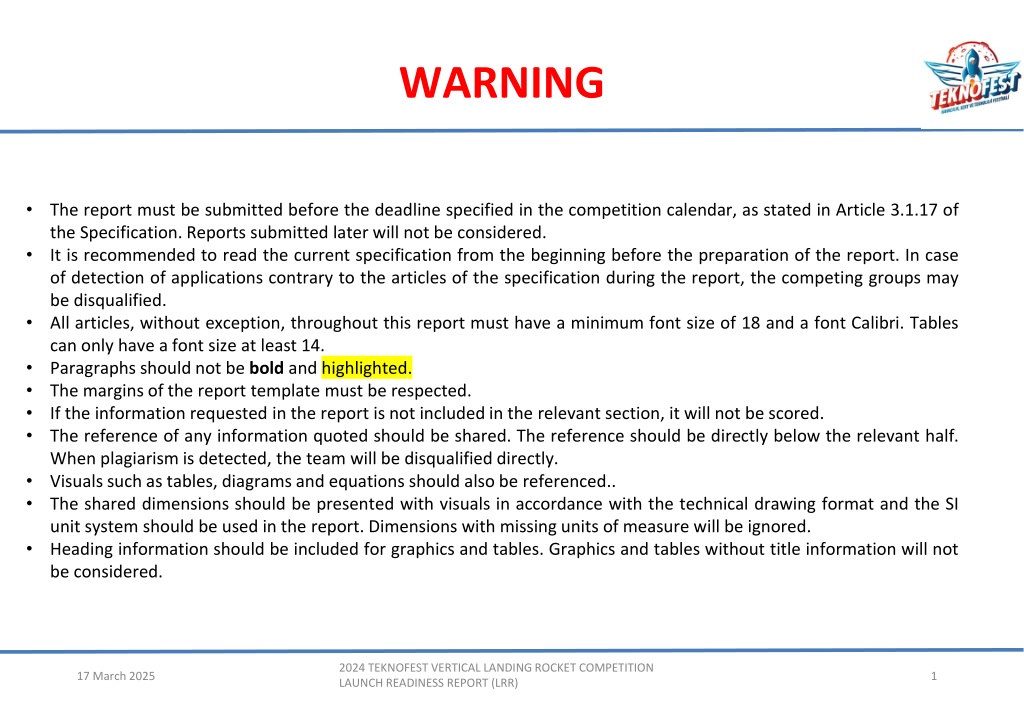
Launch Readiness Report Guidelines for Vertical Landing Rocket Competition
Ensure your Launch Readiness Report (LRR) meets the strict guidelines set forth in the competition specifications. Failure to adhere to these requirements may result in disqualification. Pay attention to details such as font sizes, margins, referencing, and use of visuals. Submit your report in PDF format before the specified deadline to avoid penalties.
Download Presentation

Please find below an Image/Link to download the presentation.
The content on the website is provided AS IS for your information and personal use only. It may not be sold, licensed, or shared on other websites without obtaining consent from the author. Download presentation by click this link. If you encounter any issues during the download, it is possible that the publisher has removed the file from their server.
E N D
Presentation Transcript
WARNING The report must be submitted before the deadline specified in the competition calendar, as stated in Article 3.1.17 of the Specification.Reports submitted later will not be considered. It is recommended to read the current specification from the beginning before the preparation of the report. In case of detection of applications contrary to the articles of the specification during the report, the competing groups may be disqualified. All articles, without exception, throughout this report must have a minimum font size of 18 and a font Calibri. Tables can only have a font size at least 14. Paragraphs should not be bold and highlighted. The margins of the report template must be respected. If the information requested in the report is not included in the relevant section, it will not be scored. The reference of any information quoted should be shared. The reference should be directly below the relevant half. When plagiarism is detected, the team will be disqualified directly. Visuals such as tables, diagrams and equations should also be referenced.. The shared dimensions should be presented with visuals in accordance with the technical drawing format and the SI unit system should be used in the report. Dimensions with missing units of measure will be ignored. Heading information should be included for graphics and tables. Graphics and tables without title information will not be considered. 2024 TEKNOFEST VERTICAL LANDING ROCKET COMPETITION LAUNCH READINESS REPORT (LRR) 17 March 2025 1
WARNING The information given in the presentation should be understandable. Tables and images should be used where needed. The font of the final element selected as a result of the comparison should be dark (bold) and the font color should be green. Information requested more than once throughout the report should be explained independently on each requested page. Information that cannot be found in the relevant place will not be scored, even if it has been explained before. The name of the documents (including tables) requested or allowed to be given in the Annex should be included in the relevant sheet and submitted together with the LRR and in full. The originals of the tables to be presented in LRR or in its ANNEX should be shared instead of screenshots. The texts to be presented in LRR or its Appendix, formula, equation (Powerpoint's formula and equation adder should be used), correlation etc. should not be presented as screenshots. There should be a logo on every page of the report and the titles should never be changed. The page in the template shared by the Competition Committee should not be added to a new and/or different page. The report must be uploaded in PDF format. The report submitted in a format other than PDF will not be evaluated. *.pptx and *.ppt submissions will not be considered. Please upload a PDF file to the system. Even if it is not specifically stated in the above articles, information that is not given in accordance with the CDR format will not be evaluated. All of the text (including the specifications), sample images and boxes that guide the contestants on the slides shall be deleted. Warning pages shall be deleted after reading and shall not be shared with the report 2024 TEKNOFEST VERTICAL LANDING ROCKET COMPETITION LAUNCH READINESS REPORT (LRR) 17 March 2025 2
Team Logo TEKNOFEST 2024 Vertical Landing Rocket Launch Readiness Report (LRR) Presentation Team Name 2024 TEKNOFEST VERTICAL LANDING ROCKET COMPETITION LAUNCH READINESS REPORT (LRR) 17 March 2025 3 WARNING: : No format other than this Format will be used. It is necessary to put the produced information on the mirrors in its original form (no screen shots), to have good resolution and legibility, and to prepare a professional presentation. Hand drawing should not be done. The numerical data presented should be shown with their units.
Team Logo Team Structure Team members' information shall be filled as shown in the table below. This section shall not exceed 2 pages. Staff Name University-Institution Name / Department / Class Mission Country Ali Y ld r m University / Mechanical Engine. / 4. Class Team Lead, Mechanic Ahmet im ek Mehmet S nmez Ay e Durmu Teams will be disqualified if the information in this section and the rules in Article 3.1.4, 3.1.5, 3.1.6, 3.1.7, 3.1.8, 3.1.9, 3.1.12, 3.1.14, 3.1.18, 3.1.19, 3.1.20, 3.1.21, 3.1.22, 3.1.23, 3.1.24, 3.1.25 and 3.1.26 are found to be violated. 2024 TEKNOFEST VERTICAL LANDING ROCKET COMPETITION LAUNCH READINESS REPORT (LRR) 17 March 2025 4
Team Logo General Information Predicted Flight Data and Analysis General Information About the Competition Rocket Value Comment Value Comment Top Speed(m/s): Altitude(m): Length (meter): Diameter(meter): StaticMargin : Rocket Total Mass: Rocket Moment of Inertia PropulsionSystem Matrix: Value Comment Gas Tank Volume: Gas Tank Filling Pressure: Number of Nozzle: Thrust of a Nozzle: Mach Number of Nozzle: Nozzle inlet Pressure: Total Mass Flow: Guidance Control System Comment Value/Definition Moment Vector around Center of Gravity (Cg): Teams should place general information about the rocket in the table here. It is recommended to complete this section at the end of the LRR report. Name of Method Elements Thrust Vectoring Fixed Nozzle Other (Explain) PropulsionSystem Reaction Control System (If Equipped) 2024 TEKNOFEST VERTICAL LANDING ROCKET COMPETITION LAUNCH READINESS REPORT (LRR) 17 March 2025 5
Team Logo Competition Rocket Overview The general view of the competition rocket produced in this section shall be given. The main units/modules that make up the rocket system must be shown on the photograph. 2024 TEKNOFEST VERTICAL LANDING ROCKET COMPETITION LAUNCH READINESS REPORT (LRR) 17 March 2025 6
General Design Team Logo The image of the rocket design must be submitted as a screenshot. Photograph of the manufactured rocket must be attached. The image shall include the static margin and the height and length information of each functional part of the rocket. This section shall not exceed 2 pages. The most up-to-date status of the rocket shall be presented. In this section, the requirements 4.3.1, 4.3.2, 4.3.3, 4.3.5 and 4.3.7 in the specification will be checked. 2024 TEKNOFEST VERTICAL LANDING ROCKET COMPETITION LAUNCH READINESS REPORT (LRR) 17 March 2025 7
Team Logo Operation Concept(CONOPS) The main points to be considered in the process before launchingthe rocket are as follows : 1. Connecting the Rocket to Crane There must be U Bolt sent by T B TAK SAGE on the rocket. The rocket will hang from this U Bolt to the crane. The U Bolt must be in line with the center of gravity and connected to the main frame. Vehicle hung with U Bolt must stand perpendicular to the ground. 2. Connecting the Safe Disconnection Connector A safe disconnection connector will be available near the area where the U bolt attaches to the rocket body (maximum 5 cm away). Note: If the safe disconnection connector is far from the center of gravity and the direction through the U Bolt, it may cause a disruptive effect on the rocket when it is disconnected from the crane. It is therefore recommended that the safe disconnection connector be close to the U Bolt. After the rocket is suspended from the crane, the male side of the safe disconnection connector on the rocket will be connected to the female side on the crane. The purpose of this connector is to prevent the cold gas propulsion system from opening before the rocket leaves the crane. 3. ApplyingElectrical Power to the Rocket With the electric switch located in the body of the rocket, electrical energy will be supplied to the vehicle from the battery. In this case, the operation of all components will be ensured except the cold gas propulsion system. The male and female side of the safe disconnection connector will be separated from each other when the electric motor driven crane hook is opened. In this way, the cold gas propulsion system will be activated when the rocket leaves the crane. In this section, the requirements 4.3.3 and 4.3.4 in the specification will be checked. 2024 TEKNOFEST VERTICAL LANDING ROCKET COMPETITION LAUNCH READINESS REPORT (LRR) 17 March 2025 8
Operation Concept (CONOPS) Team Logo The operational concept is an important stage of the launch readiness phase. Therefore, the competitors are required to plan their processes, task distribution and emergency scenarios in detail. In this context: 1. Pre-launching process table, 2. Operation process table, 3. Post-landing process table, 4. Reserve parts inventory table, 5. Task distribution table should be prepared. This part shall not exceed 7 pages. In this section, the requirements 4.3.3 and 4.3.4 in the specification will be checked. 2024 TEKNOFEST VERTICAL LANDING ROCKET COMPETITION LAUNCH READINESS REPORT (LRR) 17 March 2025 9
Operation Concept (CONOPS) Team Logo The processes in the pre-launching readiness (assembly, filling, control, testing, etc.) shall be specified in detail in the Pre-launching Process Table, respectively. Pre-launching Process Table Process Sequence Process Code Staff Process Description Risk factors 1 A001 Name Surname (more than one if any) Description Problems that may occur 2 A002 Name Surname (more than one if any) Description Problems that may occur 3 A003 Name Surname (more than one if any) Description Problems that may occur 4 A004 Name Surname (more than one if any) Description Problems that may occur 5 A005 Name Surname (more than one if any) Description Problems that may occur 2024 TEKNOFEST VERTICAL LANDING ROCKET COMPETITION LAUNCH READINESS REPORT (LRR) 17 March 2025 10
Operation Concept (CONOPS) Team Logo The process from loading the rocket to the crane and landing on the ground shall be detailed in the Operation Process Table. Operation Process Table Process Sequence Process Code Staff Process Descriptio n Altitude[m] Risk factors 1 B001 Name Surname (more than one if any) Description Problems that may occur 0-30 2 B002 Name Surname (more than one if any) Description Problems that may occur 30-25 3 B003 Name Surname (more than one if any) Description Problems that may occur 25-5 4 B004 Name Surname (more than one if any) Description Problems that may occur 5-1 5 B005 Name Surname (more than one if any) Description Problems that may occur 1-0 2024 TEKNOFEST VERTICAL LANDING ROCKET COMPETITION LAUNCH READINESS REPORT (LRR) 17 March 2025 11
Operation Concept (CONOPS) Team Logo The processes that will take place after the landing of the rocket (such as control, damage detection, reserve part replacement, functionality control) shall be specified in the Post-Landing Process Table. Post-Landing Process Table Process Sequence Process Code Staff Process Description Risk factors 1 C001 Name Surname (more than one if any) Description Problems that may occur 2 C002 Name Surname (more than one if any) Description Problems that may occur 3 C003 Name Surname (more than one if any) Description Problems that may occur 4 C004 Name Surname (more than one if any) Description Problems that may occur 5 C005 Name Surname (more than one if any) Description Problems that may occur 2024 TEKNOFEST VERTICAL LANDING ROCKET COMPETITION LAUNCH READINESS REPORT (LRR) 17 March 2025 12
Operation Concept (CONOPS) Team Logo The equipment to be brought to the field for the purpose of replacing parts when necessary during the preparation for launching shallbe specified in the Reserve Parts Inventory Table. Reserve Parts Inventory Table Reserve Part Code Reserve Part Name Piece The process code of the risk factor that will cause the need for reserve parts YP001 A001, B002 etc. YP002 Problems that may occur YP003 Problems that may occur YP004 Problems that may occur YP005 Problems that may occur 2024 TEKNOFEST VERTICAL LANDING ROCKET COMPETITION LAUNCH READINESS REPORT (LRR) 17 March 2025 13
Operation Concept (CONOPS) Team Logo In order to determine the contributions and responsibilities of the people who will take part in the processes and tasks defined within the scope of the operation concept, the Task Distribution Table shall be prepared in detail. Care shall be taken to ensure that the distribution of tasks is balanced and that people who have a good command of the design are assigned to the relevant issues. Task Distribution Table Staff Process codes in charge Number of processes in charge The Role of the staff in the Design Name Surname Name Surname Name Surname Name Surname Name Surname 2024 TEKNOFEST VERTICAL LANDING ROCKET COMPETITION LAUNCH READINESS REPORT (LRR) 17 March 2025 14
Team Logo Rocket Subsystem Details In this section, the requirements 3.2.3, 3.2.4, 3.2.6, 3.2.7, 3.2.8, 3.2.9, 3.2.10, 3.2.11, 3.2.13, 3.2.14, 3.2.15, 3.2.16, 3.2.17, 3.2.18, 3.2.19, 3.2.20, 3.2.21, 3.2.24, 3.2.26, 3.3.3, 3.3.4, 3.3.5, 3.3.6, 4.3.1, 4.3.5, 4.3.6, and 4.3.7 in the specification will be checked. 2024 TEKNOFEST VERTICAL LANDING ROCKET COMPETITION LAUNCH READINESS REPORT (LRR) 17 March 2025 15
Team Logo Pneumatic System Design Pneumatic Circuit Diagram Pneumatic circuit diagram on this page with the following information: a. Inner and outer diameters of piping with operating conditions (pressure, temperature and flow rate) b. Connection dimensions of interconnection components and brand/model information of used throttling element(s) and working conditions c. Nozzle element(s) used, together with the design conditions (Mach number, total inlet pressure, throat diameter) must be summary. This section shall not exceed 2 page In this section, the requirements 3.2.1, 3.2.3, 3.2.4, 3.2.8, 3.2.11, 3.2.14, 3.2.20, 3.3.3, 3.3.4, 3.3.6, 4.3.1, 4.3.5, 4.3.6, and 4.3.7 in the specification will be checked. 2024 TEKNOFEST VERTICAL LANDING ROCKET COMPETITION LAUNCH READINESS REPORT (LRR) 17 March 2025 16
Team Logo Pneumatic System Design- Detail The current version of your pneumatic design shall be introduced during the launching readiness. In this context, the pneumatic system update table shall be filled. The pneumatic system update table shall not exceed 7 pages. Pneumatic system update tablosu Critical Design Current Design Description of the change made 2024 TEKNOFEST VERTICAL LANDING ROCKET COMPETITION LAUNCH READINESS REPORT (LRR) 17 March 2025 17
Team Logo Pneumatic System Design- Detail All products used in the current pneumatic system design and supplied from the market should be introduced. In this context, the Pneumatic System Product Bill of Material shall be filled. The catalog (or equivalent source) containing the technical specifications of each product shall be shared in PDF format as an attachment. Catalogs shall be named in the format Teamname_Productcode_katalog.pdf . The information requested in the pneumatic system bill of materials table must be marked in the catalog documents. This section shall not exceed 5 pages. Pneumatic system bill of materials . Maximum Operation Temperature [oC] Working Pressure [bar] Working Tempera ture [oC] Flow Rate [g/s] Inlet Diamet er Outlet Diamet er Maximum Operation Pressure [bar] SAMPLE Product Name Product Code Unit Mass Piece PN001 PN002 PN003 2024 TEKNOFEST VERTICAL LANDING ROCKET COMPETITION LAUNCH READINESS REPORT (LRR) 17 March 2025 18
Team Logo Pneumatic System Tests Preliminary tests of the assembled rocket must be done before the test shots. These tests are listed as follows, respectively. 1. Leakage Test 2. Main thrust functionality testing 3. Secondary systems functionality tests (if any) This part shall not exceed 4 pages for each test to be performed. In case the test video sizes are high, they should be uploaded to youtube.com and the links shall be added to the relevant pages. In this section, the requirements 3.2.2, 4.3.1, 4.3.5, 4.3.6 and 4.3.7 in the specificationwill be checked. 2024 TEKNOFEST VERTICAL LANDING ROCKET COMPETITION LAUNCH READINESS REPORT (LRR) 17 March 2025 19
Team Logo Pneumatic System Tests Leakage Test: The safety of the design must be tested prior to launching. After the rocket is fixed with obstacles so that it does not move, the tank shall be filled and the leakage situation under pressure shall be examined for 1 hour after pressurization. o Test procedure shall be explained. o The people taking part in the test and the distribution of tasks shall be specified in a table. o The first 10 minutes of a test process shall be recorded a video the moment of filling. o The success criterion is that the tank pressure does not fall below 95% of the filling pressure for 1 hour. Whether or not the success criterion is met as a result of the test shall be indicated with the measurement results. o The test shall be repeated 5 times. In this section, the requirements 3.2.2, 4.3.1, 4.3.5, 4.3.6 and 4.3.7 in the specification will be checked. 2024 TEKNOFEST VERTICAL LANDING ROCKET COMPETITION LAUNCH READINESS REPORT (LRR) 17 March 2025 20
Team Logo Pneumatic System Tests Main Propulsion Functionality Test : The functionality of the main propulsion system shall be tested before launching. For this, after the design is fixed with obstacles so that it does not move, the tank shall be filled and the main propulsion system shall be started. This test can be performed after the leak test. o The test procedure shall be explained. o The people taking part in the test and the distribution of tasks shall be indicated in a table. o The success criterion is that the propulsion systems work in accordance with the design. As a result of the test, whether the success criterion is met or not, the measurement results (if it is not possible to take a measurement, by video recording) shall be stated. o The test shall be repeated 5 times. In this section, the requirements 3.2.2, 4.3.1, 4.3.5, 4.3.6 and 4.3.7 in the specification will be checked. 2024 TEKNOFEST VERTICAL LANDING ROCKET COMPETITION LAUNCH READINESS REPORT (LRR) 17 March 2025 21
Team Logo Pneumatic System Tests Secondary Systems Functionality Test: Functionality of secondary systems other than the main propulsion system (if used, reaction control systems etc.) should be tested before launching. For this, after the design is fixed with obstacles so that it does not move, the tank shall be filled and the related systems shall be operated. Teams with multiple secondary systems are required to repeat the same test for all systems o The test procedure shall be explained. o The people taking part in the test and the distribution of tasks shall be indicated in a table. o The success criterion is that the propulsion systems work in accordance with the design. As a result of the test, whether the success criterion is met or not, the measurement results (if it is not possible to take a measurement, by video recording) shall be stated. o The test shall be repeated 5 times. In this section, the requirements 3.2.2, 4.3.1, 4.3.5, 4.3.6 and 4.3.7 in the specification will be checked. 2024 TEKNOFEST VERTICAL LANDING ROCKET COMPETITION LAUNCH READINESS REPORT (LRR) 17 March 2025 22
Team Logo Pneumatic System Tests Design Functionality Test: It is the flight test conducted where the functionality of the main propulsion system is tested. The main propulsion system will be operated by hangingthe prototype vehicle from the U Bolt with a rope. o The test procedure shall be explained. o The people taking part in the test and the distribution of tasks shall be indicated in a table. o The success criterion is that the propulsion systems work in accordance with the design. As a result of the test, whether the success criterion is met or not, the measurement results (if it is not possible to take a measurement, by video recording) shall be stated. o The test shall be repeated 5 times. In this section, the requirements 3.2.2, 4.3.1, 4.3.5, 4.3.6 and 4.3.7 in the specificationwill be checked. 2024 TEKNOFEST VERTICAL LANDING ROCKET COMPETITION LAUNCH READINESS REPORT (LRR) 17 March 2025 23
Team Logo Mechanical System Tests Structural Integrity Test : The structural integrity of aircraft shall not be impaired during the landing process in case of possible risk situations. Structural integrity testing is required to verify this requirement. The final vehicle must be released from a height of 0.4 meters. The rope can be attached to the rocket at the center of mass axis. Tests can be performed with a comparable chassis with the same design concept and the same mechanical properties (same weight). It is not necessary to have tanks and avionic systems on this equivalent chassis. o The test procedure shall be explained. o The people taking part in the test and the distribution of tasks shall be indicated in a table. o The vehicle should be weighed before the test and its image shall be shared. o Success criteria are preservation of vehicle integrity, no deformations and no separation of connections. Whether or not the success criterion is met as a result of the test shall be recorded with a camera (video). o The test shall be repeated at least 2 times. This section shall not exceed 5 pages In this section, the requirements 3.2.2, 4.3.1, 4.3.5, 4.3.6 and 4.3.7 in the specification will be checked. 2024 TEKNOFEST VERTICAL LANDING ROCKET COMPETITION LAUNCH READINESS REPORT (LRR) 17 March 2025 24
Guidance Navigation Control Avionics Team Logo Details on the discretization of the final autopilot system (Control system (autopilot) method, sampling time, discretization method, etc.) shall be given (Max 1 page). The responses of the continuous time and discrete time autopilot designs under the test signal (0.1 -30 Hz Chirp Signal) shall be compared and given in graphs(Max 1 page). It is necessary to compare the response of the autopilot structure on the hardware with the response in the simulation at the split time (Max 1 page). Submitting a single photograph of the avionics equipment in detail to show the system in a numbered and named format (Max 1 page) Giving the Hardware in the Loop (HWIL) results in detail: Teams' reference trajectory-actual trajectory, velocity-time, acceleration-time, altitude-time, Euler angles-time, control inputs (thrust forces), PQR-time graph etc. They are required to share the charts and discuss using them. (Max 5 pages) A working video (in a single mp4 format) showing the behavior of the actuators during the control inputs (thrust time graphs) produced in HWIL shall be provided. NOTE: It is essential to use the final software and hardware designed in HWIL tests and to be used in shooting. In this section, the requirements 3.2.2, 4.3.1, 4.3.4, 4.3.5, 4.3.6 and 4.3.7 in the specificationwill be checked. 2024 TEKNOFEST VERTICAL LANDING ROCKET COMPETITION LAUNCH READINESS REPORT (LRR) 25 17 March 2025
Team Logo Mass Budget All parts of the rocket shall be given on the page in accordance with the example in the bill of material logic. Mass Budget Table Bill of Material Mass (gram) Name of Subsystem Component Material Quantity Subsystem 1 Subsystem 2 Subsystem 3 Total mass is x.xx kg In this section, the requirement 4.3.1 in the specification will be checked. 2024 TEKNOFEST VERTICAL LANDING ROCKET COMPETITION LAUNCH READINESS REPORT (LRR) 17 March 2025 26
Team Logo LRR Point Table Activity Point Operation Concept : Pre-launching process table, Operation process table, Post-landing process table, Reserve parts inventory table, Task distribution table 15 Pneumatic Circuit Diagram Pneumatic System Bill of Material Leak test Main thrust functionality testing Secondary system functionality tests Design functionality testing Structural Integrity Test Guidance Navigation Control Avionics 2 3 7 7 7 9 25 25 100 Total 2024 TEKNOFEST VERTICAL LANDING ROCKET COMPETITION LAUNCH READINESS REPORT (LRR) 17 March 2025 27