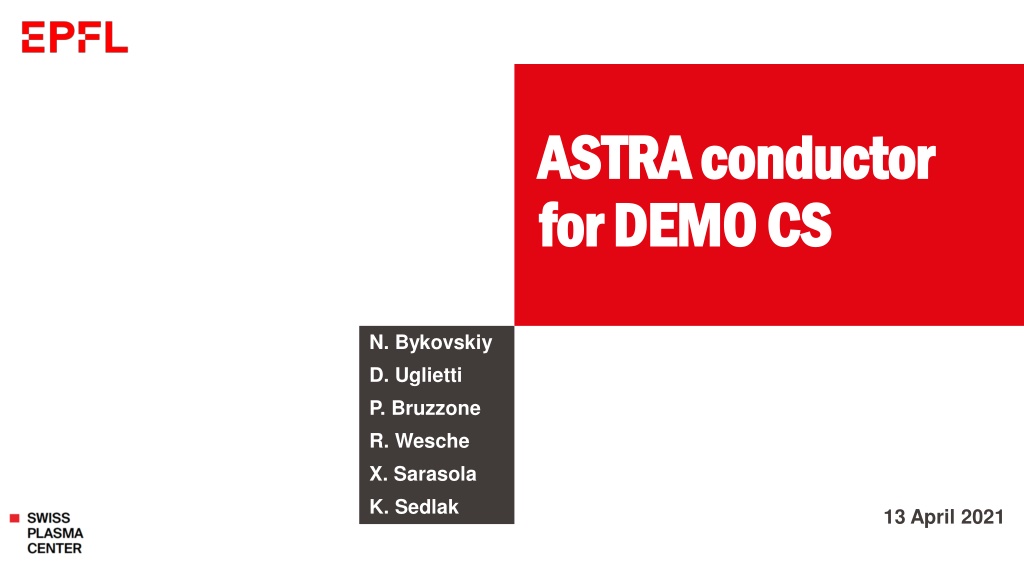
Innovative Design Solutions for ASTRA Conductor
Explore the innovative design considerations and proposed solutions for the ASTRA conductor system, aimed at addressing mechanical issues, reducing AC losses, and improving cooling conditions. Key aspects include simplified strand soldering, compression along the c-axis, and minimizing cyclic load degradation. The proposed design solutions focus on short transition of strands, reduced cable thickness, and exploring different filling options for improved performance. Additionally, a sub-scale ASTRA sample for quench experiment is highlighted for enhanced DC field operation and early quench detection using MgB2wire and superconducting wire technologies.
Download Presentation

Please find below an Image/Link to download the presentation.
The content on the website is provided AS IS for your information and personal use only. It may not be sold, licensed, or shared on other websites without obtaining consent from the author. If you encounter any issues during the download, it is possible that the publisher has removed the file from their server.
You are allowed to download the files provided on this website for personal or commercial use, subject to the condition that they are used lawfully. All files are the property of their respective owners.
The content on the website is provided AS IS for your information and personal use only. It may not be sold, licensed, or shared on other websites without obtaining consent from the author.
E N D
Presentation Transcript
ASTRA conductor ASTRA conductor for DEMO CS for DEMO CS N. Bykovskiy D. Uglietti P. Bruzzone R. Wesche X. Sarasola K. Sedlak 13 April 2021
Design Design considerations considerations 2 2 N. Bykovskiy Mechanical issue with unsupported strand section Current Field Strand design: Rectangular profile, rounded corners Open soldering channel Non-twisted soldered tapes Cable design: Roebel cabling Jacket pre-compression Separate cooling channel Force ASTRA (Aligned Stacks Transposed in Roebel Arrangement) conductor features: ASTRA conductor for DEMO CS Simplified and well controlled strand soldering Favorable direction of transverse load (compression along c-axis) Aligned stacks, thus less tapes needed (~50% in central modules, for details see last slide) Reduced AC losses (less strands needed) Conduction cooling conditions to address fatigue issues of DEMO CS Likely, the key aspects to avoid cyclic load degradation
Proposed design solutions Proposed design solutions 3 3 N. Bykovskiy 1. 2. Short transition of strands between the cable layers Impregnation of the cable space reduced cable thickness (no core), min bending radius <1.5 m 1. 2. 3. 4. Profile annealing Strand pre-shape (easy bending) Strand soldering Strand cabling (hard bending) ASTRA conductor for DEMO CS * Tape packing before or after 2.
Proposed design solutions Proposed design solutions 4 4 N. Bykovskiy 1. 2. Short transition of strands between the cable layers Impregnation of the cable space reduced cable thickness (no core), min bending radius <1.5 m Related study from 1975 Various filling options to be investigated (only the mechanical reason): Glycerin + water (aiming at reduced thermal expansion) Paraffin wax (melting point ~50oC) Nitrogen? https://doi.org/10.1016/0011-2275(75)90034-X ASTRA conductor for DEMO CS LN2 first trials In-field test Forced flow helium Liquid impregnation
Sub Sub- -scale ASTRA sample for quench experiment scale ASTRA sample for quench experiment 5 5 N. Bykovskiy QE sample features: Operation in parallel DC field Conduction cooling Electrically insulated and thermally coupled MgB2wire in highly resistive matrix for early quench detection Co-wound SC wire vs fiber optics: Cheaper, simplified and more robust instrumentation Location of hot-spot can not be identified ASTRA conductor for DEMO CS Co-wound SC wire vs voltage taps: Increased sensitivity of voltage detection (~100 times at low T) Reparability is the main issue (similar to co-wound voltage taps)
Action items towards performance demonstration Action items towards performance demonstration 6 6 N. Bykovskiy Time and amount of tape needed Liquid Short transition of strands ~4 months ~10 m ~2 months ~20 m impregnation ~10 months ~300 m Material procurement SST 3.3 mm tapes: completed Copper profiles: small (required) amount ordered Cooling channel: follow-up QE sample Protection copper: TBD Steel and copper components: TBD Test Long-length strand soldering Conduction cooling Conductor terminations Integration and instrumentation SULTAN sample Cabling New QE sample ~6 months ~80 m ASTRA conductor for DEMO CS Conductor performance assessment SST tapes characterization Discussion
DEMO CS coils: tapes needed for ASTRA conductor DEMO CS coils: tapes needed for ASTRA conductor 7 7 N. Bykovskiy 3.3 mm SST tapes Dashed lines: tapes aligned along z-axis Solid lines: 5 deg mismatch with z-axis ASTRA conductor for DEMO CS ~330 tapes (SST 3.3 mm) needed for the operation in perpendicular peak field CS module CS3L CS2L CS1 CS2U CS3U Most demanding operating conditions PREMAG: 14.66 T / 70.1o EOF: 12.59 T / 70.1o PREMAG: 18.14 T / 83.7o EOF: 13.16 T / 70.3o PREMAG: 15.03 T / 70.2o