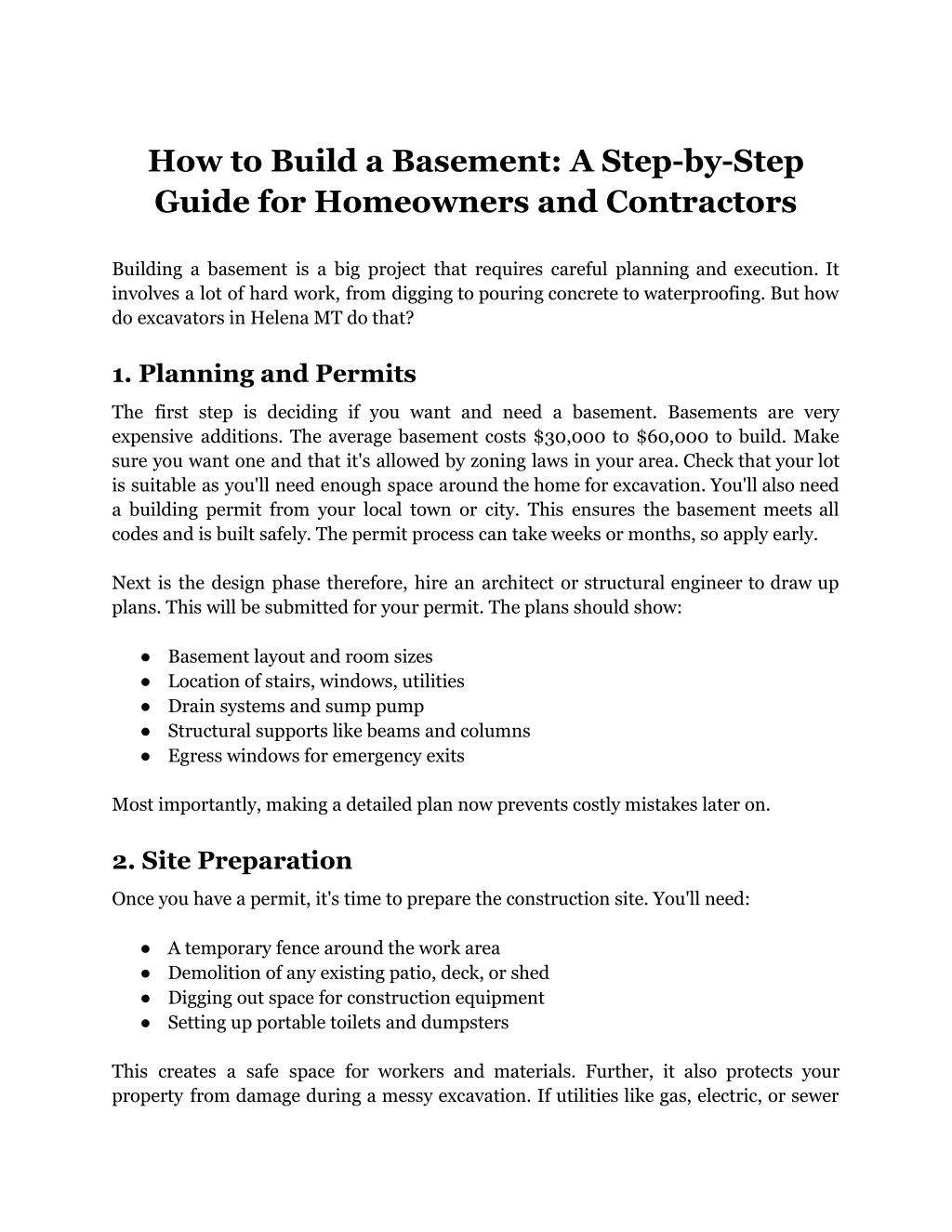
How to Build a Basement_ A Step-by-Step Guide for Homeowners and Contractors
To meet code and safety requirements, basement living spaces need egress windows andna permanent stairway. Helena excavating contractor built the staircase framing andninstalled the steps last. This provides easy basement access for all the preceding work.nRailings get installed too. For windows, acrylic blocks or pre-made window wells withnladder steps create safe egress exits. The wells get backfilled around the outside oncencomplete.
Download Presentation

Please find below an Image/Link to download the presentation.
The content on the website is provided AS IS for your information and personal use only. It may not be sold, licensed, or shared on other websites without obtaining consent from the author. Download presentation by click this link. If you encounter any issues during the download, it is possible that the publisher has removed the file from their server.
E N D
Presentation Transcript
How to Build a Basement: A Step-by-Step Guide for Homeowners and Contractors Building a basement is a big project that requires careful planning and execution. It involves a lot of hard work, from digging to pouring concrete to waterproofing. But how do excavators in Helena MT do that? 1. Planning and Permits The first step is deciding if you want and need a basement. Basements are very expensive additions. The average basement costs $30,000 to $60,000 to build. Make sure you want one and that it's allowed by zoning laws in your area. Check that your lot is suitable as you'll need enough space around the home for excavation. You'll also need a building permit from your local town or city. This ensures the basement meets all codes and is built safely. The permit process can take weeks or months, so apply early. Next is the design phase therefore, hire an architect or structural engineer to draw up plans. This will be submitted for your permit. The plans should show: Basement layout and room sizes Location of stairs, windows, utilities Drain systems and sump pump Structural supports like beams and columns Egress windows for emergency exits Most importantly, making a detailed plan now prevents costly mistakes later on. 2. Site Preparation Once you have a permit, it's time to prepare the construction site. You'll need: A temporary fence around the work area Demolition of any existing patio, deck, or shed Digging out space for construction equipment Setting up portable toilets and dumpsters This creates a safe space for workers and materials. Further, it also protects your property from damage during a messy excavation. If utilities like gas, electric, or sewer
lines run near the basement area, you must have them properly marked and secured before digging. Read More Articles: Looking for a Good London SEO Agency? 3. Excavation Now the real work begins for you as you have to dig out the giant hole! The hole needs to be: At least 8 feet deep for standard ceiling height 2-3 feet wider than basement walls on all sides Dug at a slope to prevent cave-ins An experienced operator carefully removes soil in sections. However, supplies like wooden planks may be used to brace the hole and prevent collapsing. All that dirt has to go somewhere! Many hire truck haulers to constantly remove loads of soil from the property. This is one of the messiest, noisiest parts of the project. Once the full hole is dug out, the bottom is leveled off and compacted to provide a solid base. 4. Foundation Footings With the hole ready, it's time to pour the foundation footings. These are wide concrete pads that support the basement walls. Footings must: Extend below the frost line to prevent shifting Be reinforced with steel rebar Have proper drainage for water runoff Forms are built out of wood or polystyrene foam. Concrete trucks pour the wet concrete, which is then smoothed out. After curing for days, the solid footings are ready. 5. Foundation Walls On top of the footings, workers build formwork for the basement walls. These are also reinforced with steel rebar. The concrete walls are poured into sections using special trucks with long chutes. Proper consolidation ensures no air pockets form in the concrete. Once set, the foundation walls provide the solid structural base for the basement. Removing the formwork reveals the bare concrete inner walls.
6. Waterproofing Since basements are holes in the ground, waterproofing is important. Bare concrete walls eventually develop cracks that allow moisture in. There are a few different waterproofing options: Membrane systems like plastic or rubber sheets Liquid-applied sealants that cure into a barrier Exterior plastic drain tiles and gravel coverings 7. Windows and Vents For a basement to be livable, you'll need windows and ventilation. Sectional window wells are dug out and lined to allow windows below ground level. These provide natural light and emergency exits. Vent wells also get excavated. These allow mechanical ventilation via exhaust fans or ductwork. Good air circulation prevents musty odors. The windows and vent covers get framed with wood or metal bucks at this stage before framing the interior walls. 8. Floor Slab The last major concrete pour is the basement floor slab. Polyethylene plastic sheets act as a moisture barrier laid over compacted gravel. Concrete gets poured over that, often containing radiant heating pipes. The slab is reinforced with a grid of steel rebar or mesh for extra strength. Further, control joints get cut to allow for expansion and prevent cracking. 9. Framing and Utilities Bottom wall plates get anchored into the concrete using bolts every few feet. Then vertical studs get nailed into the bottom and top plates. Door openings get framed, and horizontal blocking provides attachment for drywall later. Any utility pipes or ductwork also get framed around at this stage. Once the framing is done, plumbers and electricians start running supply lines for the basement systems. This includes: Drain pipes for sinks, showers, and toilets Supply pipes for hot and cold water Vent stacks for plumbing Electrical boxes and wiring for lights and outlets HVAC ducts or units for heating/cooling
10. Insulation The insulation prevents drafts and blocks moisture. Basements use thicker insulation than above-grade walls. Insulating the ceiling/floor above is wise too. The insulation gets installed after utilities but before drywall. Any vapor barriers and moisture protection layers go up now as well. There are a few different options: Rigid foam boards against concrete walls Fiberglass batt insulation in stud cavities Sprayed foam that fills all nooks and gaps 11. Drywall and Finishes In this step sheets of drywall get screwed to the framed walls and ceilings. The joints get taped, mudded, sanded, and primed for a smooth finish. Many homeowners like leaving ceilings unfinished and just painting drywall on walls. This maximizes ceiling height. False drop ceilings are another option. For flooring, many choose easy-to-install laminate or snap-together plank floors over the slab. Ceramic tile is also very popular for basements. You'll also add wall trim, paint, bathroom fixtures, railings, lights, switches, outlets, and other finishing touches at this stage too. This is where a basement starts feeling like a home! Read More Articles: How to Sell Your Business? 12. Egress Windows and Stairs To meet code and safety requirements, basement living spaces need egress windows and a permanent stairway. Helena excavating contractor built the staircase framing and installed the steps last. This provides easy basement access for all the preceding work. Railings get installed too. For windows, acrylic blocks or pre-made window wells with ladder steps create safe egress exits. The wells get backfilled around the outside once complete. Final Inspection After all the work is done, An inspector will thoroughly check every aspect: Structural framing and concrete integrity Proper insulation and moisture protection Electrical, plumbing, and HVAC installations Egress windows, stairs, and safety features
Wall, ceiling, and floor finishes They ensure your new basement meets all local codes and building standards. Any issues must be fixed before final approval. Conclusion Once you go through all of the above steps, your basement is officially complete and ready for use! Relax and be happy that you earned it after all that work. Trust Schaefer Excavating & Construction to deliver quality workmanship, attention to detail, and reliable Helena excavation services that stand the test of time. From excavation projects large and small, our team is here to turn your vision into reality. Site Homeowners and Contractors Article: How to Build a Basement: A Step-by-Step Guide for