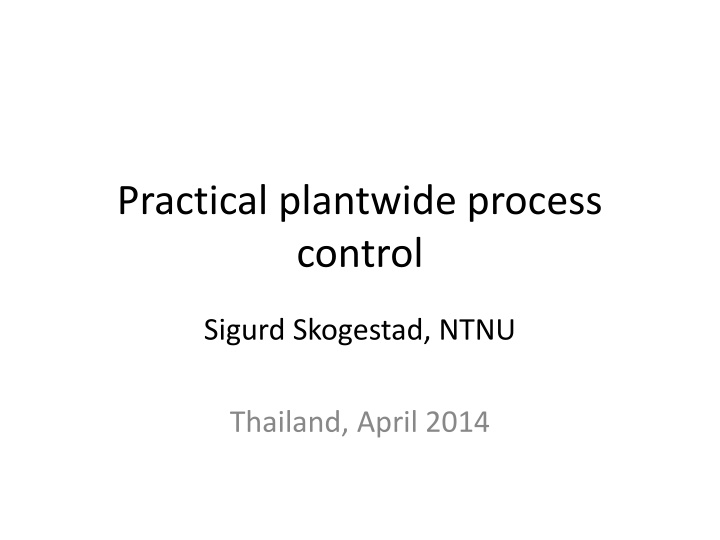
Practical Plantwide Process Control Course Overview
Learn how to improve plant stability and economics through a systematic approach without heavy mathematics. Discover controlling strategies, loop structuring, and PID controller tuning methods for optimal plant performance.
Download Presentation

Please find below an Image/Link to download the presentation.
The content on the website is provided AS IS for your information and personal use only. It may not be sold, licensed, or shared on other websites without obtaining consent from the author. If you encounter any issues during the download, it is possible that the publisher has removed the file from their server.
You are allowed to download the files provided on this website for personal or commercial use, subject to the condition that they are used lawfully. All files are the property of their respective owners.
The content on the website is provided AS IS for your information and personal use only. It may not be sold, licensed, or shared on other websites without obtaining consent from the author.
E N D
Presentation Transcript
Practical plantwide process control Sigurd Skogestad, NTNU Thailand, April 2014
Course description This practically oriented course shows how to control your plant for improved stability and economics. The approach is systematic and based on the latest methods, but uses a limited amount of mathematics. You will learn what to control, how to structure the loops and how to tune your PID controllers.
Course Summary 1. Find active constraints + self-optimizing variables (CV1). (Economic optimal operation) Locate throughput manipulator (TPM) Gas pedal Select stabilizing CV2 + tune regulatory loops SIMC PID rules Design supervisory layer (control CV1) Multi-loop (PID) ++ MPC 2. 3. 4. Difficulties: 1. 2. Optimization! May need to guess active constraints (CV1) Handling of moving active constraints Want to avoid reconfiguration of loops
Part 1 (4h): Plantwide control Introduction to plantwide control (what should we really control?) Part 1.1 Introduction. Objective: Put controllers on flow sheet (make P&ID) Two main objectives for control: Longer-term economics (CV1) and shorter-term stability (CV2) Regulatory (basic) and supervisory (advanced) control layer Part 1.2 Optimal operation (economics) Active constraints Selection of economic controlled variables (CV1). Self-optimizing variables. Part 1.3 -Inventory (level) control structure Location of throughput manipulator Consistency and radiating rule Part 1.4 Structure of regulatory control layer (PID) Selection of controlled variables (CV2) and pairing with manipulated variables (MV2) Main rule: Control drifting variables and "pair close" Summary: Sigurd s rules for plantwide control
Part 2 (4h): PID tuning Part 2 (4h). PID controller tuning: It pays off to be systematic! Derivation SIMC PID tuning rules Controller gain, Integral time, derivative time Obtaining first-order plus delay models Open-loop step response From detailed model (half rule) From closed-loop setpoint response Special topics Integrating processes (level control) Other special processes and examples When do we need derivative action? Near-optimality of SIMC PID tuning rules Non PID-control: Is there an advantage in using Smith Predictor? (No) Examples
Part 3 (1h) + Part 4 (3h): case studies Part 3 (1h). Advanced control layer Design based on simple elements: Ratio control Cascade control Selectors Input resetting (valve position control) Split range control Decouplers (including phsically based) When should these elements be used? When use MPC instead? Part 4 (3h). Case studies Example: Distillation column control Example: Plantwide control of complete plant Recycle processes: How to avoid snowballing