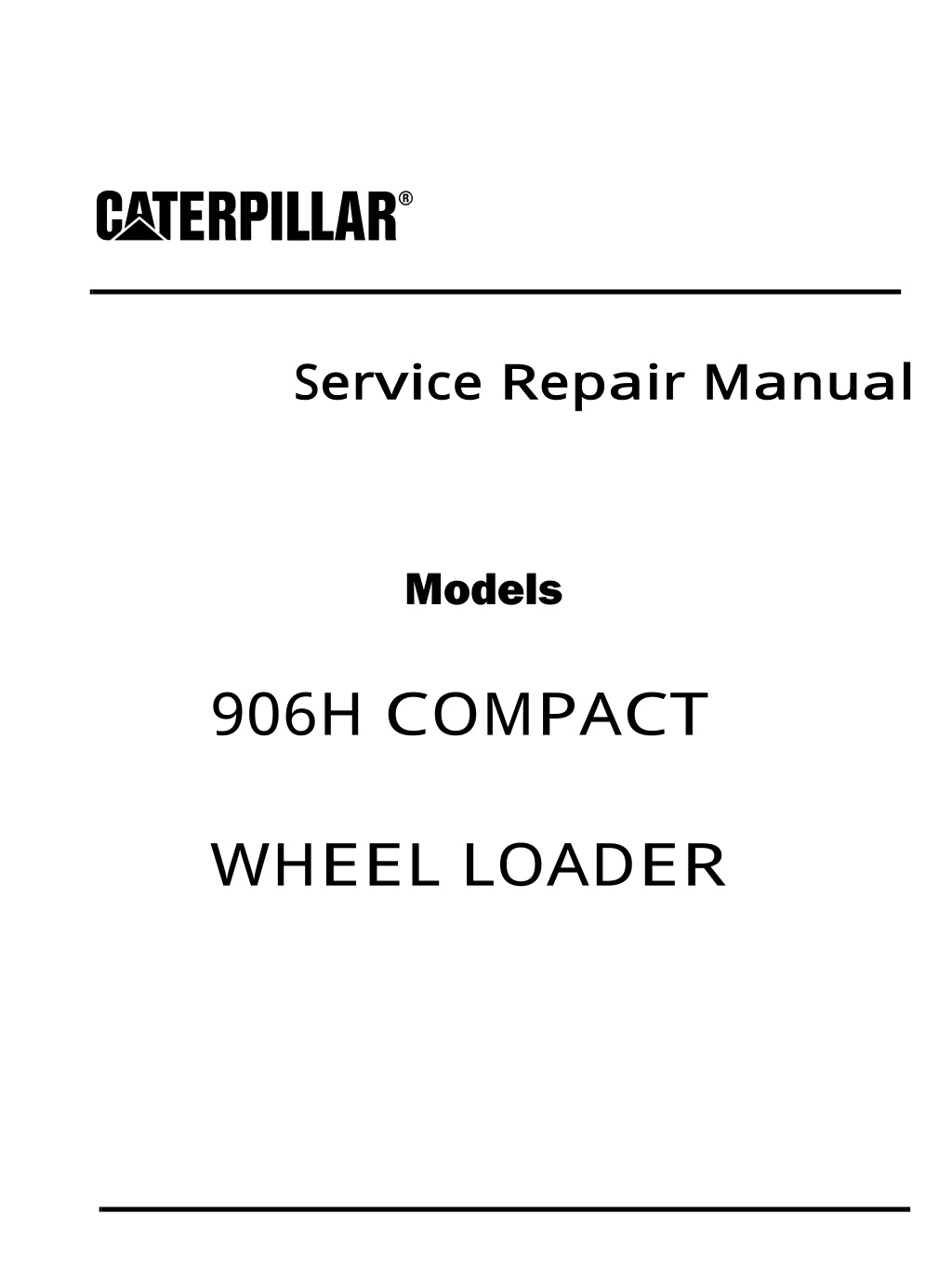
Caterpillar Cat 906H COMPACT WHEEL LOADER (Prefix SDH) Service Repair Manual Instant Download
Please open the website below to get the complete manualnn// n
Download Presentation

Please find below an Image/Link to download the presentation.
The content on the website is provided AS IS for your information and personal use only. It may not be sold, licensed, or shared on other websites without obtaining consent from the author. Download presentation by click this link. If you encounter any issues during the download, it is possible that the publisher has removed the file from their server.
E N D
Presentation Transcript
Service Repair Manual Models 906HCOM PACT WHEEL LOADER
w 1/3(W) Shutdown SIS Previous Screen Product: COMPACT WHEEL LOADER Model: 906H COMPACT WHEEL LOADER SDH Configuration: 906H Wheel Loader SDH00001-UP (MACHINE) POWERED BY C3.4 IND Engine Disassembly and Assembly 906H, 906H2, 907H, 907H2, 908H and 908H2 Compact Wheel Loaders Machine Systems Media Number -KENR5217-04 Publication Date -01/07/2017 Date Updated -26/07/2017 i02839373 Steering Frame Lock - Separate and Connect SMCS - 7506-029 Separation Procedure Personal injury or death can result from machine articulation or movement. Machine frames can move and a person can be crushed. Connect the steering frame lock link between the front and rear frames before working on machine. Secure clevis pin with locking pin. Before operating the machine, fasten the steering frame lock link into the stored position and secure the clevis pin with locking pin. Failure to lock into the stored position before operating can result in loss of steering. https://127.0.0.1/sisweb/sisweb/techdoc/techdoc_print_page.jsp?returnurl=/sisweb/siswe... 2019/9/2
w 2/3(W) Illustration 1 g01416219 1. Remove locking pin (1) and pin (2). Move steering frame lock (3) to the storage position. Illustration 2 g01416221 2. Install pin (2) through the frame and through steering frame lock (3). Install locking pin (1). Connection Procedure Personal injury or death can result from machine articulation or movement. Machine frames can move and a person can be crushed. Connect the steering frame lock link between the front and rear frames before working on machine. Secure clevis pin with locking pin. Before operating the machine, fasten the steering frame lock link into the stored position and secure the clevis pin with locking pin. Failure to lock into the stored position before operating can result in loss of steering. https://127.0.0.1/sisweb/sisweb/techdoc/techdoc_print_page.jsp?returnurl=/sisweb/siswe... 2019/9/2
https://www.ebooklibonline.com Hello dear friend! Thank you very much for reading. Enter the link into your browser. The full manual is available for immediate download. https://www.ebooklibonline.com
w 3/3(W) Illustration 3 g01416221 1. Remove locking pin (1) from pin (2). Illustration 4 g01416219 2. Move steering frame lock (3) in position to the front frame. Install pin (2) and locking pin (1). Locking pin (1). Note: To align the pin bores, move the front loader frame. Copyright 1993 - 2019 Caterpillar Inc. Mon Sep 2 07:07:35 UTC+0800 2019 All Rights Reserved. Private Network For SIS Licensees. https://127.0.0.1/sisweb/sisweb/techdoc/techdoc_print_page.jsp?returnurl=/sisweb/siswe... 2019/9/2
w 1/4(W) Shutdown SIS Previous Screen Product: COMPACT WHEEL LOADER Model: 906H COMPACT WHEEL LOADER SDH Configuration: 906H Wheel Loader SDH00001-UP (MACHINE) POWERED BY C3.4 IND Engine Disassembly and Assembly 906H, 906H2, 907H, 907H2, 908H and 908H2 Compact Wheel Loaders Machine Systems Media Number -KENR5217-04 Publication Date -01/07/2017 Date Updated -26/07/2017 i05750795 System Pressure - Release SMCS - 4250-553-PX; 4300-553-PX; 4350-553-PX; 5050-553-PX Release Procedure Personal injury can result from hydraulic oil pressure and hot oil. Hydraulic oil pressure can remain in the hydraulic system after the engine has been stopped. Serious injury can be caused if this pressure is not released before any service is done on the hydraulic system. Make sure all of the attachments have been lowered, oil is cool before removing any components or lines. Remove the oil filler cap only when the engine is stopped, and the filler cap is cool enough to touch with your bare hand. Hydraulic System Hydraulic oil pressure can remain in the hydraulic system on this machine after the engine and pump have been stopped. Serious injury can result if this pressure is not released before any service is done on the hydraulic system. In order to prevent possible injury, release the hydraulic system pressure before working on any fitting, hose, or hydraulic component. https://127.0.0.1/sisweb/sisweb/techdoc/techdoc_print_page.jsp?returnurl=/sisweb/siswe... 2019/9/2
w 2/4(W) Lower all work tools to the ground before service is started. If the hydraulic system must be serviced, tested, or adjusted with the work tool in the raised position, the work tool and lift cylinders must be supported properly. Always move the machine to a location away from the travel of other machines. Be sure that other personnel are not near the machine when the engine is running and tests or adjustments are being made. 1. Park the machine on a hard, smooth, level surface. The location should also be dry and free of debris. 2. Permit only one operator on the machine. All other personnel should be kept away from the machine. 3. If the machine is equipped with a ride control system, place the ride control system into Service .mode. Refer to Ride Control in this Operation and Maintenance, "Operator Controls" section. Illustration 1 g02727672 4. Position the bucket or the work tool just above the ground at a slight downward angle. This position will ensure that the head end of the lift cylinders is pressurized. 5. Engage the parking brake. 6. Turn the engine start switch to the OFF position. 7. When the engine has stopped, turn the engine start switch back to the ON position so the pilot oil can reach the main valve. 8. Move the implement lockout switch to the UNLOCKED position. https://127.0.0.1/sisweb/sisweb/techdoc/techdoc_print_page.jsp?returnurl=/sisweb/siswe... 2019/9/2
w 3/4(W) 9. Move the lift control lever to the FLOAT position and the tilt control lever to the TILT BACK position at the same time. This action allows the bucket or the work tool to tilt back while the boom is lowered. The bottom of the bucket or the work tool should rest flat on the ground. The weight of the linkage should be supported by the ground. The pressure from the head end of the lift cylinders and from the ride control accumulator is now vented to the hydraulic tank. 10. When the bucket or the work tool has settled to the ground, move both control levers to the HOLD position. Cycle the control levers through all positions several times in order to purge any remaining pressure from the implement hydraulic system. This action will completely drain the pilot accumulator. 11. Turn the engine start switch to the OFF position. 12. Slowly loosen the hydraulic tank filler cap in order to release the pressure from the hydraulic tank. 13. After all of the pressure has been released, tighten the hydraulic tank filler cap. The hydraulic system pressure has now been released. Hydraulic lines and components can now be removed. Release Procedure (Steering System, Braking System, and Quick Coupler) (If Equipped) Personal injury can result from hydraulic oil pressure and hot oil. Hydraulic oil pressure can remain in the hydraulic system after the engine has been stopped. Serious injury can be caused if this pressure is not released before any service is done on the hydraulic system. Make sure all of the work tools have been lowered to the ground, and the oil is cool before removing any components or lines. Remove the oil filler cap only when the engine is stopped, and the filler cap is cool enough to touch with your bare hand. 1. Park the machine on a hard, smooth, level surface. The location should also be dry and free of debris. 2. Lower the bucket to the ground and stop the engine. 3. Engage the parking brake. 4. Turn the engine start switch to the OFF position. 5. Turn the steering wheel fully to the left and fully to the right several times to relieve the pressure in the steering system. https://127.0.0.1/sisweb/sisweb/techdoc/techdoc_print_page.jsp?returnurl=/sisweb/siswe... 2019/9/2
w 4/4(W) 6. Depress the brake pedal repeatedly in order to release any pressure in the braking system. When no more resistance is felt and no pressure release is heard, the braking system, and Quick Coupler pressure is released. 7. Slowly loosen the hydraulic tank filler cap in order to release the pressure from the hydraulic tank. 8. After all of the pressure has been released, tighten the hydraulic tank filler cap. The hydraulic system pressure has now been released. Hydraulic lines and components can now be removed. Copyright 1993 - 2019 Caterpillar Inc. Mon Sep 2 07:08:30 UTC+0800 2019 All Rights Reserved. Private Network For SIS Licensees. https://127.0.0.1/sisweb/sisweb/techdoc/techdoc_print_page.jsp?returnurl=/sisweb/siswe... 2019/9/2
w 1/3(W) Shutdown SIS Previous Screen Product: COMPACT WHEEL LOADER Model: 906H COMPACT WHEEL LOADER SDH Configuration: 906H Wheel Loader SDH00001-UP (MACHINE) POWERED BY C3.4 IND Engine Disassembly and Assembly 906H, 906H2, 907H, 907H2, 908H and 908H2 Compact Wheel Loaders Machine Systems Media Number -KENR5217-04 Publication Date -01/07/2017 Date Updated -26/07/2017 i03659004 Fuel Tank - Remove SMCS - 1273-011 Removal Procedure Start By: A. Remove the cab. Refer to Disassembly and Assembly, "Cab - Remove". 1. Drain the fuel from the fuel tank into a suitable container for storage or disposal. Refer to Operation and Maintenance Manual for the correct procedure. Illustration 1 g01418332 2. Remove bolts (1) . Remove cable assembly (2) from cover (3) and remove cover (3) . https://127.0.0.1/sisweb/sisweb/techdoc/techdoc_print_page.jsp?returnurl=/sisweb/siswe... 2019/9/2
w 2/3(W) Illustration 2 g01418333 3. Remove bolts (4) . Illustration 3 g01418334 4. Disconnect hoses (5) from fuel tank (7) . 5. Disconnect harness assembly (6) from fuel tank (7) . Illustration 4 g01418336 https://127.0.0.1/sisweb/sisweb/techdoc/techdoc_print_page.jsp?returnurl=/sisweb/siswe... 2019/9/2
w 3/3(W) Illustration 5 g01962922 The fuel tank has been removed for photographic purposes. 6. Disconnect hose assemblies (9) . Ensure that all hose assemblies (9) have been disconnected. Rotate pump (10) in order to remove fuel tank (7) . 7. Remove the nuts and straps (8) . Use two people and remove fuel tank (7) from the machine. The weight of fuel tank (7) is approximately 25 kg (55 lb). Copyright 1993 - 2019 Caterpillar Inc. Mon Sep 2 07:09:25 UTC+0800 2019 All Rights Reserved. Private Network For SIS Licensees. https://127.0.0.1/sisweb/sisweb/techdoc/techdoc_print_page.jsp?returnurl=/sisweb/siswe... 2019/9/2
w 1/3(W) Shutdown SIS Previous Screen Product: COMPACT WHEEL LOADER Model: 906H COMPACT WHEEL LOADER SDH Configuration: 906H Wheel Loader SDH00001-UP (MACHINE) POWERED BY C3.4 IND Engine Disassembly and Assembly 906H, 906H2, 907H, 907H2, 908H and 908H2 Compact Wheel Loaders Machine Systems Media Number -KENR5217-04 Publication Date -01/07/2017 Date Updated -26/07/2017 i03659035 Fuel Tank - Install SMCS - 1273-012 Installation Procedure Illustration 1 g01962922 The fuel tank has been removed for photographic purposes. https://127.0.0.1/sisweb/sisweb/techdoc/techdoc_print_page.jsp?returnurl=/sisweb/siswe... 2019/9/2
w 2/3(W) Illustration 2 g01418336 1. Use two people and install fuel tank (7) in the machine. The weight of fuel tank (7) is approximately 25 kg (55 lb). Install straps (8) and the nuts. 2. Reposition pump (10) for installation. Install the mounting bolts. 3. Connect hose assemblies (9) . Illustration 3 g01418334 4. Connect harness assembly (6) to fuel tank (7) . 5. Connect hoses (5) to fuel tank (7) . https://127.0.0.1/sisweb/sisweb/techdoc/techdoc_print_page.jsp?returnurl=/sisweb/siswe... 2019/9/2
w 3/3(W) Illustration 4 g01418333 6. Install bolts (4) . Illustration 5 g01418332 7. Install cable assembly (2) through cover (3) and install cover (3) . Remove bolts (1) . End By: Install the cab. Refer to Disassembly and Assembly, "Cab - Install". Copyright 1993 - 2019 Caterpillar Inc. Mon Sep 2 07:10:20 UTC+0800 2019 All Rights Reserved. Private Network For SIS Licensees. https://127.0.0.1/sisweb/sisweb/techdoc/techdoc_print_page.jsp?returnurl=/sisweb/siswe... 2019/9/2
w 1/2(W) Shutdown SIS Previous Screen Product: COMPACT WHEEL LOADER Model: 906H COMPACT WHEEL LOADER SDH Configuration: 906H Wheel Loader SDH00001-UP (MACHINE) POWERED BY C3.4 IND Engine Disassembly and Assembly 906H, 906H2, 907H, 907H2, 908H and 908H2 Compact Wheel Loaders Machine Systems Media Number -KENR5217-04 Publication Date -01/07/2017 Date Updated -26/07/2017 i02845610 Hydraulic Tank - Remove SMCS - 5056-011 Removal Procedure Start By: a. Remove the engine. Refer to Disassembly and Assembly, "Engine - Remove". b. Remove the gear pump (hydraulic fan). Refer to Disassembly and Assembly, "Hydraulic Fan - Remove". Illustration 1 g01418960 1. Remove bolts (2) and shroud (1). https://127.0.0.1/sisweb/sisweb/techdoc/techdoc_print_page.jsp?returnurl=/sisweb/siswe... 2019/9/2
w 2/2(W) Illustration 2 g01418961 2. Remove bolts (4) and move plate (3) out of the way. 3. Remove bolts (5) from the hydraulic tank. Illustration 3 g01418962 4. Loosen the clamp and disconnect hose (6) from the radiator. 5. Loosen the clamp and disconnect hose (7) from hydraulic oil tank (10). 6. Loosen the clamp and disconnect hose (11) from hydraulic oil tank (10). 7. Move harness assembly (9) out of the way. 8. Remove bolts (8) and hydraulic oil tank (10) from the machine. Copyright 1993 - 2019 Caterpillar Inc. Mon Sep 2 07:11:14 UTC+0800 2019 All Rights Reserved. Private Network For SIS Licensees. https://127.0.0.1/sisweb/sisweb/techdoc/techdoc_print_page.jsp?returnurl=/sisweb/siswe... 2019/9/2
w 1/2(W) Shutdown SIS Previous Screen Product: COMPACT WHEEL LOADER Model: 906H COMPACT WHEEL LOADER SDH Configuration: 906H Wheel Loader SDH00001-UP (MACHINE) POWERED BY C3.4 IND Engine Disassembly and Assembly 906H, 906H2, 907H, 907H2, 908H and 908H2 Compact Wheel Loaders Machine Systems Media Number -KENR5217-04 Publication Date -01/07/2017 Date Updated -26/07/2017 i02845614 Hydraulic Tank - Install SMCS - 5056-012 Installation Procedure Illustration 1 g01418962 1. Install hydraulic oil tank (10) in the machine and install bolts (8). 2. Reposition harness assembly (9). 3. Connect hose (11) to hydraulic oil tank (10) and tighten the clamp. 4. Connect hose (7) to hydraulic oil tank (10) and tighten the clamp. 5. Connect hose (6) to the radiator and tighten the clamp. https://127.0.0.1/sisweb/sisweb/techdoc/techdoc_print_page.jsp?returnurl=/sisweb/siswe... 2019/9/2
w 2/2(W) Illustration 2 g01418961 6. Install bolts (5) to the hydraulic oil tank. 7. Reposition plate (3) and install bolts (4). Illustration 3 g01418960 8. Install shroud (1) and bolts (2). End By: a. Install the gear pump (hydraulic fan). Refer to Disassembly and Assembly, "Hydraulic Fan - Install". b. Install the engine. Refer to Disassembly and Assembly, "Engine - Install". Copyright 1993 - 2019 Caterpillar Inc. Mon Sep 2 07:12:09 UTC+0800 2019 All Rights Reserved. Private Network For SIS Licensees. https://127.0.0.1/sisweb/sisweb/techdoc/techdoc_print_page.jsp?returnurl=/sisweb/siswe... 2019/9/2
w 1/2(W) Shutdown SIS Previous Screen Product: COMPACT WHEEL LOADER Model: 906H COMPACT WHEEL LOADER SDH Configuration: 906H Wheel Loader SDH00001-UP (MACHINE) POWERED BY C3.4 IND Engine Disassembly and Assembly 906H, 906H2, 907H, 907H2, 908H and 908H2 Compact Wheel Loaders Machine Systems Media Number -KENR5217-04 Publication Date -01/07/2017 Date Updated -26/07/2017 i02867148 Gear Pump (Implement) (Steering) (Hydraulic Fan) - Remove SMCS - 1387-011-GT; 4306-011-GT; 5073-011-HFN; 5073-011-ZI; 5084-011-GT Removal Procedure Personal injury can result from hydraulic oil pressure and hot oil. Hydraulic oil pressure can remain in the hydraulic system after the engine has been stopped. Serious injury can be caused if this pressure is not released before any service is done on the hydraulic system. Make sure all of the work tools have been lowered to the ground, and the oil is cool before removing any components or lines. Remove the oil filler cap only when the engine is stopped, and the filler cap is cool enough to touch with your bare hand. NOTICE Care must be taken to ensure that fluids are contained during performance of inspection, maintenance, testing, adjusting, and repair of the machine. Be prepared to collect the fluid with suitable containers before opening any compartment or disassembling any component containing fluids. https://127.0.0.1/sisweb/sisweb/techdoc/techdoc_print_page.jsp?returnurl=/sisweb/siswe... 2019/9/2
w 2/2(W) Refer to Special Publication, NENG2500, "Caterpillar Tools and Shop Products Guide"for tools and supplies to collect and contain fluids in Caterpillar machines. Dispose of all fluids according to local regulations. Note: Put identification marks on all lines, on all hoses, on all wires, and on all tubes for installation purposes. Plug all lines, hoses, and tubes. This helps to prevent fluid loss and this helps to keep contaminants from entering the system. 1. Drain the hydraulic oil from the hydraulic oil tank into a suitable container for storage or disposal. Refer to Operation and Maintenance Manual for the correct procedure. Illustration 1 g01320213 2. Disconnect hose assembly (2), hose assembly (4), hose assembly (5), and hose assembly (6) from gear pump (3). 3. Disconnect harness assembly (7) from gear pump (3). 4. Remove bolts (1) and remove gear pump (3). Copyright 1993 - 2019 Caterpillar Inc. Mon Sep 2 07:13:04 UTC+0800 2019 All Rights Reserved. Private Network For SIS Licensees. https://127.0.0.1/sisweb/sisweb/techdoc/techdoc_print_page.jsp?returnurl=/sisweb/siswe... 2019/9/2
w 1/12(W) Shutdown SIS Previous Screen Product: COMPACT WHEEL LOADER Model: 906H COMPACT WHEEL LOADER SDH Configuration: 906H Wheel Loader SDH00001-UP (MACHINE) POWERED BY C3.4 IND Engine Disassembly and Assembly 906H, 906H2, 907H, 907H2, 908H and 908H2 Compact Wheel Loaders Machine Systems Media Number -KENR5217-04 Publication Date -01/07/2017 Date Updated -26/07/2017 i02870251 Gear Pump (Implement) (Steering) (Hydraulic Fan) - Disassemble SMCS - 1387-015-GT; 4306-015-GT; 5073-015-HFN; 5073-015-ZI; 5084-015-GT Disassembly Procedure Table 1 Required Tools Tool Part Number Part Description Qty A 1P-1857 Retaining Ring Pliers 1 Start By: a. Remove the gear pump. Refer to Disassembly and Assembly, "Gear Pump - Remove". https://127.0.0.1/sisweb/sisweb/techdoc/techdoc_print_page.jsp?returnurl=/sisweb/siswe... 2019/9/2
w 2/12(W) Illustration 1 g01037416 1. Remove bolts (1) and cover (2). https://127.0.0.1/sisweb/sisweb/techdoc/techdoc_print_page.jsp?returnurl=/sisweb/siswe... 2019/9/2
w 3/12(W) Illustration 2 g01037417 2. Remove seals (3) and bearing (4). https://127.0.0.1/sisweb/sisweb/techdoc/techdoc_print_page.jsp?returnurl=/sisweb/siswe... 2019/9/2
w 4/12(W) Illustration 3 g01037418 3. Remove gears (5), bearing (6), and seals (7). https://127.0.0.1/sisweb/sisweb/techdoc/techdoc_print_page.jsp?returnurl=/sisweb/siswe... 2019/9/2
w 5/12(W) Illustration 4 g01037421 4. Remove seal (8), housing (9), seal (10), plate (10A), and seal (11). https://127.0.0.1/sisweb/sisweb/techdoc/techdoc_print_page.jsp?returnurl=/sisweb/siswe... 2019/9/2
w 6/12(W) Illustration 5 g01037420 5. Remove seals (12) and bearing (13). https://127.0.0.1/sisweb/sisweb/techdoc/techdoc_print_page.jsp?returnurl=/sisweb/siswe... 2019/9/2
w 7/12(W) Illustration 6 g01037419 6. Remove gears (14), bearing (15), seals (17), and seal (16). https://127.0.0.1/sisweb/sisweb/techdoc/techdoc_print_page.jsp?returnurl=/sisweb/siswe... 2019/9/2
Suggest: If the above button click is invalid. Please download this document first, and then click the above link to download the complete manual. Thank you so much for reading
w 8/12(W) Illustration 7 g01037422 7. Remove housing (18) and seal (19). https://127.0.0.1/sisweb/sisweb/techdoc/techdoc_print_page.jsp?returnurl=/sisweb/siswe... 2019/9/2
https://www.ebooklibonline.com Hello dear friend! Thank you very much for reading. Enter the link into your browser. The full manual is available for immediate download. https://www.ebooklibonline.com