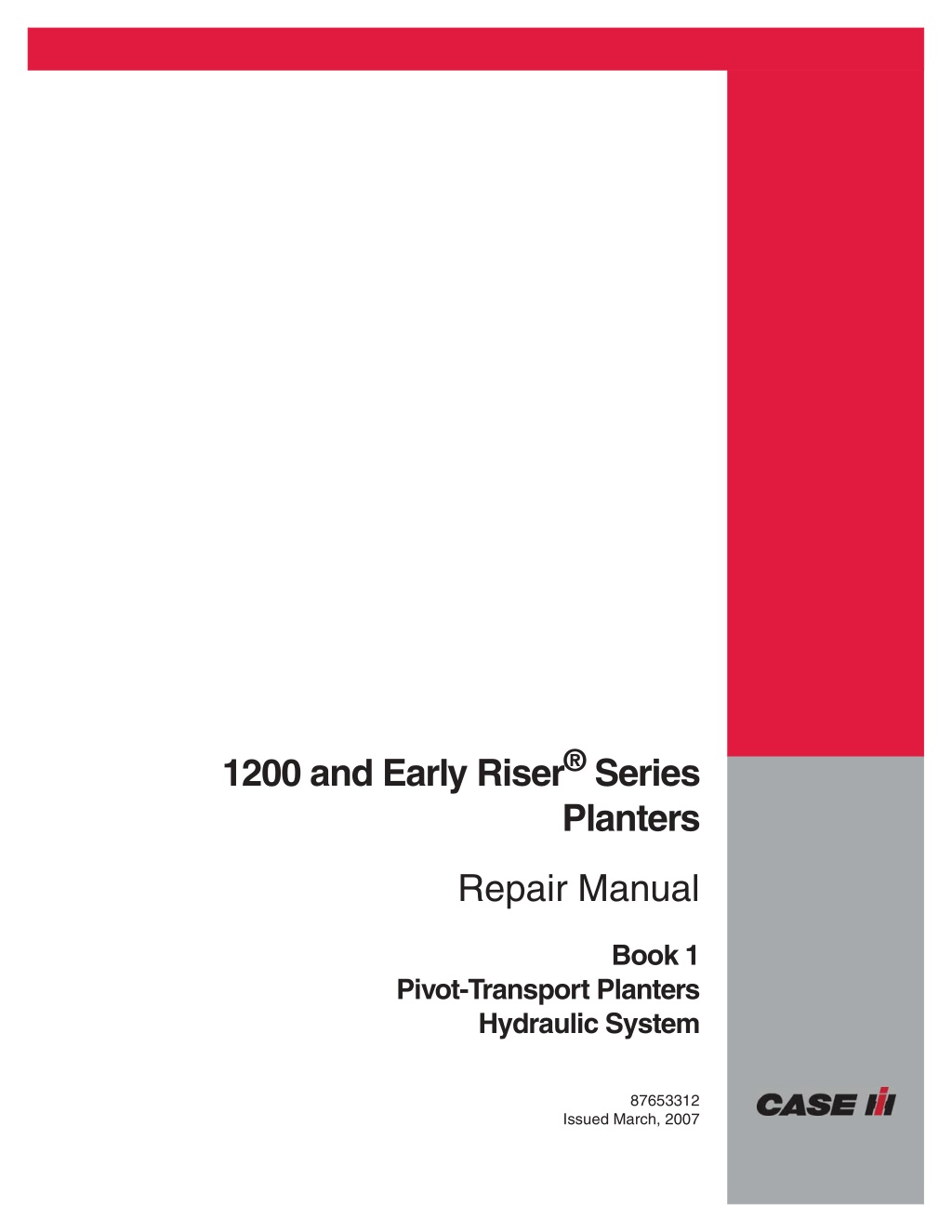
CASE IH 1200 and Early Riser Series Planters Service Repair Manual Instant Download
Please open the website below to get the complete manualnn// n
Download Presentation

Please find below an Image/Link to download the presentation.
The content on the website is provided AS IS for your information and personal use only. It may not be sold, licensed, or shared on other websites without obtaining consent from the author. Download presentation by click this link. If you encounter any issues during the download, it is possible that the publisher has removed the file from their server.
E N D
Presentation Transcript
1200 and Early Riser Series Planters Repair Manual Book 1 Pivot-Transport Planters Hydraulic System 87653312 Issued March, 2007
Repair Manual Number 87644966 1200 and Early Riser Series Planters (Replaces Complete Repair Manual 87057769) Book 1 - Publication 87653312 Pivot-Transport Planters Hydraulic System Book 11 - Publication 87653322 Variable Drive Mounted Stacker Planters Electrical System: Connectors, Schematic Electronic System: Fault Codes Book 2 - Publication 87653313 1250 Front Fold Planters Hydraulic System Book 12 - Publication 87653323 Ground Drive Planters - non-Gateway Trailing Rigid, Mounted Rigid, Mounted Stacker Electrical System: Connectors, Schematic Book 3 - Publication 87653314 Trailing Rigid, Mounted Rigid, Mounted Stacker Planters Hydraulic System Book 13 - Publication 87653324 Ground Drive Planters - non-Gateway Trailing Rigid, Mounted Rigid, Mounted Stacker Electronic System: Fault Codes Book 4 - Publication 87653315 Pivot-Transport Planters Electrical System: Connectors, Schematic Book 5 - Publication 87653316 Pivot-Transport Planters Electronic System - Part 1: MIU and MCC1 Fault Codes Book 14 - Publication 87653325 Ground Drive Planters - Gateway-equipped Trailing Rigid, Mounted Rigid, Mounted Stacker Electrical System: Connectors, Schematic Book 6 - Publication 87653317 Pivot-Transport Planters Electronic System - Part 2: MCC2 and Display Fault Codes Book 15 - Publication 87653326 Ground Drive Planters - Gateway equipped Trailing Rigid, Mounted Rigid, Mounted Stacker Electronic System: Fault Codes Book 7 - Publication 87653318 1250 Front Fold Planters Electrical System: Connectors, Schematic Book 16 - Publication 87653327 All Planters Wheels and Axles Book 8 - Publication 87653319 1250 Front Fold Planters Electronic System - Part 1: MIU and MCC1 Fault Codes Book 17 - Publication 87653328 All Planters Cylinders and Control Valves Book 9 - Publication 87653320 1250 Front Fold Planters Electronic System - Part 2: MCC2 and Display Fault Codes Book 18 - Publication 87653329 All Planters Planting Systems: Vacuum Fan, Bulk Fill Fan, Markers, Row Unit, Fertilizing System, Chemical System Book 10 - Publication 87653321 Variable Drive Trailing Rigid Planters Electrical System: Connectors, Schematic Electronic System: Fault Codes You can order Repair Manual Books separately (see publication numbers above) or you can order a complete Repair Manual 87644966.
INTRODUCTION 87644966 5 2/26/2007 1
https://www.ebooklibonline.com Hello dear friend! Thank you very much for reading. Enter the link into your browser. The full manual is available for immediate download. https://www.ebooklibonline.com
Contents INTRODUCTION Torque Hydraulic Tubes and Fittings 1200 Mounted Stacker, 1200 Mounted Rigid, 1200 Trailing Rigid, 1200 Pivot Transport Torque Fasteners 1200 Mounted Stacker, 1200 Mounted Rigid, 1200 Trailing Rigid, 1200 Pivot Transport Basic instructions Electrical testing 1200 Mounted Stacker, 1200 Mounted Rigid, 1200 Trailing Rigid, 1200 Pivot Transport 3 4 6 87644966 5 2/26/2007 2
INTRODUCTION Torque Hydraulic Tubes and Fittings 1200 Mounted Stacker, 1200 Mounted Rigid, 1200 Trailing Rigid, 1200 Pivot Transport Standard Torque Data for Hydraulic Tubes and Fittings Tube Nuts for 37 Flared Fittings O Ring Boss Plugs, Adjustable Fitting Lock Nuts, Swivel JIC 37 Seats LB FT Min Max 6 10 10 15 15 20 25 30 35 40 60 70 70 80 80 90 95 115 120 140 250 300 LB FT Min 9 12 21 35 53 77 90 110 140 160 225 Nm Min 12 16 29 47 72 104 122 149 190 217 305 Nm Min 8 14 20 34 47 81 95 108 129 163 339 Size Tubing OD Inches 1/4 5/16 3/8 1/2 5/8 3/4 7/8 1 1 1/4 1 1/2 2 Thread Size mm 6.4 7.9 9.5 12.7 15.9 19.1 22.2 25.4 31.8 38.1 50.8 Max 12 15 24 40 58 82 100 120 150 175 240 Max 16 20 33 54 79 111 136 163 204 237 325 Max 14 20 27 41 54 95 109 122 156 190 407 4 5 6 8 10 12 14 16 20 24 32 7/16 20 1/2 20 9/16 18 3/4 18 7/8 14 1 1/6 12 1 3/16 12 1 5/16 12 1 5/8 12 1 7/8 12 2 1/2 12 Above torque figures are recommended for plain, cadmium or zinc plated fittings, dry or wet installations and swivel nuts either swagged or brazed. These torques are not recommended for tubes 12.7 mm (0.5 in) OD and thicker with wall thickness of 0.889 mm (0.035 in) or less. The torque is specified for 0.889 mm (0.035 in) wall tubes on each application individually. O Ring Face Seal Fittings (Face Seal End) Thread Size LB FT Min 10 18 32 46 65 65 92 125 150 Nm Min 14 24 43 60 90 90 125 170 200 Size Tubing OD Inches 1/4 3/8 1/2 5/8 3/4 7/8 1 1 1/4 1 1/2 mm 6.4 9.5 12.7 15.9 19.1 22.2 25.4 31.8 38.1 Max 12 20 35 50 70 70 100 140 165 Max 16 27 47 68 95 95 135 190 225 2 6 8 10 12 14 16 20 24 9/16 20 11/16 16 13/16 16 1 14 1 3/16 12 1 3/16 12 1 7/16 12 1 11/16 12 2 12 Above torque figures are recommended for plain, cadmium or zinc plated fittings, dry or wet installations and swivel nuts either swagged or brazed. These torques are not recommended for tubes 12.7 mm (0.5 in) OD and thicker with wall thickness of 0.889 mm (0.035 in) or less. The torque is specified for 0.889 mm (0.035 in) wall tubes on each application individually. 87644966 5 2/26/2007 3
INTRODUCTION Torque Fasteners 1200 Mounted Stacker, 1200 Mounted Rigid, 1200 Trailing Rigid, 1200 Pivot Transport SAE FASTENER TORQUE Use these torques, unless special torques are specified. Values are for UNC and UNF thread fasteners, plated or unplated, as received from supplier. Fasteners can be dry or lubricated with normal engine oil. Values do not apply if graphite, molydisulphide or other extreme pressure lubricant is used. SAE Grade No. 2 5 Bolt Head Identification (See Note below.) 8 (See Note below.) 1 2 3 rh04h171 rh04h175 rh04h176 LB FT Min. 5 10 20 30 45 65 95 150 160 250 Nm Min. 7 14 27 41 61 88 129 203 217 339 LB FT Min. 9 17 35 54 80 110 150 270 400 580 800 1120 1460 1940 Nm Min. 12 23 48 73 109 149 203 366 542 787 1085 1519 1980 2631 LB FT Min. 12 24 45 70 110 160 220 380 600 900 1280 1820 2380 3160 Nm Min. 16 33 61 95 149 217 298 515 814 1220 1736 2468 3227 4285 Bolt Size Max. 6 12 23 35 52 75 105 185 200 300 Max. 8 16 31 47 70 102 142 251 271 406 Max. 11 20.5 42 64 96 132 180 324 480 696 880 1240 1680 2200 Max. 15 28 57 87 130 179 244 439 651 944 1193 1681 2278 2983 Max. 15 29 54 84 132 192 264 456 720 1080 1440 2000 2720 3560 Max. 20 39 73 114 179 260 358 618 976 1464 1953 2712 3688 4827 1/4 5/16 3/8 7/16 1/2 9/16 5/8 3/4 7/8 1 1 1/8 1 1/4 1 3/8 1 1/2 NOTE: Bolt head identification marks as per grade. Manufacturing marks will vary. NOTE: Thick nuts must be used with Grade 8 bolts. METRIC (ISO) FASTENER TORQUE Use these torques, unless special torques are specified. Values are for coarse thread fasteners, plated or unplated, as received from supplier. Fasteners can be dry or lubricated with normal engine oil. Values do not apply if graphite, molydisulphide or other extreme pressure lubricant is used. ISO Class No. 8.8 10.9 Bolt Head Identification (See Note below.) 12.9 4 5 6 rh04h178 rh04h179 rh04h180 Nm Min. LB FT Min. Nm Min. LB FT Min. Nm Min. LB FT Min. Bolt Size Max. Max. Max. Max. Max. Max. 87644966 5 2/26/2007 4
INTRODUCTION 5 11 17.5 43 87 150 245 380 730 1275 2400 4200 M4 M5 M6 M8 M10 M12 *M14 M16 M20 M24 M30 M36 3 6.5 10.5 26 52 90 144 217 434 675 1250 2175 4 8 12 31 61 107 172 271 515 815 1500 2600 2 5 8 19 38 66 106 160 320 500 920 1600 3 6 9 23 45 79 127 200 380 600 1100 1950 4 9.5 15 37 73 125 200 310 610 1050 2000 3500 3 7 11 27 54 93 149 230 450 780 1470 2580 4 8 13 32 64 112 179 280 540 940 1770 3090 Because of the low ductility of these fasteners, the torque range is to be determined individually for each application. As a general rule, the torque ranges specified for Grade 10.9 fasteners can be used satisfactorily on 12.9 fasteners. NOTE: Bolt head identification marks as per grade. Manufacturing marks will vary. 87644966 5 2/26/2007 5
INTRODUCTION Basic instructions Electrical testing 1200 Mounted Stacker, 1200 Mounted Rigid, 1200 Trailing Rigid, 1200 Pivot Transport Connector inspection During troubleshooting, always inspect the condition of the pins and cavities on the mating male and female connectors: Check for moisture in the connectors. Check for corrosion on the pins and in the cavities. Check for bent, broken or recessed pins. Moisture saturated connector Poor system performance can be caused by moisture in a connector however, moisture within a connector cannot be seen. If moisture is suspected, use contact cleaner or a heat gun at a low setting to dry the connector. Inspect and, if required, replace the connector cover to remove the source of the moisture. NOTE: Do not use compressed shop air to dry the con nectors. Shop air is often moisture saturated due to con densation. 1 RCIL06PTR107BAA 87644966 5 2/26/2007 6
INTRODUCTION Corroded pins or cavities Inspect the pins and cavities for corrosion which can cause a weak electrical connection between the mating connectors. If corrosion is present, replace the affected pins and cavities. 2 RCIL06PTR105BAA Bent pin Inspect the pins on the male connector. If a pin is bent and will not properly mate with its cavity in the female connector, replace the pin. 3 RCIL06PTR103BAA 87644966 5 2/26/2007 7
INTRODUCTION Touching pins Inspect the pins on the male connector. If a pin is bent to the point where it is shorted to another pin within the connector, replace the pin. 4 RCIL06PTR104BAA Recessed pin Inspect the male connector for recessed pins, where the pin is pushed back into the connector body, providing min imal contact when the two connectors are joined. If a pin is recessed, push the pin into the connector body from the back of the connector. Join and male and female connec tors and reinspect the pin. If the pin is recessed again, replace the male connector. 5 RCIL06PTR106BAA 87644966 5 2/26/2007 8
INTRODUCTION Broken pin Inspect the male connector for broken pins, where the pin remains with its female cavity, providing minimal contact when the two connectors are joined. 6 RCIL06PTR108BAA Measuring voltage 7 RCIL06PTR019CAA 1. Select the DC voltage function on the multimeter. 2. Turn system power ON. 3. Touch the positive (+) lead of the multimeter to the pin or cavity that is being tested. Touch the negative ( ) lead to a reliable source of tractor battery ground. 4. Read the displayed measurement. 87644966 5 2/26/2007 9
INTRODUCTION Measuring resistance 8 RCIL06PTR018CAA To accurately measure small resistances, the internal resistance of the multimeter must be subtracted from the measured resistance. To find the internal resistance of your multimeter: Turn the multimeter ON. Choose the lowest ohm scale on your multimeter. Touch the test leads together to display the internal resistance of the meter. Substract this value from any measured resistance when testing, or use the ZERO function on the multimeter to automatically substract the internal resistance of the meter. Turn system power OFF. 1. Disconnect both ends of the circuit or component to be tested. 2. Touch one lead to one end of the circuit or component. NOTE: Some components e.g., relays, solenoids are equipped with diodes which require that the positive (+) test lead and the negative ( ) test lead are used at specific connecting points. Always follow the instructions from the troubleshooting procedure when testing these components. 3. Touch the other lead to the other end of the circuit or component. 4. Read the displayed measurement. 87644966 5 2/26/2007 10
INTRODUCTION Measuring continuity (resistance) 9 RCIL06PTR021CAA 1. Select the continuity setting on the multimeter. 2. Turn system power OFF. 3. Disconnect both ends of the circuit or the component to be tested. 4. Touch one test lead to one end of the circuit or component pin, cavity or wire terminal. 5. Touch the other test lead to the other end of the circuit or component pin, cavity or wire terminal. 6. Read the displayed measurement. NOTE: If the multimeter continuity beeper is turned on, the multimeter beeps if resistance is less than 25 125 ohms, depending on your multimeter. If there is an open circuit, the multimeter does not beep. See the user manual for your multimeter to determine its ohm setting for a continuity beep. 87644966 5 2/26/2007 11
INTRODUCTION Short circuit to ground 10 RCIL06PTR021CAA Short circuit to ground occurs when any part of a circuit is in contact with a ground source when it is not intended. Where the test leads are applied depends on the component or circuit tested: When testing a sensor, for example, disconnect the sensor from its connector. When testing a controller harness, disconnect the harness at the controller connector and the malfunctioning component at its connector on the harness. When testing a harness, disconnect the harness connectors at its source and its terminal. 1. Turn system power OFF. 2. Disconnect the connectors for the circuits to be tested. 3. Identify the pins or cavities that need to be tested. 4. Select the resistance setting on the multimeter. 5. Touch one of the test leads from the multimeter to the pin or cavity on one end of the circuit. 6. Touch the other test lead to the pin or cavity on the other end of the circuit. 7. Read the value on the multimeter. 8. The resistance reading should be greater than 100 ohms to indicate an open circuit. If the circuit is not open, the wire is shorted to ground. NOTE: The 100 ohms value is a representative value used throughout the diagnostic procedures in this manual. The expected resistance reading for an open circuit is infinite resistance or open line on the multimeter. The actual reading on the multimeter depends on the wire gauge 0.8, 1.2, 2.0, 3.0 and the distance between the test points. 9. Locate and repair the source of the short. Or replace the shorted wire or component. 87644966 5 2/26/2007 12
INTRODUCTION Short circuit to B+ Unwanted power 11 RCIL06PTR021CAA Short circuit to B+ or unwanted power is a condition where an electrical path exists between two circuits when it is not intended to exist. a power circuit and another power/control circuit. A circuit which should be disabled by controller logic but is detected as powered is considered shorted to B+ or having unwanted power. A diagnostic procedure may use different names for B+ power MIU B+, LB+, HB+ to distinguish different power circuits. But the condition is the same: a path exists between a power circuit and another power/control circuit which is not intended. Very often, diagnostic procedures in this manual test from the power source MIU B+, LB+, HB+ to locate the problem circuit. You will be directed to touch the test leads to specific pins or cavities on the connectors for these various power sources. Follow these instructions exactly to eliminate each power circuit one by one as the source of the unwanted power. 1. Turn system power OFF. 2. Disconnect the connectors for the circuits to be tested. 3. Identify the pins or cavities that need to be tested. 4. Select the resistance setting on the multimeter. 5. Touch one of the test leads from the multimeter to the pin or cavity on one end of the circuit. 6. Touch the other test lead to the pin or cavity on the other end of the circuit. 7. Read the value on the multimeter. 8. If the resistance reading is less than 10 ohms, the circuit is shorted to this power source. NOTE: The 10 ohms value is a representative value used throughout the diagnostic procedures in this manual. The expected resistance reading for an non shorted circuit is infinite resistance or open line on the multimeter. The actual reading on the multimeter depends on the wire gauge 0.8, 1.2, 2.0, 3.0 and the distance between the test points. For example, the resistance reading on the multimeter could be 30 ohms between test points that are 13.7 m (45 ft) apart and still indicate a short circuit or the resistance reading could be 30 ohms between two test points that are 3 m (9.8 ft) on 3.0 gauge wire and still indicate a short circuit. 9. Locate and repair the source of the short. Or replace the shorted wire or component. NOTE: Check for touching pins, pinch points or exposed wires to locate the source in the harness. 87644966 5 2/26/2007 13
INTRODUCTION Short circuit pin to pin 12 RCIL06PTR018CAA Short circuit from pin to pin within an existing harness is a condition where an electrical path exists between two circuits where it is not intended to exist. 1. Turn system power OFF. 2. Disconnect the connector for the harness or component to be tested. 3. Identify the pins to be tested 4. Select the resistance setting on the multimeter. 5. Touch one of the test leads from the multimeter to the first pin or cavity on the connector. 6. Touch the other test lead to the other pins or cavities on the connector one by one, while watching the reading on the multimeter. 7. If the resistance reading is less than 10 ohms, the circuit is shorted between the pins. If the circuit is shorted, the pins are unintentionally connected. NOTE: The 10 ohms value is a representative value used throughout the diagnostic procedures in this manual. The expected resistance reading for an non shorted circuit is infinite resistance or open line on the multimeter. The actual reading on the multimeter depends on the wire gauge 0.8, 1.2, 2.0, 3.0 and the distance between the test points. For example, the resistance reading on the multimeter could be 30 ohms between test points that are 13.7 m (45 ft) apart and still indicate a short circuit or the resistance reading could be 30 ohms between two test points that are 3 m (9.8 ft) on 3.0 gauge wire and still indicate a short circuit. 8. Locate and repair the source of the short. Or replace the shorted wire or component. 87644966 5 2/26/2007 14
INTRODUCTION Testing voltage 13 RCIL06PTR020CAA A voltage test measures the difference in voltage potential between two points. 1. Disconnect the connector for the component or harness to be tested. NOTE: Follow the instructions in the troubleshooting procedure. Some voltages can only be tested when the component or harness are connected. 2. Turn system power ON. 3. Identify the pins or cavities to be tested. 4. Select the DC voltage setting on the multimeter. 5. Touch the positive (+) test lead to the pin or cavity. 6. Touch the negative ( ) test lead to a reliable source of tractor battery ground. 7. Read the value on the multimeter. Compare the reading to the desired value or range provided in the trou bleshooting procedure. 8. If the value is incorrect, follow the instructions from the procedure to repair or replace the circuit. 87644966 5 2/26/2007 15
MORE MANUALS: https://www.ebooklibonline.com/ Suggest: If the above button click is invalid. Please download this document first, and then click the above link to download the complete manual. Thank you so much for reading
INTRODUCTION Continuity test Open circuit 14 RCIL06PTR017CAA Continuity is an electrical connection between two pins or cavities on a circuit that is less than a certain resis tance value. For harness wires, the specification is less than 10 ohms. 1. Turn system power OFF. 2. Disconnect the harness connectors to be tested. 3. Select the resistance setting on the multimeter. 4. Identify the pins or cavities to be tested. 5. Touch one of the test leads to pin or cavity on one end of the circuit. 6. Touch the other test lead to the pin or cavity on the other end of the circuit. 7. Read the value on the multimeter. 8. The resistance reading for circuit continuity should be less than 10 ohms. If the reading is greater than 10 ohms, the circuit is open and must be repaired or replaced. Many multimeters display OL for open line when extremely high (infinite) resistance is detected, indicating an open circuit. NOTE: The 10 ohms value is a representative value used throughout the diagnostic procedures in this manual. The expected resistance reading for an non shorted circuit is infinite resistance or open line on the multimeter. The actual reading on the multimeter depends on the wire gauge 0.8, 1.2, 2.0, 3.0 and the distance between the test points. For example, the resistance reading on the multimeter could be 30 ohms between test points that are 13.7 m (45 ft) apart and still indicate a short circuit or the resistance reading could be 30 ohms between two test points that are 3 m (9.8 ft) on 3.0 gauge wire and still indicate a short circuit. 87644966 5 2/26/2007 16
https://www.ebooklibonline.com Hello dear friend! Thank you very much for reading. Enter the link into your browser. The full manual is available for immediate download. https://www.ebooklibonline.com