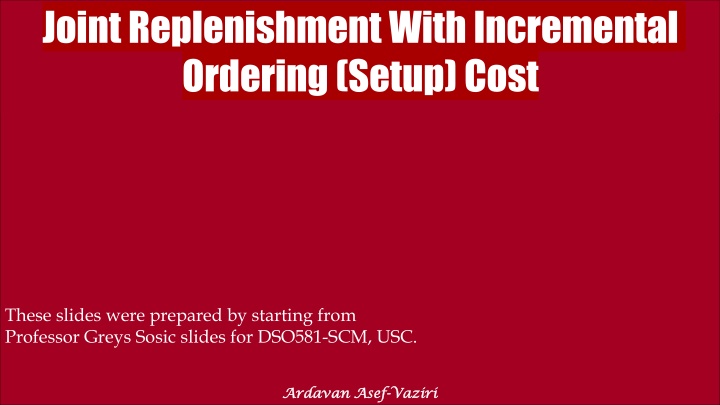
Optimizing Supply Chain Management Techniques
Explore the concepts of joint replenishment and incremental ordering in supply chain management, including cost calculations and comparison between individual and joint replenishment strategies. Learn how joint replenishment can reduce setup time and improve efficiency in ordering multiple products from suppliers.
Download Presentation

Please find below an Image/Link to download the presentation.
The content on the website is provided AS IS for your information and personal use only. It may not be sold, licensed, or shared on other websites without obtaining consent from the author. If you encounter any issues during the download, it is possible that the publisher has removed the file from their server.
You are allowed to download the files provided on this website for personal or commercial use, subject to the condition that they are used lawfully. All files are the property of their respective owners.
The content on the website is provided AS IS for your information and personal use only. It may not be sold, licensed, or shared on other websites without obtaining consent from the author.
E N D
Presentation Transcript
Joint Replenishment With Incremental Ordering (Setup) Cost These slides were prepared by starting from Professor Greys Sosic slides for DSO581-SCM, USC. Ardavan Asef Ardavan Asef- -Vaziri Vaziri
https://youtu.be/v_QD_R_Ravg Basic Models in Supply Chain Management 2
Joint Replenishment With Incremental Ordering (Setup) Cost A buyer may order multiple items from a supplier and follow joint replenishment. Suppose there are i=2 items with demand Di and holding cost Hi =hi Ci (i = 1,2). There is a joint order cost S, and an order cost Si for each item. Suppose that both items are ordered together every time and let Stotal = S + S1 + S2. A decrease in total inventory related cost through sharing of order costs! D1=1600/year, D2=900/year S = $4,000, S1 = S2 = $1,000 h = 0.2, C1 = C2 = $500 H1 = hC1 = 0.2(500) = $100, H2 = hC2 = 0.2(500) = $100. Basic Models in Supply Chain Management 3
Individual replenishment: Product 1 D1=1600/year, S+S1= 4000+1000= 5000, H1=100 EOQ1= SQRT[2D1(S+S1)/H1] = SQRT[2(1600)(5000)/100] =400 # of orders= D1/Q1 = 1600/400= 4 OC = (4000+1000)(1600/400) =20000 CC= 100(400/2) = 20000 TC = 40000 Cycle-Inventory = Q1/2= 400/2 = 200 Inventory Turns =1600/200 = 8 Flow time RT=I RT=Q/2 1600T=200 T=0.125 year Assuming 50 Weeks 50(0.125) = 6.25 weeks Assuming 360 days per year 360(0.125) = 45 days Basic Models in Supply Chain Management 4
Individual replenishment: Product 2 D2=900/year, S+S1= 4000+1000= 5000, H1=100 EOQ1= SQRT[2D1(S+S1)/H1] = SQRT[2(900)(5000)/100] =300 # of orders= D1/Q1 = 900/300= 3 OC = (4000+1000)(900/300) =15000 CC= 100(300/2) = 15000 TC = 30000 Cycle-Inventory = Q1/2= 300/2 = 150 Inventory Turns =900/150 = 6 Flow time RT=I RT=Q/2 900T=150 T=0.1667 year Assuming 50 Weeks 50(. 0.1667) = 8.33 weeks Assuming 360 days per year 360(0.1667) = 60 days TC(Individual) = TC1+TC2 = 40000+30000=70000 Basic Models in Supply Chain Management 5
Joint replenishment Can Reduce Setup Time Product Product-1 Product-2 Centralized EOQ = SQRT[2(2500)(4000+1000+1000)/100] = 547.723 # of orders= D/Q = 2500/547.723 = 4.564 OC = (4000+1000+1000)(2500/547.723) = 27386.1 CC= 100(547.723/2) = 27386.1 TC(Joint)/TC(Individual)= 54772.3/70000 = 78.24% Cycle-Inventory = 548/2 = 274 InvTrns =2500/274 = 9.129, Flow time: 2500T=274= 0.10954 year, or 5.47723 weeks or 39.436 days Each time we order 0.64(547.723) = 351 product 1, and 198 product 2 Demand 1600 900 2500 % 0.64 0.36 1.00 H H-Weighted 100 100 100 S 4000+1000 4000+1000 4000+2000 64 36 100 Basic Models in Supply Chain Management 6
Alternative Formula for the # of Joint Orders # of orders = SQRT[(D1H1+D2H2)/(2S_total)] = = [1600(100)+900(100)]/(2(6000))] = 4.56435 Ordering cost = 4.56435(6000)= 27386.1 Each time we order (1600+900)/4.56435 = 547.723 0.64(547.723) = 350.542 product 1 and 197.18 product 2 Carrying cost of Product 1 = 100(350.542/2) = 17527.1 Carrying cost of Product 2 = 100(197.18/2) = 9859.01 Total cos = 27386.1 + 17527.1 + 9859.01 =54722.2 Basic Models in Supply Chain Management 7
Practice Individual Replenishment A company purchases components from three suppliers: Components from supplier Alpha cost $90 and are used at the rate 600 units/year; components from supplier Beta cost $24 and are used at the rate 4,000 units/year; components from supplier Gamma cost $1,000 and are used at the rate 80 units/year. The trucking company is charging a fixed cost of $1,000/truck (for the purpose of this exercise assume that you do not need to worry about the truck capacity). Currently they purchase separate truckloads from each supplier. The annual holding cost is 25% of product cost, h=0.25. What is the corresponding minimal annual cost? What is the cycle inventory of each component? Product Cost/unit h (20%) H=hC S Units EOQ D/Q OC I_Cycle CC TC T (year) alpha beta gama Total_Decen 90 24 1000 0.25 0.25 0.25 22.5 6 250 1000 1000 1000 600 4000 80 231 1155 25 2.60 3.46 3.16 2598.08 3464.10 3162.28 115.47 577.35 12.65 705.47 2598.08 3464.10 3162.28 5196.15 6928.20 6324.56 18448.91 0.19 0.14 0.16 Basic Models in Supply Chain Management 8
Practice Joint Replenishment 2. Motor Company is considering aggregating orders from all three suppliers. In addition to $1,000 fixed truck cost for deliveries with one pick up the trucking company is charging $100 for each additional pickup. What is the corresponding minimal annual cost, and the cycle inventory of each component? Product Cost/unit h (20%) H=hC S Units EOQ D/Q OC I_Cycle CC TC T (year) alpha beta gama Total_Decen 90 24 1000 0.25 0.25 0.25 22.5 6 250 1000 1000 1000 600 4000 80 231 1155 25 2.60 3.46 3.16 2598.08 3464.10 3162.28 115.47 577.35 12.65 705.47 2598.08 3464.10 3162.28 5196.15 6928.20 6324.56 18448.91 0.19 0.14 0.16 Aggregate Cen/Decen 49.15 0.25 12.29 1200 4680 956 4.89 5873.67 478.07 67.77% 5873.67 11747.34 0.10 63.67% Basic Models in Supply Chain Management 9
Centralized vs Decentralized: 6-Product, Different h & C Product Cost/unit h (20%) H=hC S % Produced A B C D E F Aggregate 60 30 40 50 20 10 32 0.2 0.25 0.15 0.3 0.2 0.4 0.2425 12 7.5 6 15 4 4 7.175 1100 1100 1100 1100 1100 1100 1600 10 25 20 10 20 15 100 2,000,000 # of Orders I_Cycle 33.029 41.286 33.029 36.927 26.968 23.355 Product A B C D E F Total_Decent Total_Cent Cen/Decen Total_Cent Demand 200000 500000 400000 200000 400000 300000 EOQ 6055 12111 12111 5416 14832 12845 OC 36332 45415 36332 40620 29665 25690 214054 107145 CC 36332 45415 36332 40620 29665 25690 214054 107145 TC 72664 90830 72664 81240 59330 51381 428108 214290 50.06% 214290 Q_Cent 2987 7467 5973 2987 5973 4480 Qi/EOQ 0.49 0.62 0.49 0.55 0.40 0.35 3027.7 6055.3 6055.3 2708.0 7416.2 6422.6 31685.1 14933.1 47.13% 2,000,000 29866 66.97 29866 66.97 107145 107145 Basic Models in Supply Chain Management 10