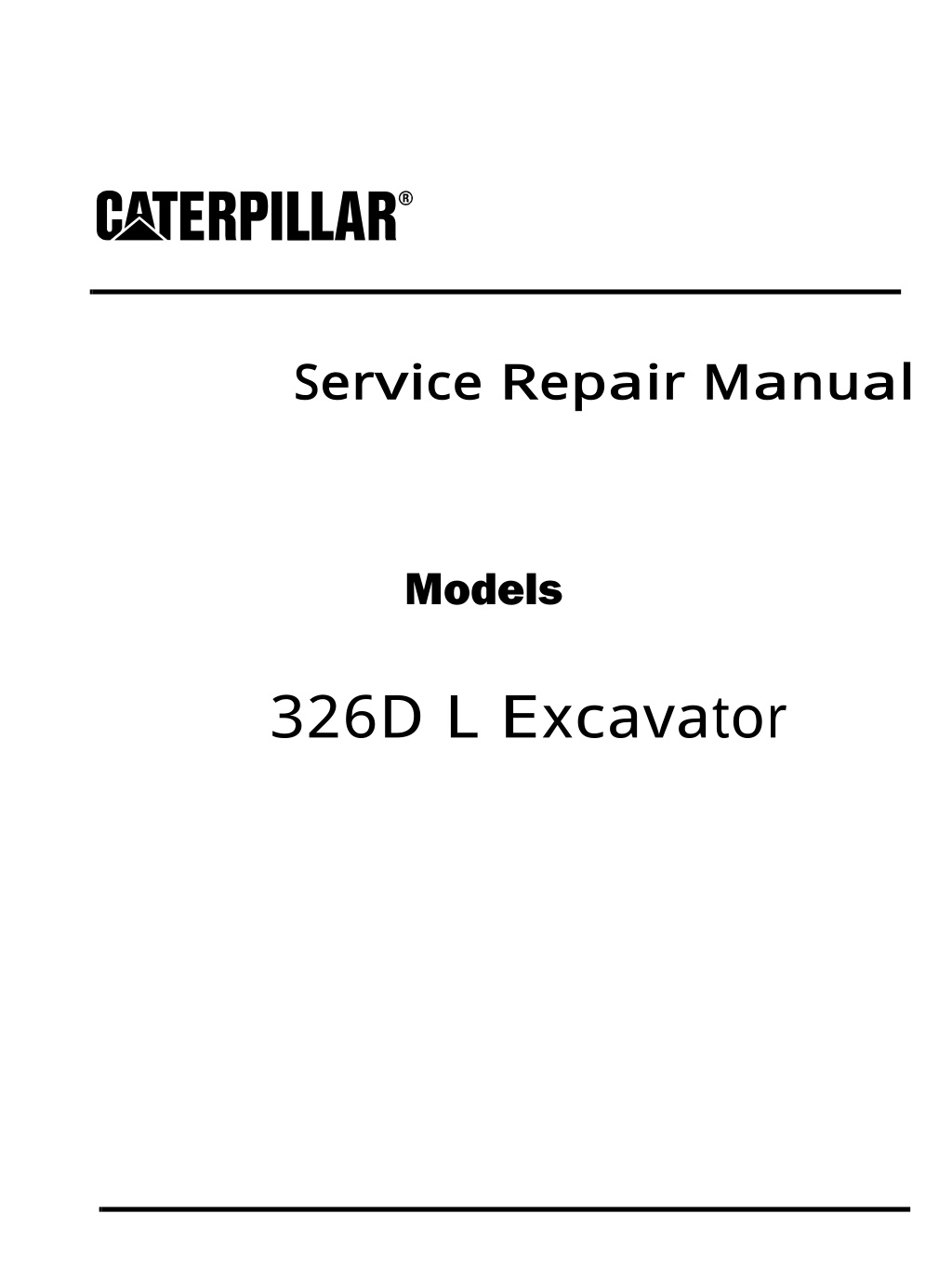
Caterpillar Cat 326D L Excavator (Prefix PJM) Service Repair Manual Instant Download
Please open the website below to get the complete manualnn// n
Download Presentation

Please find below an Image/Link to download the presentation.
The content on the website is provided AS IS for your information and personal use only. It may not be sold, licensed, or shared on other websites without obtaining consent from the author. Download presentation by click this link. If you encounter any issues during the download, it is possible that the publisher has removed the file from their server.
E N D
Presentation Transcript
Service Repair Manual Models 326DL Excavator
326D L Excavator PJM00001-UP (MACHINE) POWERED BY C7 Engine(SEBP624... 1/7 Shutdown SIS Previous Screen Product: EXCAVATOR Model: 326D L EXCAVATOR PJM Configuration: 326D L Excavator PJM00001-UP (MACHINE) POWERED BY C7 Engine Disassembly and Assembly 324D, 325D, 326D and 329D Excavators and 329D MHPU Mobile Hydraulic Power Unit Machine Systems Media Number -RENR8646-22 Publication Date -01/02/2015 Date Updated -12/09/2018 i07475189 Upper Frame and Undercarriage Frame - Connect SMCS - 4150-077; 7051-077 Connect Procedure Table 1 Required Tools Tool Part Number Part Description Qty A - Loctite C5A Copper Anti-Seize - B 228-4533 Boom Cylinder Link Gp 1 C - Bar Stock 48 inch by 5 inch Round 1 4C-6486 Stand 1 8S-7621 Tube 2 8S-8048 Saddle 2 8S-7615 Pin 2 D 8S-7625 Collar 2 396-9840 Cylinder As 2 447-0910 Electric Hydraulic Pump Gp115V 1 447-0911 Electric Hydraulic Pump Gp230V 1 E FT-2765 Support Beam As 1 F - Guide Bolt M24-3 by 250mm 4 G 9U-7536 Lift Stand 2 https://127.0.0.1/sisweb/sisweb/techdoc/techdoc_print_page.jsp?returnurl=/sis... 2020/9/20
326D L Excavator PJM00001-UP (MACHINE) POWERED BY C7 Engine(SEBP624... 2/7 447-0910 Electric Hydraulic Pump Gp115V 1 447-0911 Electric Hydraulic Pump Gp 1 H - Guide Bolt M20-2.5 by 250mm 2 J 276-8831 Pin Driver 1 K - Loctite RTV Clear Silicone Sealant - L 311-1362 Vacuum Gauge Gp 1 Illustration 1 g03794298 1. Use a suitable towing device and slowly pull the undercarriage frame assembly into position under upper frame assembly (14). The weight of undercarriage frame assembly is approximately 12383 kg (27300 lb). Illustration 2 g03792578 https://127.0.0.1/sisweb/sisweb/techdoc/techdoc_print_page.jsp?returnurl=/sis... 2020/9/20
https://www.ebooklibonline.com Hello dear friend! Thank you very much for reading. Enter the link into your browser. The full manual is available for immediate download. https://www.ebooklibonline.com
326D L Excavator PJM00001-UP (MACHINE) POWERED BY C7 Engine(SEBP624... 3/7 Illustration 3 g02458377 2. Use Tooling (D) and Tooling (G) to lower the upper structure onto the undercarriage in increments of 13 mm (0.5 inch). The weight of the upper structure is approximately 22217 kg (48980 lb). Note: Lower the rear of upper structure first in designated increments to clear the pinion gear with the ring gear. Illustration 4 g02458501 Illustration 5 g02458500 https://127.0.0.1/sisweb/sisweb/techdoc/techdoc_print_page.jsp?returnurl=/sis... 2020/9/20
326D L Excavator PJM00001-UP (MACHINE) POWERED BY C7 Engine(SEBP624... 4/7 3. Remove Tooling (F). Apply Tooling (A) to the threads of bolts (17). Install two bolts (17). Install remaining bolts (17). Torque bolts (17) to a torque of 900 100 N m (665 75 lb ft). Install tube assembly (16). Note: Torque for bolts (17) is 250 25 N m (184 18 lb ft). Turn an additional angle of 60 5 degrees for 330D and 326D excavators. Refer to Service Magazine , M0083843 , "An Improved Bolt Tightening Procedure for the Critical Joints Is Now Used on all Excavators" for more detailed information. Illustration 6 g02463380 4. Attach a suitable lifting device to Tooling (E) and remove Tooling (E) from Tooling (G). The weight of Tooling (E) is approximately 249 kg (550 lb). Illustration 7 g02458416 At operating temperature, the hydraulic oil is hot and under pressure. Hot oils can cause burns. To prevent possible personal injury, release the pressure in the work tool hydraulic circuit (boom, stick, bucket, and swing), travel circuits, https://127.0.0.1/sisweb/sisweb/techdoc/techdoc_print_page.jsp?returnurl=/sis... 2020/9/20
326D L Excavator PJM00001-UP (MACHINE) POWERED BY C7 Engine(SEBP624... 5/7 and the hydraulic oil tank at the filler cap before any hydraulic lines or components are disconnected or removed. Remove the filler cap only when the engine is stopped and the filler cap is cool enough to touch. 5. Install clamp (13), retaining ring (12), and bracket (11). Connect hoses (10). Illustration 8 g03792863 6. Attach a suitable lifting device to Tooling (B). Tooling (B) weights approximately 332 kg (732 lb). Remove plate (7) and bolts (6). Illustration 9 g02458380 7. Attach a suitable lifting device to boom cylinder (8). Boom cylinder (8) weights approximately 380 kg (840 lb). Using Tooling (J) to drive pin (9). https://127.0.0.1/sisweb/sisweb/techdoc/techdoc_print_page.jsp?returnurl=/sis... 2020/9/20
326D L Excavator PJM00001-UP (MACHINE) POWERED BY C7 Engine(SEBP624... 6/7 Illustration 10 g02458379 8. Install plate (7) and bolts (6). Install grease hose assembly (5). Illustration 11 g02458360 9. Remove cover assembly (2). Install ring gear (4) and bolts (3) into cover assembly (2). Apply Tooling (K) onto cover assembly (2). Fill final drive with oil. Refer to Operation and Maintenance Manual, "Final Drive - Oil Change". Illustration 12 g02458357 https://127.0.0.1/sisweb/sisweb/techdoc/techdoc_print_page.jsp?returnurl=/sis... 2020/9/20
326D L Excavator PJM00001-UP (MACHINE) POWERED BY C7 Engine(SEBP624... 7/7 10. The planetary gear group is being held onto the sprocket housing only by Tooling (H). The approximate weight of the planetary group is 163 kg (360 lb). Be careful not to allow the planetary gear group to slide outward. Illustration 13 g02458336 11. Install cover assembly (2). Install bolts (1). Remove Tooling (H). Install remaining bolts (1). Tighten bolts (1). 12. Fill each final drive. Refer to Operation and Maintenance Manual, "Final Drive Oil - Change". End By: a. Install the bucket. Copyright 1993 - 2020 Caterpillar Inc. Sun Sep 20 08:02:11 UTC+0800 2020 All Rights Reserved. Private Network For SIS Licensees. https://127.0.0.1/sisweb/sisweb/techdoc/techdoc_print_page.jsp?returnurl=/sis... 2020/9/20
326D L Excavator PJM00001-UP (MACHINE) POWERED BY C7 Engine(SEBP624... 1/6 Shutdown SIS Previous Screen Product: EXCAVATOR Model: 326D L EXCAVATOR PJM Configuration: 326D L Excavator PJM00001-UP (MACHINE) POWERED BY C7 Engine Disassembly and Assembly 324D, 325D, 326D and 329D Excavators and 329D MHPU Mobile Hydraulic Power Unit Machine Systems Media Number -RENR8646-22 Publication Date -01/02/2015 Date Updated -12/09/2018 i06889712 Recoil Spring - Disassemble SMCS - 4158-015 Disassembly Procedure Table 1 Required Tools Tool Part Number Part Description QTY A 4C-9540 Recoil Spring Bench 1 146-2457 Hydraulic Power Supply Gp 1 B 223-3506 Hydraulic Cylinder and Lines Gp 1 C 8S-9971 Adapter 1 Table 2 Required Sockets Thread Socket Part Number M36 138 5189 4C-4467 M42 193 8100 (1) 5S-6081 M48 FT-3033 (2) 371 1080 (3) M64 5S-6086 https://127.0.0.1/sisweb/sisweb/techdoc/techdoc_print_page.jsp?returnurl=/sis... 2020/9/20
326D L Excavator PJM00001-UP (MACHINE) POWERED BY C7 Engine(SEBP624... 2/6 (1)Used with M42 flat sided nut. (2)Used with M48 flat sided nut that is 54 mm (2.13 inch) between the two flats. (3)Used with M48 flat sided nut that is 65 mm (2.56 inch) between the two flats. Start By: a. Remove the front idler and the recoil spring assembly. The spring of the recoil spring assembly is compressed under several tons of force. Do not attempt to compress or release the tension of the spring with the nut on the end of the retaining rod. Damaged threads on the retaining rod or nut can cause the assembly to come apart with force, resulting in injury or death. 1. Prior to disassembling the recoil spring assembly, make sure that Tooling (A) is on a level surface. 2. Prior to disassembling the recoil spring thoroughly clean the outside surface. Illustration 1 g00483426 3. Install Tooling (C) on Tooling (B), as shown. https://127.0.0.1/sisweb/sisweb/techdoc/techdoc_print_page.jsp?returnurl=/sis... 2020/9/20
326D L Excavator PJM00001-UP (MACHINE) POWERED BY C7 Engine(SEBP624... 3/6 Illustration 2 g00494710 Illustration 3 g00483437 Note: Two adjustable supports (1), reaction plate (2), and movable plate (3) are part of Tooling (A). 4. Adjust the spacing between reaction plate (2) and movable plate (3). The spacing is approximately the same length as the recoil spring assembly (free length). Also, make sure that two adjustable supports (1) are positioned between the reaction plate and the movable plate, as shown. Level the two supports. Note: The recoil spring assembly may be installed in Tooling (A) from the end. In this case, reaction plate (2) must be removed. Then reinstall the reaction plate after the recoil spring assembly is in place on two adjustable supports (1). NOTICE Do not remove the hoist from the recoil spring assembly until the unit is leveled, centered and locked in the specified tooling. 5. The combined weight of the recoil spring assembly is approximately 116 kg (255 lb). https://127.0.0.1/sisweb/sisweb/techdoc/techdoc_print_page.jsp?returnurl=/sis... 2020/9/20
326D L Excavator PJM00001-UP (MACHINE) POWERED BY C7 Engine(SEBP624... 4/6 6. Fasten a suitable lifting device to the recoil spring assembly. Put the recoil spring assembly in position on two adjustable supports (1) in Tooling (A). 7. Adjust the two adjustable supports to align the centerline of the recoil spring assembly with the centerline of Tooling (A). Illustration 4 g00498760 The hoist has been removed from the recoil spring assembly to provide a better illustration of level gauge (4). 8. Put a level gauge (4) on the recoil spring assembly. Illustration 5 g00498781 9. Reposition the recoil spring assembly until the recoil spring assembly is level. Reposition the recoil spring assembly until the retaining rod and nut (6) are centered in the hole in reaction plate (2). 10. The recoil spring assembly is leveled by moving adjustable supports (1) higher or lower. After the recoil spring assembly is leveled and centered, install two pins (5) on the back side of reaction plate (2), as shown. 11. Operate Tooling (B) to hold the recoil spring assembly in position between reaction plate (2) and movable plate (3) (not shown). Make sure that the recoil spring assembly is level and centered. https://127.0.0.1/sisweb/sisweb/techdoc/techdoc_print_page.jsp?returnurl=/sis... 2020/9/20
326D L Excavator PJM00001-UP (MACHINE) POWERED BY C7 Engine(SEBP624... 5/6 Illustration 6 g00498784 12. Close covers (7) on Tooling (A). Use Tooling (B) to compress the recoil spring assembly slightly. Illustration 7 g02148287 Several tons of force are required to compress the recoil spring during assembly. Do not compress the spring assembly until the covers on the tooling have been closed. It is possible for the recoil spring to twist under load and come out of the tooling resulting in injury or death. https://127.0.0.1/sisweb/sisweb/techdoc/techdoc_print_page.jsp?returnurl=/sis... 2020/9/20
326D L Excavator PJM00001-UP (MACHINE) POWERED BY C7 Engine(SEBP624... 6/6 13. Through the opening in the end of Tooling (A), remove the socket head bolts and lock strip (8) from the end of the retaining rod. 14. Remove nut (6). Refer to Table 2 for the correct socket part number. Release the force on the recoil spring assembly. 15. Open the covers on Tooling (A). Attach a suitable lifting device to the recoil spring assembly, and remove the recoil spring assembly from Tooling (A). 16. Separate the components of the recoil spring assembly. Remove support (12), spring (10), support (9), and rod (11). Copyright 1993 - 2020 Caterpillar Inc. Sun Sep 20 08:03:06 UTC+0800 2020 All Rights Reserved. Private Network For SIS Licensees. https://127.0.0.1/sisweb/sisweb/techdoc/techdoc_print_page.jsp?returnurl=/sis... 2020/9/20
326D L Excavator PJM00001-UP (MACHINE) POWERED BY C7 Engine(SEBP624... 1/7 Shutdown SIS Previous Screen Product: EXCAVATOR Model: 326D L EXCAVATOR PJM Configuration: 326D L Excavator PJM00001-UP (MACHINE) POWERED BY C7 Engine Disassembly and Assembly 324D, 325D, 326D and 329D Excavators and 329D MHPU Mobile Hydraulic Power Unit Machine Systems Media Number -RENR8646-22 Publication Date -01/02/2015 Date Updated -12/09/2018 i06889768 Recoil Spring - Assemble SMCS - 4158-016 Assembly Procedure Table 1 Required Tools Tool Part Number Part Description QTY A 4C-9540 Recoil Spring Bench 1 146-2457 Hydraulic Power Supply Gp 1 B 223-3506 Hydraulic Cylinder and Lines Gp 1 C 8S-9971 Adapter 1 E 9S-3263 Thread Lock Compound 1 Table 2 Required Sockets Thread Socket Part Number M36 138 5189 4C-4467 M42 193 8100 (1) 5S-6081 M48 FT-3033 (2) 371 1080 (3) https://127.0.0.1/sisweb/sisweb/techdoc/techdoc_print_page.jsp?returnurl=/sis... 2020/9/20
326D L Excavator PJM00001-UP (MACHINE) POWERED BY C7 Engine(SEBP624... 2/7 M64 5S-6086 (1)Used with M42 flat sided nut. (2)Used with M48 flat sided nut that is 54 mm (2.13 inch) between the two flats. (3)Used with M48 flat sided nut that is 65 mm (2.56 inch) between the two flats. The spring of the recoil spring assembly is compressed under several tons of force. Do not attempt to compress or release the tension of the spring with the nut on the end of the retaining rod. Damaged threads on the retaining rod or nut can cause the assembly to come apart with force, resulting in injury or death. Note: Prior to assembling the recoil spring assembly, make sure that Tooling (A) is on a level surface. Illustration 1 g01157185 1. Check the condition of the threads on rod (11) and nut (6). If the threads are worn or damaged, use new parts for replacement. 2. Assemble the recoil spring assembly loosely. Position spring (10) onto support (9). Install rod (11) into support (9). Position support (12). https://127.0.0.1/sisweb/sisweb/techdoc/techdoc_print_page.jsp?returnurl=/sis... 2020/9/20
326D L Excavator PJM00001-UP (MACHINE) POWERED BY C7 Engine(SEBP624... 3/7 Illustration 2 g00483426 3. Install Tooling (C) on Tooling (B). Illustration 3 g00494710 Illustration 4 g00483437 Note: Two adjustable supports (1), reaction plate (2), and movable plate (3) are part of Tooling (A). 4. Adjust the spacing between reaction plate (2) and movable plate (3) so that the spacing is approximately the same length as the recoil spring assembly. Also, make sure that two https://127.0.0.1/sisweb/sisweb/techdoc/techdoc_print_page.jsp?returnurl=/sis... 2020/9/20
326D L Excavator PJM00001-UP (MACHINE) POWERED BY C7 Engine(SEBP624... 4/7 adjustable supports (1) are positioned between the reaction plate and the movable plate, as shown. Level the two supports. Note: The recoil spring assembly may be installed in Tooling (A) from the end. In this case, reaction plate (2) must be removed. Then reinstall the reaction plate after the recoil spring assembly is in place on two adjustable supports (1). NOTICE Do not remove the hoist from the recoil spring assembly until the unit is leveled, centered and locked in the specified tooling. 5. The combined weight of the recoil spring assembly is approximately 116 kg (255 lb). 6. Fasten a suitable lifting device to the recoil spring assembly. Put the recoil spring assembly in position on two adjustable supports (1) in Tooling (A). 7. Adjust the two adjustable supports to align the centerline of the recoil spring assembly with the centerline of Tooling (A). Illustration 5 g00949740 The hoist has been removed from the recoil spring assembly to provide a better illustration of level gauge (4). 8. Operate Tooling (B) and guide the end of the recoil spring assembly through the hole in reaction plate (2). Put a level gauge (4) on the recoil spring assembly. Make sure that the recoil spring assembly is level and centered in Tooling (A). Remove the suitable lifting device from the recoil spring assembly. https://127.0.0.1/sisweb/sisweb/techdoc/techdoc_print_page.jsp?returnurl=/sis... 2020/9/20
326D L Excavator PJM00001-UP (MACHINE) POWERED BY C7 Engine(SEBP624... 5/7 Illustration 6 g00498784 Improper assembly of parts that are spring loaded can cause bodily injury. To prevent possible injury, follow the established assembly procedure and wear protective equipment. 9. Close covers (7) on Tooling (A). Compress the recoil spring assembly with Tooling (B). Illustration 7 g01157190 (X) Compressed length of the spring https://127.0.0.1/sisweb/sisweb/techdoc/techdoc_print_page.jsp?returnurl=/sis... 2020/9/20
326D L Excavator PJM00001-UP (MACHINE) POWERED BY C7 Engine(SEBP624... 6/7 Illustration 8 g00498784 10. Open the covers on Tooling (A). Measure the compressed length of the recoil spring. The compressed length is Dimension (X). Refer to Table 3 for the correct compressed spring length. Table 3 Recoil Spring Compressed Length Model Dimension (X) 315D 448.0 mm (17.64 inch) 319D 550.0 mm (21.65 inch) 320D 550.0 mm (21.65 inch) 550.0 mm (21.65 inch) 323D 686.0 mm (27.01 inch)(1) 324D 606.0 mm (23.86 inch) 325C 551.0 mm (21.69 inch) 686.0 mm (27.01 inch) 325D 845.0 mm (33.27 inch)(2) 326D L 606.0 mm (23.86 inch) 328D 644.0 mm (25.35 inch) 329D 686.0 mm (27.01 inch) 644.0 mm (25.35 inch) 330D 785.0 mm (30.91 inch)(3) 644.0 mm (25.35 inch) 336D 785 mm (30.91inch)(4) (1)This Dimension is for (S/N: DKW1-Up; SED1-Up; NES1-Up) (2)This Dimension is for (S/N: GBR1-Up; MCL1-Up) https://127.0.0.1/sisweb/sisweb/techdoc/techdoc_print_page.jsp?returnurl=/sis... 2020/9/20
326D L Excavator PJM00001-UP (MACHINE) POWERED BY C7 Engine(SEBP624... 7/7 (3)This Dimension is for (S/N: ERN1-Up) (4)This Dimension is for (S/N: DTS1-Up; LMG1-Up; JWR1-Up) 11. If the assembled length is not correct, close covers (7) on Tooling (A), and adjust the spring length with Tooling (B). If the assembled length is correct, then assembly of the recoil spring assembly can be completed. Illustration 9 g01157193 12. Apply a rust inhibitor to the threads on the end of the retaining rod for the recoil spring. Install nut (6). Tighten nut (6). Refer to Table2 for the correct socket part number. 13. Apply Tooling (E) on the threads of the socket head bolts that hold strip (8) in place. Install the strip and the socket head bolts that hold the strip. 14. Attach a suitable lifting device to the recoil spring assembly, and remove the recoil spring assembly from Tooling (A). The weight of the recoil spring assembly is approximately 116 kg (255 lb). End By: a. Install the front idler and the recoil spring. Copyright 1993 - 2020 Caterpillar Inc. Sun Sep 20 08:04:02 UTC+0800 2020 All Rights Reserved. Private Network For SIS Licensees. https://127.0.0.1/sisweb/sisweb/techdoc/techdoc_print_page.jsp?returnurl=/sis... 2020/9/20
326D L Excavator PJM00001-UP (MACHINE) POWERED BY C7 Engine(SEBP624... 1/12 Shutdown SIS Previous Screen Product: EXCAVATOR Model: 326D L EXCAVATOR PJM Configuration: 326D L Excavator PJM00001-UP (MACHINE) POWERED BY C7 Engine Disassembly and Assembly 324D, 325D, 326D and 329D Excavators and 329D MHPU Mobile Hydraulic Power Unit Machine Systems Media Number -RENR8646-22 Publication Date -01/02/2015 Date Updated -12/09/2018 i02606369 Final Drive - Disassemble SMCS - 4050-015 S/N - A3R1-UP S/N - AZP1-UP S/N - BFC1-UP S/N - BYS1-UP S/N - CZF1-UP S/N - DBH1-UP S/N - DJF1-UP S/N - DTZ1-UP S/N - EBM1-UP S/N - EJC1-UP S/N - GBR1-UP S/N - GPB1-UP S/N - GPK1-UP S/N - JAT1-UP S/N - JHJ1-UP S/N - JJG1-UP https://127.0.0.1/sisweb/sisweb/techdoc/techdoc_print_page.jsp?returnurl=/sis... 2020/9/20
326D L Excavator PJM00001-UP (MACHINE) POWERED BY C7 Engine(SEBP624... 2/12 S/N - JZR1-UP S/N - KBE1-UP S/N - LAB1-UP S/N - LAL1-UP S/N - MCL1-UP S/N - MNB1-UP S/N - MND1-UP S/N - NAC1-UP S/N - PJM1-UP S/N - PKE1-UP S/N - PYT1-UP S/N - RSK1-UP S/N - SCR1-UP S/N - SCY1-UP S/N - SYM1-UP S/N - T2D1-UP S/N - T2S1-UP S/N - TPM1-UP S/N - TRH1-UP S/N - TSN1-UP S/N - TZL1-UP S/N - WDK1-UP S/N - XDB1-UP S/N - YFW1-UP Disassembly Procedure Table 1 https://127.0.0.1/sisweb/sisweb/techdoc/techdoc_print_page.jsp?returnurl=/sis... 2020/9/20
326D L Excavator PJM00001-UP (MACHINE) POWERED BY C7 Engine(SEBP624... 3/12 Required Tools Tool Part Number Part Description Qty A 1P-2420 Transmission Repair Stand 1 B 138-7573 Link Bracket 2 C 154-6181 Forcing Screw 1 D 138-7574 Link Bracket 2 5F-7366 Forcing Screw 1 1P-5546 Crossblock 1 1U-9889 Crossblock 1 E 1P-0520 Driver Group 1 6V-7888 Puller Leg 2 1H-3112 Puller Assembly 1 1P-5551 Adjustable Screw Assembly 1 F 1U-8846 Gasket Sealant 1 Start By: a. Remove the final drive. Refer to Disassembly and Assembly, "Final Drive - Remove". Note: Cleanliness is an important factor. Before the disassembly procedure, the exterior of the component should be thoroughly cleaned. This will prevent dirt from entering the internal mechanism. 1. Put an alignment mark across the sections of the final drive for assembly purposes. The parts must be reinstalled in the part's original locations. Illustration 1 g00708089 2. Fasten the final drive to Tooling (A), as shown. The combined weight of the final drive and final drive sprocket is approximately 312 kg (688 lb). https://127.0.0.1/sisweb/sisweb/techdoc/techdoc_print_page.jsp?returnurl=/sis... 2020/9/20
326D L Excavator PJM00001-UP (MACHINE) POWERED BY C7 Engine(SEBP624... 4/12 3. Remove bolts (1) and the washers that hold the cover in position. Illustration 2 g00708090 4. Remove the setscrews from the cover. Fasten Tooling (B) and a suitable lifting device to cover (2), as shown. The weight of cover (2) is approximately 32 kg (70 lb). Remove cover (2). Illustration 3 g00708091 5. Remove thrust plate (3) from cover (2). 6. Remove plugs (4) from cover (2). https://127.0.0.1/sisweb/sisweb/techdoc/techdoc_print_page.jsp?returnurl=/sis... 2020/9/20
Suggest: If the above button click is invalid. Please download this document first, and then click the above link to download the complete manual. Thank you so much for reading
326D L Excavator PJM00001-UP (MACHINE) POWERED BY C7 Engine(SEBP624... 5/12 Illustration 4 g00708235 7. Remove O-ring seals (5) from both plugs (4) that were in the cover. Illustration 5 g00708092 8. Remove spacer (6) from carrier assembly (7). 9. Remove sun gear (8) from carrier assembly (7). 10. Remove carrier assembly (7) by lifting the carrier assembly straight up. The weight of carrier assembly (7) is approximately 14 kg (30 lb). Illustration 6 g01304883 11. Disassemble carrier assembly (7), as follows. a. Drive spring pin (10) into planetary shaft (9) with a hammer and a punch. https://127.0.0.1/sisweb/sisweb/techdoc/techdoc_print_page.jsp?returnurl=/sis... 2020/9/20
https://www.ebooklibonline.com Hello dear friend! Thank you very much for reading. Enter the link into your browser. The full manual is available for immediate download. https://www.ebooklibonline.com