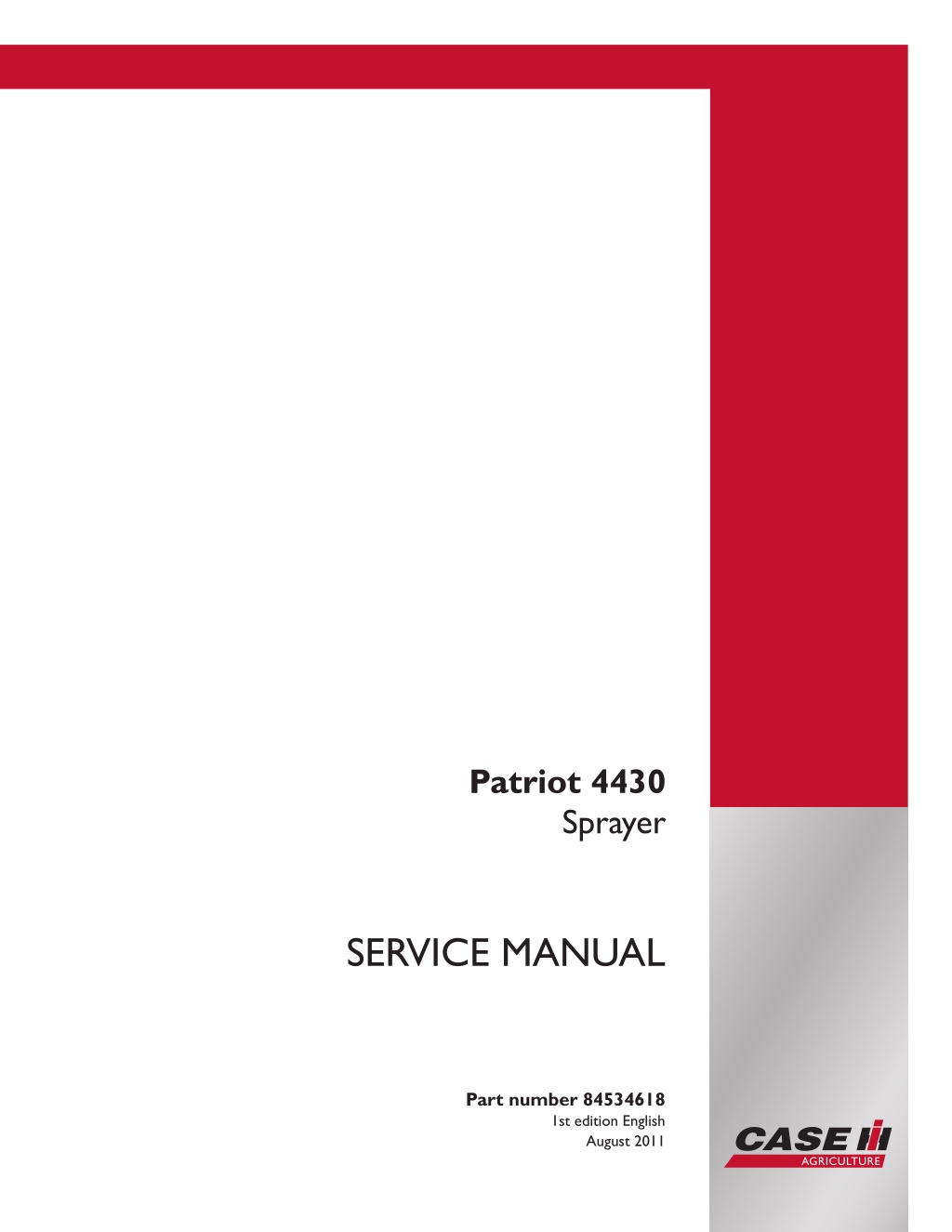
CASE IH Patriot 4430 Sprayer Service Repair Manual Instant Download
Please open the website below to get the complete manualnn// n
Download Presentation

Please find below an Image/Link to download the presentation.
The content on the website is provided AS IS for your information and personal use only. It may not be sold, licensed, or shared on other websites without obtaining consent from the author. Download presentation by click this link. If you encounter any issues during the download, it is possible that the publisher has removed the file from their server.
E N D
Presentation Transcript
Patriot 4430 Sprayer SERVICE MANUAL Part number 84534618 1st edition English Printed in U.S.A. Copyright 2011 CNH America LLC. All Rights Reserved. Case IH is a registered trademark of CNH America LLC. Racine Wisconsin 53404 U.S.A. August 2011
SERVICE MANUAL Patriot 4430 84534618 27/08/2011 EN
Contents INTRODUCTION HYDRAULIC, PNEUMATIC, ELECTRICAL, ELECTRONIC SYSTEMS A PRIMARY HYDRAULIC POWER SYSTEM.............................................. A.10.A ELECTRICAL POWER SYSTEM ........................................................ A.30.A LIGHTING SYSTEM...................................................................... A.40.A FAULT CODES ........................................................................... A.50.A ENGINE AND PTO IN................................................................... B ENGINE .................................................................................. B.10.A FUEL AND INJECTION SYSTEM........................................................ B.20.A AIR INTAKE SYSTEM.................................................................... B.30.A EXHAUST SYSTEM Emissions control .................................................. B.40.B ENGINE COOLANT SYSTEM ........................................................... B.50.A TRANSMISSION, DRIVE AND PTO OUT........................................ C TRANSMISSION Hydrostatic............................................................. C.20.F AXLES, BRAKES AND STEERING................................................. D FRONT AXLE ............................................................................ D.10.A REAR AXLE .............................................................................. D.12.A STEERING Hydraulic..................................................................... D.20.C SERVICE BRAKE Hydraulic.............................................................. D.30.C PARKING BRAKE Hydraulic ............................................................. D.32.C SUSPENSION Mechanical............................................................... D.40.B SUSPENSION Hydraulic ................................................................. D.40.C WHEELS AND TRACKS Wheels......................................................... D.50.C FRAME AND CAB ........................................................................ E SHIELD................................................................................... E.20.A OPERATOR AND SERVICE PLATFORM................................................ E.30.A USER CONTROLS AND SEAT Operator seat ........................................... E.32.C USER PLATFORM ....................................................................... E.34.A 84534618 27/08/2011
https://www.ebooklibonline.com Hello dear friend! Thank you very much for reading. Enter the link into your browser. The full manual is available for immediate download. https://www.ebooklibonline.com
ENVIRONMENT CONTROL Heating, ventilation and air-conditioning................... E.40.D FRAME POSITIONING ................................................................. F TRAVELLING Towing..................................................................... F.10.D STABILISING Static levelling............................................................. F.20.C STABILISING Working stabilising ........................................................ F.20.D HITCH AND WORKING TOOL....................................................... H BOOM Lift ................................................................................ H.20.B BOOM Tilt ................................................................................ H.20.C BOOM Unfold............................................................................. H.20.G BOOM Stabilising......................................................................... H.20.J FIELD PROCESSING ................................................................... L SPRAYING ............................................................................... L.20.A SPRAYING Plumbing system ............................................................ L.20.B SPRAYING Pressure system............................................................. L.20.C SPRAYING End marker .................................................................. L.20.D RINSING ................................................................................. L.22.A 84534618 27/08/2011
INTRODUCTION 84534618 27/08/2011 1
INTRODUCTION Safety rules WARNING Misuse hazard! Before starting the engine, make sure you are fully aware of the location and the function of each control. Failure to comply could result in death or serious injury. W0226A WARNING Hazard to bystanders! Always sound the horn before starting the machine. Make sure the work area is clear of other persons, domestic animals, tools, etc. before you operate the machine. Never allow anyone in the work area during machine operation. Failure to comply could result in death or serious injury. W0304A WARNING Unexpected machine movement! Always sit in the operator's seat to operate the machine. DO NOT bypass the key start switch. Sudden and unexpected machine movement or machine runaway could result. Failure to comply could result in death or serious injury. W0464A WARNING Entanglement hazard! Always keep hair and clothing away from moving parts. Do not wear loose clothing, jewelry, or other items that could entangle with moving parts and/or levers. Failure to comply could result in death or serious injury. W0445A WARNING Escaping fluid! Hydraulic fluid or diesel fuel leaking under pressure can penetrate the skin and cause infection or other injury. To prevent personal injury: Relieve all pressure before disconnecting fluid lines or per- forming work on the hydraulic system. Before applying pressure, make sure all connections are tight and all components are in good condition. Never use your hand to check for suspected leaks under pressure. Use a piece of cardboard or wood for this purpose. If injured by leaking fluid, see your doctor immediately. Failure to comply could result in death or serious injury. W0178A WARNING Avoid injury! Always do the following before lubricating, maintaining, or servicing the machine. 1. Disengage all drives. 2. Engage parking brake. 3. Lower all attachments to the ground, or raise and engage all safety locks. 4. Shut off engine. 5. Remove key from key switch. 6. Switch off battery key, if installed. 7. Wait for all machine movement to stop. Failure to comply could result in death or serious injury. W0047A CAUTION Flying objects! Wear eye protection. Do not strike steel parts with a steel hammer. Parts may break. Failure to comply could result in minor or moderate injury. C0024A 84534618 27/08/2011 3
INTRODUCTION CAUTION Flying debris! Compressed air can propel dirt, rust, etc. into the air. Wear eye and face protection when using com- pressed air. Failure to comply could result in minor or moderate injury. C0049A WARNING Personal Protective Equipment (PPE) required. When assembling, operating, or servicing the machine, wear protective clothing and PPE necessary for the particular procedure. Some PPE that may be necessary includes protective shoes, eye and/or face protection, hard hat, heavy gloves, filter mask, and hearing protection. Failure to comply could result in death or serious injury. W0353A WARNING Crushing hazard! Unit could fall if not properly supported. Follow jacking instructions provided for the unit. Use suitable jack stands. Be sure to position them properly. Failure to comply could result in death or serious injury. W0919A WARNING Explosive gas! Batteries emit explosive hydrogen gas and other fumes while charging. Ventilate the charging area. Keep the battery away from sparks, open flames, and other ignition sources. Never charge a frozen battery. Failure to comply could result in death or serious injury. W0005A WARNING Hazardous chemicals! Battery electrolyte contains sulfuric acid. Contact with skin and eyes could result in severe irritation and burns. Always wear splash-proof goggles and protective clothing (gloves and aprons). Wash hands after handling. Failure to comply could result in death or serious injury. W0006A WARNING Battery gas can explode! To prevent an explosion: 1. Always disconnect the negative (-) battery cable first. 2. Always connect the negative (-) battery cable last. 3. Do not short circuit the battery posts with metal objects. 4. Do not weld, grind, or smoke near a battery. Failure to comply could result in death or serious injury. W0011A DANGER Explosion hazard! Welding to a wheel can create an explosive air and gas mixture. Removing air from the tire or loosen- ing the tire on the wheel (breaking the bead) will NOT eliminate the hazard. ALWAYS remove the tire completely from the wheel before welding. Failure to comply will result in death or serious injury. D0033A 84534618 27/08/2011 4
SERVICE MANUAL HYDRAULIC, PNEUMATIC, ELECTRICAL, ELECTRONIC SYSTEMS Patriot 4430 84534618 27/08/2011 A
Contents HYDRAULIC, PNEUMATIC, ELECTRICAL, ELECTRONIC SYSTEMS - A PRIMARY HYDRAULIC POWER SYSTEM................................................ A.10.A Patriot 4430 ELECTRICAL POWER SYSTEM .......................................................... A.30.A Patriot 4430 LIGHTING SYSTEM........................................................................ A.40.A Patriot 4430 FAULT CODES ............................................................................. A.50.A Patriot 4430 84534618 27/08/2011 A
HYDRAULIC, PNEUMATIC, ELECTRICAL, ELECTRONIC SYSTEMS - A PRIMARY HYDRAULIC POWER SYSTEM - 10.A Patriot 4430 84534618 27/08/2011 A.10.A / 1
Contents HYDRAULIC, PNEUMATIC, ELECTRICAL, ELECTRONIC SYSTEMS - A PRIMARY HYDRAULIC POWER SYSTEM - 10.A TECHNICAL DATA PRIMARY HYDRAULIC POWER SYSTEM Torque . . . . . . . . . . . . . . . . . . . . . . . . . . . . . . . . . . . . . . . . . . . . . . . . . . . . . . . . . . . . . . . . . . . . . . . . . . . . . . . . . . . . 4 General specification - Hydraulic system pressures . . . . . . . . . . . . . . . . . . . . . . . . . . . . . . . . . . . . . . . . . . . . . 4 Valve Torque - Manifold . . . . . . . . . . . . . . . . . . . . . . . . . . . . . . . . . . . . . . . . . . . . . . . . . . . . . . . . . . . . . . . . . . . . . . . . . . 5 Valve block Torque - Two and six section valve bank . . . . . . . . . . . . . . . . . . . . . . . . . . . . . . . . . . . . . . . . . . . . . . . . . . . . . . 6 FUNCTIONAL DATA PRIMARY HYDRAULIC POWER SYSTEM Hydraulic symbol - Schematic components . . . . . . . . . . . . . . . . . . . . . . . . . . . . . . . . . . . . . . . . . . . . . . . . . . . . 7 Hydraulic symbol - Pressure control . . . . . . . . . . . . . . . . . . . . . . . . . . . . . . . . . . . . . . . . . . . . . . . . . . . . . . . . . 13 Hydraulic symbol - Directional control . . . . . . . . . . . . . . . . . . . . . . . . . . . . . . . . . . . . . . . . . . . . . . . . . . . . . . . . 15 Hydraulic symbol - Composite . . . . . . . . . . . . . . . . . . . . . . . . . . . . . . . . . . . . . . . . . . . . . . . . . . . . . . . . . . . . . . 16 Hydraulic symbol - Flow control . . . . . . . . . . . . . . . . . . . . . . . . . . . . . . . . . . . . . . . . . . . . . . . . . . . . . . . . . . . . . 19 Hydraulic symbol - Table of symbols . . . . . . . . . . . . . . . . . . . . . . . . . . . . . . . . . . . . . . . . . . . . . . . . . . . . . . . . . 20 Overview - Cylinder system troubleshooting chart . . . . . . . . . . . . . . . . . . . . . . . . . . . . . . . . . . . . . . . . . . . . . 24 Hydraulic pump Fixed displacement pump - Overview - Gear pump . . . . . . . . . . . . . . . . . . . . . . . . . . . . . . . . . . . . . . . . . . . . 25 Valve block Overview - Two section valve bank . . . . . . . . . . . . . . . . . . . . . . . . . . . . . . . . . . . . . . . . . . . . . . . . . . . . . . . . . . 26 Overview - Six section valve bank . . . . . . . . . . . . . . . . . . . . . . . . . . . . . . . . . . . . . . . . . . . . . . . . . . . . . . . . . . . 28 Identification - Two section valve bank axle/boom height electrical . . . . . . . . . . . . . . . . . . . . . . . . . . . . . . . 29 Identification - Six section valve bank functions electrical . . . . . . . . . . . . . . . . . . . . . . . . . . . . . . . . . . . . . . . 30 Pressure/flow compensating (PFC) pump Overview . . . . . . . . . . . . . . . . . . . . . . . . . . . . . . . . . . . . . . . . . . . . . . . . . . . . . . . . . . . . . . . . . . . . . . . . . . . . . . . . . 31 SERVICE Hydraulic pump Fixed displacement pump - Remove - Gear pump . . . . . . . . . . . . . . . . . . . . . . . . . . . . . . . . . . . . . . . . . . . . . 32 Fixed displacement pump - Install - Gear pump . . . . . . . . . . . . . . . . . . . . . . . . . . . . . . . . . . . . . . . . . . . . . . . 33 Fixed displacement pump - Test - Gear pump . . . . . . . . . . . . . . . . . . . . . . . . . . . . . . . . . . . . . . . . . . . . . . . . . 34 84534618 27/08/2011 A.10.A / 2
Reservoir Remove - Hydraulic tank . . . . . . . . . . . . . . . . . . . . . . . . . . . . . . . . . . . . . . . . . . . . . . . . . . . . . . . . . . . . . . . . . . . 36 Install - Hydraulic tank . . . . . . . . . . . . . . . . . . . . . . . . . . . . . . . . . . . . . . . . . . . . . . . . . . . . . . . . . . . . . . . . . . . . . 42 Oil cooler Remove . . . . . . . . . . . . . . . . . . . . . . . . . . . . . . . . . . . . . . . . . . . . . . . . . . . . . . . . . . . . . . . . . . . . . . . . . . . . . . . . . 47 Install . . . . . . . . . . . . . . . . . . . . . . . . . . . . . . . . . . . . . . . . . . . . . . . . . . . . . . . . . . . . . . . . . . . . . . . . . . . . . . . . . . . . 52 Valve Remove - Manifold . . . . . . . . . . . . . . . . . . . . . . . . . . . . . . . . . . . . . . . . . . . . . . . . . . . . . . . . . . . . . . . . . . . . . . . . 57 Disassemble - Manifold . . . . . . . . . . . . . . . . . . . . . . . . . . . . . . . . . . . . . . . . . . . . . . . . . . . . . . . . . . . . . . . . . . . . 58 Assemble - Manifold . . . . . . . . . . . . . . . . . . . . . . . . . . . . . . . . . . . . . . . . . . . . . . . . . . . . . . . . . . . . . . . . . . . . . . . 59 Install - Manifold . . . . . . . . . . . . . . . . . . . . . . . . . . . . . . . . . . . . . . . . . . . . . . . . . . . . . . . . . . . . . . . . . . . . . . . . . . 60 Test - Manifold . . . . . . . . . . . . . . . . . . . . . . . . . . . . . . . . . . . . . . . . . . . . . . . . . . . . . . . . . . . . . . . . . . . . . . . . . . . . 61 Test - Two section valve bank . . . . . . . . . . . . . . . . . . . . . . . . . . . . . . . . . . . . . . . . . . . . . . . . . . . . . . . . . . . . . . . 62 Test - Six section valve bank . . . . . . . . . . . . . . . . . . . . . . . . . . . . . . . . . . . . . . . . . . . . . . . . . . . . . . . . . . . . . . . . 63 Test - Six section valve bank relief valve . . . . . . . . . . . . . . . . . . . . . . . . . . . . . . . . . . . . . . . . . . . . . . . . . . . . . . 64 Adjust - Six section valve bank relief valve . . . . . . . . . . . . . . . . . . . . . . . . . . . . . . . . . . . . . . . . . . . . . . . . . . . . 65 Valve block Remove - Two section valve bank . . . . . . . . . . . . . . . . . . . . . . . . . . . . . . . . . . . . . . . . . . . . . . . . . . . . . . . . . . . 66 Disassemble - Two section valve bank . . . . . . . . . . . . . . . . . . . . . . . . . . . . . . . . . . . . . . . . . . . . . . . . . . . . . . . 67 Assemble - Two section valve bank . . . . . . . . . . . . . . . . . . . . . . . . . . . . . . . . . . . . . . . . . . . . . . . . . . . . . . . . . . 70 Install - Two section valve bank . . . . . . . . . . . . . . . . . . . . . . . . . . . . . . . . . . . . . . . . . . . . . . . . . . . . . . . . . . . . . 73 Remove - Six section valve bank . . . . . . . . . . . . . . . . . . . . . . . . . . . . . . . . . . . . . . . . . . . . . . . . . . . . . . . . . . . . 75 Disassemble - Six section valve bank . . . . . . . . . . . . . . . . . . . . . . . . . . . . . . . . . . . . . . . . . . . . . . . . . . . . . . . . 77 Assemble - Six section valve bank . . . . . . . . . . . . . . . . . . . . . . . . . . . . . . . . . . . . . . . . . . . . . . . . . . . . . . . . . . . 79 Install - Six section valve bank . . . . . . . . . . . . . . . . . . . . . . . . . . . . . . . . . . . . . . . . . . . . . . . . . . . . . . . . . . . . . . 82 Test - Solenoid function test . . . . . . . . . . . . . . . . . . . . . . . . . . . . . . . . . . . . . . . . . . . . . . . . . . . . . . . . . . . . . . . . 84 Pressure/flow compensating (PFC) pump Remove . . . . . . . . . . . . . . . . . . . . . . . . . . . . . . . . . . . . . . . . . . . . . . . . . . . . . . . . . . . . . . . . . . . . . . . . . . . . . . . . . 85 Install . . . . . . . . . . . . . . . . . . . . . . . . . . . . . . . . . . . . . . . . . . . . . . . . . . . . . . . . . . . . . . . . . . . . . . . . . . . . . . . . . . . . 86 84534618 27/08/2011 A.10.A / 3
HYDRAULIC, PNEUMATIC, ELECTRICAL, ELECTRONIC SYSTEMS - PRIMARY HYDRAULIC POWER SYSTEM PRIMARY HYDRAULIC POWER SYSTEM - Torque NOTICE: Plugs or fittings installed into aluminum housings should always be torqued to the lower values specified for internal hex plugs of the same size. NOTE: If any plugs or fittings are removed from the pump or motor during servicing, they should be torqued as indi- cated below. NOTE: Always install new O-rings before reinstalling the plugs or fittings. Description Torque Pump/Fitting 7/16-20 O-ring Pump/Fitting 9/16-18 O-ring Pump/Fitting 3/4-16 O-ring Pump/Fitting 7/8-14 O-ring Pump/Fitting 1-1/16-12 O-ring Pump/Fitting 1-5/16-12 O-ring Compensated Pump Mounting Bolts 20 N m (14.8 lb ft) 37 N m (27.3 lb ft) 68 N m (50.2 lb ft) 95 N m (70.1 lb ft) 163 N m (120.2 lb ft) 190 N m (140.1 lb ft) 67.8 - 74.6 N m (50.0 - 55.0 lb ft) PRIMARY HYDRAULIC POWER SYSTEM - General specification - Hydraulic system pressures Description Specification Pressure compensated pump setting 189.6 bar (2750 psi) 90 and 120 ft. boom 203.4 bar (2950 psi) 100 ft boom Pressure compensated pump flow (maximum) 58.7 l/min (15.5 US gpm) Check at 2200 RPM. Auxiliary gear pump flow (maximum) 70.8 l/min (18.7 US gpm) Check at 2200 RPM. Product pump circuit relief valve setting 172.3 bar (2500 psi) Check at 2200 RPM. Inner boom fold relief valve settings Port A Port B Boom level relief valve setting 203.4 bar (2950 psi) 103.4 bar (1500 psi) 13.8 bar (200 psi) 84534618 27/08/2011 A.10.A / 4
HYDRAULIC, PNEUMATIC, ELECTRICAL, ELECTRONIC SYSTEMS - PRIMARY HYDRAULIC POWER SYSTEM Valve - Torque - Manifold Description Torque Manifold Valve 1255-8 Plugs Manifold Valve 1255-6 Plugs Manifold Valve #8 Morb x #6 90 fitting Manifold Valve #12 Morb x #8 Straight fitting Manifold Valve #12 Morb x #12 90 fitting 47.5 N m (35.0 lb ft) 25.4 N m (225 lb in) 65.1 N m (48 lb ft) 101.7 N m (75 lb ft) 122.1 - 149.1 N m (90 - 110 lb ft) 84534618 27/08/2011 A.10.A / 5
HYDRAULIC, PNEUMATIC, ELECTRICAL, ELECTRONIC SYSTEMS - PRIMARY HYDRAULIC POWER SYSTEM Valve block - Torque - Two and six section valve bank Description Torque Two Section Valve Bank 3/4 Way Solenoid Valve Two Section Valve Bank 12 Volt DC Coil Nut Two Section Valve Bank Check Valve Two Section Valve Bank Orifice Plug Two Section Valve Bank SAE 2 Plug Two Section Valve Bank SAE -6MB x 60 FS Adapter Two Section Valve Bank SAE -6MB x 60 FS Adapter (90 Bend) Six Section Valve Bank Solenoid Valve Six Section Valve Bank 12 Volt Coil Nut Six Section Valve Bank Relief Valve 3.78 L at 13.78 Bar (1 GPM at 200 PSI) Six Section Valve Bank Relief Valve 3.78 L at 103.35 Bar (1 GPM at 1500 PSI) Six Section Valve Bank Relief Valve 3.78 L at 203.25 Bar (1 GPM at 2950 PSI) Six Section Valve Bank Check Valve Six Section Valve Bank Check Valve Six Section Valve Bank 0.125 in. Internal Hex Head SAE 2 Plug Six Section Valve Bank 0.125 in. Internal Hex Head SAE 4 Plug Six Section Valve Bank 0.3125 in. Internal Hex Head SAE 6 Plug Six Section Valve Bank SAE -6MB x -60FS Adapter Six Section Valve Bank SAE -6MB x -60FS Adapter (90 Bend) Six Section Valve Bank SAE -8MB x 80FS Adapter (90 Bend) Six Section Valve Bank Orifice Plug (1/16 in. NPTF With 0.039 in. Orifice) Six Section Valve Bank Orifice Plug (1/16 in. NPTF With 0.069 in. Orifice) Six Section Valve Bank Hollow Lock Plug 29.8 N m (22 lb ft) 4 N m (3.0 lb ft) 40.7 N m (30.0 lb ft) 4 N m (3.0 lb ft) 8.1 N m (6.0 lb ft) 31.2 N m (23.0 lb ft) 31.2 N m (23.0 lb ft) 29.8 N m (22.0 lb ft) 4 N m (3.0 lb ft) 40.7 N m (30 lb ft) 50.2 N m (37.0 lb ft) 50.2 N m (37.0 lb ft) 50.2 N m (37.0 lb ft) 40.7 N m (30.0 lb ft) 8.1 N m (6.0 lb ft) 19 N m (14 lb ft) 56.9 N m (42.0 lb ft) 31.2 N m (23.0 lb ft) 31.2 N m (23.0 lb ft) 56.9 N m (42.0 lb ft) 6.8 N m (5.0 lb ft) 6.8 N m (5.0 lb ft) 5.4 N m (4 lb ft) 84534618 27/08/2011 A.10.A / 6
HYDRAULIC, PNEUMATIC, ELECTRICAL, ELECTRONIC SYSTEMS - PRIMARY HYDRAULIC POWER SYSTEM PRIMARY HYDRAULIC POWER SYSTEM - Hydraulic symbol - Schematic components Accurate diagrams of hydraulic circuits are essential to the technician who must repair them. The diagram shows how the components interact. The diagram shows how the system works, what each component should be doing and where the oil should be going so the technician can diagnose and repair the system. There are two types of circuit diagrams: Cutaway circuit diagrams show the internal construction of the components as well as the flow paths. Using colors, shades or various patterns in the lines and passages, they show many different conditions of flow and pressure. Cutaway diagrams take considerably longer to produce because of their complexity. Schematic circuit diagrams, the shorthand system of the industry, are usually preferred for troubleshooting. A schematic diagram is made up of simple geometric symbols for the components and their controls and connec- tions. There are several systems of symbols used when making schematic diagrams: ISO International Standards Organization ANSI American National Standards Institute ASA American Standards Association JIC Joint Industry Conference A combination of symbols from these systems are shown. There are differences between the symbol systems. There is enough similarity, however, so if you understand the symbols shown, you will be able to interpret other symbols as well. Reservoirs A rectangle with the top removed represents a vented reservoir (A). A rectangle with the top in place represents a pressurized reservoir (B). 1 RCIL07CCH025AAA There are other schematic diagrams that show a slightly different version of a pressurized reservoir, but the sym- bols are similar and easily recognized. An oval with a short line on top or a rectangle with curved sides repre- sents a reservoir that is pressurized. 2 RCIL07CCH027AAA Lines connected to the reservoir usually are drawn from the top, regardless of where the actual connection is. This symbol shows a line which returns fluid above the level in the reservoir. 3 RCIL07CCH030AAA If the hydraulic line returns fluid below the level in the reservoir, it is drawn all the way to the bottom of the sym- bol. 4 RCIL07CCH032AAA 84534618 27/08/2011 A.10.A / 7
HYDRAULIC, PNEUMATIC, ELECTRICAL, ELECTRONIC SYSTEMS - PRIMARY HYDRAULIC POWER SYSTEM A hydraulic line connected to the bottom of the reservoir may be drawn from the bottom of the symbol if the bottom connection is essential to the systems operation. 5 RCIL07CCH033AAA If the pump inlet (B) must be charged or flooded with fluid above the inlet port, the reservoir symbol (A) appears above the pump symbol, and the suction line is drawn out of the bottom of the reservoir symbol. Every system reservoir has at least two hydraulic lines connected to it, and some may have many more. Often the components that are connected to the reservoir are spread all over the schematic. Rather than multiplying lines all over the schematic, individual reservoir symbols are drawn close to the components. The reservoir is usu- ally the only component symbol pictured more than once on a diagram. 6 RCIL07CCH124AAA Lines, tubes and hoses A hydraulic line, tube, hose or any conductor that carries the fluid between components is shown as a line. A work- ing line, such as an inlet pressure or return, is shown as a solid line. 7 RCIL07CCH034AAA Working lines with arrows show direction of flow. In the first example (A), fluid flows in one direction only; in the second example (B), fluid can flow in both directions. 8 RCIL07CCH035AAA Pilot or control lines (A) are broken into long dashes. Drain lines (B) for leakage oil are broken into short dashes. 9 RCIL07CCH036AAA A flexible line is shown as an arc between two dots and is always represented by a solid line. 10 RCIL07CCH026AAA 84534618 27/08/2011 A.10.A / 8
HYDRAULIC, PNEUMATIC, ELECTRICAL, ELECTRONIC SYSTEMS - PRIMARY HYDRAULIC POWER SYSTEM An enclosure outline indicates that there are several sym- bols that make up a component assembly such as a valve or a valve stack. The enclosure outline is rectangular and is broken with dashes on all sides. 11 RCIL07CCH028AAA Lines between components are drawn differently when they are crossing or connected. There are lines that cross other lines but are not connected. There are several ways to show crossing lines which are not connected. 12 RCIL07CCH038AAA Lines that are connected are shown with a dot that repre- sents the connection or shown as a tee connection. The dot connection is the most commonly used when drawing schematic diagrams. 13 RCIL07CCH047AAA Pumps There are many basic pump designs. A simple fixed dis- placement pump (A) is shown as a circle with a solid ar- row that pointing outward. The arrow points in the direc- tion that the fluid flows. If the pump is reversible (B) or designed to pump in either direction, the symbol has two arrows which point in opposite directions. The pump nor- mally has a pressure port and line (1) from which pressur- ized fluid is discharged and a suction port and line (2) into which fluid is drawn from the reservoir. 14 RCIL07CCH048AAA A variable displacement pump (A) is shown by an arrow drawn through the pump symbol at a 45 degree angle. A variable displacement, pressure compensated pump (B) is shown by a small box with an arrow, added to the side of the pump symbol. 15 RCIL07CCH040AAA If the pump is controlled by a lever (A) or a pedal (B), the appropriate symbol is added to the side of the pump. 16 RCIL07CCH041AAA 84534618 27/08/2011 A.10.A / 9
HYDRAULIC, PNEUMATIC, ELECTRICAL, ELECTRONIC SYSTEMS - PRIMARY HYDRAULIC POWER SYSTEM A drive shaft is shown as two short parallel lines extending from the side of the pump. A curved arrow, if present, on the drive shaft indicates the direction of rotation. 17 RCIL07CCH049AAA Motors Motor symbols are circles with solid black arrows, which point in the opposite direction of a pump s arrow, to show the motor as a receiver of fluid. One arrow is used for non-reversible motors (A); and two arrows are used for reversible motors (B). 18 RCIL07CCH051AAA A simple schematic diagram is shown of a hydraulic motor (A) connected to a hydraulic pump (B). 19 RCIL07CCH046AAA Cylinders A cylinder is a simple rectangle (A) representing the bar- rel. The piston and rod are represented by a tee (B), in- serted into the rectangle. The symbol can be drawn in any position. 20 RCIL07CCH055AAA 84534618 27/08/2011 A.10.A / 10
HYDRAULIC, PNEUMATIC, ELECTRICAL, ELECTRONIC SYSTEMS - PRIMARY HYDRAULIC POWER SYSTEM If the cylinder is single-acting (A), there is only one port shown on the end of the cylinder that receives pressurized fluid. The opposite end of the cylinder is left open. Both ends are closed on a double-acting cylinder (B), and two ports are shown. 21 RCIL07CCH054AAA A double rod end cylinder has a rod extending from each end of the rectangle. 22 RCIL07CCH057AAA Some cylinders have cushions built into them. The cush- ionslowsthemovementofthepistonasitnearstheendof its stroke. Cylinder cushions are shown as a smaller rec- tangle (A) on the piston. If the cushion has an adjustable orifice, a slanted arrow is drawn at 45 degrees (B) across the symbol. 23 RCIL07CCH126AAA Accessories Filters, strainers and heat exchangers are represented as squares that are turned 45 degrees and have the port connections at the corners. A dotted line perpendicular to the flow line represent a filter, strainer or screen. 24 RCIL07CCH080AAA 84534618 27/08/2011 A.10.A / 11
HYDRAULIC, PNEUMATIC, ELECTRICAL, ELECTRONIC SYSTEMS - PRIMARY HYDRAULIC POWER SYSTEM A solid line perpendicular to the flow with solid arrows pointing outward represents a cooler. 25 RCIL07CCH081AAA The symbol for a heater is like the symbol for a cooler, except the solid arrows point inward. 26 RCIL07CCH118AAA Two sets of arrows pointing inward and outward repre- sents a temperature control unit The solid arrows point in the direction that heat is dissi- pated. Or in the case of the control unit, they show that heat can be regulated. 27 RCIL07CCH119AAA An oval with details inside represents an accumulator. The details explain what type of accumulator it is: spring loaded (A), gas charged (B), or other features. The divider line indicates there is a separator between the charge and the fluid. A hollow arrow indicates gas. A spring indicates that the accumulator is spring-loaded. 28 RCIL07CCH130AAA Reference: PRIMARY HYDRAULIC POWER SYSTEM - Hydraulic symbol - Pressure control (A.10.A) PRIMARY HYDRAULIC POWER SYSTEM - Hydraulic symbol - Directional control (A.10.A) PRIMARY HYDRAULIC POWER SYSTEM - Hydraulic symbol - Composite (A.10.A) PRIMARY HYDRAULIC POWER SYSTEM - Hydraulic symbol - Flow control (A.10.A) PRIMARY HYDRAULIC POWER SYSTEM - Hydraulic symbol - Table of symbols (A.10.A) 84534618 27/08/2011 A.10.A / 12
MORE MANUALS: https://www.ebooklibonline.com/ Suggest: If the above button click is invalid. Please download this document first, and then click the above link to download the complete manual. Thank you so much for reading
HYDRAULIC, PNEUMATIC, ELECTRICAL, ELECTRONIC SYSTEMS - PRIMARY HYDRAULIC POWER SYSTEM PRIMARY HYDRAULIC POWER SYSTEM - Hydraulic symbol - Pressure control The basic valve symbol is a square (which is called an envelope) with external port connections and an arrow inside to show the fluid passage and direction of flow. The valve usually operates by balancing fluid pressure against a spring, so a spring is shown on one side of the symbol and a pilot pressure line on the other side. Normally closed valve A normally closed valve, such as a relief or sequence valve, is shown with an arrow offset from the ports [in- let (A), outlet (B)] toward the pilot pressure line (C) side of the square. The spring (D) holds the valve closed until the pilot line pressure is greater than the spring pressure. Mentally visualize a build up of pressure in the pilot line and the envelope moving over, compressing the spring. Fluid can now flow through the valve. 1 RCIL07CCH059AAA Normally open valve A normally open valve is shown with the arrow connecting the inlet and outlet ports. It closes when pressure over- comes spring force. Mentally visualize a build up of pres- sure in the pilot line and the envelope moving over, com- pressing the spring. Fluid flow through the valve is now blocked. 2 RCIL07CCH060AAA Relief valve A relief valve is shown as a normally closed symbol con- nected between the pressure line (A) and the reservoir (B). The flow direction arrow points away from the pres- sure line port and toward the reservoir. This graphically represents how a relief valve operates. When pressure in the system overcomes the valve spring (C), flow is from the pressure line through the relief valve to the reservoir. 3 RCIL07CCH061AAA 84534618 27/08/2011 A.10.A / 13
https://www.ebooklibonline.com Hello dear friend! Thank you very much for reading. Enter the link into your browser. The full manual is available for immediate download. https://www.ebooklibonline.com