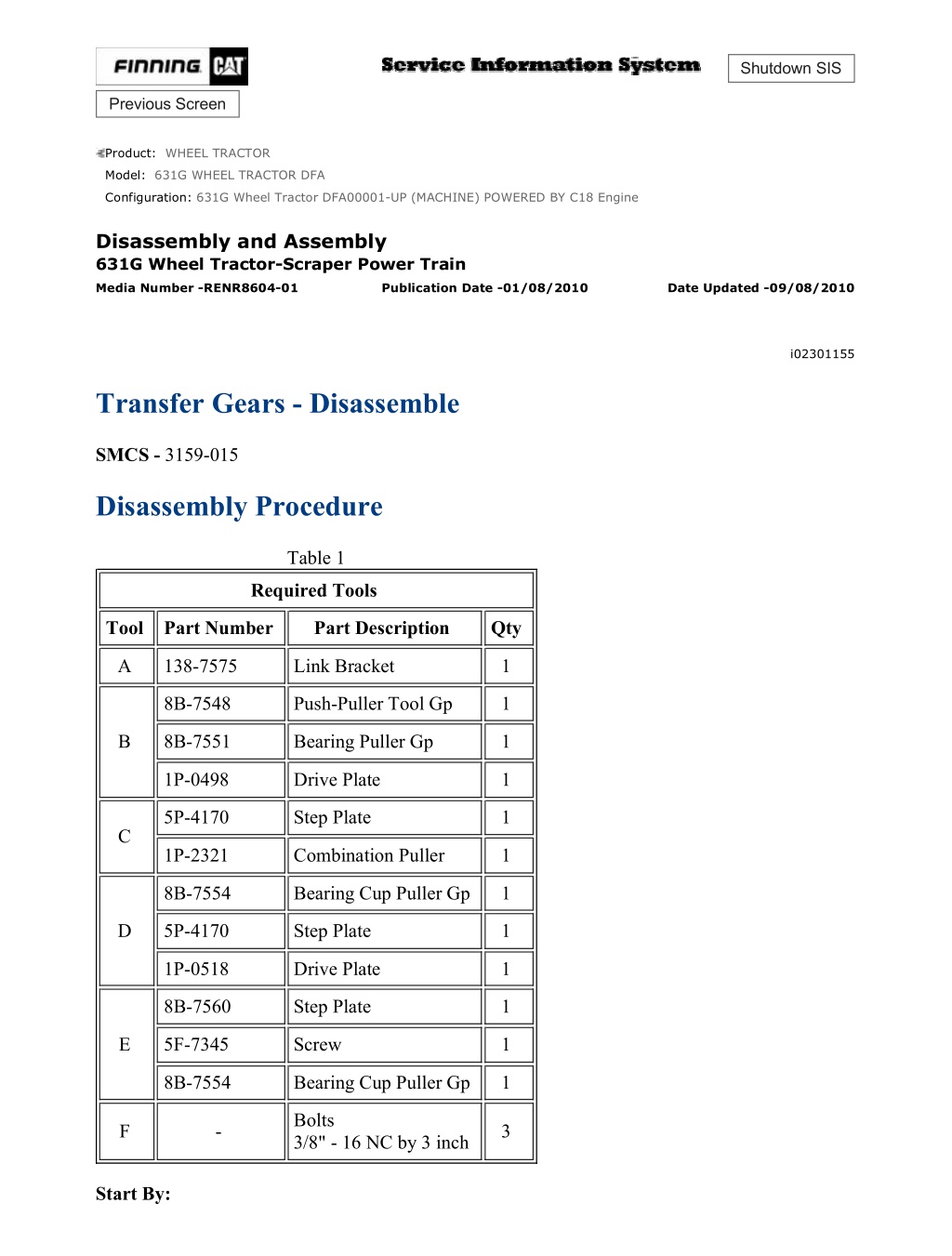
Caterpillar Cat 631G Wheel Tractor (Prefix DFA) Service Repair Manual Instant Download
Please open the website below to get the complete manualnn//
Download Presentation

Please find below an Image/Link to download the presentation.
The content on the website is provided AS IS for your information and personal use only. It may not be sold, licensed, or shared on other websites without obtaining consent from the author. Download presentation by click this link. If you encounter any issues during the download, it is possible that the publisher has removed the file from their server.
E N D
Presentation Transcript
w 1/8(W) Shutdown SIS Previous Screen Product: WHEEL TRACTOR Model: 631G WHEEL TRACTOR DFA Configuration: 631G Wheel Tractor DFA00001-UP (MACHINE) POWERED BY C18 Engine Disassembly and Assembly 631G Wheel Tractor-Scraper Power Train Media Number -RENR8604-01 Publication Date -01/08/2010 Date Updated -09/08/2010 i02301155 Transfer Gears - Disassemble SMCS - 3159-015 Disassembly Procedure Table 1 Required Tools Tool Part Number Part Description Qty A 138-7575 Link Bracket 1 8B-7548 Push-Puller Tool Gp 1 B 8B-7551 Bearing Puller Gp 1 1P-0498 Drive Plate 1 5P-4170 Step Plate 1 C 1P-2321 Combination Puller 1 8B-7554 Bearing Cup Puller Gp 1 D 5P-4170 Step Plate 1 1P-0518 Drive Plate 1 8B-7560 Step Plate 1 E 5F-7345 Screw 1 8B-7554 Bearing Cup Puller Gp 1 Bolts 3/8" - 16 NC by 3 inch F - 3 Start By: https://127.0.0.1/sisweb/sisweb/techdoc/techdoc_print_page.jsp?returnurl=/sisweb/sisw... 2021/6/14
w 2/8(W) a. Remove the transfer gear case. Refer to Disassembly and Assembly, "Transfer Gears - Remove". b. Remove the transmission oil filter base. Refer to Disassembly and Assembly, "Transmission Oil Filter Base - Remove and Install". c. Remove the transmission scavenge pump. Refer to Disassembly and Assembly, "Transmission Scavenge Pump - Remove". d. Remove the transmission oil pump. Refer to Disassembly and Assembly, "Transmission Oil Pump - Remove". NOTICE Care must be taken to ensure that fluids are contained during performance of inspection, maintenance, testing, adjusting, and repair of the product. Be prepared to collect the fluid with suitable containers before opening any compartment or disassembling any component containing fluids. Refer to Special Publication, NENG2500, "Dealer Service Tool Catalog" for tools and supplies suitable to collect and contain fluids on Cat products. Dispose of all fluids according to local regulations and mandates. NOTICE Keep all parts clean from contaminants. Contamination of the hydraulic system with foreign material will reduce the service life of the hydraulic system components. To prevent contaminants from entering the hydraulic system, always plug or cap the lines, fittings, or hoses as they are disconnected. Cover any disassembled components and clean them properly before assembly. Clean the hydraulic system properly after any major component exchange or especially after a component failure, to remove any contamination. 1. Put identification marks on components for installation purposes. https://127.0.0.1/sisweb/sisweb/techdoc/techdoc_print_page.jsp?returnurl=/sisweb/sisw... 2021/6/14
w 3/8(W) Illustration 1 g01048669 2. Remove the bolts that secure bearing cage (1) to the transfer gear case. Use Tooling (F) in order to separate bearing cage (1) from the transfer gear case. 3. Remove bearing cage (1), shims (2), and pump drive gear (3) from the transfer gear case. Illustration 2 g01102869 4. Remove the bolts that secure bearing cage (4) to the transfer gear case. Use Tooling (F) in order to separate bearing cage (4) from the transfer gear case. 5. Remove bearing cage (4), shims (5), and gear (6) from the transfer gear case. Illustration 3 g00529211 https://127.0.0.1/sisweb/sisweb/techdoc/techdoc_print_page.jsp?returnurl=/sisweb/sisw... 2021/6/14
https://www.ebooklibonline.com Hello dear friend! Thank you very much for reading. Enter the link into your browser. The full manual is available for immediate download. https://www.ebooklibonline.com
w 4/8(W) 6. Remove bearing cups (7) and (8) from the transfer gear case. Attach Tooling (A) and a suitable lifting device onto the transfer gear case. The weight of the transfer gear case is approximately 340 kg (750 lb). Turn over the transfer gear case. Remove Tooling (A). Illustration 4 g01102873 7. Remove the bolts that secure bearing cage (9) to the transfer gear case. Use Tooling (F) in order to separate bearing cage (9) from the transfer gear case. 8. Remove bearing cage (9), shims (10), and gear (11) from the transfer gear case. Illustration 5 g00529214 9. Remove bearing cup (12) from the transfer gear case. Attach Tooling (A) and a suitable lifting device onto the transfer gear case. Turn over the transfer gear case. https://127.0.0.1/sisweb/sisweb/techdoc/techdoc_print_page.jsp?returnurl=/sisweb/sisw... 2021/6/14
w 5/8(W) Illustration 6 g00529215 10. Remove bolts (13) that secure bearing cage (14) to the transfer gear case. If necessary, rotate the gear until the three threaded holes are visible in bearing cage (14). Install Tooling (F) through gear (15) and into bearing cage (14). Tighten Tooling (F) evenly until bearing cage (14) and gear (15) separate from the transfer gear case. Remove bearing cage (14) and gear (15) as a unit from the transfer gear case. Illustration 7 g00529216 Illustration 8 g00529257 11. Remove retaining ring (16) from gear (15). Remove bearing (17) and bearing cage (14) from gear (15). https://127.0.0.1/sisweb/sisweb/techdoc/techdoc_print_page.jsp?returnurl=/sisweb/sisw... 2021/6/14
w 6/8(W) Illustration 9 g01048544 12. Remove bearing (17) from bearing cage (14). Illustration 10 g01048548 13. Remove bolts (19) and separate gear (20) from gear (11). Use Tooling (B) to remove bearing cone (18) from gear (11). Repeat the procedure for the bearing cone on the opposite side of the gear. Illustration 11 g01048549 14. Use Tooling (C) to remove bearing cone (21) from gear (6). Repeat the procedure for the bearing cone on the opposite side of gear (6). https://127.0.0.1/sisweb/sisweb/techdoc/techdoc_print_page.jsp?returnurl=/sisweb/sisw... 2021/6/14
w 7/8(W) Illustration 12 g01048550 15. Use Tooling (C) to remove bearing cone (22) from gear (3). Repeat the procedure for the bearing cone on the opposite side of gear (3). Illustration 13 g01048551 16. Use Tooling (D) to remove bearing cup (23) from bearing cage (4). Remove O-ring seal (24) from bearing cage (4). Illustration 14 g01048553 17. Remove bearing cup (25) from bearing cage (9). https://127.0.0.1/sisweb/sisweb/techdoc/techdoc_print_page.jsp?returnurl=/sisweb/sisw... 2021/6/14
w 8/8(W) Illustration 15 g01048552 18. Use Tooling (E) to remove bearing cup (26) from bearing cage (1). Remove O-ring seal (27) from bearing cage (1). Copyright 1993 - 2021 Caterpillar Inc. Mon Jun 14 08:38:06 UTC+0800 2021 All Rights Reserved. Private Network For SIS Licensees. https://127.0.0.1/sisweb/sisweb/techdoc/techdoc_print_page.jsp?returnurl=/sisweb/sisw... 2021/6/14
w 1/9(W) Shutdown SIS Previous Screen Product: WHEEL TRACTOR Model: 631G WHEEL TRACTOR DFA Configuration: 631G Wheel Tractor DFA00001-UP (MACHINE) POWERED BY C18 Engine Disassembly and Assembly 631G Wheel Tractor-Scraper Power Train Media Number -RENR8604-01 Publication Date -01/08/2010 Date Updated -09/08/2010 i07232119 Transfer Gears - Assemble SMCS - 3159-016 Assembly Procedure Table 1 Required Tools Tool Part Number Part Description Qty A 138-7575 Link Bracket 1 G 1P-0510 Driver Group 1 H 8T-5096 Dial Indicator 1 NOTICE Keep all parts clean from contaminants. Contamination of the hydraulic system with foreign material will reduce the service life of the hydraulic system components. To prevent contaminants from entering the hydraulic system, always plug or cap the lines, fittings, or hoses as they are disconnected. Cover any disassembled components and clean them properly before assembly. Clean the hydraulic system properly after any major component exchange or especially after a component failure, to remove any contamination. https://127.0.0.1/sisweb/sisweb/techdoc/techdoc_print_page.jsp?returnurl=/sisweb/sisw... 2021/6/14
w 2/9(W) 1. Clean all parts and inspect all parts. If any parts are worn or damaged, use new parts for replacement. 2. Lubricate O-ring seals with the lubricant that is being sealed. Illustration 1 g01048544 3. Install bearing (17) into bearing cage (14). Illustration 2 g00529216 4. Use Tooling (G) to install bearing (17) and bearing cage (14) to gear (15). Install bearing (17) and bearing cage (14) until the retaining ring groove is visible. Install retaining ring (16) to gear (15). https://127.0.0.1/sisweb/sisweb/techdoc/techdoc_print_page.jsp?returnurl=/sisweb/sisw... 2021/6/14
w 3/9(W) Illustration 3 g00529215 5. Position gear (15) and bearing cage (14) in the transfer gear case. Install bolts (13) that secure bearing cage (14) to the transfer gear case. Tighten bolts (13) to a torque of 55 10 N m (41 7 lb ft). Illustration 4 g01048552 6. Install O-ring seal (27) onto bearing cage (1). Lower the temperature of bearing cup (26). Install bearing cup (26) to bearing cage (1). Check that bearing cup (26) is seated in the bore of bearing cage (1). Illustration 5 g01048553 7. Lower the temperature of bearing cup (25). Install bearing cup (25) to bearing cage (9). Check that bearing cup (25) is seated in the bore of bearing cage (9). https://127.0.0.1/sisweb/sisweb/techdoc/techdoc_print_page.jsp?returnurl=/sisweb/sisw... 2021/6/14
w 4/9(W) Illustration 6 g01048551 8. Install O-ring seal (24) to bearing cage (4). Lower the temperature of bearing cup (23). Install bearing cup (23) to bearing cage (4). Check that bearing cup (23) is seated in the bore of bearing cage (4). Illustration 7 g01048550 9. Raise the temperature of bearing cone (22). Install bearing cone (22) on gear (3). Repeat the procedure for the bearing cone on the opposite side of gear (3). Illustration 8 g01048549 https://127.0.0.1/sisweb/sisweb/techdoc/techdoc_print_page.jsp?returnurl=/sisweb/sisw... 2021/6/14
w 5/9(W) 10. Raise the temperature of bearing cone (21). Install bearing cone (21) on gear (6). Repeat the procedure for the bearing cone on the opposite side of gear (6). Illustration 9 g01048548 11. Raise the temperature of bearing cone (18). Install bearing cone (18) on gear (11). Repeat the procedure for the bearing cone on the opposite side of gear (11). 12. Position gear (20) on gear (11). Install bolts (19). Tighten bolts (19) to a torque of 55 10 N m (41 7 lb ft). Attach Tooling (A) and a suitable lifting device onto the transfer gear case. The weight of the transfer gear case is approximately 340 kg (750 lb). Turn over the transfer gear case. Remove Tooling (A). Illustration 10 g00529214 13. Lower the temperature of bearing cup (12). Use Tooling (G) to install bearing cup (12) to the transfer gear case. Check that bearing cup (12) is seated in the bore of the transfer gear case. https://127.0.0.1/sisweb/sisweb/techdoc/techdoc_print_page.jsp?returnurl=/sisweb/sisw... 2021/6/14
w 6/9(W) Illustration 11 g00529695 Illustration 12 g01048735 14. Position gear (11) in the transfer gear case. Install bearing cage (9) and shims (10). Install bolts (28) that hold bearing cage (9) in position. Tighten bolts (28) to a torque of 55 10 N m (41 7 lb ft). 15. Position Tooling (H) in the transfer gear case, as shown. Make sure that the dial indicator is in contact with gear (11). Use a pry bar to move gear (11) up and down. Adjust shims (10) to obtain an end play of 0.15 0.05 mm (0.006 0.002 inch). Tighten bolts (28) to a torque of 55 10 N m (41 7 lb ft). Illustration 13 g00529211 https://127.0.0.1/sisweb/sisweb/techdoc/techdoc_print_page.jsp?returnurl=/sisweb/sisw... 2021/6/14
w 7/9(W) 16. Use Tooling (G) to install bearing cups (7) and (8) to the transfer gear case. Check that bearing cups (7) and (8) is seated in the bore of the transfer gear case. Illustration 14 g00529696 Illustration 15 g01048736 17. Position gear (6) in the transfer gear case with the internal snap ring groove facing up. Install bearing cage (4) and shims (5). Install the bolts (29) that hold bearing cage (4) in position. Tighten bolts (29) to a torque of 55 10 N m (41 7 lb ft). 18. Attach Tooling (A) and a suitable lifting device to the transfer gear case. Place the transfer gear case on wood blocks, as shown. Position Tooling (H) on the transfer gear case, as shown. Make sure that the dial indicator is in contact with gear (6). Use a pry bar to move gear (6) up and down. Adjust shims (5) to obtain an end play of 0.15 0.05 mm (0.006 0.002 inch). Tighten bolts (29) to a torque of 55 10 N m (41 7 lb ft). https://127.0.0.1/sisweb/sisweb/techdoc/techdoc_print_page.jsp?returnurl=/sisweb/sisw... 2021/6/14
w 8/9(W) Illustration 16 g00529697 Illustration 17 g01048737 19. Position gear (3) in the transfer gear case. Install bearing cage (1) and shims (2). Install the bolts (30) that hold bearing cage (1) in position. Tighten bolts (30) to a torque of 55 10 N m (41 7 lb ft). 20. Position Tooling (H) on the transfer gear case, as shown. Make sure that the dial indicator is in contact with gear (3). Use a pry bar to move gear (3) up and down. Adjust shims (2) to obtain an end play of 0.15 0.05 mm (0.006 0.002 inch). Tighten bolts (30) to a torque of 55 10 N m (41 7 lb ft). End By: a. Install the transmission oil pump. Refer to Disassembly and Assembly, "Transmission Oil Pump - Install". b. Install the transmission scavenge pump. Refer to Disassembly and Assembly, "Transmission Scavenge Pump - Install". c. Install the transmission oil filter base. Refer to Disassembly and Assembly, "Transmission Oil Filter Base - Remove and Install". d. Install the transfer gear case. Refer to Disassembly and Assembly, "Transfer Gears - Install". https://127.0.0.1/sisweb/sisweb/techdoc/techdoc_print_page.jsp?returnurl=/sisweb/sisw... 2021/6/14
w 9/9(W) Copyright 1993 - 2021 Caterpillar Inc. Mon Jun 14 08:39:02 UTC+0800 2021 All Rights Reserved. Private Network For SIS Licensees. https://127.0.0.1/sisweb/sisweb/techdoc/techdoc_print_page.jsp?returnurl=/sisweb/sisw... 2021/6/14
w 1/36(W) Shutdown SIS Previous Screen Product: WHEEL TRACTOR Model: 631G WHEEL TRACTOR DFA Configuration: 631G Wheel Tractor DFA00001-UP (MACHINE) POWERED BY C18 Engine Disassembly and Assembly 631G Wheel Tractor-Scraper Power Train Media Number -RENR8604-01 Publication Date -01/08/2010 Date Updated -09/08/2010 i02568748 Transmission Planetary - Disassemble SMCS - 3030-015 Disassembly Procedure Table 1 Required Tools Tool Part Number Part Description Qty A 1P-2420 Transmission Repair Stand 1 B FT-0833 Clamp 2 C 2P-8312 Retaining Ring Pliers 1 D FT-1335 Transmission Fixture 1 E 1P-0520 Driver Group 1 F 138-7575 Link Bracket 2 G 138-7573 Link Bracket 2 Forcing Bolt 3/8 - 16 NC by 3 inch H - 2 Start By: A. Separate the transfer gears from the transmission. Refer to Disassembly and Assembly , "Torque Converter, Transmission and Transfer Gear - Separate". B. Remove the transmission hydraulic control valve. Refer to Disassembly and Assembly , "Transmission Hydraulic Control Valve - Remove". NOTICE https://127.0.0.1/sisweb/sisweb/techdoc/techdoc_print_page.jsp?returnurl=/sisweb/sisw... 2021/6/14
w 2/36(W) Care must be taken to ensure that fluids are contained during performance of inspection, maintenance, testing, adjusting and repair of the product. Be prepared to collect the fluid with suitable containers before opening any compartment or disassembling any component containing fluids. Refer to Special Publication, NENG2500, "Caterpillar Dealer Service Tool Catalog" for tools and supplies suitable to collect and contain fluids on Caterpillar products. Dispose of all fluids according to local regulations and mandates. Illustration 1 g01013127 1. Install Tooling (F) and a suitable lifting device onto transmission assembly (1) . Position transmission assembly (1) onto Tooling (A) . The transmission assembly weighs approximately 703 kg (1550 lb). Illustration 2 g01013128 https://127.0.0.1/sisweb/sisweb/techdoc/techdoc_print_page.jsp?returnurl=/sisweb/sisw... 2021/6/14
w 3/36(W) 2. Remove bolts (2) . Remove the transmission assembly from transmission housing (3) . Position the transmission assembly ontosuitable blocks. Illustration 3 g00506814 3. Remove bolts (4) from clutch housing (5) . Illustration 4 g01013129 Personal injury can result from being struck by parts propelled by a released spring force. Make sure to wear all necessary protective equipment. Follow the recommended procedure and use all recommended tooling to release the spring force. https://127.0.0.1/sisweb/sisweb/techdoc/techdoc_print_page.jsp?returnurl=/sisweb/sisw... 2021/6/14
w 4/36(W) 4. Use Tooling (B) in order to hold the piston into clutch housing (5) . Install Tooling (F) and a suitable lifting device onto clutch housing (5) . Remove clutch housing (5) from the transmission assembly. The weight of clutch housing (5) is approximately 27 kg (60 lb). Illustration 5 g00506820 5. Remove piston (6) from clutch housing (5) . Remove a seal ring (7) from piston (6) and from clutch housing (5) . Illustration 6 g00506843 Note: Friction discs and clutch plates that are removed from each clutch housing should be kept with the correct clutch housing. Mixing the clutch plates and friction discs may cause improper operation of the transmission or damage to the transmission. 6. Remove springs (8) , dowels (9) , friction discs (10) and clutch plates (11) from clutch housing (12) . https://127.0.0.1/sisweb/sisweb/techdoc/techdoc_print_page.jsp?returnurl=/sisweb/sisw... 2021/6/14
w 5/36(W) Illustration 7 g00506849 7. Remove ring gear (13) from clutch housing (12) . Illustration 8 g01013132 Personal injury can result from being struck by parts propelled by a released spring force. Make sure to wear all necessary protective equipment. Follow the recommended procedure and use all recommended tooling to release the spring force. 8. Use Tooling (B) in order to hold the piston into clutch housing (12) . Install Tooling (F) and a suitable lifting device onto clutch housing (12) . Remove clutch housing (12) from housing assembly (14) . The weight of clutch housing (12) is approximately 27 kg (60 lb). https://127.0.0.1/sisweb/sisweb/techdoc/techdoc_print_page.jsp?returnurl=/sisweb/sisw... 2021/6/14
w 6/36(W) Illustration 9 g00506903 9. Remove piston (15) from clutch housing (12) . Remove seal rings (16) from piston (15) and from clutch housing (12) . Illustration 10 g00506952 10. Remove springs (17) , dowels (18) , friction discs (19) and clutch plates (20) from housing assembly (14) . https://127.0.0.1/sisweb/sisweb/techdoc/techdoc_print_page.jsp?returnurl=/sisweb/sisw... 2021/6/14
w 7/36(W) Illustration 11 g00506953 11. Remove retaining ring (21) from shaft (22) . Illustration 12 g01013138 12. Install Tooling (G) and a suitable lifting device onto carrier assembly (23) . Remove carrier assembly (23) from housing assembly (14) . The weight of carrier assembly (14) is approximately 34 kg (75 lb). Illustration 13 g00506968 13. Remove bolts (24) and oil slinger (25) from carrier assembly (23) . Remove bearing (26) from carrier assembly (23) . https://127.0.0.1/sisweb/sisweb/techdoc/techdoc_print_page.jsp?returnurl=/sisweb/sisw... 2021/6/14
w 8/36(W) Illustration 14 g00506977 14. Use a hammer and a punch in order to push pin (27) into shaft (28) . Illustration 15 g01110560 15. Remove shaft (28) , thrust discs (29) and planetary gears (30) from carrier assembly (23) . Remove pin (27) from shaft (28) . Illustration 16 g00506999 https://127.0.0.1/sisweb/sisweb/techdoc/techdoc_print_page.jsp?returnurl=/sisweb/sisw... 2021/6/14
w 9/36(W) 16. Remove bearings (31) from planetary gear (30) . 17. Repeat Steps 14, 15, and 16 in order to remove the remaining shaft assemblies. Illustration 17 g00507000 18. Use a hammer and a punch in order to push pin (32) into shaft (33) . Illustration 18 g01110562 19. Remove shaft (33) , thrust discs (34) and gear (35) from carrier assembly (23) . Remove tube (36) from shaft (33) . Remove pin (32) from shaft (33) . https://127.0.0.1/sisweb/sisweb/techdoc/techdoc_print_page.jsp?returnurl=/sisweb/sisw... 2021/6/14
w 10/36(W) Illustration 19 g00834162 20. Remove bearings (37) from gear (35) . 21. Repeat Steps 18, 19, and 20 in order to remove the remaining three shaft assemblies from the carrier assembly. Illustration 20 g00834167 22. Remove bolts (39) and plates (40) from clutch housing (41) . Remove ring gear (42) from clutch housing (41) . https://127.0.0.1/sisweb/sisweb/techdoc/techdoc_print_page.jsp?returnurl=/sisweb/sisw... 2021/6/14
w 11/36(W) Illustration 21 g00507153 23. Remove bolts (43) that secure clutch housing (41) to housing assembly (14) . Illustration 22 g01013141 Personal injury can result from being struck by parts propelled by a released spring force. Make sure to wear all necessary protective equipment. Follow the recommended procedure and use all recommended tooling to release the spring force. 24. Use Tooling (B) in order to hold the piston into clutch housing (41) . Install Tooling (F) and a suitable lifting device onto clutch housing (41) . Remove clutch housing (41) from housing assembly (14) . The weight of clutch housing (41) is approximately 34 kg (75 lb). https://127.0.0.1/sisweb/sisweb/techdoc/techdoc_print_page.jsp?returnurl=/sisweb/sisw... 2021/6/14
w 12/36(W) Illustration 23 g00507166 25. Remove piston (44) from clutch housing (41) . Remove a seal ring (45) from piston (44) and from clutch housing (41) . Illustration 24 g00834173 26. Remove springs (46) , friction discs (47) , and clutch plates (48) from housing assembly (14) . Illustration 25 g00834185 27. Remove ring gear (49) from housing assembly (14) . Remove plate assembly (50) from housing assembly (14) . https://127.0.0.1/sisweb/sisweb/techdoc/techdoc_print_page.jsp?returnurl=/sisweb/sisw... 2021/6/14
w 13/36(W) Illustration 26 g00834190 28. Remove retaining ring (51) from shaft (22) . Remove sun gear (52) and sun gear (53) from shaft (22) . Illustration 27 g00834176 29. Remove bolts (54) in order to remove carrier assembly (55) from housing assembly (14) . Illustration 28 g01110565 https://127.0.0.1/sisweb/sisweb/techdoc/techdoc_print_page.jsp?returnurl=/sisweb/sisw... 2021/6/14
Suggest: If the above button click is invalid. Please download this document first, and then click the above link to download the complete manual. Thank you so much for reading
w 14/36(W) Personal injury can result from being struck by parts propelled by a released spring force. Make sure to wear all necessary protective equipment. Follow the recommended procedure and use all recommended tooling to release the spring force. 30. Install Tooling (G) and a suitable lifting device onto carrier assembly (55) . Remove carrier assembly (55) from housing assembly (14) . The weight of carrier assembly (55) is approximately 23.5 kg (51.8 lb). Illustration 29 g00834192 31. Use a hammer and a punch in order to push pin (56) into shaft (57) . Illustration 30 g01110566 https://127.0.0.1/sisweb/sisweb/techdoc/techdoc_print_page.jsp?returnurl=/sisweb/sisw... 2021/6/14
https://www.ebooklibonline.com Hello dear friend! Thank you very much for reading. Enter the link into your browser. The full manual is available for immediate download. https://www.ebooklibonline.com