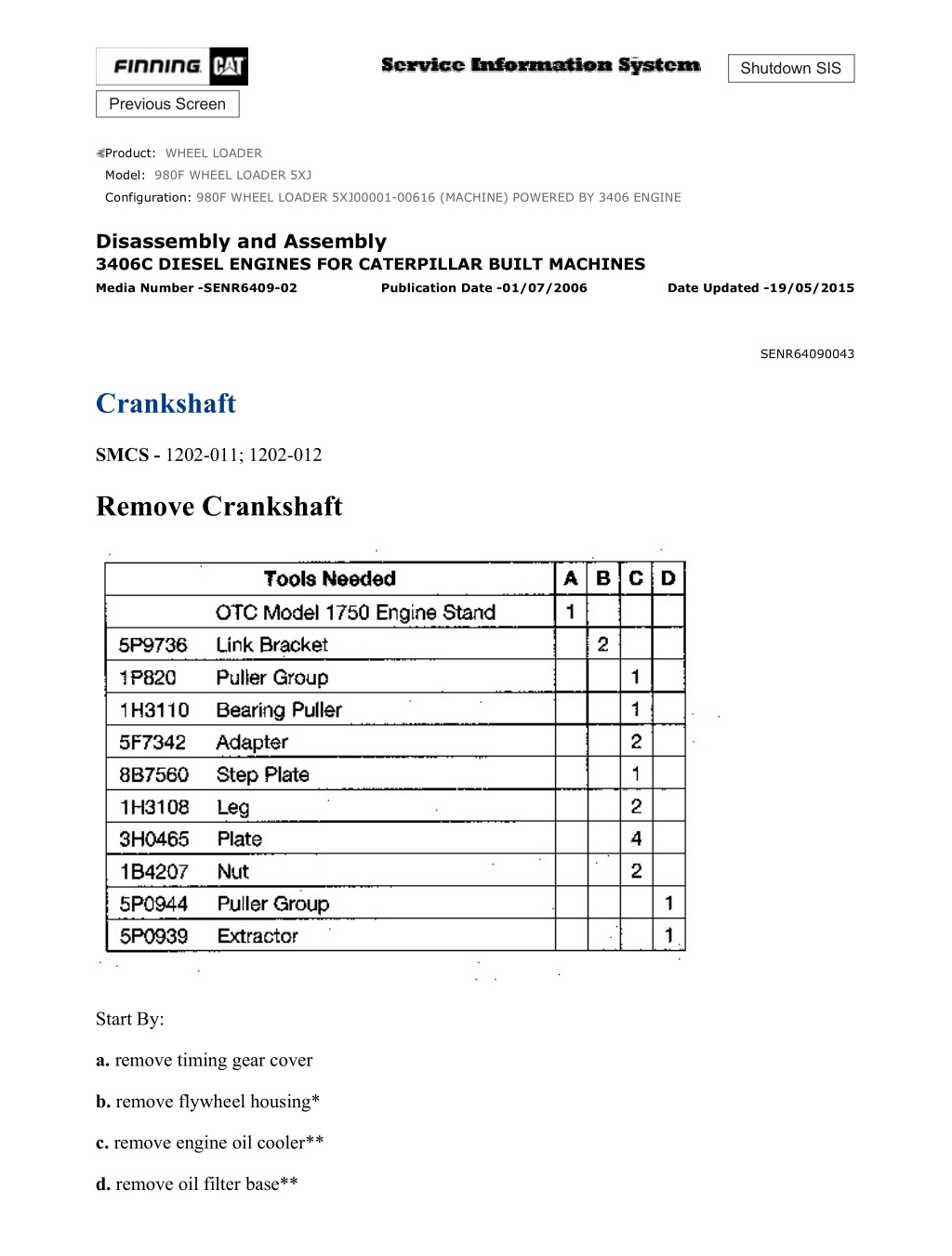
Caterpillar Cat 980F WHEEL LOADER (Prefix 5XJ) Service Repair Manual Instant Download 1
Please open the website below to get the complete manualnn//
Download Presentation

Please find below an Image/Link to download the presentation.
The content on the website is provided AS IS for your information and personal use only. It may not be sold, licensed, or shared on other websites without obtaining consent from the author. Download presentation by click this link. If you encounter any issues during the download, it is possible that the publisher has removed the file from their server.
E N D
Presentation Transcript
w 1/8(W) Shutdown SIS Previous Screen Product: WHEEL LOADER Model: 980F WHEEL LOADER 5XJ Configuration: 980F WHEEL LOADER 5XJ00001-00616 (MACHINE) POWERED BY 3406 ENGINE Disassembly and Assembly 3406C DIESEL ENGINES FOR CATERPILLAR BUILT MACHINES Media Number -SENR6409-02 Publication Date -01/07/2006 Date Updated -19/05/2015 SENR64090043 Crankshaft SMCS - 1202-011; 1202-012 Remove Crankshaft Start By: a. remove timing gear cover b. remove flywheel housing* c. remove engine oil cooler** d. remove oil filter base** https://127.0.0.1/sisweb/sisweb/techdoc/techdoc_print_page.jsp?returnurl=/sisweb/sisw... 2022/2/21
w 2/8(W) *Put the engine in time before the flywheel housing is removed. See the topic, "Finding Top Center Compression Position For No. 1 Piston" in Testing & Adjusting Manual SENR6471. **These operations must be done to install Tool (A) on the engine. Typical Example 1. Fasten the engine on Tool (A). The weight of the engine is 1362 kg (3000 lb). 2. Remove the bolts and nuts that hold air cleaner group (1), pipe assembly (3), bracket assembly (4) and lifting plate (5) as a unit to the engine. Fasten a hoist to the unit and remove it from the engine. The weight of the unit is approximately 39 kg (85 lb). 3. Remove tube assembly (2) from the engine. Typical Example 4. Install the two bolts to hold the primary fuel filter bracket (6) in place while the engine is turned with Tool (A). 5. Turn the engine to the position shown with Tool (A). Remove rod bearing caps (8) from the ends of the connecting rods. Push the connecting rods away from the crankshaft. 6. Remove the bolts and remove main bearing caps (7) from the crankshaft. https://127.0.0.1/sisweb/sisweb/techdoc/techdoc_print_page.jsp?returnurl=/sisweb/sisw... 2022/2/21
w 3/8(W) 7. Remove thrust plates (9) from the center main bearing journal. 8. Fasten a hoist to crankshaft (10) with tooling (B). Remove crankshaft (10) from the engine block. The weight of the crankshaft is 159 kg (350 lb). 9. Use Tool (C) to remove outer gear (2) from the end of the crankshaft. 10. Use a hammer and chisel to remove the spacer from the crankshaft. 11. Use Tool (D) to remove the gear alignment dowel from the crankshaft. 12. Use Tool (C) to remove inner gear (11) from the end of the crankshaft. https://127.0.0.1/sisweb/sisweb/techdoc/techdoc_print_page.jsp?returnurl=/sisweb/sisw... 2022/2/21
https://www.ebooklibonline.com Hello dear friend! Thank you very much for reading. Enter the link into your browser. The full manual is available for immediate download. https://www.ebooklibonline.com
w 4/8(W) NOTE: If new main bearings are not to be installed, put identification on the old main bearings as to their location in the cylinder block and to which main bearings caps they belong. 13. Remove main bearings (13) from the cylinder block and the main bearing caps. Install Crankshaft 1. If the dowel was removed from the flywheel end of the crankshaft, install it in the crankshaft to a maximum dimension of 6.4 mm (.25 in). 2. Heat the crankshaft gears to a maximum temperature of 205 C (400 F). 3. The centerline of inner gear key must be in alignment with the centerline of the dowel hole within 0.51 mm (.020 in). Install crankshaft inner gear (14) on the crankshaft. 4. Install the spacer on the crankshaft. 5. Install the dowel in the crankshaft. The dowel must be extended no more than 4.1 0.5 mm (.16 .02 in) from the surface of the crankshaft. NOTE: The dowel in the crankshaft must be in alignment with the notch in crankshaft gear (15). 6. Make sure the "V" mark on the crankshaft gear is toward the outside, and install crankshaft gear (15). https://127.0.0.1/sisweb/sisweb/techdoc/techdoc_print_page.jsp?returnurl=/sisweb/sisw... 2022/2/21
w 5/8(W) 7. Thoroughly clean the cylinder block and main bearing caps. NOTICE Make sure the upper and lower halves of the main bearings are installed so the bearing tabs fit into the notch in the cylinder block and main bearing caps. NOTE: Install the main bearings dry when the clearance checks are made. Put clean engine oil on the main bearings for final assembly. 8. Install the upper half of main bearings (13) (bearings with oil holes) in the cylinder block. 9. Fasten a hoist to crankshaft (10) with tooling (B) and put it in position on the cylinder block. Make sure the "V" marks on the crankshaft and the idler gear are in alignment and the "K" marks on the camshaft gear can be seen at the outer edges of the idler gear. The timing gears are in correct position. 10. Install thrust plates (9) on both sides of the center main bearing journal. Make sure the plates are installed with side marked "BLOCK SIDE" toward the cylinder block. 11. Install the lower half of main bearings (13) in main bearing caps (7). https://127.0.0.1/sisweb/sisweb/techdoc/techdoc_print_page.jsp?returnurl=/sisweb/sisw... 2022/2/21
w 6/8(W) NOTE: When the bearing clearance is checked and the engine is vertical position, such as in the vehicle, the crankshaft will have to be lifted up and held against the upper halves of the main bearings to get a correct measurement with the Plastigage. The Plastigage will not hold the weight of the crankshaft and give a correct indication. If the engine is in a horizontal position, it is not necessary to hold the crankshaft up. Do not turn the crankshaft when the Plastigage is in position to check clearances. 12. Put a piece of Plastigage on the surface of the lower main bearing half. 13. Install main bearing caps (7) with the arrow on the bottom surface of the cap toward the front of the cylinder block. Also, the stamped number on the cap must be the same as the cast number on the left side of the cylinder block. NOTICE Do not use an impact wrench to tighten the bolts the additional 120 5 degrees of a turn more. 14. Put 2P2506 Thread Lubricant on the threads of the main bearing cap bolts. Install the bolts and tighten them as follows: a. Tighten the tab end bolt to a torque of 258 14 N m (190 10 lb ft). b. Tighten the opposite end bolt to a torque of 258 14 N m (190 10 lb ft). c. Turn the opposite end bolt an additional 120 5 degrees. d. Turn the tab end bolt an additional 120 5 degrees. 15. Remove the main bearing caps and measure the Plastigage. The main bearing clearance must be 0.091 - 0.185 mm (.0036 - .0073 in) with new bearings. Maximum clearance with used bearings is 0.25 mm (.010 in). 16. Install the main bearing caps again and tighten the bolts as in Step 13. https://127.0.0.1/sisweb/sisweb/techdoc/techdoc_print_page.jsp?returnurl=/sisweb/sisw... 2022/2/21
w 7/8(W) 17. Put the connecting rods in position on the crankshaft. Install rod bearing caps (8) with the bolts and nuts to hold them. See the topic, "Remove & Install Connecting Rod Bearings", for the correct bolt tightening procedure and bearing clearance check procedure. 18. Check the crankshaft end play with tooling (E). The end play is controlled by the thrust plates on the center main bearing. End play with new plates is 0.15 - 0.51 mm (.006 - .020 in). The maximum permissible end play with used bearings is 0.89 mm (.035 in). 19. Use Tool (A) to turn the engine back to its vertical position as shown. 20. Install tube assembly (2) on the engine. 21. Fasten a hoist to and install air cleaner group (1), pipe assembly (3), bracket assembly (4) and lifting plate (5) as a unit on the engine. End By: a. install oil filter base b. install engine oil cooler c. install flywheel housing d. install timing gear cover Mon Feb 21 10:41:01 UTC+0800 2022 https://127.0.0.1/sisweb/sisweb/techdoc/techdoc_print_page.jsp?returnurl=/sisweb/sisw... 2022/2/21
w 8/8(W) Copyright 1993 - 2022 Caterpillar Inc. All Rights Reserved. Private Network For SIS Licensees. https://127.0.0.1/sisweb/sisweb/techdoc/techdoc_print_page.jsp?returnurl=/sisweb/sisw... 2022/2/21
w 1/8(W) Shutdown SIS Previous Screen Product: WHEEL LOADER Model: 980F WHEEL LOADER 5XJ Configuration: 980F WHEEL LOADER 5XJ00001-00616 (MACHINE) POWERED BY 3406 ENGINE Disassembly and Assembly 980F & 980F SERIES II WHEEL LOADERS POWER TRAIN Media Number -SENR4991-02 Publication Date -01/08/2004 Date Updated -18/04/2012 SENR49910001 Duo-Cone Seals SMCS - 7561-016 Assembly And Installation Of Conventional Duo-Cone Seals Introduction This instruction gives the procedure for installing Conventional Duo-Cone Seals. It is most important that correct assembly and installation procedures are followed when Duo- Cone Seals are used. Many of the Duo-Cone Seal failures are the direct result of one or more mistakes made during assembly or installation of the seal components. (1) Seal (2) Rubber Toric Ring (3) Housing Retaining Lip (4) Housing Ramp (5) Seal Ring Housing https://127.0.0.1/sisweb/sisweb/techdoc/techdoc_print_page.jsp?returnurl=/sisweb/sisw... 2022/2/21
w 2/8(W) (6) Seal Ring Face (7) Seal Ring Ramp (8) Seal Ring Retaining Lip (9) Installation Tool 1. Remove any oil film, dust or other foreign matter from rubber toric rings (2) and from ramps (4) and (7) and lips (3) and (8) of both seal rings (1) and housings (5). Use Isopropyl alcohol and a suitable cloth for wiping. NOTICE Never permit oil to get on the toric rings or ramps before both seal rings are put together in their final assembled position (Step 10). Avoid prolonged skin contact with Isopropyl alcohol. Avoid breathing the vapors in enclosed areas without adequate ventilation and do not smoke. Do not use near open flame or welding operations or other heated surfaces exceeding 482 C (900 F). https://127.0.0.1/sisweb/sisweb/techdoc/techdoc_print_page.jsp?returnurl=/sisweb/sisw... 2022/2/21
w 3/8(W) 2. Put toric ring (2) on seal ring (1), at the bottom of seal ring ramp (7) and against retaining lip (8). NOTICE Make sure that toric ring (2) is straight on seal ring (1) and is not twisted. Be careful when you work on the rubber toric ring. Nicks, cuts and scratches can cause leaks. https://127.0.0.1/sisweb/sisweb/techdoc/techdoc_print_page.jsp?returnurl=/sisweb/sisw... 2022/2/21
w 4/8(W) 3. Put installation tool (9) onto seal ring (1) with toric ring (2). Lower the rings into a container with Isopropyl alcohol until all surfaces of toric ring (2) are wet. NOTICE Do not use Stanisol or any other liquid that leaves an oil film or does not evaporate quickly. 4. With all surfaces of toric ring (2) wet, use installation tool (9) to position seal ring (1) and toric ring (2) squarely against housing (5) as shown. Use sudden and even pressure to pop (push) toric ring (2) under retaining lip (3) of housing (5). https://127.0.0.1/sisweb/sisweb/techdoc/techdoc_print_page.jsp?returnurl=/sisweb/sisw... 2022/2/21
w 5/8(W) 5. Check assembled height (A) in at least four places, 90 apart. The difference in height around the ring must not be more than 1 mm (.04"). 6. If small adjustments are necessary, do not push directly on seal ring (1); use installation tool (9). 7. Toric ring (2) can twist if it is not wet all around during installation or if there are burrs or fins on retaining lip (3) of housing (5). NOTICE Misalignment, twists and bulges of the toric ring will cause Duo-Cone Seal failures. If correct installation is not obvious, remove seal from housing and repeat steps 3 through 6. IMPORTANT: Toric rings (2) must never slip on the ramps of either seal rings (1) or seal ring housings (5). To prevent slippage, wait a minimum of two minutes to let the Isopropyl alcohol evaporate before further assembly. Once correctly in place, the toric ring must roll on the ramps only. https://127.0.0.1/sisweb/sisweb/techdoc/techdoc_print_page.jsp?returnurl=/sisweb/sisw... 2022/2/21
w 6/8(W) 8. Wipe seal faces (6) of seal rings (1) clean. Use a lint free cloth or paper towel. No particles of any kind are permissible on the sealing surfaces. Even a small piece from a paper towel can hold the seal faces apart and cause leakage. https://127.0.0.1/sisweb/sisweb/techdoc/techdoc_print_page.jsp?returnurl=/sisweb/sisw... 2022/2/21
w 7/8(W) 9. Put a thin film of clean oil on the seal faces. Use an applicator, disposable tissue or a finger to distribute the oil evenly. Be careful not to get any oil on the rubber toric rings. 10. Make sure both housings (5) are in correct alignment and are concentric. Move the parts slowly and carefully toward each other. NOTICE Do not slam seals together. High impact can scratch or break the seal components. 11. Once in place, fasten all parts tightly. Mon Feb 21 10:42:42 UTC+0800 2022 https://127.0.0.1/sisweb/sisweb/techdoc/techdoc_print_page.jsp?returnurl=/sisweb/sisw... 2022/2/21
w 8/8(W) Copyright 1993 - 2022 Caterpillar Inc. All Rights Reserved. Private Network For SIS Licensees. https://127.0.0.1/sisweb/sisweb/techdoc/techdoc_print_page.jsp?returnurl=/sisweb/sisw... 2022/2/21
w 1/2(W) Shutdown SIS Previous Screen Product: WHEEL LOADER Model: 980F WHEEL LOADER 5XJ Configuration: 980F WHEEL LOADER 5XJ00001-00616 (MACHINE) POWERED BY 3406 ENGINE Disassembly and Assembly 980F & 980F SERIES II WHEEL LOADERS POWER TRAIN Media Number -SENR4991-02 Publication Date -01/08/2004 Date Updated -18/04/2012 SENR49910002 Steering Frame Lock Link SMCS - 7506-029 Separate & Connect Steering Frame Lock Link There is no clearance for a person in the area between the front and rear frames of the machine when turning the vehicle. When a machine is to be lifted, transported on another vehicle or service work is being performed near the center of the machine, connect the steering frame lock link between the front and rear loader frames to keep the machine in a straight ahead position. Before operation and when operating, be sure the steering frame lock link, located near the center of the machine, is disconnected and pinned to the retaining plates. Steering Frame Lock Link In The Stored Position 1. To connect the steering frame lock link, first put the machine in a straight ahead position. 2. Remove the cotter pins from pins (1) and (2). Remove pins (1) and (2) from the steering frame lock link. https://127.0.0.1/sisweb/sisweb/techdoc/techdoc_print_page.jsp?returnurl=/sisweb/sisw... 2022/2/21
w 2/2(W) 3. Slide the steering frame lock link into the front loader frame. Be sure the bores in the lock link are in alignment with the bores in the front and rear loader frames. Reinstall pins (1) and (2) and the cotter pins that hold them. NOTE: The following step is for the separation of the steering frame lock link. 4. Remove the cotter pins from pins (1) and (2). Slide the steering frame lock link into the storage position in the rear loader frame. Reinstall pins (1) and (2) to hold the steering frame lock link in the stored position. Install the cotter pins to hold pins (1) and (2) in place. Copyright 1993 - 2022 Caterpillar Inc. Mon Feb 21 10:43:38 UTC+0800 2022 All Rights Reserved. Private Network For SIS Licensees. https://127.0.0.1/sisweb/sisweb/techdoc/techdoc_print_page.jsp?returnurl=/sisweb/sisw... 2022/2/21
w 1/1(W) Shutdown SIS Previous Screen Product: WHEEL LOADER Model: 980F WHEEL LOADER 5XJ Configuration: 980F WHEEL LOADER 5XJ00001-00616 (MACHINE) POWERED BY 3406 ENGINE Disassembly and Assembly 980F & 980F SERIES II WHEEL LOADERS POWER TRAIN Media Number -SENR4991-02 Publication Date -01/08/2004 Date Updated -18/04/2012 SENR49910003 Power Train Guard SMCS - 7153-010 Remove & Install Power Train Guard 1. Put tool (A) in position under power train guard (1) as shown. 2. Remove six bolts (2). Remove power train guard (1). The weight of the power train guard is 88 kg (195 lb). NOTE: Install the power train guard in the reverse order of removal. Copyright 1993 - 2022 Caterpillar Inc. Mon Feb 21 10:44:34 UTC+0800 2022 All Rights Reserved. Private Network For SIS Licensees. https://127.0.0.1/sisweb/sisweb/techdoc/techdoc_print_page.jsp?returnurl=/sisweb/sisw... 2022/2/21
w 1/5(W) Shutdown SIS Previous Screen Product: WHEEL LOADER Model: 980F WHEEL LOADER 5XJ Configuration: 980F WHEEL LOADER 5XJ00001-00616 (MACHINE) POWERED BY 3406 ENGINE Disassembly and Assembly 980F & 980F SERIES II WHEEL LOADERS POWER TRAIN Media Number -SENR4991-02 Publication Date -01/08/2004 Date Updated -18/04/2012 SENR49910004 Tire And Rim Assemblies SMCS - 4202-010 Remove And Install Front Tires & Rim Assemblies Removal Procedure Start By: a. Connect the steering frame lock. Refer to Disassembly and Assembly, "Steering Frame Lock - Separate and Connect" for the machine that is being serviced. b. Remove the front fenders. Refer to Disassembly and Assembly, "Fender - Remove and Install" for the machine that is being serviced. 1. Place wood blocks in front of the rear tires and behind the rear tires. 2. Place Tooling (A) under the loader frame on both sides of the machine, as shown. https://127.0.0.1/sisweb/sisweb/techdoc/techdoc_print_page.jsp?returnurl=/sisweb/sisw... 2022/2/21
w 2/5(W) 3. Use Tooling (A) to raise the front of the machine until the tires are off the ground. 4. Lock Tooling (A) in position with lockring ring (1). 5. Fasten a hoist and suitable lifting slings to tire (3), as shown. 6. Remove 26 bolts (2) and the washers from the rim. 7. Use the hoist to carefully remove tire (3) and the rim as a unit. The combined weight of the tire and the rim is 815 kg (1800 lb). 8. Repeat the procedure for the removal of the other front tire. Installation Procedure 1. Thoroughly clean the contacting surfaces of the rim assembly and axle housing. 2. Fasten a hoist and suitable lifting slings to tire (3) and the rim, as shown. 3. Use the hoist to carefully install tire (3) and the rim as a unit. The combined weight of the tire and the ring is 815 kg (1800 lb). 4. Install bolts (2) and the washers in the rim. Tighten the bolts to a torque of 750 80 N m (550 60 lb ft). 5. Repeat the procedure for the installation of the other front tire. https://127.0.0.1/sisweb/sisweb/techdoc/techdoc_print_page.jsp?returnurl=/sisweb/sisw... 2022/2/21
w 3/5(W) 6. Move lockring ring (1) up from Tooling (A). 7. Lower the machine to the ground. 8. Remove Tooling (A). 9. Remove the wood blocks from the rear tires. End By: a. Install the front fenders. Refer to Disassembly and Assembly, "Fender - Remove and Install" for the machine that is being serviced. b. Separate the steering frame lock. Refer to Disassembly and Assembly, "Steering Frame Lock - Separate and Connect" for the machine that is behind serviced. Remove & Install Rear Tires & Rim Assemblies https://127.0.0.1/sisweb/sisweb/techdoc/techdoc_print_page.jsp?returnurl=/sisweb/sisw... 2022/2/21
w 4/5(W) Connect steering frame lock link (1) to the loader frames of the machine before lifting the machine and removing the rear tire and rim assemblies. 1. Connect the steering frame lock link. See the topic, "Separate & Connect Steering Frame Lock Link" in this module. 2. Put wood blocks in front of and behind the front tires. 3. Position tooling (A) under the rear axle housing assembly as shown. Raise the rear of the machine until the rear tires are just off the floor. 4. Put tooling (B) in position under the rear of the machine as shown. Use tooling (A) to lower the weight of the machine onto tooling (B). The rear axle housing group is made to oscillate. During removal and installation of the rear tires and rim assemblies, the rear axle housing https://127.0.0.1/sisweb/sisweb/techdoc/techdoc_print_page.jsp?returnurl=/sisweb/sisw... 2022/2/21
w 5/5(W) group must be blocked to prevent the machine from oscillating. Improper blocking of the rear axle housing assembly can result in possible personal injury. 5. Put wood blocks between the rear axle housing assembly and the frame of the machine on both sides of the machine as shown. The wood blocks must have a tight fit. NOTE: Tooling (C) turns in approximately 60 increments. 6. Use tooling (C) and the appropriate size socket to loosen twenty nuts (2) that hold the tire and rim assembly to the wheel assembly. DO NOT remove the nuts at this time. 7. Fasten lifting cables and a hoist to the rear tire and rim assembly as shown. Remove twenty nuts (2) and the washers that hold the rear tire and rim assembly in place. Remove rear tire and rim assembly (3). The weight of the rear tire and rim assembly is 612 kg (1350 lb). 8. Remove the other rear tire and rim assembly as in Step 6 and 7. NOTE: The following steps are for the installation of the rear tires and rim assemblies. 9. Be sure the mating surface of the rim assembly and wheel assembly are clean and free of dirt and debris prior to installing the tire and rim assembly. 10. Fasten lifting cables and a hoist to tire and rim assembly (3). Put the tire and rim assembly in position on the wheel assembly. 11. Install the twenty washers and nuts (2) that hold the tire and rim assembly in place. 12. Using tool (C) and the appropriate size socket, tighten nuts (2) to a torque of 750 80 N m (550 60 lb ft). 13. Install the other rear tire and rim assembly as in Steps 9 through 12. 14. Raise the rear of the machine with tooling (A), and remove tooling (B) from under the rear axle housing assembly. Lower the machine to the floor with tooling (A). 15. Separate the steering frame lock link. See the topic, "Separate & Connect Steering Frame Lock Link" in this module. Copyright 1993 - 2022 Caterpillar Inc. Mon Feb 21 10:45:29 UTC+0800 2022 All Rights Reserved. Private Network For SIS Licensees. https://127.0.0.1/sisweb/sisweb/techdoc/techdoc_print_page.jsp?returnurl=/sisweb/sisw... 2022/2/21
w 1/3(W) Shutdown SIS Previous Screen Product: WHEEL LOADER Model: 980F WHEEL LOADER 5XJ Configuration: 980F WHEEL LOADER 5XJ00001-00616 (MACHINE) POWERED BY 3406 ENGINE Disassembly and Assembly 980F & 980F SERIES II WHEEL LOADERS POWER TRAIN Media Number -SENR4991-02 Publication Date -01/08/2004 Date Updated -18/04/2012 SENR49910005 Drive Axle Shafts SMCS - 3278-011; 3278-012 Remove Drive Axle Shafts 1. Start the machine, and move it forward or to the rear until drain plug (3) is in the position shown. 2. Drain the oil from the final drive to be serviced into a suitable container. The capacity of the front axle housing group is 87 liters (23 U.S. gal). The capacity of the rear axle housing group is 81 liters (21.4 U.S. gal). 3. Remove bolts (1). Remove cover assembly (2). Remove the O-ring seal from the cover assembly. NOTE: If the axle shaft can not be removed from the final drive, move the machine a small amount to the front or rear until the axle shaft can be pulled free from the final drive. https://127.0.0.1/sisweb/sisweb/techdoc/techdoc_print_page.jsp?returnurl=/sisweb/sisw... 2022/2/21
w 2/3(W) 4. Install a 7/16" - 14 NC forged eyebolt (4) in the end of the axle shaft as shown. Pull the axle shaft out of the final drive approximately 381 mm (15 in). Fasten a lifting strap and a hoist to the axle shaft. Remove axle shaft (5). The weight of the axle shaft is 34 kg (75 lb). 5. Remove retainer ring (6) from the axle shaft. Remove sun gear (7). Install Drive Axle Shafts 1. Be sure the axle shaft is clean and free of dirt and foreign material. 2. Fasten a lifting strap and a hoist to the axle shaft. Put axle shaft (1) in position in the final drive. 3. Install sun gear (3) half way on the end of the axle shaft. 4. Slide pipe (2) which has a 50.8 mm (2 in) outside diameter and is 610 mm (24 in) long into the end of sun gear (3) as shown. Push down on pipe, and slide the axle shaft into position on the final drive. 5. Remove the pipe. Slide sun gear (3) into position in the final drive planetary carrier. 6. Install retainer ring on the end of the axle shaft. Turn the flat sides of the three planet shafts toward the outside to provide clearance for the counterbore in cover assembly (4). https://127.0.0.1/sisweb/sisweb/techdoc/techdoc_print_page.jsp?returnurl=/sisweb/sisw... 2022/2/21
w 3/3(W) NOTICE If cover assembly (4) does not fit flat up against the final drive, remove the cover assembly, and repeat Step 6. 7. Check the condition of the O-ring seal used on the cover assembly (4). If the seal is worn or damaged, use a new part for replacement. Install the O-ring seal and cover assembly (4) on the final drive planetary carrier. 8. Fill the front or rear axle housing groups with oil to the correct level. See the Operation & Maintenance Manual for the correct filling procedure. Copyright 1993 - 2022 Caterpillar Inc. Mon Feb 21 10:46:25 UTC+0800 2022 All Rights Reserved. Private Network For SIS Licensees. https://127.0.0.1/sisweb/sisweb/techdoc/techdoc_print_page.jsp?returnurl=/sisweb/sisw... 2022/2/21
w 1/3(W) Shutdown SIS Previous Screen Product: WHEEL LOADER Model: 980F WHEEL LOADER 5XJ Configuration: 980F WHEEL LOADER 5XJ00001-00616 (MACHINE) POWERED BY 3406 ENGINE Disassembly and Assembly 980F & 980F SERIES II WHEEL LOADERS POWER TRAIN Media Number -SENR4991-02 Publication Date -01/08/2004 Date Updated -18/04/2012 SENR49910006 Final Drive Planet Carriers SMCS - 4092-010; 4092-017 Remove & Install Final Drive Planet Carriers Start By: a. remove drive axle shafts b. remove tires and rim assemblies (front or rear) 1. Turn the wheel assembly so drain plug (2) is at the bottom of the wheel assembly. 2. Remove three bolts (1) that hold the final drive planet carrier to the wheel assembly. https://127.0.0.1/sisweb/sisweb/techdoc/techdoc_print_page.jsp?returnurl=/sisweb/sisw... 2022/2/21
w 2/3(W) 3. Pull the final drive planet carrier outward on the studs approximately 38.1 mm (1.50 in). Fasten tool (A) to the final drive planet carrier as shown. Fasten a hoist to tool (A). Remove the final drive planet carrier (3). The weight of the final drive planet carrier is 79 kg (175 lb). 4. Remove the O-ring seal from the final drive planet carrier. 5. Put retainer (4) under compression. Slide ring gear (5) outward approximately 6.4 mm (.25 in) so the retainer ring can not go back into the groove in the ring gear. 6. Fasten tool (B) to a hoist. Put tool (B) in position in the groove of the ring gear as shown. Remove the ring gear. The weight of the ring gear is 24 kg (53 lb). NOTE: The following steps are for the installation of the final drive planet carriers. 7. Fasten a hoist and tool (B) to ring gear (5). Put the ring gear in position in the wheel assembly. Put retainer ring (4) in the hub assembly under compression. Slide the ring gear on the hub assembly until the retainer ring can be installed in the groove of the ring gear. 8. Check the condition of the O-ring seal used on final drive planet carrier (3). If the seal is worn or damaged, use a new part for replacement. Install the O-ring seal used on the final drive planet carrier. 9. Install tooling (A) on the final drive planet carrier. Fasten a hoist to tooling (A). Put SAE 90 oil on the O-ring seal. Put the final drive planet carrier in position on the wheel assembly. Install three bolts (1) that hold it. Tighten the bolts to a torque of 55 7 N m (41 5 lb ft). End By: https://127.0.0.1/sisweb/sisweb/techdoc/techdoc_print_page.jsp?returnurl=/sisweb/sisw... 2022/2/21
w 3/3(W) a. install tires and rim assemblies (front or rear) b. install drive axle shafts Disassemble & Assemble Final Drive Planet Carriers Start By: a. remove final drive planet carriers 1. Remove three planetary shafts (1) from the planetary carrier. NOTE: Identify the position of the six steel and six bronze spacers used in the final drive planet carrier. 2. Remove three planetary gears (2) and the twelve spacers from the planetary carrier. 3. Remove the lock ring from each planetary shaft (1). 4. Remove the sleeve bearing from each planetary gear (2). NOTE: The following steps are for the assembly of the final drive planet carrier. 5. Install a sleeve bearing in each planetary gear (2). 6. Install a lock ring on each planetary shaft (1). 7. Put planetary gears in position in the planetary carrier. Install the steel spacers next to the planetary gears and the bronze spacers between the planetary carrier and the steel spacers. Be sure the oil grooves on the steel spacers are facing toward the bronze spacers. 8. Install the three planetary shafts in the planetary carrier. Be sure the flat side on each planetary shaft in facing toward the outside diameter of the planetary carrier. End By: a. install final drive planet carriers Copyright 1993 - 2022 Caterpillar Inc. Mon Feb 21 10:47:21 UTC+0800 2022 All Rights Reserved. Private Network For SIS Licensees. https://127.0.0.1/sisweb/sisweb/techdoc/techdoc_print_page.jsp?returnurl=/sisweb/sisw... 2022/2/21
Suggest: If the above button click is invalid. Please download this document first, and then click the above link to download the complete manual. Thank you so much for reading
w 1/13(W) Shutdown SIS Previous Screen Product: WHEEL LOADER Model: 980F WHEEL LOADER 5XJ Configuration: 980F WHEEL LOADER 5XJ00001-00616 (MACHINE) POWERED BY 3406 ENGINE Disassembly and Assembly 980F & 980F SERIES II WHEEL LOADERS POWER TRAIN Media Number -SENR4991-02 Publication Date -01/08/2004 Date Updated -18/04/2012 SENR49910007 Wheel Assemblies & Wheel Brake Assemblies SMCS - 4208; 4251-016; 4251-011; 4251-012; 4251-015 Remove Wheel Assemblies & Wheel Brake Assemblies Start By: a. remove final drive planet carriers 1. Disconnect brake tube assembly (3) from the elbow. 2. Remove bolts (1), and remove housing (2), the spring and piston from the anchor plate. https://127.0.0.1/sisweb/sisweb/techdoc/techdoc_print_page.jsp?returnurl=/sisweb/sisw... 2022/2/21
https://www.ebooklibonline.com Hello dear friend! Thank you very much for reading. Enter the link into your browser. The full manual is available for immediate download. https://www.ebooklibonline.com