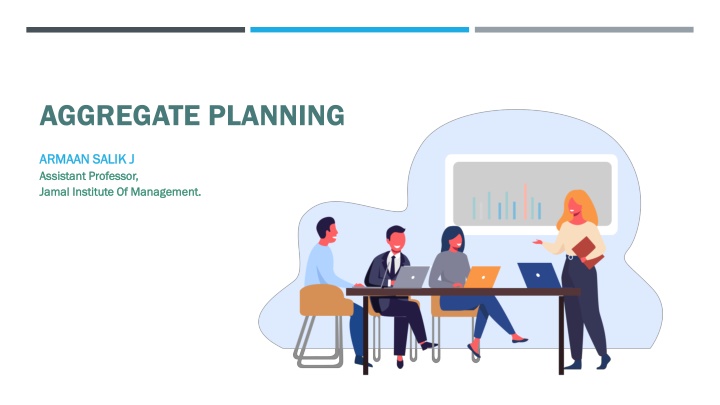
Aggregate Planning Strategies and Steps Unveiled
Dive into the world of aggregate planning and discover its definition, importance, requirements, and strategic steps for effective implementation in medium-term resource allocation scenarios to meet market demands efficiently.
Uploaded on | 0 Views
Download Presentation

Please find below an Image/Link to download the presentation.
The content on the website is provided AS IS for your information and personal use only. It may not be sold, licensed, or shared on other websites without obtaining consent from the author. If you encounter any issues during the download, it is possible that the publisher has removed the file from their server.
You are allowed to download the files provided on this website for personal or commercial use, subject to the condition that they are used lawfully. All files are the property of their respective owners.
The content on the website is provided AS IS for your information and personal use only. It may not be sold, licensed, or shared on other websites without obtaining consent from the author.
E N D
Presentation Transcript
AGGREGATE PLANNING ARMAAN ARMAAN SALIK Assistant Professor, Assistant Professor, Jamal Institute Of Management. Jamal Institute Of Management. SALIK J J
INTRODUCTION TO AGGREGATE PLANNING Definition Definition: Aggregate planning is a strategic process aimed at determining the best way to allocate resources to meet expected demand over a medium-term horizon, typically 3 to 18 months. Purpose Purpose: Balance supply and demand efficiently. Minimize overall costs related to production, labor, inventory, and distribution. Provide a roadmap for decision-making in production, hiring, and resource allocation. Key Key Example Example: A manufacturer planning quarterly production levels to avoid overstocking or shortages.
WHY AGGREGATE PLANNING IS IMPORTANT Alignment Alignment of of Supply Supply and and Demand Demand: Helps synchronize production with market needs, reducing mismatches. Optimized Optimized Resource Resource Utilization Utilization: Ensures that resources like labor, machinery, and materials are used effectively. Cost Cost Savings Savings: Minimizes waste, avoids unnecessary overtime, and reduces storage costs. Improved Improved Service Service Levels Levels: Ensures timely delivery and customer satisfaction by planning adequately for peak and low-demand periods.
REQUIREMENTS FOR AGGREGATE PLANNING Demand Demand Forecast Forecast: : Reliable and data-driven predictions for future demand based on historical trends, market analysis, and seasonality. Production Production Capacity Capacity: Analysis of the maximum output capabilities of facilities, considering regular and overtime operations. Inventory Inventory Levels Levels: : Understanding current stock levels and determining acceptable inventory limits (minimum and maximum). Cost Cost Structure Structure: : Breakdown of fixed and variable costs, including labor, raw materials, storage, and transportation. Lead Lead Times Times: : Accurate knowledge of procurement and production times to meet deadlines.
STEPS IN AGGREGATE PLANNING 1. Define 1. Define Goals Goals: Clearly outline the objectives, such as minimizing costs, maximizing resource use, or meeting service levels. 2. 2. Demand Demand Forecasting Forecasting: Use historical data, market trends, and statistical tools to predict future demand. 3. Capacity 3. Capacity Assessment Assessment: Assess the availability of workforce, equipment, and facilities. Identify bottlenecks or surplus capacity. 4. Develop 4. Develop Alternatives Alternatives: Create various production scenarios like chase strategy (adjusting production as per demand), level strategy (steady production), or hybrid methods. 5. Select 5. Select Optimal Plan Optimal Plan: Evaluate the alternatives against the objectives, considering constraints like budget, capacity, and policies. 6. Implement 6. Implement and Monitor and Monitor: Execute the chosen plan and establish KPIs (Key Performance Indicators) to monitor its effectiveness.
STRATEGIES IN AGGREGATE PLANNING 1 1. . Chase Chase Strategy Strategy: Adjusts production rates to match demand directly, minimizing inventory costs. Suitable for industries with fluctuating demand (e.g., retail or seasonal goods). Example Example: A toy manufacturer increasing production before the holiday season. 2 2. . Level Level Strategy Strategy: Maintains a consistent production rate and uses inventory to buffer demand fluctuations. Suitable for industries with stable demand or high-cost changes (e.g., automotive manufacturing). Example Example: A car manufacturer producing a fixed number of vehicles monthly. 3 3. . Hybrid Hybrid Strategy Strategy: Combines elements of both chase and level strategies to balance costs and service levels. Example Example: A clothing retailer using steady production for core items and flexible production for seasonal collections.
ADVANTAGES OF AGGREGATE PLANNING Cost Cost Efficiency Efficiency: Reduces unnecessary overtime, inventory holding costs, and hiring expenses. Resource Resource Optimization Optimization: Maximizes the utilization of workforce, machinery, and materials. Demand Demand Management Management: Aligns supply with customer needs, reducing the risk of underproduction or overproduction. Improved Improved Decision Decision- -Making Making: Provides a structured framework for strategic and operational planning. Customer Customer Satisfaction Satisfaction: Ensures consistent delivery times and product availability.
CHALLENGES IN AGGREGATE PLANNING Demand Variability Demand Variability: Forecasting inaccuracies due to sudden market changes, new competitors, or economic shifts. Resource Constraints Resource Constraints: Limited flexibility in workforce, equipment, or raw materials. Cost Pressures Cost Pressures: Balancing the costs of holding inventory, overtime, or hiring temporary labor. Coordination Issues Coordination Issues: Difficulty in integrating aggregate planning with other supply chain processes like procurement and distribution. Example Example: A manufacturer facing raw material shortages due to supplier delays, impacting their aggregate plan.
CONCLUSION Aggregate planning is vital for optimizing resources and meeting demand cost- effectively. It bridges the gap between short-term operational planning and long-term strategic goals. Despite challenges, it significantly enhances decision-making and customer satisfaction when implemented effectively.