/3 Failure to lock into the stored position before operating can result in loss of steering. Illustration 3 g01377066 1. Remove pin (1) and hitch pin (2). Move steering frame lock (3) to the storage position. Illustration 4 g01377068 2. Install pin (1) and hitch pin (2). Copyright 1993 - 2020 Caterpillar Inc. Fri Apr 24 11:00:52 UTC+0800 2020 All Rights Reserved. Private Network For SIS Licensees. https://127.0.0.1/sisweb/sisweb/techdoc/techdoc_print_page.jsp?returnurl=/sis... 2020/4/24
928HZ 930H Wheel Loader DHC00001-04199 (MACHINE) POWERED BY C6.6 En... 1/4 Shutdown SIS Previous Screen Product: WHEEL LOADER Model: 930H WHEEL LOADER DHC Configuration: 928HZ 930H Wheel Loader DHC00001-04199 (MACHINE) POWERED BY C6.6 Engine Disassembly and Assembly 924H, 924Hz, 928Hz and 930H Wheel Loaders Machine Systems Media Number -KENR7617-01 Publication Date -01/04/2010 Date Updated -21/04/2010 i05079160 System Pressure - Release SMCS - 4250-553-PX; 4300-553-PX; 5050-553-PX Machine Preparation Personal injury can result from hydraulic oil pressure and hot oil. Hydraulic oil pressure can remain in the hydraulic system after the engine has been stopped. Serious injury can be caused if this pressure is not released before any service is done on the hydraulic system. Make sure all of the work tools have been lowered to the ground, and the oil is cool before removing any components or lines. Remove the oil filler cap only when the engine is stopped, and the filler cap is cool enough to touch with your bare hand. Escaping fluid under pressure, even a pinhole size leak, can penetrate body tissue, causing serious injury, and possible death. If fluid is injected into your skin, it must be treated immediately by a doctor familiar with this type of injury. Always use a board or cardboard when checking for a leak. https://127.0.0.1/sisweb/sisweb/techdoc/techdoc_print_page.jsp?returnurl=/sis... 2020/4/24
928HZ 930H Wheel Loader DHC00001-04199 (MACHINE) POWERED BY C6.6 En... 2/4 NOTICE Care must be taken to ensure that fluids are contained during performance of inspection, maintenance, testing, adjusting, and repair of the product. Be prepared to collect the fluid with suitable containers before opening any compartment or disassembling any component containing fluids. Refer to Special Publication, NENG2500, "Dealer Service Tool Catalog" for tools and supplies suitable to collect and contain fluids on Cat products. Dispose of all fluids according to local regulations and mandates. 1. Refer to Testing and Adjusting, "Machine Preparation for Troubleshooting" for the machine that is being serviced before performing the following procedure. Release System Pressure 1. Move the machine to a location that is smooth, level, and hard. The location should also be dry and free of debris. Stop the engine. 2. Permit only one operator on the machine. All other personnel should be kept away from the machine. 3. If the machine is equipped with a ride control system, move the ride control switch to the Manual position. Illustration 1 g02009358 https://127.0.0.1/sisweb/sisweb/techdoc/techdoc_print_page.jsp?returnurl=/sis... 2020/4/24
Suggest: If the above button click is invalid. Please download this document first, and then click the above link to download the complete manual. Thank you so much for reading
928HZ 930H Wheel Loader DHC00001-04199 (MACHINE) POWERED BY C6.6 En... 3/4 4. Position the bucket or work tool just above the ground at a slight downward angle. This position will ensure that the head end of the lift cylinders is pressurized. 5. Engage the parking brake. 6. Turn the engine start switch to the OFF position. 7. When the engine has stopped, turn the engine start switch back to the ON position so the pilot oil can reach the main valve. 8. Move the implement lockout switch to the UNLOCKED position. 9. Move the lift control lever to the FLOAT position and the tilt control lever to the TILT BACK position at the same time. This action allows the bucket or the work tool to tilt back while the boom is lowered. The bottom of the bucket or the work tool should rest flat on the ground. The weight of the linkage should be supported by the ground. The pressure from the head end of the lift cylinders and from the ride control accumulator is now vented to the hydraulic tank. 10. When the bucket or the work tool has settled to the ground, move both control levers to the HOLD position. Then, repeatedly cycle the control levers through all positions in order to purge any remaining pressure from the implement hydraulic system. 11. Turn the steering wheel several times in both directions in order to relieve the pressure in the steering system. To release the pressure from steering cylinders on machines equipped with joystick steering, the machine must not be operated for a minimum of 10 minutes. 10 minutes will allow sufficient time for the pressure in the steering system to dissipate. 12. Turn the engine start switch to the OFF position. 13. Depress the brake pedal repeatedly. This step will relieve any pressure that may be present in the braking system. 14. Push in the plunger for the hydraulic tank breaker relief valve until all pressure is released. Note: If the machine is not equipped with a hydraulic tank breaker relief valve, remove the hydraulic tank cap slowly to relieve tank pressure. Dead Electronics 1. If the electronics fail, all stored hydraulic oil pressure may not be relieved. The following precautions should be taken. 2. Turn the engine OFF. 3. The machine should be secured with a lockout. 4. Use the appropriate stand or blocks to prevent undesired drift of implements. 5. Barriers should be used in order to prevent personnel from entering areas that implement drift or movement could be hazardous. https://127.0.0.1/sisweb/sisweb/techdoc/techdoc_print_page.jsp?returnurl=/sis... 2020/4/24
https://www.ebooklibonline.com Hello dear friend! Thank you very much for reading. Enter the link into your browser. The full manual is available for immediate download. https://www.ebooklibonline.com