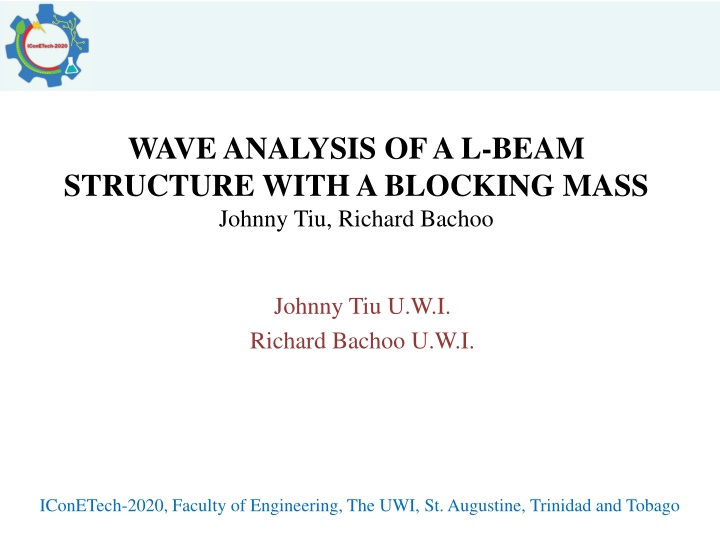
Wave Analysis of L-Beam Structure with Blocking Mass
Explore the wave analysis of an L-beam structure with a blocking mass, including the methodology, objectives, and results obtained on natural frequencies. This study dives into wave transformation matrices, boundary reflection, joint transmission, and the impact of blocking mass parameters on the structure's response.
Download Presentation

Please find below an Image/Link to download the presentation.
The content on the website is provided AS IS for your information and personal use only. It may not be sold, licensed, or shared on other websites without obtaining consent from the author. If you encounter any issues during the download, it is possible that the publisher has removed the file from their server.
You are allowed to download the files provided on this website for personal or commercial use, subject to the condition that they are used lawfully. All files are the property of their respective owners.
The content on the website is provided AS IS for your information and personal use only. It may not be sold, licensed, or shared on other websites without obtaining consent from the author.
E N D
Presentation Transcript
WAVE ANALYSIS OF A L-BEAM STRUCTURE WITH A BLOCKING MASS Johnny Tiu, Richard Bachoo Johnny Tiu U.W.I. Richard Bachoo U.W.I. IConETech-2020, Faculty of Engineering, The UWI, St. Augustine, Trinidad and Tobago
INTRODUCTION What is Wave Analysis? And how does it work? IConETech-2020, Faculty of Engineering, The UWI, St. Augustine, Trinidad and Tobago
INTRODUCTION Why use wave analysis? When should wave analysis be used? IConETech-2020, Faculty of Engineering, The UWI, St. Augustine, Trinidad and Tobago
OBJECTIVES Develop wave transformation matrices. Boundary Reflection and Transmission across joint Propagation Obtain wave relations for an example structure. Determine the natural frequencies of structure. Determine how blocking mass parameters affect the response of the structure. IConETech-2020, Faculty of Engineering, The UWI, St. Augustine, Trinidad and Tobago
METHODOLOGY Heavily influenced by Mei and Mace ?2? ?,? ? ?2 ?? ?,? ?? EA?2u x,t + ???2? ?,? ?? ?,? ? ? ??? = ? ?,? ??2 ???2? ?,? ???2? ?,? + ??? ? ?,? = 0 ??2 ??2 A?2u x,t = ?(?,?) ?t2 ?x2 IConETech-2020, Faculty of Engineering, The UWI, St. Augustine, Trinidad and Tobago
METHODOLOGY Boundary reflection Boundary reflection a = rAa+ b+= rBb Joint reflection and transmission Joint reflection and transmission j2 j1 = rj22j2 += rj11j1 +,+tj12j1 + tj21j2 + Propagation along beam Propagation along beam j1 a+= f ? j1 b = f ? j2 j2 = f ? a + += f ? b+ IConETech-2020, Faculty of Engineering, The UWI, St. Augustine, Trinidad and Tobago
RESULTS I 0 r? I 0 0 0 0 0 0 0 0 I 0 0 0 0 0 I 0 0 0 0 0 0 0 0 0 0 I 0 0 0 0 0 ? ?+ j1 j1 j2 j2 b b+ ? 0 I 0 0 0 0 ? 0 0 0 0 0 + rj11 tj12 0 0 0 tj12 rj22 I 0 0 = 0 + ? 0 I ? 0 r? IConETech-2020, Faculty of Engineering, The UWI, St. Augustine, Trinidad and Tobago
RESULTS IConETech-2020, Faculty of Engineering, The UWI, St. Augustine, Trinidad and Tobago
RESULTS Natural Frequencies obtained from characteristic polynomial Mode Number Natural Frequency (Hz) 87.741 128.58 282.48 349.16 576.5 627.47 688.97 730.31 1 2 3 4 5 6 7 8 IConETech-2020, Faculty of Engineering, The UWI, St. Augustine, Trinidad and Tobago
RESULTS Variation of natural frequencies due to scaling factor, Mode number Natural Frequency (Hz) =1 =3 =5 Wave Ansys Wave Ansys Wave Ansys 1 87.741 87.066 84.638 82.596 80.117 75.154 2 128.58 126.99 122.5 127.74 108.84 127.78 3 282.48 280.49 238.78 264.13 154.74 222.41 4 349.16 346.95 240.02 348.33 161.44 344.82 5 576.5 579.59 293.68 539.72 268.46 417.43 IConETech-2020, Faculty of Engineering, The UWI, St. Augustine, Trinidad and Tobago
RESULTS IConETech-2020, Faculty of Engineering, The UWI, St. Augustine, Trinidad and Tobago
RESULTS Initial transition frequency band IConETech-2020, Faculty of Engineering, The UWI, St. Augustine, Trinidad and Tobago
RESULTS Secondary transition frequency exhibiting total reflection IConETech-2020, Faculty of Engineering, The UWI, St. Augustine, Trinidad and Tobago
RESULTS Variation of Natural frequencies due to change of joint material Mode number Natural Frequency (Hz) Aluminium Wave 87.741 128.58 283.15 352.83 587.15 Cast Iron Wave 87.741 128.58 282.48 349.77 579.16 Low Carbon Steel Wave 87.741 128.58 282.48 349.16 576.5 Brass Ansys 87.064 124.25 280.46 340.6 579.5 Ansys 87.066 126.64 280.49 346.11 579.59 Ansys 87.066 126.99 280.49 346.95 579.59 Wave 87.741 127.97 282.48 349.16 574.5 Ansys 87.064 125.54 280.46 343.53 579.49 1 2 3 4 5 IConETech-2020, Faculty of Engineering, The UWI, St. Augustine, Trinidad and Tobago
CONCLUSION Wave model currently limited fairly simple planar structures Constrained by number of members and types of discontinuities. Wave model as it stands only holds for low scaling factors. Model flexibility of joint. Include out of plane within model. IConETech-2020, Faculty of Engineering, The UWI, St. Augustine, Trinidad and Tobago
THANK YOU! IConETech-2020, Faculty of Engineering, The UWI, St. Augustine, Trinidad and Tobago