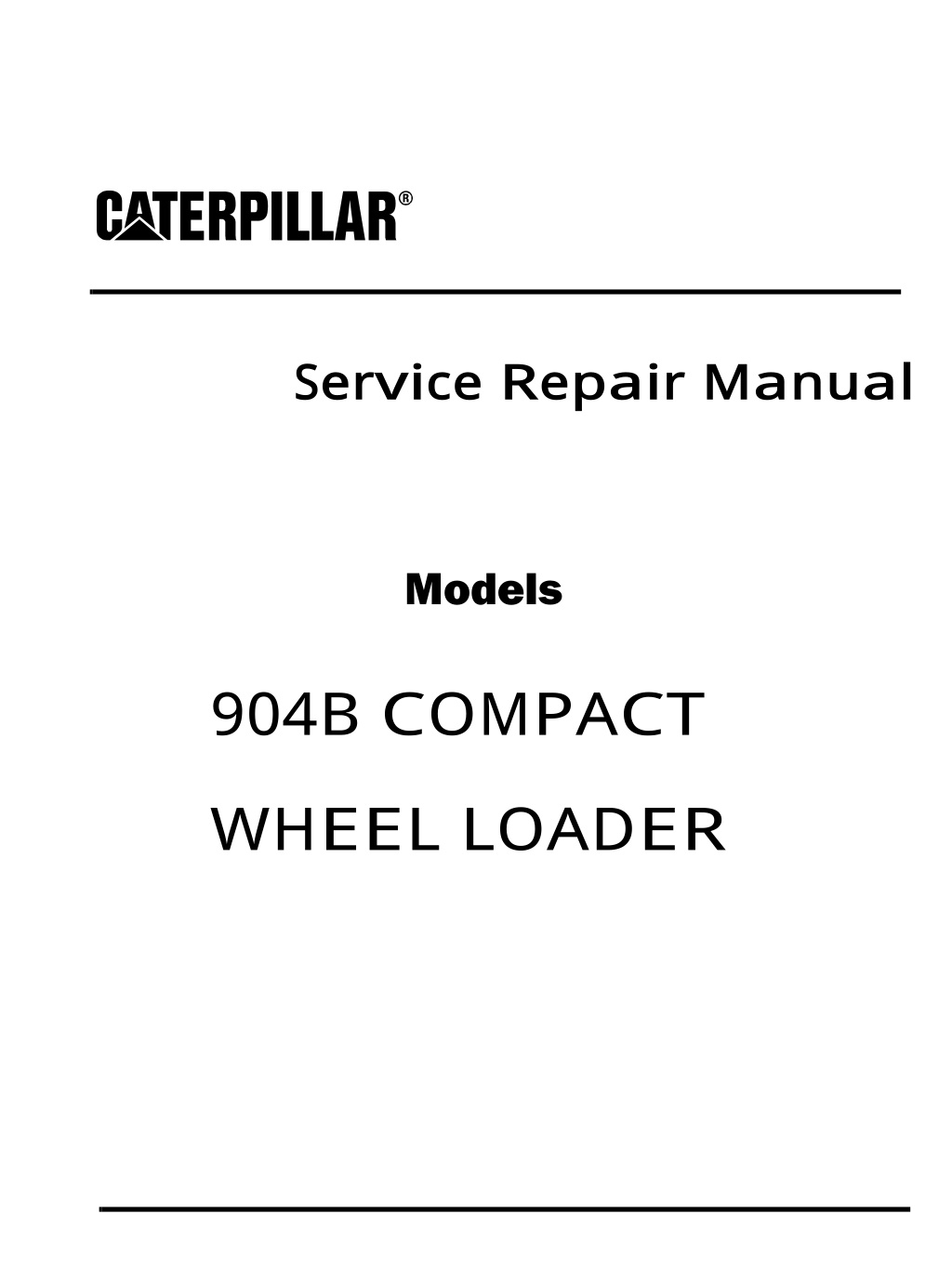
Caterpillar Cat 904B COMPACT WHEEL LOADER (Prefix B4L) Service Repair Manual Instant Download
Please open the website below to get the complete manualnn//
Download Presentation

Please find below an Image/Link to download the presentation.
The content on the website is provided AS IS for your information and personal use only. It may not be sold, licensed, or shared on other websites without obtaining consent from the author. Download presentation by click this link. If you encounter any issues during the download, it is possible that the publisher has removed the file from their server.
E N D
Presentation Transcript
Service Repair Manual Models 904BCOM PACT WHEEL LOADER
w 1/8(W) Shutdown SIS Previous Screen Product: COMPACT WHEEL LOADER Model: 904B COMPACT WHEEL LOADER B4L Configuration: 904B Compact Wheel Loader B4L00001-UP (MACHINE) POWERED BY S4Q2T Engine Disassembly and Assembly 904B Wheel LoaderPower Train Media Number -RENR9758-00 Publication Date -01/06/2005 Date Updated -23/06/2005 i02338391 Piston Pump (Hydrostatic) - Remove SMCS - 3203-011 Removal Procedure Table 1 Tool Part Number Description Quantity A 140-7742 Sleeve 1 1U-9200 Ratchet 1 B 189-0410 Shackle 1 C 242-6163 Wrench 1 Start By: A. Remove the seat. Refer to Disassembly and Assembly, "Seat - Remove". B. Remove the gear pump. Refer to Disassembly and Assembly, "Gear Pump - Remove". Personal injury can result from hydraulic oil pressure and hot oil. Hydraulic oil pressure can remain in the hydraulic system after the engine has been stopped. Serious injury can be caused if this pressure is not released before any service is done on the hydraulic system. Make sure all of the attachments have been lowered, oil is cool before removing any components or lines. Remove the oil filler cap only when the engine is stopped, and the filler cap is cool enough to touch with your bare hand. https://127.0.0.1/sisweb/sisweb/techdoc/techdoc_print_page.jsp?returnurl=/sisweb/sisw... 2019/8/31
w 2/8(W) NOTICE Care must be taken to ensure that fluids are contained during performance of inspection, maintenance, testing, adjusting and repair of the machine. Be prepared to collect the fluid with suitable containers before opening any compartment or disassembling any component containing fluids. Refer to Special Publication, NENG2500, "Caterpillar Tools and Shop Products Guide", for tools and supplies suitable to collect and contain fluids in Caterpillar machines. Dispose of all fluids according to local regulations and mandates. Note: Put identification marks on all lines, on all hoses, on all wires, and on all tubes for installation purposes. Plug all lines, all hoses and all tubes. This helps to prevent fluid loss and this helps to keep contaminants from entering the system. Illustration 1 g01167299 1. Remove plate (1) . https://127.0.0.1/sisweb/sisweb/techdoc/techdoc_print_page.jsp?returnurl=/sisweb/sisw... 2019/8/31
https://www.ebooklibonline.com Hello dear friend! Thank you very much for reading. Enter the link into your browser. The full manual is available for immediate download. https://www.ebooklibonline.com
w 3/8(W) Illustration 2 g01167332 2. Disconnect harness assembly (2) . Illustration 3 g01167334 3. Disconnect hose assemblies (3) and (4) from piston pump (5) . https://127.0.0.1/sisweb/sisweb/techdoc/techdoc_print_page.jsp?returnurl=/sisweb/sisw... 2019/8/31
w 4/8(W) Illustration 4 g01167336 4. Disconnect hose assemblies (6) and (7) from piston pump (5) . Illustration 5 g01167337 5. Disconnect hose assemblies (8) and (9) from piston pump (5) . https://127.0.0.1/sisweb/sisweb/techdoc/techdoc_print_page.jsp?returnurl=/sisweb/sisw... 2019/8/31
w 5/8(W) Illustration 6 g01167341 6. Disconnect cable assembly (10) from piston pump (5). Disconnect hose assembly (11) from piston pump (5) . Illustration 7 g01167425 7. Disconnect hose assembly (12) from the bottom of piston pump (5) . https://127.0.0.1/sisweb/sisweb/techdoc/techdoc_print_page.jsp?returnurl=/sisweb/sisw... 2019/8/31
w 6/8(W) Illustration 8 g01167342 Illustration 9 g01167431 8. Attach Tooling (A) and Tooling (B) to the cab. https://127.0.0.1/sisweb/sisweb/techdoc/techdoc_print_page.jsp?returnurl=/sisweb/sisw... 2019/8/31
w 7/8(W) Illustration 10 g01167343 9. Attach Tooling (B) and a suitable lifting device to piston pump (5) . Illustration 11 g01167344 10. Use Tooling (C) in order to remove mounting bolts (13) from piston pump (5) and mounting flange (14) . https://127.0.0.1/sisweb/sisweb/techdoc/techdoc_print_page.jsp?returnurl=/sisweb/sisw... 2019/8/31
w 8/8(W) Illustration 12 g01167346 11. Raise piston pump (5) in order to remove the pump from the machine. The weight of piston pump (5) is approximately 45 kg (100 lb). Copyright 1993 - 2019 Caterpillar Inc. Sat Aug 31 22:53:44 UTC+0800 2019 All Rights Reserved. Private Network For SIS Licensees. https://127.0.0.1/sisweb/sisweb/techdoc/techdoc_print_page.jsp?returnurl=/sisweb/sisw... 2019/8/31
w 1/23(W) Shutdown SIS Previous Screen Product: COMPACT WHEEL LOADER Model: 904B COMPACT WHEEL LOADER B4L Configuration: 904B Compact Wheel Loader B4L00001-UP (MACHINE) POWERED BY S4Q2T Engine Disassembly and Assembly 904B Wheel LoaderPower Train Media Number -RENR9758-00 Publication Date -01/06/2005 Date Updated -23/06/2005 i02327908 Piston Pump (Hydrostatic) - Disassemble SMCS - 3203-015 Disassembly Procedure Table 1 Required Tools Tool Part Number Part Description Qty A 1P-0510 Driver Group 1 B 1P-1861 Retaining Ring Pliers 1 C 5P-4758 Internal Pliers 1 D 1U-7600 Slide Hammer Puller 1 E 1P-1859 Retaining Ring Pliers 1 F 1P-1857 Retaining Ring Pliers 1 G 1S-4208 Spanner Wrench 1 Start By: A. Remove the hydraulic drive pump. Refer to Disassembly and Assembly, "Hydraulic Drive Pump - Remove". Personal injury can result from hydraulic oil pressure and hot oil. https://127.0.0.1/sisweb/sisweb/techdoc/techdoc_print_page.jsp?returnurl=/sisweb/sisw... 2019/8/31
w 2/23(W) Hydraulic oil pressure can remain in the hydraulic system after the engine has been stopped. Serious injury can be caused if this pressure is not released before any service is done on the hydraulic system. Make sure all of the work tools have been lowered to the ground, and the oil is cool before removing any components or lines. Remove the oil filler cap only when the engine is stopped, and the filler cap is cool enough to touch with your bare hand. Note: Cleanliness is an important factor. Before the disassembly procedure, the exterior of the component should be thoroughly cleaned. This will help to prevent dirt from entering the internal mechanism. Dirt and contaminants can damage the components of the pump or the motor. All disassembly and assembly procedures must be performed on a clean work surface. Clean all the interior components in clean solvent. Dry all the interior components with compressed air. Plug ports and plug hoses on the machine during repair. NOTICE Care must be taken to ensure that fluids are contained during performance of inspection, maintenance, testing, adjusting and repair of the product. Be prepared to collect the fluid with suitable containers before opening any compartment or disassembling any component containing fluids. Refer to Special Publication, NENG2500, "Caterpillar Tools and Shop Products Guide" for tools and supplies suitable to collect and contain fluids on Caterpillar products. Dispose of all fluids according to local regulations and mandates. Illustration 1 g00775547 1. Remove bolts (1) and remove charge pump (2) . https://127.0.0.1/sisweb/sisweb/techdoc/techdoc_print_page.jsp?returnurl=/sisweb/sisw... 2019/8/31
w 3/23(W) Illustration 2 g00716074 Note: Mark the location of the charge pump on the head assembly. Crescent (M) of gear set (4) must face toward the valves for installation purposes. The valves are indicated by arrows. 2. Remove O-ring seal (3). Remove gear set (4). Keep the gear set together in order to ensure proper installation of the gear set. Illustration 3 g00580966 3. Remove bushing (5). Note the orientation of the bushing. The bushing must be installed in the original location. https://127.0.0.1/sisweb/sisweb/techdoc/techdoc_print_page.jsp?returnurl=/sisweb/sisw... 2019/8/31
w 4/23(W) Illustration 4 g00580969 4. Remove plate (6). Note the position of the plate. Illustration 5 g00580995 5. Remove shaft (7) and O-ring seal (8) . Illustration 6 g00581004 6. Remove retaining ring (9) and key (10) from the shaft. https://127.0.0.1/sisweb/sisweb/techdoc/techdoc_print_page.jsp?returnurl=/sisweb/sisw... 2019/8/31
w 5/23(W) Illustration 7 g00581009 7. Remove bolts (11) and head assembly (12) . Illustration 8 g00581016 8. Remove O-ring seals (13) and (14) from the head. https://127.0.0.1/sisweb/sisweb/techdoc/techdoc_print_page.jsp?returnurl=/sisweb/sisw... 2019/8/31
w 6/23(W) Illustration 9 g00581023 Illustration 10 g00581022 9. Use Tooling (A) in order to remove bushing (15) . Illustration 11 g00581027 10. Remove bushing (16) . Note: Mark orientation of groove in bushing (16) for later installation of new bushing into the original location. https://127.0.0.1/sisweb/sisweb/techdoc/techdoc_print_page.jsp?returnurl=/sisweb/sisw... 2019/8/31
w 7/23(W) Illustration 12 g00794209 Note: Mark the position of the port plate for installation purposes. The groove in the port plate must face the two valves on the head assembly. 11. Remove port plate (17) and bearing (18), if necessary. Note: Perform Steps 12 and 13, if equipped. Illustration 13 g00794067 12. Remove plug assembly (19) from the head. https://127.0.0.1/sisweb/sisweb/techdoc/techdoc_print_page.jsp?returnurl=/sisweb/sisw... 2019/8/31
w 8/23(W) Illustration 14 g00794187 13. Disassemble the plug assembly, as follows: O-ring seal (20), O-ring seal (21) and locking plug (22) . Illustration 15 g00722813 14. Remove valve (23) from the head. https://127.0.0.1/sisweb/sisweb/techdoc/techdoc_print_page.jsp?returnurl=/sisweb/sisw... 2019/8/31
w 9/23(W) Illustration 16 g00581200 15. Disassemble the valve, as follows: O-ring seal (26), backup ring (25) and O-ring seal (24) . Illustration 17 g00581207 16. Remove valve (27) from the head. Refer to Step 15 for the disassembly procedure. Illustration 18 g01162895 https://127.0.0.1/sisweb/sisweb/techdoc/techdoc_print_page.jsp?returnurl=/sisweb/sisw... 2019/8/31
w 10/23(W) Illustration 19 g01162947 17. Remove caps (28), O-ring seals (31), coil (29), and coil (30) . Illustration 20 g01162896 18. Remove five bolts (32) . Illustration 21 g01162948 https://127.0.0.1/sisweb/sisweb/techdoc/techdoc_print_page.jsp?returnurl=/sisweb/sisw... 2019/8/31
w 11/23(W) Illustration 22 g01162976 Personal injury can result from being struck by parts propelled by a released spring force. Make sure to wear all necessary protective equipment. Follow the recommended procedure and use all recommended tooling to release the spring force. 19. Remove cartridge (33), cartridge (35), and gasket (34) . 20. Remove springs (36), retainers (37), and spool (39) from housing (38) . 21. Remove O-ring seal (40) . Illustration 23 g00581734 22. Remove barrel assembly (41) from the pump housing. Keep the barrel assembly together with the pistons. https://127.0.0.1/sisweb/sisweb/techdoc/techdoc_print_page.jsp?returnurl=/sisweb/sisw... 2019/8/31
w 12/23(W) Illustration 24 g00581740 23. Mark the location of the pistons in the barrel assembly. Remove pistons and plate (42) from the barrel assembly. Illustration 25 g00581773 24. Remove spring retainer (43) . https://127.0.0.1/sisweb/sisweb/techdoc/techdoc_print_page.jsp?returnurl=/sisweb/sisw... 2019/8/31
w 13/23(W) Illustration 26 g00581780 Personal injury can result from being struck by parts propelled by a released spring force. Make sure to wear all necessary protective equipment. Follow the recommended procedure and use all recommended tooling to release the spring force. 25. Remove shim (44) and springs (45). Note the position of the springs. The springs must be installed in the same position for proper clearance. Illustration 27 g00581784 Personal injury can result from being struck by parts propelled by a released spring force. Make sure to wear all necessary protective equipment. Follow the recommended procedure and use all recommended tooling to release the spring force. 26. Use a suitable press and Tooling (B) in order to remove retaining ring (46) . https://127.0.0.1/sisweb/sisweb/techdoc/techdoc_print_page.jsp?returnurl=/sisweb/sisw... 2019/8/31
w 14/23(W) Illustration 28 g00581786 27. Remove washer (47), spring (48), and washer (47) from the barrel assembly. Illustration 29 g00581792 28. Use Tooling (C) in order to remove retaining ring (49) . Illustration 30 g00581821 https://127.0.0.1/sisweb/sisweb/techdoc/techdoc_print_page.jsp?returnurl=/sisweb/sisw... 2019/8/31
w 15/23(W) 29. Use Tooling (D) in order to remove seal (50) . Illustration 31 g00581830 30. Use Tooling (C) in order to remove retaining ring (51) . Illustration 32 g00581848 Illustration 33 g00581850 https://127.0.0.1/sisweb/sisweb/techdoc/techdoc_print_page.jsp?returnurl=/sisweb/sisw... 2019/8/31
w 16/23(W) 31. Remove shaft (52). It may be necessary to use a soft faced hammer in order to remove the shaft. Illustration 34 g00581928 32. Use Tooling (E) in order to remove retaining ring (53) . Illustration 35 g00581934 33. Use a suitable press in order to remove shaft (52) from bearing (54) . https://127.0.0.1/sisweb/sisweb/techdoc/techdoc_print_page.jsp?returnurl=/sisweb/sisw... 2019/8/31
w 17/23(W) Illustration 36 g00581942 34. Remove swashplate assembly (55) . Illustration 37 g00581947 35. Remove plate (56) from the swashplate. Remove rods (57) from the swashplate. Illustration 38 g00582435 36. Remove bearings (58) . https://127.0.0.1/sisweb/sisweb/techdoc/techdoc_print_page.jsp?returnurl=/sisweb/sisw... 2019/8/31
w 18/23(W) Illustration 39 g01164798 37. Remove bearing cradles (59) . Illustration 40 g00720021 38. Remove plug (61) and retainer (60) on both sides of the pump housing. https://127.0.0.1/sisweb/sisweb/techdoc/techdoc_print_page.jsp?returnurl=/sisweb/sisw... 2019/8/31
w 19/23(W) Illustration 41 g00582463 Illustration 42 g00582491 39. Remove bolts (62). Remove cover (63) with valve assembly (64) . Illustration 43 g00582495 40. Remove bolts (65) and cover (66) . https://127.0.0.1/sisweb/sisweb/techdoc/techdoc_print_page.jsp?returnurl=/sisweb/sisw... 2019/8/31
w 20/23(W) Illustration 44 g00582504 41. Remove O-ring seal (67) from the cover. Illustration 45 g00794220 42. Remove nut (68). Unscrew the cover from the valve assembly. Illustration 46 g00794221 43. Remove O-ring seal (69) . https://127.0.0.1/sisweb/sisweb/techdoc/techdoc_print_page.jsp?returnurl=/sisweb/sisw... 2019/8/31
Suggest: If the above button click is invalid. Please download this document first, and then click the above link to download the complete manual. Thank you so much for reading
w 21/23(W) Illustration 47 g00794223 Ring (71) is on the opposite end. 44. Remove O-ring seal (72), and rings (70) and (71) from each side. Illustration 48 g00582619 Personal injury can result from parts and/or covers under spring pressure. Spring force will be released when covers are removed. Be prepared to hold spring loaded covers as the bolts are loosened. 45. Use a suitable press to relieve the pressure on the spring. Use Tooling (F) in order to remove retaining ring (73) . https://127.0.0.1/sisweb/sisweb/techdoc/techdoc_print_page.jsp?returnurl=/sisweb/sisw... 2019/8/31
https://www.ebooklibonline.com Hello dear friend! Thank you very much for reading. Enter the link into your browser. The full manual is available for immediate download. https://www.ebooklibonline.com