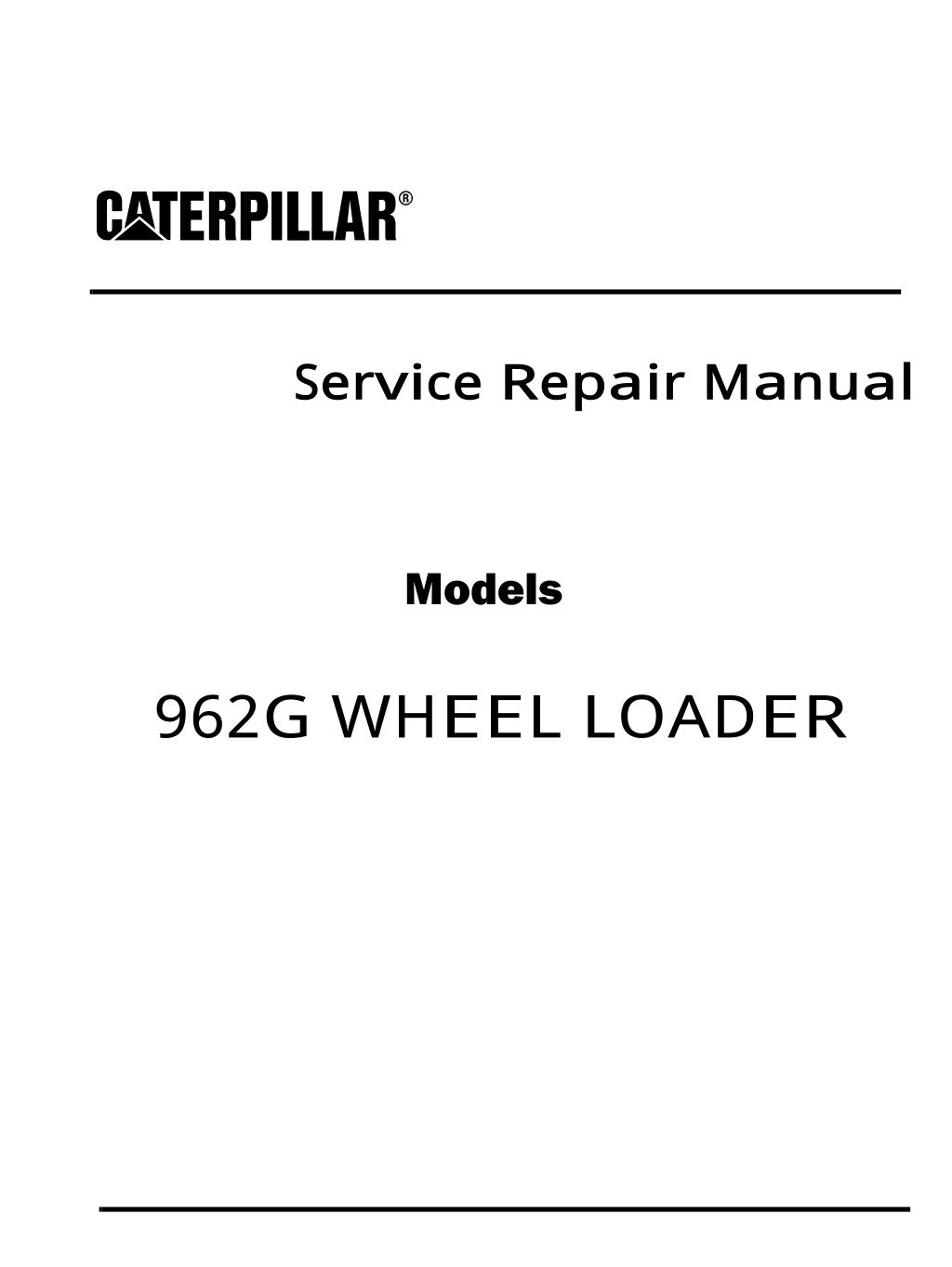
Caterpillar Cat 962G Wheel Loader (Prefix 3BS) Service Repair Manual Instant Download
Please open the website below to get the complete manualnn// n
Download Presentation

Please find below an Image/Link to download the presentation.
The content on the website is provided AS IS for your information and personal use only. It may not be sold, licensed, or shared on other websites without obtaining consent from the author. Download presentation by click this link. If you encounter any issues during the download, it is possible that the publisher has removed the file from their server.
E N D
Presentation Transcript
Service Repair Manual Models 962G WHEEL LOADER
962G Wheel Loader 3BS00001-UP (MACHINE) POWERED BY 3126 Engine(SEBP... 1/8 Shutdown SIS Previous Screen Product: WHEEL LOADER Model: 962G WHEEL LOADER 3BS Configuration: 962G Wheel Loader 3BS00001-UP (MACHINE) POWERED BY 3126 Engine Disassembly and Assembly 950G and 962G Wheel Loaders and IT62G Integrated Toolcarrier Power Train Media Number -SENR1381-10 Publication Date -01/10/2007 Date Updated -25/10/2007 i07093515 Axle Housing - Disassemble SMCS - 3260-015 Disassembly Procedure Table 1 Required Tools Tool Part Number Part Description Qty A 138-7573 Link Bracket 2 1P-2420 Transmission Repair Stand 1 B FT-0996 Positioning Group 4 FT-0957 Adapter Group 4 C 1P-1863 Pliers 1 D 4C-8358 Lifting Eyes 3 6V-7820 Torque Multiplier 1 E 120-9877 Spanner Wrench As(1) 1 Spanner Wrench As(2) 1U-9478 1 150-1782 Crossblock 1 5F-7366 Forcing Screw 1 F 3H-0466 Nut 1 3H-0468 Plate 2 9U-7692 Threaded Rod 2 (1)For use with M105 bearing nut. https://127.0.0.1/sisweb/sisweb/techdoc/techdoc_print_page.jsp?returnurl=/sis... 2020/3/30
962G Wheel Loader 3BS00001-UP (MACHINE) POWERED BY 3126 Engine(SEBP... 2/8 (2)For use with M95 bearing nut. Start By: a. Remove the fixed axle. Refer to Disassembly and Assembly, "Fixed Axle (Front) - Remove and Install". b. Remove the oscillating axle. Refer to Disassembly and Assembly, "Oscillating Axle (Rear) - Remove". Note: The axle housing assemblies that are used in the front fixed axle and in the rear oscillating axle are similar. Therefore, both axle housing assemblies can be removed in the same manner. Illustration 1 g00301040 Typical Example 1. Install the axle housing in a vertical position on Tooling (B). Note: Carefully remove the axle housing assembly. Part of the wear gauge pin will remain in the axle housing assembly. The pin will remain in the axle housing assembly. The spring and the piston will remain in the differential housing. 2. Fasten Tooling (A) and a hoist to the rim of the axle shaft, as shown. Remove bolts (1) that secure axle housing assembly (2) to the differential housing. Carefully remove the axle housing assembly. The weight of axle housing assembly (2) is 295 kg (650 lb). https://127.0.0.1/sisweb/sisweb/techdoc/techdoc_print_page.jsp?returnurl=/sis... 2020/3/30
https://www.ebooklibonline.com Hello dear friend! Thank you very much for reading. Enter the link into your browser. The full manual is available for immediate download. https://www.ebooklibonline.com
962G Wheel Loader 3BS00001-UP (MACHINE) POWERED BY 3126 Engine(SEBP... 3/8 Illustration 2 g00303123 3. Remove the bottom half of the axle housing from Tooling (B). Install axle housing assembly (2) on Tooling (B), as shown. Illustration 3 g00303124 Note: To remove retaining ring (3), planetary carrier assembly (5) must be disassembled. 4. Use Tooling (C) to remove retaining ring (3) from axle shaft (4). Illustration 4 g00303169 5. Install Tooling (D) and suitable lifting slings to planetary carrier assembly (5), as shown. 6. Use a hoist to remove the planetary carrier assembly from the axle housing assembly. The weight of the planetary carrier assembly is 80 kg (175 lb). https://127.0.0.1/sisweb/sisweb/techdoc/techdoc_print_page.jsp?returnurl=/sis... 2020/3/30
962G Wheel Loader 3BS00001-UP (MACHINE) POWERED BY 3126 Engine(SEBP... 4/8 Illustration 5 g00303170 Illustration 6 g00303171 7. Use the following steps to disassemble planetary carrier assembly (5): a. Use a hammer and a punch to push spring pin (7) all the way into shaft (6). b. Remove shaft (6), thrust washers , and (8) planetary gear (9) from the carrier. c. Remove bearing (10) from planetary gear (9). d. Use a hammer and a punch to remove spring pin (7) from shaft (6). e. Repeat Steps 7.a through 7.d for the remaining two planetary gears. f. Remove retaining ring (3) from the carrier. https://127.0.0.1/sisweb/sisweb/techdoc/techdoc_print_page.jsp?returnurl=/sis... 2020/3/30
962G Wheel Loader 3BS00001-UP (MACHINE) POWERED BY 3126 Engine(SEBP... 5/8 Illustration 7 g00303172 Illustration 8 g00303173 8. Install two bolts (11) of a suitable size in the rim of the axle flange. This will prevent the axle shaft from turning when bearing nut (12) is removed. Illustration 9 g00303174 9. Use Tooling (E) to remove bearing nut (12) from the axle shaft. https://127.0.0.1/sisweb/sisweb/techdoc/techdoc_print_page.jsp?returnurl=/sis... 2020/3/30
962G Wheel Loader 3BS00001-UP (MACHINE) POWERED BY 3126 Engine(SEBP... 6/8 Illustration 10 g00303176 10. Install Tooling (A) and suitable lifting slings to the axle housing, as shown. Put slight lifting tension on the axle housing. Illustration 11 g00303177 Note: The bearing cone which is located under bearing nut (12) will be removed at the same time as the axle housing. 11. Fasten Tooling (F) to the axle housing, as shown. Use the center stud to push the axle shaft and the bearing cone from the axle housing. Make sure that upward pressure is constantly applied. 12. Use the hoist to remove the axle housing and the inner bearing cone from the axle shaft. The weight of the axle housing is 105 kg (231 lb). 13. Remove the inner bearing cone from the axle housing. https://127.0.0.1/sisweb/sisweb/techdoc/techdoc_print_page.jsp?returnurl=/sis... 2020/3/30
962G Wheel Loader 3BS00001-UP (MACHINE) POWERED BY 3126 Engine(SEBP... 7/8 Illustration 12 g00303179 14. Remove inner bearing cup (13) from the axle housing. Note: Planetary ring gear (15) will be destroyed during removal. 15. Remove ring gear (15) from the axle housing. Use a torch to cut the ring gear in two places that are directly across from each other. Cut the ring gear at the position of the locating dowels. For an alternate method, make three welds that are equally spaced around the circumference of the ring gear. This will cause the ring gear to shrink. 16. Remove dowels (14). Illustration 13 g00303180 17. Remove Duo-Cone seal (16) and bearing cup (17) from the opposite end of the axle housing. https://127.0.0.1/sisweb/sisweb/techdoc/techdoc_print_page.jsp?returnurl=/sis... 2020/3/30
962G Wheel Loader 3BS00001-UP (MACHINE) POWERED BY 3126 Engine(SEBP... 8/8 Illustration 14 g00303181 18. Remove Duo-Cone seal (19) and bearing cone (18) from the axle shaft. Copyright 1993 - 2020 Caterpillar Inc. Mon Mar 30 10:39:14 UTC+0800 2020 All Rights Reserved. Private Network For SIS Licensees. https://127.0.0.1/sisweb/sisweb/techdoc/techdoc_print_page.jsp?returnurl=/sis... 2020/3/30
962G Wheel Loader 3BS00001-UP (MACHINE) POWERED BY 3126 Engine(SEBP... 1/7 Shutdown SIS Previous Screen Product: WHEEL LOADER Model: 962G WHEEL LOADER 3BS Configuration: 962G Wheel Loader 3BS00001-UP (MACHINE) POWERED BY 3126 Engine Disassembly and Assembly 950G and 962G Wheel Loaders and IT62G Integrated Toolcarrier Power Train Media Number -SENR1381-10 Publication Date -01/10/2007 Date Updated -25/10/2007 i01076945 Duo-Cone Conventional Seals - Install SMCS - 7561-012 Installation Procedure Note: This procedure is only for Duo-Cone conventional seals. This procedure does not pertain to Duo-Cone floating seals. It is extremely important to follow the correct procedure for installing Duo-Cone seals. Many seal failures are the direct result of mistakes during installation of the seal components. Illustration 1 g00296728 (1) Rubber toric ring. (2) Seal ring. (3) Housing retaining lip. (4) Housing ramp. (5) Seal ring housing. https://127.0.0.1/sisweb/sisweb/techdoc/techdoc_print_page.jsp?returnurl=/sis... 2020/3/30
962G Wheel Loader 3BS00001-UP (MACHINE) POWERED BY 3126 Engine(SEBP... 2/7 Illustration 2 g00296926 (6) Seal ring face. (7) Seal ring ramp. (8) Installation tool. (9) Seal ring retaining lip. Use caution when you are using isopropyl alcohol. Avoid prolonged skin contact with isopropyl alcohol. Vapors may be harmful if inhaled. Use only in a well ventilated area. Do not smoke while using isopropyl alcohol. Isopropyl alcohol is flammable. Do not use near an open flame or near welding operations. Keep isopropyl alcohol away from heated surfaces exceeding 482 C (900 F). 1. Remove any oily film, dust or other foreign matter from all of the seal components. Use isopropyl alcohol and a clean cloth to wipe the components. (Paper towels may also be used.) Note: Do not allow oil to contact rubber toric rings (1) or seal ring ramps (7) before both seal rings (2) are assembled in Step 10. https://127.0.0.1/sisweb/sisweb/techdoc/techdoc_print_page.jsp?returnurl=/sis... 2020/3/30
962G Wheel Loader 3BS00001-UP (MACHINE) POWERED BY 3126 Engine(SEBP... 3/7 Illustration 3 g00296933 Illustration 4 g00296971 2. Put rubber toric ring (1) on seal ring (2). Make sure that the toric ring is at the bottom of seal ring ramp (7) and against seal ring retaining lip (9). Note: Make sure that rubber toric ring (1) is straight on seal ring (2). There must not be a twist in the toric ring. Be careful when you are working on the rubber toric ring. Nicks, cuts and scratches can cause leaks. https://127.0.0.1/sisweb/sisweb/techdoc/techdoc_print_page.jsp?returnurl=/sis... 2020/3/30
962G Wheel Loader 3BS00001-UP (MACHINE) POWERED BY 3126 Engine(SEBP... 4/7 Illustration 5 g00296975 3. Put installation tool (8) on seal ring (2) with rubber toric ring (1). Lower the rings into a container of isopropyl alcohol until all surfaces of rubber toric ring (1) are wet. Note: Do not use Stanisol or any other liquid that may leave an oily film. Illustration 6 g00297112 4. While all surfaces of rubber toric ring (1) are still wet, use installation tool (8) to position seal ring (2) and the toric ring squarely against seal ring housing (5), as shown. https://127.0.0.1/sisweb/sisweb/techdoc/techdoc_print_page.jsp?returnurl=/sis... 2020/3/30
962G Wheel Loader 3BS00001-UP (MACHINE) POWERED BY 3126 Engine(SEBP... 5/7 Illustration 7 g00297146 5. Measure dimension (A) from seal ring face (6) to the top surface of seal ring housing (5). Check dimension (A) in at least four places (90 degree intervals). The measurements must not differ by more than 1 mm (.04 inch). Note: If small adjustments are necessary, do not push on seal ring (2). Use installation tool (8). 6. Rubber toric ring (1) can twist if the toric ring is not completely wet during installation. Burrs on housing retaining lip (3) or on seal ring housing (5) can also cause a twist. If a twist occurs or if the toric ring is misaligned, repeat Steps 3 through 5. 7. Before further installation, wait for at least two minutes so that the isopropyl alcohol can evaporate. This will prevent slippage on seal ring ramps (7) and on housing ramps (4). The toric ring must roll only on the seal ring ramps and on the housing ramps. https://127.0.0.1/sisweb/sisweb/techdoc/techdoc_print_page.jsp?returnurl=/sis... 2020/3/30
962G Wheel Loader 3BS00001-UP (MACHINE) POWERED BY 3126 Engine(SEBP... 6/7 Illustration 8 g00297155 8. Use a clean cloth or a paper towel to wipe off seal ring faces (6). Note: No particles of any kind can be left on the sealing surfaces. A small piece from a paper towel can cause a leak by keeping the sealing surfaces from contacting each other. Illustration 9 g00297156 9. Apply a thin film of clean oil on seal ring faces (6). Use an applicator, a disposable tissue or a clean finger to distribute the oil evenly. Be careful so that no oil contacts the toric rings. Illustration 10 g00297157 https://127.0.0.1/sisweb/sisweb/techdoc/techdoc_print_page.jsp?returnurl=/sis... 2020/3/30
962G Wheel Loader 3BS00001-UP (MACHINE) POWERED BY 3126 Engine(SEBP... 7/7 10. Make sure that both seal ring housings (5) are correctly aligned and concentric. Slowly move the seals toward each other. Note: Do not slam the seals together. High impact can damage the seal components and leakage will occur. 11. When the seals are in place, fasten all of the parts securely. Copyright 1993 - 2020 Caterpillar Inc. Mon Mar 30 10:40:14 UTC+0800 2020 All Rights Reserved. Private Network For SIS Licensees. https://127.0.0.1/sisweb/sisweb/techdoc/techdoc_print_page.jsp?returnurl=/sis... 2020/3/30
962G Wheel Loader 3BS00001-UP (MACHINE) POWERED BY 3126 Engine(SEBP... 1/10 Shutdown SIS Previous Screen Product: WHEEL LOADER Model: 962G WHEEL LOADER 3BS Configuration: 962G Wheel Loader 3BS00001-UP (MACHINE) POWERED BY 3126 Engine Disassembly and Assembly 950G and 962G Wheel Loaders and IT62G Integrated Toolcarrier Power Train Media Number -SENR1381-10 Publication Date -01/10/2007 Date Updated -25/10/2007 i07307652 Axle Housing - Assemble SMCS - 3260-016 Assembly Procedure Table 1 Required Tools Tool Part Number Part Description Qty A 138-7573 Link Bracket 2 1P-2420 Transmission Repair Stand 1 B FT-0996 Positioning Group 4 FT-0957 Adapter Group 4 C 1P-1863 Pliers 1 D 4C-8358 Lifting Eyes 3 6V-7820 Torque Multiplier 1 E 120-9877 Spanner Wrench As(1) 1 Spanner Wrench As(2) 1U-9478 1 F 1U-6439 Duo-Cone Seal Installer 1 G FT-2530 Bar (Rolling Torque) 1 H - Loctite 5127 - (1)For use with M105 bearing nut. (2)For use with M95 bearing nut. https://127.0.0.1/sisweb/sisweb/techdoc/techdoc_print_page.jsp?returnurl=/sis... 2020/3/30
962G Wheel Loader 3BS00001-UP (MACHINE) POWERED BY 3126 Engine(SEBP... 2/10 Note: The axle housing assemblies that are used in the fixed axle and in the oscillating axle are similar. Therefore, both axle assemblies can be assembled in the same manner. Illustration 1 g00311383 1. Use bolts of a suitable size to fasten the rim of the axle shaft to Tooling (B). 2. Heat bearing cone (17) to a maximum temperature of 135 C (275 F). 3. Install bearing cone (17) on the axle shaft, as shown. Make sure that the bearing cone is seated against the shoulder. Note: Allow the bearing cone and the axle to reach a uniform temperature. 4. Use a suitable driver or a press to reset the bearing cone. This will ensure that the bearing cone is seated properly. 5. Apply a thin coat of clean SAE 30 oil on bearing cone (17). Note: Make sure that the rubber seals and all surfaces that contact the seals are clean and dry. After installation of the seals, apply clean SAE 30 oil on the contact surfaces of the metal seals. 6. Use Tooling (F) to install the Duo-Cone seal in the axle assembly. Refer to Disassembly and Assembly, "Duo-Cone Conventional Seals - Install". Illustration 2 g00303180 https://127.0.0.1/sisweb/sisweb/techdoc/techdoc_print_page.jsp?returnurl=/sis... 2020/3/30
962G Wheel Loader 3BS00001-UP (MACHINE) POWERED BY 3126 Engine(SEBP... 3/10 7. Lower the temperature of bearing cup (16). Install bearing cup (16) in the end of the axle housing. Make sure that the bearing cup is seated with the mating surface. Note: Allow the bearing cone and the axle to reach a uniform temperature. 8. Use a suitable driver or a press to reset bearing cup (16). This will ensure that bearing cup (16) is seated properly. Note: Make sure that the rubber seals and all surfaces that contact the seals are clean and dry. After installation of the seals, apply clean SAE 30 oil on the contact surfaces of the metal seals. 9. Use Tooling (F) to install Duo-Cone seal (15) in the end of the axle housing. Refer to Disassembly and Assembly, "Duo-Cone Conventional Seals - Install". Illustration 3 g00303179 10. Lower the temperature of bearing cup (13). Install bearing cup (13) in the opposite end of the axle housing, as shown. Make sure that the bearing cup is seated on the mating surface. Note: Allow the bearing cone and the axle to reach a uniform temperature. 11. Use a suitable driver or a press to reset bearing cup (12). This will ensure that bearing cup (12) is seated properly. Note: The following steps are for the installation of the ring gear. Note: Dowels (14) are used to locate ring gear (15). 12. Locate the position of the ring gear in relation to the axle housing. Align the holes to install the dowels. Put alignment marks on the ring gear and on the axle housing to ensure correct installation. 13. Lower the temperature of ring gear (15) to 70 C ( 94 F). Install ring gear (15) in the axle housing. 14. Install dowels (14). Peen the axle housing near the dowels to retain the dowels. https://127.0.0.1/sisweb/sisweb/techdoc/techdoc_print_page.jsp?returnurl=/sis... 2020/3/30
962G Wheel Loader 3BS00001-UP (MACHINE) POWERED BY 3126 Engine(SEBP... 4/10 Illustration 4 g00303176 15. Install Tooling (A) on the axle housing, as shown. Attach a hoist and suitable lifting slings to Tooling (A). 16. Use the hoist to install the axle housing on the axle shaft. The weight of the axle housing is 105 kg (231 lb). Illustration 5 g00311444 17. Heat bearing cone (20) to a maximum temperature of 135 C (275 F). 18. Install bearing cone (20) on the axle shaft so that there is slight end play. When bearing cone (20) is cool, apply clean SAE 30 oil to the bearing cone. Note: The adjusting nut must be installed so that the part number is facing away from bearing cone (20). 19. Apply clean SAE 30 oil on bearing nut (12). Install bearing nut (12) on the axle shaft. Tighten the nut until a small amount of end play remains. 20. The seal drag torque is the torque that is needed to rotate the axle housing. Use one of the following methods to measure the seal drag torque: https://127.0.0.1/sisweb/sisweb/techdoc/techdoc_print_page.jsp?returnurl=/sis... 2020/3/30
962G Wheel Loader 3BS00001-UP (MACHINE) POWERED BY 3126 Engine(SEBP... 5/10 Illustration 6 g00311446 a. To measure seal drag torque, install Tooling (G) on the axle housing. Place a torque wrench on the bolt at the center of the bar, as shown. Use the torque wrench to rotate the housing. Record the reading on the torque wrench. Illustration 7 g00311903 b. To measure seal drag torque, install a bolt and a nut through an outer mounting hole on the axle housing. Install a torque wrench on the bolt. Make sure that the handle is aligned with the center of the axle shaft. Use the torque wrench to rotate the housing. Record the reading on the torque wrench. Use the following formula to calculate the actual seal drag torque: Table 2 B "SDT" is the actual seal drag torque in newton meters (N m). "C" is the torque wrench reading in newton meters (N m). "B" is the length of the torque wrench in meters. "A" is the bolt circle radius of axle housing (2) in meters. This is equal to 0.229 m (9.016 inch). 21. Tighten nut (11) by using one of the following methods: https://127.0.0.1/sisweb/sisweb/techdoc/techdoc_print_page.jsp?returnurl=/sis... 2020/3/30
962G Wheel Loader 3BS00001-UP (MACHINE) POWERED BY 3126 Engine(SEBP... 6/10 Illustration 8 g00303174 Illustration 9 g00311446 a. Rotate the axle housing. Use Tooling (E) to tighten bearing nut (11). Install Tooling (G) on the axle housing. Place a torque wrench on the bolt at the center of Tooling (G). The torque wrench reading is equal to the seal drag torque plus the axle bearing preload rolling torque. Use the seal drag torque that was recorded in Step 20. Note: The preload rolling torque for new bearings is 9 to 16 N m (7 to 12 lb ft). The preload rolling torque for used bearings is 4.5 to 8 N m (3.5 to 6 lb ft). Illustration 10 g00311903 https://127.0.0.1/sisweb/sisweb/techdoc/techdoc_print_page.jsp?returnurl=/sis... 2020/3/30
962G Wheel Loader 3BS00001-UP (MACHINE) POWERED BY 3126 Engine(SEBP... 7/10 Illustration 11 g00303174 b. Use the torque wrench to rotate the axle housing. Use Tooling (E) to tighten nut (11). The torque wrench reading must equal the axle bearing preload rolling torque plus the actual seal drag torque. Use the seal drag torque that was recorded in Step 20. Use the following formula to calculate the required torque wrench reading. This formula is used to measure torque at the bolt circle. Table 3 B + A "C" is the torque wrench reading in newton meters (N m). "B" is the length of the torque wrench in meters. "A" is the bolt circle radius of axle housing (2) in meters. This equals 0.229 m (9.016 inch). "SDT" is the actual seal drag torque in newton meters (N m). "T" is the axle bearing preload rolling torque. The preload rolling torque for new bearings is 9 to 16 N m (7 to 12 lb ft). The preload rolling torque for used bearings is 4.5 to 8 N m (3.5 to 6 lb ft). 22. Make sure that axle shaft (4) has zero end play. 23. If the axle bearing preload rolling torque exceeds the specification, back off nut (11) by 1/8 turn and reseat bearing cone (13) against nut (11). Perform Step 21 again. https://127.0.0.1/sisweb/sisweb/techdoc/techdoc_print_page.jsp?returnurl=/sis... 2020/3/30
962G Wheel Loader 3BS00001-UP (MACHINE) POWERED BY 3126 Engine(SEBP... 8/10 Illustration 12 g00303171 Illustration 13 g00303170 24. The following steps are for the assembly of planetary carrier assembly (5): a. Install retaining ring (3) in the carrier. b. Apply a thin coat of clean SAE 30 oil on all parts of planetary carrier assembly (5). c. Install bearing (10) in planetary gear (9). d. Install thrust washers (8), planetary gear (9), and shaft (7) in the carrier. Note: If thrust washers (8) have alignment tabs, the alignment tabs should be installed towards the center of the carrier. e. Install shaft (6) in the carrier. Make sure that the spring pin hole in the shaft is aligned with the spring pin hole in the carrier. Install new spring pin (7) through the carrier and in shaft (6). Install spring pin (7) slightly below the outside surface of the carrier. f. Repeat Steps 24.a through 24.e for the remaining two planetary gears. https://127.0.0.1/sisweb/sisweb/techdoc/techdoc_print_page.jsp?returnurl=/sis... 2020/3/30
962G Wheel Loader 3BS00001-UP (MACHINE) POWERED BY 3126 Engine(SEBP... 9/10 Illustration 14 g00303169 25. Install Tooling (D) and suitable lifting slings to planetary carrier assembly (5). 26. Use a hoist to install the planetary carrier assembly in the axle housing assembly. The weight of the planetary carrier assembly is 80 kg (175 lb). Illustration 15 g00303124 27. Use Tooling (C) to install retaining ring (3) on axle shaft (4). 28. Remove axle housing assembly (2) from Tooling (B). Install the bottom half of the axle group on Tooling (B) in a vertical position. 29. Apply 6V-6640 RTV Silicone Sealant on the mating surfaces of the axle housing and of the differential housing. https://127.0.0.1/sisweb/sisweb/techdoc/techdoc_print_page.jsp?returnurl=/sis... 2020/3/30
962G Wheel Loader 3BS00001-UP (MACHINE) POWERED BY 3126 Engine(SE... 10/10 Illustration 16 g00301040 30. Apply a thin layer of Tooling (H) to the mating surface of the axle housing. Attach Tooling (A) and a suitable lifting device to axle housing assembly (2). The weight of axle housing assembly (2) is approximately 295 kg (650 lb). Carefully install the axle housing assembly. 31. Install bolts (1) that secure axle housing assembly (2) to the differential housing. Tighten bolts (1) to a torque of 300 40 N m (220 30 lb ft). End By: a. Install the fixed axle. Refer to Disassembly and Assembly, "Fixed Axle (Front) - Remove and Install". b. Install the oscillating axle. Refer to Disassembly and Assembly, "Oscillating Axle (Rear) - Install". Copyright 1993 - 2020 Caterpillar Inc. Mon Mar 30 10:41:13 UTC+0800 2020 All Rights Reserved. Private Network For SIS Licensees. https://127.0.0.1/sisweb/sisweb/techdoc/techdoc_print_page.jsp?returnurl=/sis... 2020/3/30
Suggest: If the above button click is invalid. Please download this document first, and then click the above link to download the complete manual. Thank you so much for reading
962G Wheel Loader 3BS00001-UP (MACHINE) POWERED BY 3126 Engine(SEBP... 1/5 Shutdown SIS Previous Screen Product: WHEEL LOADER Model: 962G WHEEL LOADER 3BS Configuration: 962G Wheel Loader 3BS00001-UP (MACHINE) POWERED BY 3126 Engine Disassembly and Assembly 950G and 962G Wheel Loaders and IT62G Integrated Toolcarrier Power Train Media Number -SENR1381-10 Publication Date -01/10/2007 Date Updated -25/10/2007 i02457299 Service Brakes - Remove SMCS - 4011-011; 4251-011 Removal Procedure Table 1 Required Tools Tool Part Number Part Description Qty A 138-7573 Link Bracket 2 1P-2420 Transmission Repair Stand 1 B FT-0996 Positioning Group 4 FT-0957 Adapter Group 4 Start By: A. Remove the fixed axle. Refer to Disassembly and Assembly, "Fixed Axle (Front) - Remove". B. Remove the oscillating axle. Refer to Disassembly and Assembly, "Oscillating Axle (Rear) - Remove". Note: The axle housing assemblies that are used in the front fixed axle and in the rear oscillating axle are similar. Therefore, both axle housing assemblies can be disassembled in the same manner. https://127.0.0.1/sisweb/sisweb/techdoc/techdoc_print_page.jsp?returnurl=/sis... 2020/3/30
https://www.ebooklibonline.com Hello dear friend! Thank you very much for reading. Enter the link into your browser. The full manual is available for immediate download. https://www.ebooklibonline.com