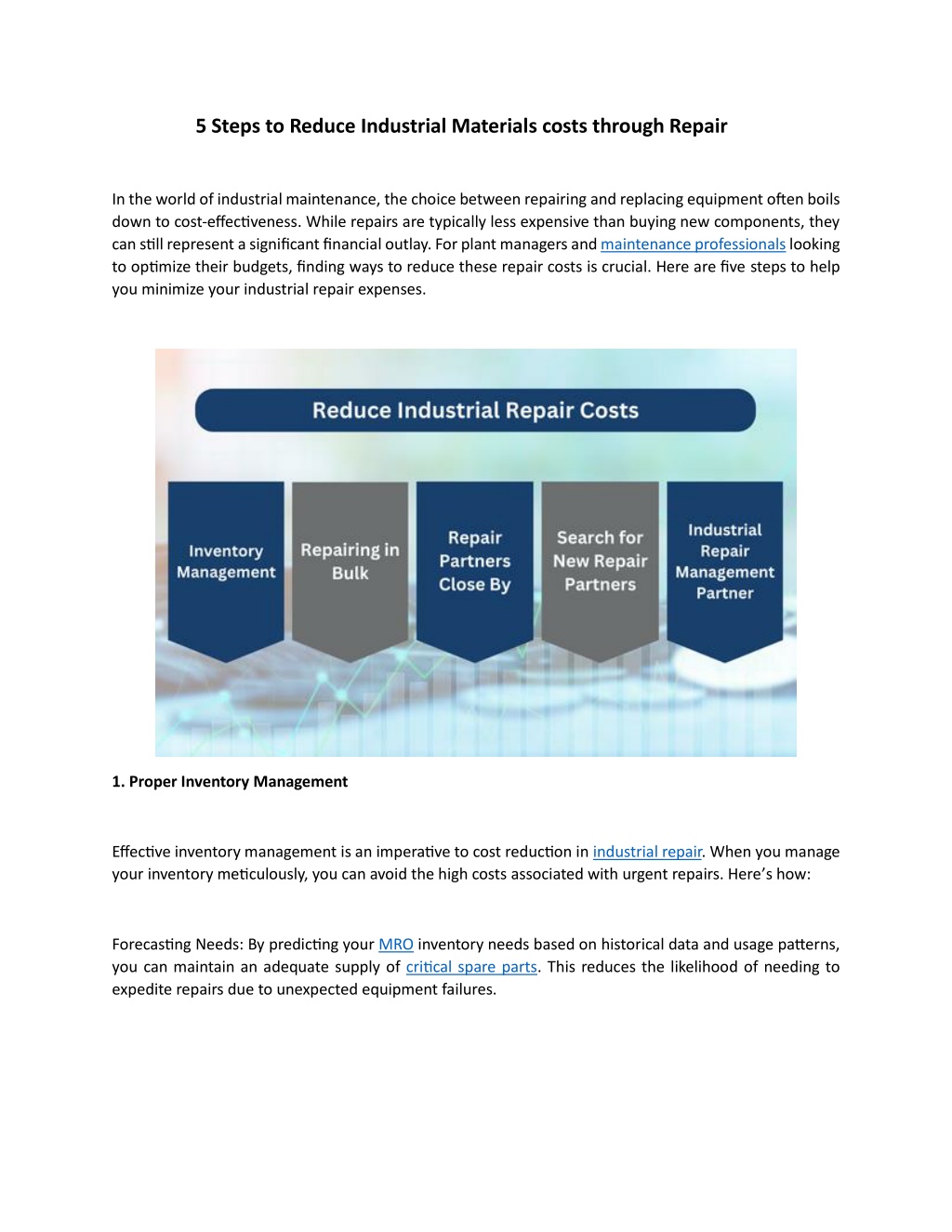
5 Steps to Reduce Industrial Materials costs through Repair
Optimize your maintenance budget with these five strategies to reduce industrial repair costs: effective inventory management, bulk repairs, local repair partners, exploring new repair providers, and partnering with an industrial repair management ex
Download Presentation

Please find below an Image/Link to download the presentation.
The content on the website is provided AS IS for your information and personal use only. It may not be sold, licensed, or shared on other websites without obtaining consent from the author. If you encounter any issues during the download, it is possible that the publisher has removed the file from their server.
You are allowed to download the files provided on this website for personal or commercial use, subject to the condition that they are used lawfully. All files are the property of their respective owners.
The content on the website is provided AS IS for your information and personal use only. It may not be sold, licensed, or shared on other websites without obtaining consent from the author.
E N D
Presentation Transcript
5 Steps to Reduce Industrial Materials costs through Repair In the world of industrial maintenance, the choice between repairing and replacing equipment often boils down to cost-effectiveness. While repairs are typically less expensive than buying new components, they can still represent a significant financial outlay. For plant managers and maintenance professionals looking to optimize their budgets, finding ways to reduce these repair costs is crucial. Here are five steps to help you minimize your industrial repair expenses. 1. Proper Inventory Management Effective inventory management is an imperative to cost reduction in industrial repair. When you manage your inventory meticulously, you can avoid the high costs associated with urgent repairs. Here s how: Forecasting Needs: By predicting your MRO inventory needs based on historical data and usage patterns, you can maintain an adequate supply of critical spare parts. This reduces the likelihood of needing to expedite repairs due to unexpected equipment failures.
Avoiding Stockouts: Keeping essential parts in stock prevents production delays and the costly rush orders that come with needing repairs done immediately. Rotating Stock: Regularly use and inspect your inventory to ensure that parts don t become obsolete or degraded over time. Inventory Value Reduction: Having repaired spares in inventory vs new spares helps reduce total value of inventory and a positive impact on your company s balance sheet. Proper inventory management not only saves on repair costs but also ensures smooth and uninterrupted operations. 2. Repairing in Bulk Bulk repairs can lead to significant cost savings. When you consolidate multiple repair needs, you gain leverage to negotiate better terms and pricing with your repair service providers. Here s why bulk repairs are beneficial: Volume Discounts: Many repair shops offer discounts for bulk orders. By combining multiple repair jobs, you can reduce the cost per unit significantly. Efficiency Gains: Repairing in bulk allows for more efficient use of labor and resources, both for your team and the repair shop, which can translate into lower costs. Reduced Logistics Costs: Sending multiple parts for repair in one shipment can decrease transportation expenses.
Strategically planning your repair schedule to bundle similar needs together can yield considerable financial benefits. 3. Finding Repair Partners Close By Location matters when it comes to repair services. Partnering with repair facilities close to your plant can help you avoid high shipping costs and reduce turnaround times. Here s how proximity can save you money: Lower Shipping Costs: Shipping heavy, large, or bulky equipment across long distances can be expensive. Local repair shops eliminate or significantly reduce these costs. Faster Service: Local partners can often provide quicker repair services due to reduced shipping times, minimizing the downtime of your equipment. Convenient Communication: Proximity facilitates easier and more frequent communication, ensuring that any issues can be addressed promptly and effectively. Establishing relationships with nearby repair facilities can streamline your maintenance processes and reduce costs associated with logistics. 4. Always Search for New Repair Partners Diversifying your network of repair partners is key to finding competitive pricing and quality service. Regularly seeking quotes from multiple repair providers ensures you are getting the best deal available. Consider these steps:
Competitive Quotes: By obtaining quotes from several repair shops, you can compare prices and services to choose the best option for your budget. Evaluating Quality: Different providers offer varying levels of quality and service. Regularly evaluating new partners ensures you are not only cost-effective but also receiving reliable repairs. Flexibility and Options: Having a broader network gives you more options to choose from, especially in urgent situations where your primary repair partner may be unavailable or too costly. Maintaining a diverse and competitive pool of repair partners keeps you informed about market rates and service capabilities. 5. Working with an Industrial Repair Management Partner Industrial repair management partners can be a game-changer in managing and reducing repair costs. These partners leverage their extensive networks and collective buying power to secure preferred pricing on repairs. Here s how they can help: Bulk Leverage: Repair management partners often manage large volumes of repairs across multiple clients, allowing them to negotiate better rates with repair shops. Vendor Networks: They continuously evaluate and engage with a broad network of repair providers, ensuring access to the best prices and services. Simplified Process: These partners handle the complexities of finding and negotiating with repair vendors, freeing up your team to focus on core operations.
By working with an industrial repair management partner, you can take advantage of their expertise and buying power to achieve significant cost savings. Reducing industrial repair costs requires strategic planning and a proactive approach. Proper inventory management, bulk repairs, choosing local repair partners, continually searching for new vendors, and partnering with an industrial repair management expert are all effective strategies to cut costs. To learn more about how an industrial repair management partner can help you lower your repair costs and take the workload of repair off of your shoulders, contact info@ahgroupna.com. AH Group offers comprehensive MRO services centered around critical spare parts management and repair and warranty management, along with inventory management, vendor management, and performance tracking. Using our vast network of over 3,000 repair partners, AH Group ensures MRO cost savings and efficient MRO management tailored to each client s needs. Read More : https://ahgroupna.com/5-steps-to-reduce-industrial-materials-costs-through-repair/