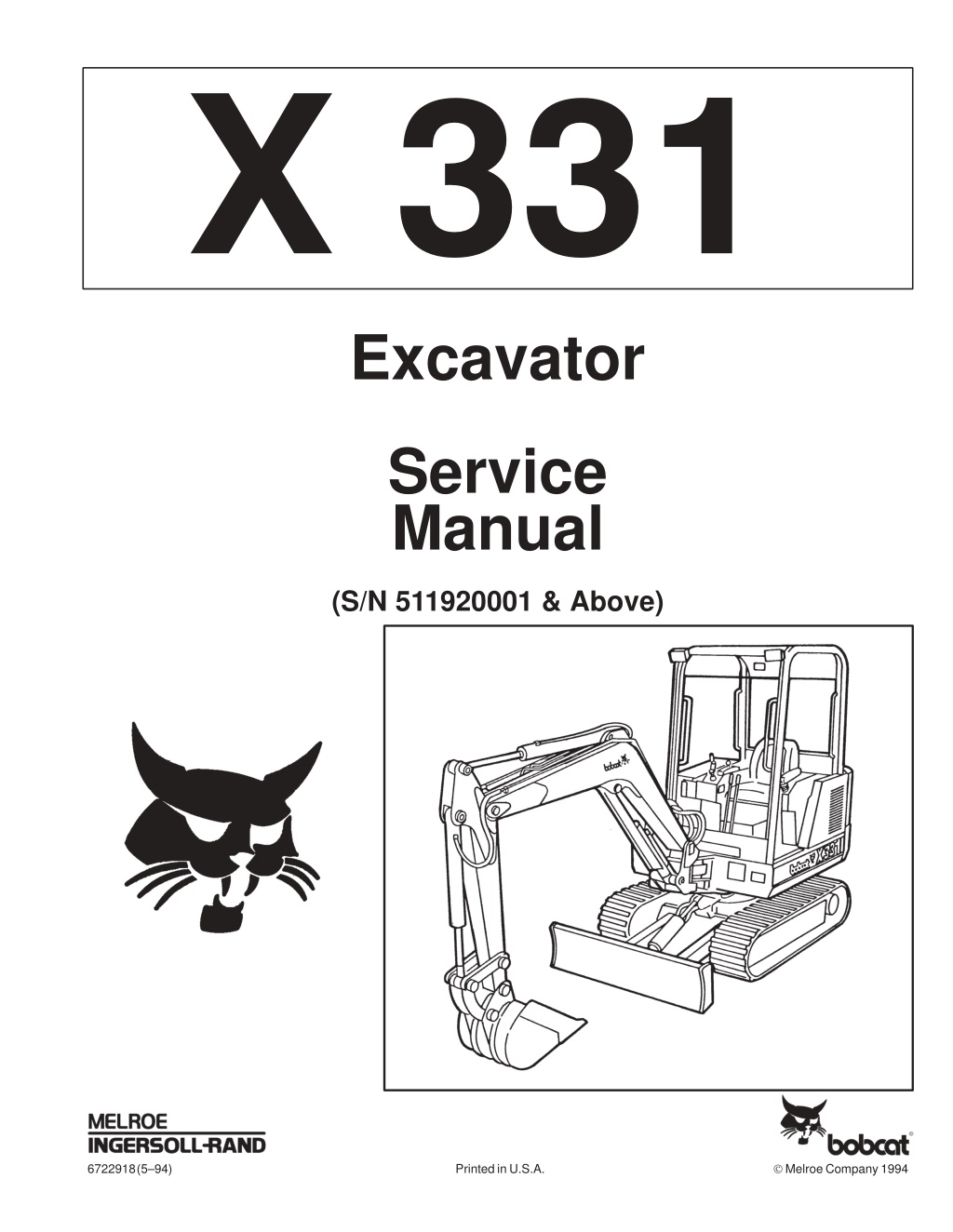
BOBCAT 331 COMPACT EXCAVATOR Service Repair Manual Instant Download (SN 511920001 & Above)
Please open the website below to get the complete manualnn// n
Download Presentation

Please find below an Image/Link to download the presentation.
The content on the website is provided AS IS for your information and personal use only. It may not be sold, licensed, or shared on other websites without obtaining consent from the author. Download presentation by click this link. If you encounter any issues during the download, it is possible that the publisher has removed the file from their server.
E N D
Presentation Transcript
????? Excavator Service Manual (S/N 511920001 & Above) Melroe Company 1994 6722918 (5 94) Printed in U.S.A.
MAINTENANCE SAFETY Instructions are necessary before operating or servicing machine. Read and understand the Operation & Maintenance Manual, Operator s Handbook and signs (decals) on machine. Follow warnings and instructions in the manuals when making repairs, adjustments or servicing. Check for correct function after adjustments, repairs or service. Untrained operators and failure to follow instructions can cause injury or death. WARNING W-2003-0903 Safety Alert Symbol: This symbol with a warning statement, means: Warning, be alert! Your safety is involved! Carefully read the message that follows. CORRECT CORRECT CORRECT B-10731a B-14148 B-14142 Use the correct procedure to lift and support the excavator. Always lift the blade fully before installing jackstands. Never Hydraulic instructions. service Excavator the Bobcat without Cleaning and maintenance are required daily. WRONG WRONG WRONG B-14145 B-14141 B-14147 Have good ventilation when welding or grinding painted parts. Wear dust mask when grinding painted parts. Toxic dust and gas can be produced. Vent exhaust to outside when engine must be run for service. Exhaust system must be tightly sealed. Exhaust Fumes can kill without warning. Always lower the bucket and blade to the ground before doing any maintenance. Never modify equipment or add attachments not approved by Bobcat Company. WRONG WRONG WRONG B-14143 B-14146 B-6589 B-16102 B-16102 Stop, cool and clean engine of flammable materials checking fluids. Never service or adjust machine with the engine running unless instructed to do so in the manual. Avoid contact hydraulic fluid or diesel fuel under pressure. It can penetrate the skin or eyes. Never fill fuel tank with engine running, while smoking or when near open flame. Keep body, jewelry and clothing away from electrical contact, hot parts and exhaust. Wear eye protection to guard from battery acid, compressed springs, fluids under pressure and flying debris when engines are running or tools are used. Use eye protection approved for type of welding. Keep rear door closed except for service. Close and latch door before operating the excavator. Lead-acid flammable and explosive gases. Keep arcs, sparks, flames and lighted tobacco batteries. Batteries contain acid which burns eyes or skin on contact. Wear protective clothing. If acid contacts body, flush well with water. For eye contact flush well and get immediate attention. batteries produce before moving parts, away from with leaking medical Maintenance procedures which are given in the Operation & Maintenance Manual can be performed by the owner/ operator without any specific technical training. Maintenance procedures which are not in the Operation & Maintenance Manual must be performed ONLY BY QUALIFIED BOBCAT SERVICE PERSONNEL. Always use genuine Bobcat replacement parts. The Service Safety Training Course is available from your Bobcat dealer. MSW20-0805
CONTENTS PREVENTIVE MAINTENANCE SAFETY INSTRUCTIONS SERIAL NUMBER LOCATIONS DELIVERY REPORT HYDRAULIC EXCAVATOR IDENTIFICATION PREVENTIVE MAINTENANCE HYDRAULIC SECTION DRIVE SECTION . . . . . . . . . . . . . . . . . . . . . . . . . . . . . . . . . . . . . . . . . . . . . . . . UPPER WORKS & SWING SECTION MAIN FRAME & TRACKS . . . . . . . . . . . . . . . . . . . . . . . . . . . . . . . . . . . . . . . . . ELECTRICAL SYSTEM . . . . . . . . . . . . . . . . . . . . . . . . . . . . . . . . . . . . . . . . . . . ENGINE SERVICE . . . . . . . . . . . . . . . . . . . . . . . . . . . . . . . . . . . . . . . . . . . . . . . TECHNICAL DATA . . . . . . . . . . . . . . . . . . . . . . . . . . . . . . . . . . . . . . . . . . . . . . . . . . . . . . . . . . . . . . . . . . . . . . . . . . . . . . . . . . . . . . . . . . . . . . . . . . . . . . . . . . . . . . . . . . . . . . . . . . . . . . . . . . . . . . . . . . . . . . . . . . . . . . . . . . . . . . . . . . . . . . . . . . . . . . . . . . . . . . . . . . . . . . . . . . . . . . . . . . . . . . . . . . . . . . . . . . . . . . . . . . . . . . . . . . . . . . . . . . . . . . . . . . . . . . . . . . . . . . . . . . . . . . . . . . . . . . . . i ii ii iii HYDRAULIC SECTION 1 1 2 1 3 1 4 1 5 1 6 1 7 1 8 1 . . . . . . . . . . . . . . . . . . . . . . . . . . . . . . DRIVE SECTION UPPER WORKS & SWING SECTION MAIN FRAME & TRACKS ELECTRICAL SYSTEM ENGINE SERVICE TECHNICAL DATA 331 Hydraulic Excavator (S/N 20001) 3 Service Manual
https://www.ebooklibonline.com Hello dear friend! Thank you very much for reading. Enter the link into your browser. The full manual is available for immediate download. https://www.ebooklibonline.com
FOREWORD This manual is for the Bobcat hydraulic excavator mechanic. It provides necessary servicing and adjustment procedures for the hydraulic excavator and its component parts and systems. Refer to the Operation & Maintenance Manual for operating instructions, starting procedure, daily checks, etc. A general inspection of the following items must be made after the hydraulic excavator has had service or repair: 1. Check that the ROPS/TOPS/ FOGS is in good condition and is not modified. 9. Safety treads must in good condition. 2. Check that ROPS/TOPS mounting hardware is tightened and is Melroe approved. 10. Check for correct function of indicator lamps. 3. The seat belt must be correctly installed, functional and in good condition. 11. Check hydraulic fluid level, engine oil level and fuel supply. 12. Inspect for fuel, oil or hydraulic fluid leaks. 4. Inspect for loose or broken parts or connections. 5. Machine signs must be legible and in the correct location. 13. Lubricate the hydraulic excavator. 6. Steering levers, control levers and foot pedals must return to neutral. Check that foot pedals lock and control lever locks are in working condition. 14. Check the condition of the battery and cables. 7. Inspect the air cleaner for damage or leaks. Check the condition of the element. Recommend to the owner that all necessary corrections be made before the machine is returned to service. 8. Check the electrical charging system. 331 Hydraulic Excavator (S/N 20001) 1 Service Manual
SAFETY INSTRUCTIONS Instructions are necessary before operating or servicing machine. Read Operation & Maintenance Manual, Handbook and signs (decals) on machine. Follow warnings and instructions in the manuals when making repairs, adjustments or servicing. Check for correct function after adjustments, repairs or service. Failure to follow instructions can cause injury or death. W 2003 0797 The following publications provide information on the safe use and maintenance of the loader and attachments: The Delivery Report is used to assure that complete instructions have been given to the new owner and that the machine is in safe operating condition. The Operation & Maintenance Manual delivered with the excavator gives operating information as well as routine maintenance and service procedures. It is a part of the excavator and must stay with the machine when it is sold. The excavator has machine signs (decals) which instruct on the safe operation and care. The signs and their locations are shown in the Operation & Maintenance Manual. Replacement signs are available from your Bobcat Excavator dealer. The CIMA Safety Manual delivered with the excavator gives information for safe operating and standard signals. The Service Manual and Parts Manual are available from your dealer for use by mechanics to do shop type service and repair work. Warnings on the machine and in the manuals are for your safety. Failure to obey warnings can cause injury or death. This notice identifies procedures which must be followed to avoid damage to the machine. I 2019 0284 W 2044 1285 Safety Alert Symbol: This Safety Symbol is used for important safety messages. When you see this symbol follow the safety message to avoid personal injury or death. Wear tight fitting clothing and any other required safety apparel when operating or servicing the excavator. Wear safety glasses when maintaining or servicing the excavator. Exhaust gases can kill, vent engine exhaust outdoors. Know where fire extinguishers and first aid kits are located and how to use them. Do not run the excavator where exhaust, arcs, sparks or hot components can contact flammable material, explosive dust or gases. Check fuel and hydraulic tubes, hoses and fittings for damage and leakage. Never use open flame or bare skin to check for leaks. Tighten or replace any parts that show leakage. Always clean fluid spills. Do not use gasoline or diesel fuel for cleaning parts. Use commercial nonflammable solvents. Do not use ether or starting fluids on an engine that has glow plugs. These starting aids can explode and injure you. Clean the excavator before doing any welding. Cover rubber hoses, battery and all other flammable parts. Keep a fire extinguisher near the excavator when welding. Have good ventilation when welding or grinding painted parts. Wear a dust mask when grinding painted parts. Toxic dust or gas can be produced. Stop the engine and let it cool before adding fuel. No smoking! Use the procedure in this manual for installing, connecting and jump starting batteries. 331 Hydraulic Excavator (S/N 20001) i Service Manual
SERIAL NUMBER LOCATIONS A Always use the serial number of the machine when requesting service information or when ordering parts. Early or later models (identification made by serial number) may use different parts, or it may be necessary to use a different procedure in doing a specific service operation. HYDRAULIC EXCAVATOR SERIAL NUMBER The excavator serial number is on the front of the machine frame, to the left of the boom [A]. P 2932 ENGINE SERIAL NUMBER B The engine serial number is located on the engine block, near the fuel injection pump [B]. P 2880 C DELIVERY REPORT All Delivery Report items must be explained to the owner/operator by the dealer. The dealer is to fill out the form and the owner/operator signs the form to indicate his understanding [C]. 331 Hydraulic Excavator (S/N 20001) ii Service Manual
HYDRAULIC EXCAVATOR IDENTIFICATION CONTROL LEVERS (JOYSTICK) OPERATOR SEAT BOOM BOOM CYLINDER BUCKET CYLINDER SEAT BELT BUCKET LINK BLADE CYLINDER BUCKET CANOPY (ROPS) ARM CYLINDER ENGINE COVER ARM UPPERSTRUCTURE BLADE TRACK FRAME TRACK CD 13291 CD 13292 331 Hydraulic Excavator (S/N 20001) iii Service Manual
MACHINE SIGNS TRANSLATIONS (DECALS) Follow the instructions on all the Machine Signs (Decals) that are on the excavator. Replace any damaged machine signs and be sure they are in the correct locations. Machine signs are available from your Bobcat Hydraulic Excavator dealer. 6539688 6537588 ISO 6537457 STANDARD 6588730 6537634 6587587 ISO 6537456 STANDARD 6587247 6587139 6533901 6589059 6539812 6577754 6534217 6588921 6534739 6539813 6588382 6539811 PI 13291 331 Hydraulic Excavator (S/N 20001) iv Service Manual
MACHINE SIGNS TRANSLATIONS (DECALS) (Contd) 6577754 6588380 6643356 6588716 6561379 6565990 6643355 6534739 6588715 PI 13292 331 Hydraulic Excavator (S/N 20001) v Service Manual
PREVENTIVE MAINTENANCE PREVENTIVE MAINTENANCE Page Number AIR CLEANER SERVICE Replacing the Filter Element . . . . . . . . . . . . . . . . . . . . . . . . . . . . . . . . . . . . 1 2 COOLING SYSTEM Coolant Level Coolant Replacement . . . . . . . . . . . . . . . . . . . . . . . . . . . . . . . . . . . . . . . . . . . . . . . . . . . . . . . . . . . . . . . . . . . . . . . . . . . . . . . . . . . . . . . . . . . 1 7 1 7 ENGINE COVER Procedure . . . . . . . . . . . . . . . . . . . . . . . . . . . . . . . . . . . . . . . . . . . . . . . . . . . . 1 2 ENGINE LUBRICATION SYSTEM Checking the Engine Oil Engine Oil and Filter Replacement . . . . . . . . . . . . . . . . . . . . . . . . . . . . . . . . . . . . . . . . . . . . . . . . . . . . . . . . . . . . . . . . . . . . . 1 6 1 6 FUEL SYSTEM Fuel Filters Fuel Specifications Fuel System Service Removing Air From The Fuel System . . . . . . . . . . . . . . . . . . . . . . . . . . . . . . . . . . . . . . . . . . . . . . . . . . . . . . . . . . . . . . . . . . . . . . . . . . . . . . . . . . . . . . . . . . . . . . . . . . . . . . . . . . . . . . . . . . . . . . . . . . . . . . . . . . . . . . . . . . . . . . . . . . . . . . . . . . . . . . . . . . . . . . 1 5 1 4 1 4 1 5 FINAL DRIVE CASE Checking Oil Level Draining Final Drive Case . . . . . . . . . . . . . . . . . . . . . . . . . . . . . . . . . . . . . . . . . . . . . . . . . . . . . . . . . . . . . . . . . . . . . . . . . . . . . . . . . . 1 13 1 13 HYDRAULIC SYSTEM Checking and Adding Fluid Diagnostic Couplers Hydraulic Reservoir Replacement of the Hydraulic Filter . . . . . . . . . . . . . . . . . . . . . . . . . . . . . . . . . . . . . . . . . . . . . . . . . . . . . . . . . . . . . . . . . . . . . . . . . . . . . . . . . . . . . . . . . . . . . . . . . . . . . . . . . . . . . . . . . . . . . . . . . . . . . . . . . . . . . . . . . . . . . . . . . . . . . . . . . 1 8 1 9 1 9 1 8 LUBRICATION OF THE HYDRAULIC EXCAVATOR Procedure . . . . . . . . . . . . . . . . . . . . . . . . . . . . . . . . . . . . . . . . . . . . . . . . . . . . . 1 11 SERVICE SCHEDULE Chart . . . . . . . . . . . . . . . . . . . . . . . . . . . . . . . . . . . . . . . . . . . . . . . . . . . . . . . . 1 1 USING A BOOSTER BATTERY (JUMP STARTING) Procedure . . . . . . . . . . . . . . . . . . . . . . . . . . . . . . . . . . . . . . . . . . . . . . . . . . . . 1 10 331 Hydraulic Excavator (S/N 20001) 1 1 Service Manual
SERVICE SCHEDULE Maintenance work must be done at regular intervals. Failure to do so may result in excessive and early failures. The Service Schedule is a guide for correct maintenance of the Hydraulic Excavator. Instructions are necessary before operating or servicing machine. Maintenance Manual, Handbook and signs (decals) on machine. Follow warnings and instructions in the manuals when making repairs, adjustments or servicing. Check for correct function after adjustments, repairs or service. Failure to follow instructions can cause injury or death. Read Operation & W 2003 0797 SERVICE SCHEDULE HOURS 8 10 50 100 250 500 1000 ITEM SERVICE REQUIRED Engine Air Cleaner Empty the just cap. Replace the filter element only when the red ring shows in the indicator window. Check for leaks and damaged components. Check the oil level & add oil as needed. Check coolant level in recovery bottle. Check for correct operation. Check the fastening bolts, nuts & condition of cab. Check the condition & that fasteners are tight. Check for damaged signs (decals), replace as needed. Check & adjust tension & clean. Check fluid level. Lubricate 25 grease fittings. Drain water and sediment from fuel tank/filter. Lubricate two grease fittings. Lubricate one grease fitting. Replace oil & filter element. Check & adjust tension. Check fluid level & add oil as needed. Replace filter element. Replace filter elements. Check & clean cable ends & check electrolyte level. Replace the filter element. Clean the radiator fins. Check the condition. Check & adjust valve clearance. Clean the screen with solvent. Drain, flush & add new coolant to the cooling system. Change the fluid, clean fill neck strainer. Change the oil. Engine Oil Engine Coolant System Indicator Lights Operator Cab Seat Belt Safety Signs (Decals) Tracks Hydraulic Reservoir All Machinery Pivot Points Fuel Tank/Fuel Filter Swing Circle Swing Pinion Engine Oil & Filter Alternator Belt Final Drive Case Hydraulic Filter Fuel Filters Battery Air Cleaner Cooling System Alternator & Starter Engine Valve Clearance Port Block Screen Filter Cooling System Hydraulic Tank Final Drive Case After the first 50 hours of machine operation do the following: Replace hydraulic fluid filter Check condition of fan belt. After the first 250 hours of machine operation do the following procedures: Change oil in final drive case. Check and adjust engine valve clearance. 331 Hydraulic Excavator (S/N 20001) 1 1 Service Manual
ENGINE COVER A Procedure AVOID INJURY OR DEATH Never service or adjust the machine when the engine is running unless instructed to do so in the manual. W 2012 0497 P 02885 Keep the engine cover closed when operating the machine. B W 2141 0189 Open the engine cover to service the engine. Pull on the latch and lift the engine cover up until it is fully open [A]. AIR CLEANER SERVICE Replacing the Filter Element See the Service Schedule (Page 1 1) for the correct service interval. Replace the filter element when the red ring shows in the window of the condition indicator (Item 1) [B]. P 02896 NOTE: Push the button on the condition indicator and start the engine. If the red ring does not show, do not replace the filter element. C Service the air cleaner as follows: 1. Loosen the clamp on the dust cup and remove the dust cup [C]. P 02895 2. Remove the rubber cup to clean the dust cup [D]. D P 02892 331 Hydraulic Excavator (S/N 20001) 1 2 Service Manual
AIR CLEANER SERVICE (Contd) A Replacing the Filter Element (Cont d) 3. Remove the wing nut (Item 1) [A]. 1 P 02897 4. Remove the filter element [B]. B 5. Check the air cleaner housing for damage. 6. Wiper the canister and the seal surface with a clean cloth. Do Not use compressed air. 7. Install a new filter element. Install and tighten the wing nut. 8. Install the dust cup so the arrow points up. 9. Check that all the air cleaner 10. Push the button on the condition indicator so the red ring does not show. P 02898 331 Hydraulic Excavator (S/N 20001) 1 3 Service Manual
FUEL SYSTEM A Use Number 2 diesel fuel in the engine. During very cold temperatures, Number 1 fuel can be used. (See Fuel, Coolant and Lubricants Chart, Page 8 8). 2 1 Stop and cool the engine before adding fuel. NO SMOKING! Failure to obey warnings can cause an explosion or fire. P 02921 W 2063 0887 B Fuel System Service The fuel level in the tank is indicated by the fuel gauge (Item 1) when the engine is running [A]. NOTE: When the fuel level reaches the 2.5 gals. (9,3 L) fuel setting, the low fuel light (Item 2) will come ON to alert the operator of this condition. Use the key to unlock the fuel fill door [B]. P 02920 C Turn the fill cap to remove it [C]. Use a clean, approved safety container to add fuel to the tank. Add fuel only in an area that has a free movement of air and no open flames or sparks. NO SMOKING! After the tank is full, install and tighten the fuel fill cap. Close and lock the fuel door. P 02917 Always clean up spilled fuel or oil. Keep heat, flames, sparks or lighted tobacco away from fuel and oil. Failure to use care around combustibles can cause explosion or fire which can result in injury or death. W 2103 1285 331 Hydraulic Excavator (S/N 20001) 1 4 Service Manual
FUEL SYSTEM(Contd) A To remove the water and sediment from the fuel tank, turn the upperstructure until the fuel tank is centered between the rear tracks. (If time allows, let machine sit overnight so water and sediment will settle to the bottom of the tank.) Open the drain valve (Item 1) at the bottom of the fuel tank [A]. 1 Drain all water and sediment into a container. P 03012 Fuel Filters B 2 See the Service Schedule (Page 1 1) for the correct service interval. 4 To remove the water from the filter element, open the drain valve (Item 1) at the bottom of the fuel filter [B]. Drain the water into a container. When fuel, free of water emerges from the drain valve, close the drain valve. 3 See the Service Schedule (Page 1 1) for the correct service interval for fuel filter element replacement. 1 Remove the hose (Item 2) from the filter housing and plug the hose [B], or firmly squeeze the hose, to eliminate the fuel from siphoning out of the tank when the element is removed. P 02891 C Remove the fuel filter element (Item 3) [B]. Clean the area around the filter housing. Put oil on the seal of the new filter element. Install the new fuel filter element and hand tighten only. 1 Removing Air From the Fuel System The fuel system uses an electric fuel pump (Item 1) [C]. Turn the ignition key to the ON position (do not start the engine). Loosen the filter bleed screw (Item 4) on the filter housing [B]. When fuel, free of air bubbles emerges from the filter, tighten the bleed screw (Item 4) [B]. P 02640 Leave the key in the ON position for a short period, or until all air is removed from the fuel system. 331 Hydraulic Excavator (S/N 20001) 1 5 Service Manual
ENGINE LUBRICATION SYSTEM A Checking The Engine Oil Check the engine oil every day. Stop the engine. Open the engine cover. Remove the dipstick [A]. Keep the oil between the marks on the dipstick. Use a good quality motor oil that meets API Service Classification of CE (See Fuel, Coolant and Lubrication Chart, Page 8 8). P 02888 B 1 Engine Oil and Filter Replacement P 02954 See the Service Schedule (Page 1 1) for the correct service interval. C Use the following procedure to change the oil and filter: 1. Run the engine until it is at operating temperature. 2. Turn the upperstructure so the engine oil drain plug is located between the tracks. Stop the engine. 3. Remove the drain plug (Item 1) [B]. Drain the oil into a container. 1 4. Remove the oil filter (Item 1), using a filter wrench [C]. P 02882 5. Clean the filter housing surface. Put clean oil on the filter gasket. Install the new filter and hand tighten only. D 1 6. Install and tighten the oil drain plug. 7. Remove the oil fill cap (Item 1) [D]. Put 9.0 quarts (8,5 L) of oil into the engine (See Fuel, Coolant and Lubricants Chart, Page 8 8). 8. Start the engine and let it run for several minutes. Stop the engine. Check for leaks at the oil filter and the drain plug. 9. Check the oil level and add oil as needed to bring it to the top mark on the dipstick. P 02884 331 Hydraulic Excavator (S/N 20001) 1 6 Service Manual
COOLING SYSTEM A Coolant Level 1 When the engine is cool, the coolant level in the recovery tank (Item 1) must be half full [A]. If the coolant level is low, add premixed coolant (50% water and 50% ethylene glycol) to the recovery tank. Coolant Replacement P 02879 B Do not remove radiator cap when the engine is hot. You can be seriously burned. W 2070 1285 1. Turn the upperstructure so there is access to the engine and radiator from between the tracks. Stop the engine. 2. Loosen and remove the radiator cap [B]. P 02886 C 3. Open the radiator drain valve (Item 1) [C]. 4. Drain all the coolant from the system. NOTE: Also remove all coolant from the coolant recovery tank (Item 1) [A]. 1 5. When all the coolant is removed, close the drain valve. 6. Premix 50% water and 50% ethylene glycol in separate container. Fill the radiator with the premixed coolant until it is full. Add coolant to the recovery tank until it is half full. P 03077 7. Run the engine at idle speed for about 5 10 minutes to remove the air from the cooling system (leave the radiator cap off during this operation). 8. Stop the engine. Check the coolant level and add as needed to bring it up to the radiator filler neck. Install the radiator cap and tighten. 331 Hydraulic Excavator (S/N 20001) 1 7 Service Manual
HYDRAULIC SYSTEM A Checking and Adding Fluid To check and add hydraulic fluid to the reservoir, use the following procedure: 1. Put the machine on a flat level surface. 1 2. Retract the arm and bucket cylinders, put the bucket on the ground and raise the blade. Stop the engine. 3. Check the hydraulic fluid level, it must be visible in the sight gauge (Item 1) located on the side of the hydraulic reservoir [A]. P 02916 4. If fluid level is not correct, open the hydraulic tank access door [B]. B 5. Remove the oil fill cap (Item 1) [B]. 1 6. Check the condition of the fill strainer [C]. The screen must be installed in the fill neck when adding oil. P 02917 C 7. Add the correct fluid to the reservoir until it is visible in the sight gauge (See Fuel, Coolant and Lubricants Chart, Page 8 8). 8. Install the reservoir cap and close and lock the access door. Replacement of the Hydraulic Filter P 02919 See the Service Schedule (Page 1 1) for the correct service interval. D 1. Open the engine cover. 2. Use a filter wrench and remove the filter element (Item 1) [D]. 3. Clean the housing where the filter gasket makes contact. 1 4. Put clean hydraulic oil on the gasket. Install the new filter element and hand tighten only. 5. Start the engine. Run the machine through the hydraulic functions. Stop the engine. Check the fluid level at the reservoir and add as needed. Check around the filter for leaks. P 02950 331 Hydraulic Excavator (S/N 20001) 1 8 Service Manual
HYDRAULIC SYSTEM (Contd) A Hydraulic Reservoir See the Service Schedule (Page 1 1) for the correct service interval). 1 1. Move the upperstructure so there is clearance for the reservoir drain between the tracks. 2. Retract the arm and bucket cylinders, lower the bucket to the ground. Stop the engine. 3. Remove and replace the hydraulic filter (See Page 1 8). P 03014 4. Remove the drain plug (Item 1) from the bottom of the reservoir [A]. B 5. Drain the fluid into a container. 6. Install the drain plug. 1 7. Add approximately 10.6 gals. (40 L.) of fluid to the reservoir (See Fuel, Coolant and Lubricants Chart, Page 8 8). 8. Run the machine through the hydraulic functions. Check the fluid level and add as needed. P 03075 Always clean up spilled fuel or oil. Keep heat, flames, sparks or lighted tobacco away from fuel and oil. Failure to use care around combustibles can cause explosion or fire which can result in injury or death. W 2103 1285 Diagnostic Couplers The diagnostic couplers (Item 1) located on each hydraulic pump are used to check circuit pressures [B]. 331 Hydraulic Excavator (S/N 20001) 1 9 Service Manual
USING A BOOSTER BATTERY (JUMP STARTING) Procedure A If jump starting the excavator from a second machine: When jump starting the excavator from a battery installed in a second machine. Make sure that the second machine is NOT running while using the glow plugs. High voltage spikes from a running machine can burn out the glow plugs. 1 P 02952 I 2060 0195 B If it is necessary to use a booster battery to start the engine, BE CAREFUL! Make sure the swing locking lever is in the engaged position. 1 The key switch must be in the OFF position. The booster battery must be 12 volt. Open the engine cover. Remove the two (2) bolts (Item 1) from the inside of the rear engine cover [A]. Remove the two (2) bolts (Item 1) from the side cover [B]. Remove the side cover. P 02942 Connect the end of the first cable to the positive (+) terminal of the booster battery. Connect the other end of the same cable to the positive (+) terminal (Item 1) of the machine battery [C]. C 1 Connect the end of the second cable to the negative ( ) terminal of the booster battery. Connect the other end of the same cable to the machine frame (Item 2) [C]. 2 (+) NOTE: Also see Cold Temperature Starting ( ) Condition , on Page 10 of the Operation &Maintenance Manual. Start the engine. After the engine is running, remove the cable (Item 2) connected to the frame first. Disconnect the cable from the machine battery (Item 1) [C]. (+) ( ) P 02951 Keep arcs, sparks, flames and lighted tobacco away from batteries. When jumping from booster battery make (negative) at engine frame. final connection Damage to the alternator can occur if: Do not jump start or charge a frozen or damaged battery. Warm battery to 60 F. (16 C.) before connecting to a charger. Unplug charger before connecting or disconnecting cables to battery. Never lean over battery while boosting, testing or charging. Engine is operated with battery cables disconnected. Battery cables are connected when using a fast charger or when welding on the loader. (Remove both cables from the battery.) Extra battery cables (booster cables) are connected wrong. Battery gas can explode and cause serious injury. I 2023 1285 W 2066 1296 331 Hydraulic Excavator (S/N 20001) 1 10 Service Manual
LUBRICATION OF THE HYDRAULIC EXCAVATOR A Procedure 1 Lubricate the Hydraulic Excavator as specified in the Service Schedule (Page 1 1) for the best performance of the machine. 2 Always use a good quality lithium based multi purpose grease when lubricating the machine. Apply the lubricant until extra grease shows. 3 Ref. Description (Number of Fittings) 1. Blade Cylinder Rod End, every 8 10 hours (1) [A]. 2. Blade Pivots, every 8 10 hours (2) [A]. 3. Blade Cylinder Base End, every 8 10 hours (1) [A]. P 02908 B 4. Boom Swing Bracket Pivot, top L.H., every 8 10 hours (2) [B]. 5. Boom Swing Bracket Pivot, bottom L.H., every 8 10 hours (1) [B]. 6. Boom Base Pivot, every 8 10 hours (1) [B]. 6 1 5 P 02905 7. Boom Swing Bracket Pivot, top R.H., every 8 10 hours (1) [C]. 8. Boom Swing Bracket Pivot, bottom R.H., every 8 10 hours (2) [C]. 9. Swing Circle Pinion, every 50 hours (1) [C]. Install 4 pumps of grease from a grease gun into the grease fitting. Rotate the upperstructure 180 and install 4 more pumps of grease into the grease fitting. 10. Boom Swing Cylinder Rod End, every 8 10 hours (1) [C]. 11. Boom Cylinder Base End, every 8 10 hours (1) [C]. C 7 10 11 9 8 P 02904 D 12. Boom Cylinder Rod End, every 8 10 hours (1) [D]. 13. Arm Cylinder Base End, every 8 10 hours (1) [D]. 13 12 P 02906 331 Hydraulic Excavator (S/N 20001) 1 11 Service Manual
LUBRICATION OF THE HYDRAULIC EXCAVATOR (Cont d) A Procedure (Cont d) 14 Ref. Description (Number of Fittings) 15 14. Arm Cylinder Rod End, every 8 10 hours (1) [A]. 15. Arm, Base Pivot, every 8 10 hours (1) [A]. 16. Bucket Cylinder Base End, every 8 10 hours (1) [A]. 16 P 02903 B 17. Bucket Cylinder Rod End, every 8 10 hours (1) [B]. 18. Bucket Link Pivots, every 8 10 hours (2) [B]. 19. Bucket Pivots, every 8 10 hours (3) [B]. 18 19 17 P 02909 20. Swing Circle Ball Bearings, every 50 hours (2) [C]. C NOTE: Do not over grease the swing circle or damage to the seals could result. Install 4 to 5 pumps of grease from a grease gun into each of the 2 grease fittings. Rotate the upperstructure 90 and install 4 to 5 pumps of grease into each of the 2 grease fittings. 20 P 02910 D 21. Boom Swing Cylinder Base End, every 8 10 hours (1) [D]. (Under the right side of upperstructure) 21 P 03011 331 Hydraulic Excavator (S/N 20001) 1 12 Service Manual
FINAL DRIVE CASE A Checking Oil Level 1. Put the machine on a flat surface with the plugs positioned as shown in figure [A]. 1 2. Remove the top plug (Item 1) [A]. The oil level should be at the bottom edge of the plug hole. 2 3. Add gear lube 90W through the hole if the oil level is below the hole (See Fuel, Coolant and Lubricant Chart, Page 8 8). 4. Install and tighten the plug. P 02955 5. Repeat the procedure for the other side. Draining Final Drive Case See the Service Schedule (Page 1 1) for the correct service interval. 1. Put the machine on flat level surface with the plugs positioned as shown in figure [A]. 2. Remove the bottom plug (Item 2) and top plug (Item 1) [A]. 3. After all the oil is removed, install and tighten the bottom plug (Item 2) [A]. 4. Add .55 quarts (0,5 L) of gear lube 90W to the top plug hole (or until gear lube level is at the bottom edge of the plug hole). Install the plug. 5. Repeat the procedure for the other side. 331 Hydraulic Excavator (S/N 20001) 1 13 Service Manual
HYDRAULIC SERVICE INFORMATION A When repairing hydrostatic and hydraulic systems, clean the disassembly and keep all parts clean. Always use caps and plugs on hoses, tubelines and ports to keep dirt out. Dirt can quickly damage the system. work area before I 2003 0888 1 P 03075 Description There are three (3) main relief valves, five (5) port relief valves, one (1) joystick relief valve and one (1) unloading relief valve in the hydraulic system. See hydraulic schematic for relief valve locations. MAIN RELIEF VALVES The hydraulic system has three (3) main relief valves protecting the hydraulic components from high pressure. The six (6) spool hydraulic valve uses two (2), dual pressure relief valves. These relief valves operate at 2450 2500 PSI (16896 17241 kPa) for the boom, arm, bucket and auxiliary functions. When the drive motors are activated, a shuttle valve is used to activate the high pressure side of the two (2) relief valves which increases their pressure setting to 2950 3000 PSI (20344 20689 kPa). As soon as the drive motor levers are returned to neutral, the relief valves return to the standard pressure setting at 2450 2500 PSI (16896 17241 kPa). The three spool hydraulic valve uses a single stage relief valve with a constant pressure setting of 2450 2500 PSI (16896 17241 kPa). The hydraulic pump has three (3) diagnostic couplers (Item 1) for checking each pump section s hydraulic pressure [A]. The following tools will be needed for the diagnostic coupler check: MEL 1355 Test Kit MEL 1355 3 5000 PSI Gauge MEL 1355 12 Coupler MEL 1355 4 Hose Connect the coupler and the gauge to the hose. 331 Hydraulic Excavator (S/N 20001) 2 1 Service Manual
MAIN RELIEF VALVE (Contd) A Checking the Dual Pressure Relief Valves at Diagnostic Couplers Remove the floormat, the floorboards and the rear floorcover (See Pages 4 3). To check the high pressure setting on the dual pressure relief valves, the four (4) hoses that go to the left and right hand travel sections must be removed [A]. Mark the hoses for ease of assembly. NOTE: For safety purposes, when doing any testing and/or adjusting of the dual pressure relief valves, make sure that the four (4) travel section hoses are removed from the valve. Plug the hoses and cap the tee fittings with steel caps. This will prevent the excavator from accidently being moved during the pressure tests. PI 13212 Install steel caps onto the tees and plug the hoses [B]. B NOTE: Make sure the swing locking lever is in the engaged (locked) position. With the engine off, connect the gauge assembly onto the diagnostic coupler on the pump [C]. Steel Caps NOTE: Pump Section 1 (closest to the engine) supplies fluid to the right hand side (P1 inlet port) of the 6 spool valve. Pump Section 2 (middle section) supplies fluid to the left hand side (P2 inlet port) of the 6 spool valve. Pump Section 3 (outer section) supplies fluid to the (P1 inlet port) 3 spool valve. Start the engine. Run the engine at high idle and warm the hydraulic fluid to 140 F (60 C). PI 13213 For Pump Section 1 (closest to the engine): Raise the boom. Curl the bucket until the bucket cylinder is fully extended and continue to apply hydraulic pressure until the relief valve opens. Record the pressure gauge reading. Repeat this five (5) times to get the average pressure reading (this is the right hand side, low pressure setting of the dual pressure relief valve). C Low pressure setting: 2450 2500 PSI (16896 17241 kPa) Move the RIGHT HAND travel lever forward and hold in the forward position until the relief valve opens. Record the pressure gauge reading. Repeat this five (5) times to get the average pressure reading (this is the right hand side, high pressure setting of the dual pressure relief valve). High Pressure Setting: 2950 3000 PSI (20344 20689 kPa) Stop the engine. For Pump Section 2 (center pump section) P 03226 Move the coupler/pressure gauge assembly onto the diagnostic coupler at the center pump section (Item 2) [D]. D Start the engine. Raise the boom. Move the arm towards the excavator until the arm cylinder is fully extended and the relief valve opens. Record the pressure gauge reading. Repeat this five (5) times to get the average pressure reading (this is the left hand side, low pressure setting, of the dual pressure relief valve). Low Pressure Setting: 2450 2500 PSI (16896 17241 kPa) Lower the boom to the ground. Move the LEFT HAND travel lever forward and hold in the forward position until the pressure relief valve opens. Record the pressure gauge reading. Repeat this five (5) times to get the average pressure reading (this is the left hand side, high pressure setting, of the dual pressure relief valve). P 03222 High Pressure Setting: 2950 3000 PSI (20344 20689 kPa). 331 Hydraulic Excavator (S/N 20001) 2 2 Service Manual
MORE MANUALS: https://www.ebooklibonline.com/ Suggest: If the above button click is invalid. Please download this document first, and then click the above link to download the complete manual. Thank you so much for reading
MAIN RELIEF VALVES (Contd) A Check the Single Pressure Relief Valve (3 Spool Valve) For Pump Section 3 (farthest from engine). Move the coupler/pressure gauge assembly onto the diagnostic coupler at the end of the pump (farthest from the engine) [A]. Start the engine. Raise the blade up until the blade cylinder is fully retracted and the relief valve opens. Record the pressure gauge reading. Repeat this five (5) times to get the average pressure reading. P 03225 Pressure Setting: 2450 2500 PSI (16896 17241 kPa) Lower the blade to the ground. Stop the engine. For Relief Valve Adjustment procedure (See Pages 2 4 & 2 5). 331 Hydraulic Excavator (S/N 20001) 2 3 Service Manual
https://www.ebooklibonline.com Hello dear friend! Thank you very much for reading. Enter the link into your browser. The full manual is available for immediate download. https://www.ebooklibonline.com