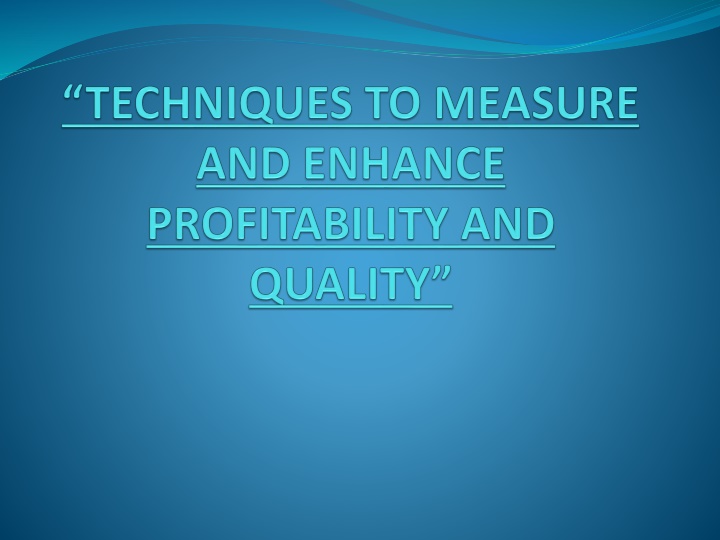
Techniques to Enhance Profitability in Business
Discover effective strategies to improve profitability in business by focusing on increasing sales, controlling and reducing costs, and exercising better control over capital employed. Explore techniques like standard costing and budgetary control to drive financial success.
Download Presentation

Please find below an Image/Link to download the presentation.
The content on the website is provided AS IS for your information and personal use only. It may not be sold, licensed, or shared on other websites without obtaining consent from the author. If you encounter any issues during the download, it is possible that the publisher has removed the file from their server.
You are allowed to download the files provided on this website for personal or commercial use, subject to the condition that they are used lawfully. All files are the property of their respective owners.
The content on the website is provided AS IS for your information and personal use only. It may not be sold, licensed, or shared on other websites without obtaining consent from the author.
E N D
Presentation Transcript
TECHNIQUES TO ENHANCE PROFITABILITY :- The profitability of products, service, processes or whole business depends upon three factors: Sales, Cost of sales and capital employed. There are three techniques to enhance the profitability : Increasing sales Controlling and reducing cost Exercising better control over capital employed
Increasing sales: Profitability depends on sales potential of a product or service. So profitability can be enhanced by increasing sales in the following alternatives:- The selling price of product or service can be increased when it will not affect the market. It is more beneficial for the companies under monopoly or who are following price leadership strategies of pricing as it is possible to increase the price withoutaffecting the market. The selling price can also be reduced when there is possibility of greatersales volumedue to lowerselling prices. New sales potentials through market research can be discovered. Before entering the market detailed analysis can be done through various techniques like targetcosting, activity based costing etc. As competition is increasing day by day, every businessman wants to prove his product superior than others. So design of products can also bechanged for increasing demand forthose products. i. ii. iii. iv.
Controlling and Reducing cost: Control is the process by which management ensures that the company is confirming to prescribe plans and policies in working towards theattainmentof corporategoals. Cost control is operated through setting standards of targets and comparing actual performance therewith, with a view to identify deviations from standards and taking corrective action in order to ensure that future performanceconforms to standards. Each aspect of the business is critically examined and reviewed with a view of improving efficiency and effectiveness and reducing the cost. In cost reduction, standards which are the basis of control are constantly challenged for improvement. Cost reduction may be achieved by various techniques like incentive scheme, work measurement techniques etc.
Exercising better control over Capital Employed: This may include: Better control over working capital e.g., reduced investment in stock according to business need, control over purchases etc. Better utilization of existing plant and machinery. Thus, a company may enhance its profitability by taking the above actions. But this is possible with the help of some techniques that a company have to adopt which are as follows: 1. 2. STANDARD COSTING : The technique of using standard costs for the purposes of cost control is known as standard costing. It is a system of cost accounting which is designed to find out how much should be the cost of a product under the existing conditions. The price for materials be lowest and wastes will be minimum possible. Wage rates will be low. The overhead expenses will also be minimum. The actual cost can be ascertained only when production is undertaken. The predetermined cost is then compared with the actual cost and a variance between the two enables the management to take necessary corrective measures. a.
b. BUDGETARY CONTROL : Budgetary control is the analysis of the plans which the organization has made, what was the result when those plans were implemented implementation of the budget, if any variation is seen in the actual result to the budget result then the reasons for the variations are found out and corrective measures are taken. On the basis of functional areas various types of budgets are prepared like sales budget, production budget, direct material budget, direct labour cost budget, overheads budgetetc. practically. After practical c. COST VOLUME PROFIT ANALYSIS : CVP analysis is a managerial accounting technique which deals with how operating profit is affected by changes in variable costs, fixed costs and selling price per unit. Managers use CVP analysis to identify the levels of operating activity needed to avoid losses, achieve targeted profits, plan future operationsand monitororganizational performance.
d. ACTIVITY BASED COSTING AND ACTIVITY BASED MANAGEMANT : ABC links expenses related to resources supplied to the company to the activities performed within the company. Expenses flow from resources to activities and then to products, services and customers. After ABC has provided accurate information about the true costs of those activities, ABM makes use of this information through value analysis and performance measures which support strategic and operational decision making. Where ABM is implemented it can provide the data needs toplan and direct improvementactivities and eliminatewaste. e. TARGET COSTING : Target costing involves setting a target cost by subtracting desired profit margin from the competitive market price. It is an allowable cost for the product or service, given a competitive price, so that thecompanycan earn thedesired profit margin.
f. KAIZEN COSTING : Kaizen costing is a cost reduction system that is applied during the manufacturing process of an existing product. Kaizen refers to continuous improvement through small betterment activities and in small incremental amounts. Under Kaizen costing, the cost reduction can be effected by improving inefficiencies from the production process. Kaizen aims to eliminate waste. Some of the cost reduction strategies employed involve producing cheaper re designs, eliminating wastesand reducing process costs. g. LIFE CYCLE COSTING : It is the process of economic analysis to assess the cost of a product over its life cycle. This analysis is to quantify the total cost of a product throughout its full life cycle, which includes R&D, construction, operation and maintenance and disposal. It is the concept used for making decisions between alternative options, optimizing design, scheduling maintenance.
h. VALUE CHAIN ANALYSIS : identifying which activities are best undertaken by a business and which are provided by others i.e., outsourced. It describes the activities that take place in a business and related them to an analysis of the competitivestrengthof the business. Value chain analysis is one way of i. BENCHMARKING : Benchmarking is a practice of identifying, understanding and adapting the successful business practices and processes used by other companies or even other departments to increase your own business success. The objective of benchmarking is to find examples of superior examples performances and to understand the processes driving that performance. Companies then improve their performance by tailoring and incorporating these best practices in theirown operations not by imitating but by innovating. j. JUST IN TIME SYSTEM : JIT is an inventory management strategy that is aimed at monitoring the inventory process in such a manner as to minimize the costs associated maintenance. Thus, the companies employ this technique to increase efficiency and decrease waste by receiving goods only as they are needed in the production process, thereby reducing inventorycosts. with inventory control and
QUALITY :- Quality is a perceptual, conditional and somewhat subjective attribute and may be understood differently by different people. Thus, simply put, quality item has the ability to perform satisfactorily in service and is suitable for its intended purpose. In manufacturing, quality is a measure of excellence or a state of being free from defects, deficiencies and significant variations. ISO 8402:1986 standard defines quality as the totality of features and characteristics of a product or service that bears its ability to satisfy stated or implied needs.
TECHNIQUES TO MEASURE QUALITY :- INSPECTION : Inspection is a critical path of measuring quality. The product can be evaluated to see if it conforms to predetermined criteria, perhaps by going over a checklist of required functions and physical attributes. TESTING : This usually includes stressing the mechanical properties of the product such as material strength, elasticity and impact resistance. Test for vibration and temperature might also be conducted. Which tests to use are determined by the product, its use and the time and financial constraintsof the business. PROCESS CONTROL AND OWNERSHIP : Everyone involved in the manufacturing of the product should be encouraged to take ownership of a part of the success. Given the responsibility, employees will take more pride I their work and strive to have a successful outcome of the job forwhich theyare responsible.
CONTROL CHARTS : Charts can be effective tool when it comes to evaluate the product s quality. univariate and multivariate depends characteristics that will be measuring. The univariate chart displays one characteristic and the multivariate chart is used when multiple characteristics need to beevaluated. The use of two types of charts- upon the number of METRICS: measurement program. They include definitions of quality terms, how your measurement process relates to customer specifications and the decision process to accept or reject items inspected. If your business customers have a specific need for speed in receipt of their orders, you will measure the things that will affect the speed of your delivery process. Quality metrics are the parameters of a quality
BENCH MARKING : It is a quality measuring tool that establishes a starting point for a quality issue against which future quality measures will be evaluated. It involves quality data on issues like the no. of customers a company serves, the no. of defect product items acompany receives back from customers. ERROR COUNTS : Error counts is a basic quality measuring tool , tallying the number of errors in the production process or service. It can be a place to start measuring quality or a motivating tool to raise awareness and generate ideas toreduceerrors.
TECHNIQUES TO ENHANCE QUALITY :- TQM(Total Quality Management): TQM describes as a continuous process of reducing error in manufacturing, supply chain management, improving the customer experience and ensuring the employees are up-to-speed with their training. It aims to hold all parties involved in the production process as accountable for the overall quality of the final product orservice. It involves : Executive management Top management should act as a driver for TQM and createan environmentthatensures its success. Training- Employees should receive regular training on the methods and concepts of quality Customer focus- improvements in quality should improve customer satisfaction Continuous improvement companies should continuously work to improve manufacturing and quality procedures. Employee involvement Employees should be encouraged to be pro- active in identifying and addressing quality related problems. 1. 2. 3. 4. 5.
Six sigma : Six sigma seeks to improve the quality of process outputs by identifying and defects/errors. A six sigma process is one in which 99.99966% of the products manufactured are statistically expected to be free of defects. Process sigma can be calculated using a six sigma calculator. The six sigma project an be accomplished through the use of two six sigma sub-methodologies: DMAIC and DMADV. The six sigma DMAIC(define, measure, analyse, improve, control) process is an improvement system for existing processes falling below specification and looking for incremental improvement. The six sigma DMADV(define, measure, analyse, design, verify) process is an improvement system used to develop new processes or products at six sigma quality levels. It can also be employed if a current process requires improvement. removing the causes of more than just incremental
BENCHMARKING : Companies may also use benchmarking to improve product quality. Engineers sometimes, purchase leading competitors products. They may then take them apart, study them and determine how the competitors products outlast in the industry. They then compare various elements of that product improvements can be made to product quality. to their own. Subsequently, BUSINESS PROCESS REENGINEERING : BPR involves the redesign of core business processes to achieve dramatic improvements in productivity, cycle times and quality. Companies reduce organizational layers and eliminate unproductive activities. KAIZEN (CONTINOUS IMPROVEMENT): It is the policy of constantly introducing small incremental changes in a business in order to improve quality. Some of the features are : 1. Improvements are based on many small changes rather than the big radical changes. 2. As ideas come from workers themselves, they are less likely to be differentand therefore easier to implement. 3. Small improvements are less likely to require major capital investment than major process changes. 4. All employees should continually be seeking ways to improve their own performance.