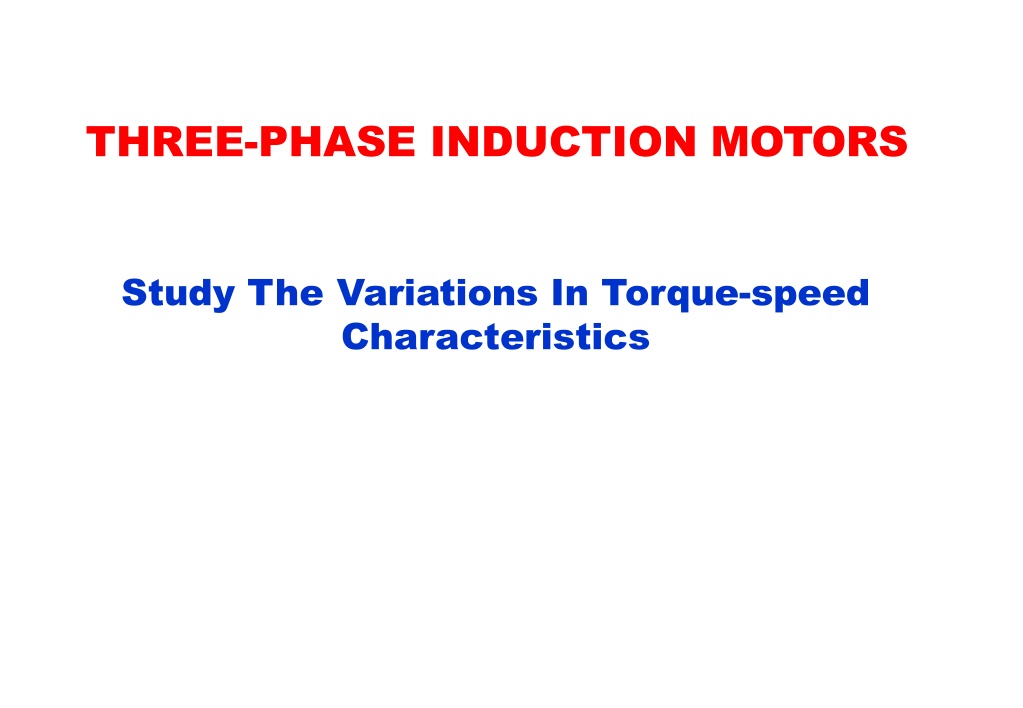
Variations in IM Torque-Speed Characteristics
The study explores the variations in torque-speed characteristics of three-phase induction motors, focusing on the performance of a specific motor example. It covers topics such as maximum torque, starting torque, and the impact of rotor resistance on motor efficiency and performance. The analysis provides insights into the trade-offs between high and low rotor resistance designs in terms of starting torque, slip, and efficiency.
Download Presentation

Please find below an Image/Link to download the presentation.
The content on the website is provided AS IS for your information and personal use only. It may not be sold, licensed, or shared on other websites without obtaining consent from the author. If you encounter any issues during the download, it is possible that the publisher has removed the file from their server.
You are allowed to download the files provided on this website for personal or commercial use, subject to the condition that they are used lawfully. All files are the property of their respective owners.
The content on the website is provided AS IS for your information and personal use only. It may not be sold, licensed, or shared on other websites without obtaining consent from the author.
E N D
Presentation Transcript
THREE-PHASE INDUCTION MOTORS Study The Variations In Torque-speed Characteristics
Three-Phase Induction Motor Performance EXAMPLE 1-8 A 460-V, 25-hp, 60-Hz, four-pole, Y-connected wound-rotor induction motor has the following impedances in ohms per phase referred to the stator circuit: R1 = 0.641 , R2 = 0.332 , X1= 1.106 , X2 = 0.464 , Xm = 26.3 a) What is the maximum torque of this motor? At what speed and slip does it occur? b) What is the starting torque of this motor? c) When the rotor resistance is doubled, what is the speed at which the maximum torque now occurs? What is the new starting torque of the motor? SOLUTION The per-phase applied voltage is V =VL=460 = 255.2V 1 3 3 a) the slip at which the motor develops maximum torque is 0.332 R2 s = =0.196 = b + (X + X )2 0.6412 + (1.106 +0.464)2 R2 1 1 2 The synchronous speed of the motor is N =120 f =120 60 = 1800 rpm or 188.5rad / s s 4 P 2
Three-Phase Induction Motor Performance SOLUTION (1-8) cont. This corresponds to a mechanical speed of Nm = (1 sb ) Ns = (1 0.196)1800 = 1447rpm or 151.6 rad / s the torque at this speed is 3V2 1 = 1 2 s Tdm R + R2+ (X + X )2 1 1 1 2 = 222 N.m 3 255.22 2 188.5 0.641+ 1 = Tdm 0.6412 + (1.106 + 0.464)2 b) The starting torque of this motor is found by setting s = 1 in the torque equation 3V 2 Tds= (R + R R +(X + X 1 2 ) ) 2 2 s 1 2 1 2 3 255.22 0.332 2+(1.106 + 0.464) =101 N.m = Tds (0.641+ 0.332) 188.5 2 3
Three-Phase Induction Motor Performance SOLUTION (1-8) cont. c) If the rotor resistance is doubled, then the slip at maximum torque doubles, too. Therefore, sb2 = 2sb = 2 x 0.192 =0.392 and the speed at maximum torque is Nm = (1 sb2 ) Ns = (1 0.392)1800 = 1094 rpm or 114.6 rad / s The maximum torque is still: Tdm = 222N.m The starting torque of this motor is now Tdm = 222N.m 3 255.22 2 0.332 2+(1.106 + 0.464) = Tds (0.641+ 2 0.332) 188.5 2 Tds= 165N.m Td[N.m] Figure 1-13 Torque-speed characteristics for the motor of Example 1-8, which is similar to Figure 1-11. Nm[rpm] 4
Variations in IM Torque-Speed Characteristics In Example 1-8 two characteristic curves were shown, depending on the rotor resistance, R2. Also, Example 1-8 illustrated an induction motor designer's dilemma - if a rotor is designed with high resistance, R2, then the motor's starting torque is quite high, but the slip is also quite high at normal operating conditions. Recall that Pd = (1 - s)Pag, so the higher the slip, the smaller the fraction of air-gap power actually converted to mechanical form, and thus the lower the motor's efficiency. A motor with high rotor resistance has a good starting torque but poor efficiency at normal operating conditions. On the other hand, a motor with low rotor resistance has a low starting torque and high starting current, but its efficiency at normal operating conditions is quite high. 5
Variations in IM Torque-Speed Characteristics An induction motor designer is forced to compromise between the conflicting requirements of high starting torque and good efficiency. One possible solution to this is to use a wound-rotor induction motor and insert extra resistance into the rotor during starting. The extra resistance could be completely removed for better efficiency during normal operation. Unfortunately, wound-rotor motors are more expensive, need more maintenance, and require a more complex automatic control circuit than cage rotor motors. Also, it is sometimes important to completely seal a motor when it is placed in a hazardous or explosive environment, and this is easier to do with a completely self-contained rotor. It would be nice to figure out some way to add extra rotor resistance at starting and to remove it during normal running without slip rings and without operator or control circuit intervention. 6
Variations in IM Torque-Speed Characteristics LOW resistancerotor HIGH resistancerotor Starting torque HIGH, Low starting current Starting torque LOW, HIGH starting current Slip HIGH at normal conditions Slip LOW at normal conditions Pd = (1-s) Pag ; sincreases Pd = (1-s) Pag ; sdecreases Pd decrease, and efficiencydecrease. Pd increase, and efficiencyincrease Use a wound rotor induction motor and insert extra resistance into the rotor during starting, and then removed for better efficiency during normal operations. But, wound rotor induction motors are more expensive, need more maintenanceetc. Solution - utilising leakage reactance to obtain the desired curve as shown next 7
Variations in IM Torque-Speed Characteristics Figure 1-14 illustrates the desired motor characteristic. This figure shows two wound-rotor motor characteristics, one with high resistance and one with low resistance. At high slips, the desired motor should behave like the high-resistance wound-rotor motor curve; at low slips, it should behave like the low- resistance wound-rotor motor curve. Fortunately, it is possible to accomplish just this effect by properly taking advantage of leakage reactance in induction motor rotor design. Td Figure 1-14. A torque-speed characteristic curve combining high-resistance effects at low speeds (high slip) with low-resistance effects at high speed (low slip). Ns 8
Control of Induction Motor Characteristics Control of Motor Characteristics by Cage Rotor Design The reactance X2 in an induction motor equivalent circuit represents the referred form of the rotor's leakage reactance. Recall that leakage reactance is the reactance due to the rotor flux lines that do not also couple with the stator windings. In general, the farther away from the stator a rotor bar or part of a bar is, the greater its leakage reactance, since a smaller percentage of the bar's flux will reach the stator. Therefore, if the bars of a cage rotor are placed near the surface of the rotor, they will have only a small leakage flux and the reactance X2 will be small in the equivalent circuit. On the other hand, if the rotor bars are placed deeper into the rotor surface, there will be more leakage and the rotor reactance X2 will be larger. 9
Control of Induction Motor Characteristics Figure 1-15(a) shows a photograph of a rotor lamination showing the cross section of the bars in the rotor. The rotor bars in the figure are quite large and are placed near the surface of the rotor. Such a design will have a low resistance (due to its large cross section) and a low leakage reactance and X2 (due to the bar's location near the stator). Because of the low rotor resistance, the pullout torque will be quite near synchronous speed, and the motor will be quite efficient. However, since R2is small, the motor's starting torque will be small, and its starting current will be high. Figure 1-15(a) 1 0
Control of Induction Motor Characteristics This type of design is called the National Electrical Manufacturers Association (NEMA) design class A. It is more or less a typical induction motor, and its characteristics are basically the same as those of a wound-rotor motor with no extra resistance inserted. Its torque-speed characteristic is shown in Figure 1-16. Figure 1-15 (d), however, shows the cross section of an induction motor rotor with small bars placed near the surface of the rotor. (a) (b) NEMA design classB large, deep rotorbars NEMA design classA Large bars near thesurface (d) (c) NEMA design classC double-cagerotordesign NEMA design classD small bars near thesurface FIGURE 1-15. Laminations from typical cage induction motor rotors. showing the cross section of the rotorbars. 11
Control of Induction Motor Characteristics Since the cross-sectional area of the bars is small, the rotor resistance is relatively high. Since the bars are located near the stator, the rotor leakage reactance is still small. This motor is very much like a wound- rotor induction motor with extra resistance inserted into the rotor. Because of the large rotor resistance, this motor has a pullout torque occurring at a high slip, and its starting torque is quite high. A cage motor with this type of rotor construction is called NEMA design class D. Its torque-speed characteristic is also shown in Figure 1-16. FIGURE 1-16. Typical torque-speed curves for different rotor designs. 1 2
Control of Induction Motor Characteristics Deep-Bar and Double-Cage Rotor Designs Both of the previous rotor designs are essentially similar to awound- rotor motor with a set rotorresistance. How can a variable rotor resistance be produced to combine thehigh starting torque and low starting current of a class D design with the low normal operating slip and high efficiency of a class Adesign? It is possible to produce a variable rotor resistance by the useof deep-rotor bars or double-cage rotors. The basic concept isillustrated with a deep-bar rotor in Figure 1-17. Deep-Bar Rotor: Figure 1-17(a) shows a current flowing through the upper part of a deep rotor bar. Since currentflowing in that area is tightly coupled to the stator,the leakage inductance is small for this region. (a) FIGURE 1-17. (a)Flux
Control of Induction Motor Characteristics Figure 1-17(b) shows current flowing deeper inthe bar. Here, the leakage inductance is higher. Since all parts of the rotor bar are in parallel electrically, the bar essentially represents a series of parallel electric circuits, the upper ones having a smaller inductance and the lower ones having a larger inductance, Figure 1-17(c). At low slip (running conditions), the rotor's frequency is very small, and the reactances of all the parallel paths through the bar are small compared to their resistances. The impedancesof all parts of the bar are approximately equal, so current flows through all parts of the bar equally. The resulting large cross-sectional area makes the rotor resistance quite small, resulting in good efficiency at low slips. (b) (c) FIGURE 1-17. (b)&(c) Flux
Control of Induction Motor Characteristics At high slip (starting conditions), thereactances are large compared to the resistances in the rotor bars, so all the current is forced to flow in the low- reactance part of the bar near thestator, Figure 1-17(c). Since the effective cross section is lower, the rotor resistance is higher than before. With ahigh rotor resistance at starting conditions, thestarting torque is relatively higher and the starting current is relatively lower than in a class Adesign. A photograph of a rotor lamination showing the cross-sectional view of a deep rotor bar is shown in Figure 1-15(b). A typical torque-speed characteristic forthis construction is the design class B curve in Figure 1-16. Figure 1-17(c) Figure 1-15(b) 15
Control of Induction Motor Characteristics Double-Cage Rotor: A cross-sectional view of a double-cage rotor is shown in Figure 1-15c. It consists of (1) a large, low-resistance set of bars buried deeply in the rotor and (2) a small, high-resistance set of bars set at the rotorsurface. It is similar to the deep-bar rotor, except that the difference between low-slip and high-slip operation is even more exaggerated. At starting conditions, only the small bar is effective, and the rotorresistance is quite high. This high resistance results in a large startingtorque. However, at normal operating speeds, both bars are effective, and the resistance is almost as lowas in a deep-bar rotor. Double-cage rotors of this sort are used to produce NEMA class C characteristic, and its torque-speed characteristic curve is shown in Figure 1-16. Figure 1-15(c) 1 6
NEMA Classes of Induction Motors ClassA: Tst= 1.25-1.75 TR & Ist= 5-7 IR & s < 5% & SR=2-4% AclassAmotor is considered a standard motor and is suitable for constant-speed applications. The motor can be started by applying the ratedvoltage. It develops a starting torque of 125% to 175% of full-loadtorque. The starting current at the rated voltage is 5 to 7 times therated current. The full-load slip is usually less than 5% because the rotorresistance is relatively low. The speed regulation is 2% to 4%. The rotor bars are placed close to the surface of the rotorlaminations in order to reduce the leakage reactance. Typical applications as fans, blowers, centrifugal type pumps,and machine tools. 1 7
NEMA Classes of Induction Motors Class B: Tst= 1.25-1.75 TR & Ist= 4.5-5.5 IR & s< 5% & SR=3-5% A class B motor is considered a general-purpose motor and can bestarted by applying the rated voltage. The rotor conductors are placed deeper in the slots than for the classA motor. The increase in the rotor reactance reduces the starting torque, whereas an increase in the rotor resistance increases the starting torque. Thus,the starting torque range for a class B motor is almost the same as that of the class Amotor. The starting current is about 4.5 to 5.5 times the full-loadcurrent. The low starting current and almost the same starting torque make classB motors appropriate for class A applications aswell. The speed regulation for class B motors is 3% to5%. Class B motors can be substituted in all applications using class Amotors. 1 8
NEMA Classes of Induction Motors Class C: Tst= 2-2.75 TR & Ist= 3.5-5 IR & s< 5% & SR=4-5% A class C motor usually has a double-cage rotor and is designed forfull- voltage starting. The high-resistance rotor limits the starting current to 3.5 to 5 timesthe full-load current. The starting torque is 200% to 275% of the full-load torque. The speed regulation is 4% to5%. Class C motors are used in applications that require high starting torques, such as compression pumps, crushers, boring mills, conveyor equipment, textile machinery, and wood-working equipment. 1 9
NEMA Classes of Induction Motors Class D: Tst= 2.5-3 TR & Ist= 3-8 IR & s high ( 1) & SR=10% A class D motor is a high-resistance motor capable of developinga starting torque of 250% to 300% of the ratedtorque. The high rotor resistance is created by using high-resistance alloys forthe rotor bars and by reducing the cross-sectional area of the bar. Depending upon the design, the starting current may be 3 to 8 times the rated current. The efficiency of a class D motor is lower than that of thosediscussed above. The speed regulation may be as high as10%. These motors are used in such applications as bulldozers, shearing machines, punch presses, stamping machines, laundry equipment,and hoists. 2 0
Speed Control of 3-Phase Induction Motors Speed Control of Induction Motors The normal operating range of a typical induction motor is confined to less than 5% slip, and the speed variation over that range is more orless directly proportional to the load on the shaft of themotor. Even if the slip could be made larger, the efficiency of the motorwould become very poor, since the rotor copper losses PRCL are directly proportional to the slip on the motor (PRCL = sPag). The rotor speed is given by Nm = (1 s)Ns Therefore, there are only two techniques by which the speed Nm of an induction motor can be controlled: I. One is to vary the synchronous speed, Ns. II.The other technique is to vary the slip,s. 2 1
Speed Control of 3-Phase Induction Motors I. Varying the synchronous speed, which is the speed of the stator and rotor magnetic fields. The synchronous speed of an induction motor is given by ??=120? ? so the only ways in which the synchronous speed Ns of the machine can be varied are by changing one of the following: 1. The number of poles P on the machine. 2. The electrical frequency f. I. Varying the slip of the motor for a given load. Slip s control maybe accomplished by varying either 1. The terminal voltage, V1. 2. The rotor resistance of the motor,R2. 2 2
Speed Control of 3-Phase Induction Motors I-1 Changing Stator Poles Synchronous Speed Control This method is quite suitable for an induction motor with a squirrel-cage rotor. In this case, the stator can be wound with two or more entirely independent windings. Each winding corresponds to a different number of poles and therefore different synchronous speed. At any time, only one winding is inoperation. All other windings are disconnected. For example, an induction motor wound for 4 and 6 poles at a frequencyof 50 Hz can operate either at a synchronous speed of 1500 rpm (4-pole operation) or at 1000 rpm (6-poleoperation). I-2 Frequency Control Synchronous Speed Control The operating speed of an induction motor can be increased ordecreased by increasing or decreasing the frequency of the applied voltagesource. 2 3
Speed Control of 3-Phase Induction Motors This method enables us to obtain a wide variation in the operatingspeed of an induction motor. The only requirement is that we must have a variable-frequency supply. To maintain constant flux density and thereby the maximum torque developed, the applied voltage must be varied in direct proportion tothe frequency. The speed-torque characteristics of an induction motor at differentfrequencies below and above the base frequency (60Hz) are shown in Figure1-18. Also shown in the figure is a typical load curve. At each frequency themotor operates at a speed at which the load line intersects the speed-torque characteristic for thatfrequency. 6-Pole/60HZ Loadline Loadline Figure 1-18 Speed-torque characteristics for various frequencies and adjusted supplyvoltages. 2 4
Speed Control of 3-Phase Induction Motors II-1 Stator Voltage Control Slip Control Since the torque developed by the motor is proportional to the square of the applied voltage, the (reduction/augmentation) in operating speed ofan induction motor can be achieved by (reducing/augmenting) the applied voltage. The speed-torque characteristics for two values of the applied voltage are depicted in Figure 1-19. The method is very convenient to use but is very limited in its scope because to achieve an appreciable change in speed a relatively large change in the applied voltage is required. Figure 1-19 Speed-torque characteristics as a function of supply voltage. 2 5
Speed Control of 3-Phase Induction Motors II-2 Rotor Resistance Control Slip Control We discussed the effect of changes in the rotor resistance on thespeed-torque characteristic of an induction motor as shown in Figure 1-20. This method of speed control is suitable only for wound-rotor inductionmotors. The operating speed of the motor canbe decreased by adding external resistance in the rotor circuit. However, an increase in the rotorresistance causes Loadline an increase in the rotor copper loss, an increase in the operating temperature of the motor, a reduction in the motor efficiency. Because of these drawbacks, this methodof speed control can be used only for short periods. Figure 1-20 Speed-torque characteristics as a function of rotor resistance of a wound-rotor induction motor. 26