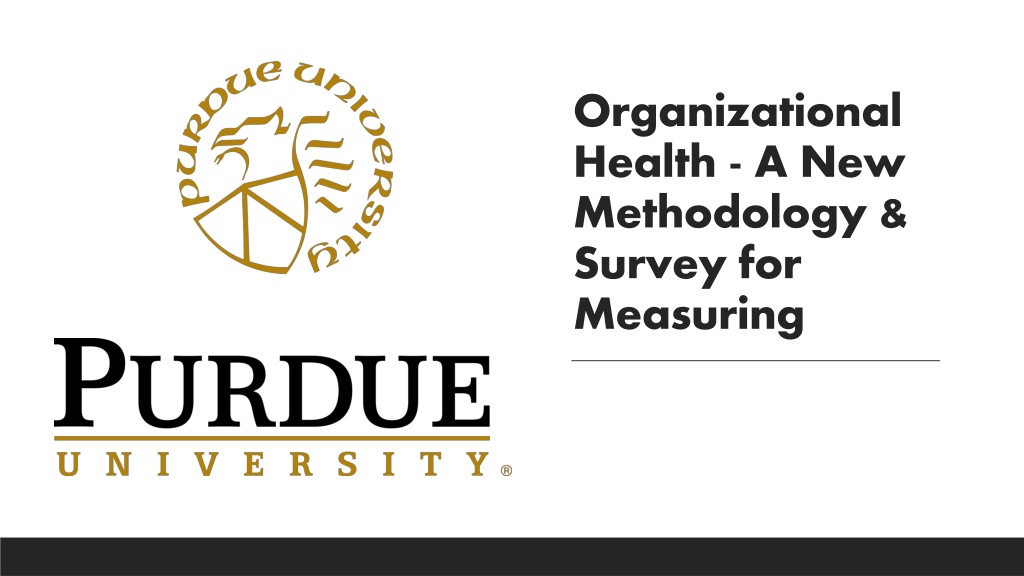
New Methodology for Measuring Organizational Health
Explore a new methodology and survey for measuring organizational health, developed through research partnerships and leveraging tools from industry experts. Learn about the key elements of organizational health, its importance, and how it differs from safety culture.
Download Presentation

Please find below an Image/Link to download the presentation.
The content on the website is provided AS IS for your information and personal use only. It may not be sold, licensed, or shared on other websites without obtaining consent from the author. Download presentation by click this link. If you encounter any issues during the download, it is possible that the publisher has removed the file from their server.
E N D
Presentation Transcript
Organizational Health - A New Methodology & Survey for Measuring
Organization Health Research Overview Undergraduate Researchers: Undergraduate Researchers: Elizabeth Rosene (2 semesters), Benjamin Hall (1 semester) Objective Statement Objective Statement: This study examines organizational health , what it consists of, how it is measured, and keys to improvement. Research Partners Research Partners: Professor Ray Mentzer, Marsh, American Chemistry Council (ACC) 2ndSemester undergraduate research project Draws upon work from McKinsey & Company BST CCPS
Safety Culture vs. Organizational Health Safety Culture Safety Culture Organizational Health Organizational Health Composed of organizational culture and Shared beliefs, practices, & attitudes toward safety Through design or default capability Organization s ability to align around a common vision, execute that vision, and renew itself through innovation Shaped by leadership with clear expectations Leaders & employees show caring for each other: stories, observations, and conversations Important to company s sustainability Capacity to learn and motivation to make continuous change Achieve & maintain high performance
Development of Research & Tools Void in area of organizational health (OH) No metric available for measuring current OH or providing guidance to improve High performance in OH difficult to achieve without commitment & resources Prior development of OH tools from McKinsey & Company McKinsey & Company: Definition of & Key Organizational Outcomes BST BST: Idea of Organization Culture and Organization Capability CCPS CCPS: Core Principles to Drive Performance Improvement
Development of Research & Tools OH metric fishbone model developed OH metric fishbone model developed Provides visual representation of key factors of OH Fishbone design allows for proper division of OH elements (aptitude & culture), and providing grouping of associated metric elements while also showcasing key factors OH metric support tables OH metric support tables Provides additional guidance to further analyze and improve upon OH Pulls tangible standards, programs, etc. to create an interactive and in- depth resource for one time or periodic company use
Process Safety, Occupational Health & Safety Elements Further Explained Process Safety Process Safety Occupational Health & Safety Occupational Health & Safety KPIs* Audit & Assurance Hazard Analysis Employee Health Promotion Emergency Response Job Safety Analysis Incident Investigation* Safety Management System* Management of Change
https://www.surveymonkey.com/r/VSRYTCY Organizational Health Fishbone Survey
Organizational Health Support Tables Metric to evaluate factors contributing to the six key fishbone elements of Organizational Health Include standards, methods, programs, information, etc. to improve upon or properly maintain any organizational health element Tables divided into Essentials or must haves (blue color) Excellence or must wins (amber color)
Table 1: Organizational Health Metric Support Table (Policies / Experience & Knowledge) Policies Score Experience & Knowledge Score Company Vision, Company Expectations, Industry Standards, Design & Operability, Utilization of Data Knowledge Management, Career Development, Competence 0-3 0-3 Learning Management System: Knowledge assessment, refresher training, etc. with clear documentation and assessment of effectiveness Compliance with applicable laws & regulations, licenses, permits, codes, etc. (Documented and accessible) Drawings, records, & documentation for design, operation, inspection & maintenance readily accessible Onboarding programs for new hires, including mentorship Ensure compliance and understanding of company expectations- safety management system in place with clear accountability Contractor Management Program in place: Ensure contractors are aware of hazards, risks, and mitigations at operating sites Essentials x 1 Assessment of operating conditions to confirm if within safe operating range through use of models, data analysis, etc. Make process safety performance and leadership significant considerations in career development Career development plan and ongoing screening for all employees enabling them to reach their potential with well thought out assignments Develop and provide training on internal standards to share engineering design and operating knowledge Operations safety audits addressing maintenance, inspections, operating procedures, recent incidents, etc. Personnel management of change criteria in place to ensure adherence to operating standards Utilize OSHA PSM standards to establish specific performance objectives, regardless as to whether required by regulations Periodic survey of existing safety culture/attitude "Storytelling" Safety Training Excellence x 1.5 Assess applicability of guidelines for process safety issued by the Center for Chemical Process Safety, et al Implement personal-leadership workshops to develop employees ability to improve continuously Promote external / 3rd party education & training to ensure competence with respect to company standards Encourage contractors to participate in development and implementation of safety systems Work with regulators to make standards effective and efficient Organizational Health Support Tables
Table 2: Organizational Health Metric Support Table (Process Safety / Operational Reliability) Process Safety Score Operational Reliability Score KPI's, Hazard Analysis, Emergency Response, Incident Investigation, Management of Change Operational Excellence, Mechanical Integrity, Preventative Maintenance, Security 0-3 0-3 Tier 1 & 2 Process safety metrics part of KPIs and stewarded by senior management Mechanical Integrity Program (testing, inspection, & maintenance) Alarm Management (prioritization of alarms, action plan for each alarm, etc.) Safety Critical equipment identified & included in PM with designated roles and responsibilities Process hazard analysis completed every 3-5 years and actions taken to complete recommendations PM Completed (% On Time) with goals and follow up, as appropriate Internal inspection and audits completed on process safety hazards Business continuity & crisis management plans, including periodic drills Essentials x 1 Active hazard recognition program Monitoring of physical & cyber security breaches Safe work permits properly completed (Lockout Tagout, Hot Work, etc.) Turnaround planning (scope, schedule, etc.) Safety Control System information collected & processed for improvement (nuisance alarms, facility downtime, etc.) Companywide Life Saving Rules developed and practiced Management of Change processes uniformly applied % Root Cause Analysis completed following incidents & shared internally Tier 3 & 4 Process safety metrics & appropriate leading indicators developed & implemented Safety culture initiative scores (Safety programs differ per company) Excellence x 1.5 Clarify understanding of acceptable/unacceptable risk tolerance GEMBA: Safety inspection walk & reporting Risk matrix applied with risk register to document significant risks Organizational Health Support Tables
Table 3: Organizational Health Metric Support Table (Engagement / Occupational Health & Safety) Engagement Score Occupational Health & Safety Score Internal and External Communication, Sense of Ownership, Visible and Felt Leadership Safety Management System, Job Safety Analysis, Employee Health Promotion, Audit & Assurance 0-3 0-3 Safety Management Systems core elements are in place with roles, responsibilities, authorities, & accountabilities known Process & personnel safety incidents communicated internally & externally Steward OSHA recordable injury illness rates with annual goals Training completed for all EHS roles Legislative monitoring for environmental and community affairs Managers & supervisors credibly demonstrate commitment to safety culture Emergency planning meetings with community and LEPC Ergonomics program in place policy, program scope, and KPIs Essentials x 1 Engagement/Participation with external Safety Organizations (OSHA, EPA, CCPS, etc...) PPE identified & available for appropriate situations Role of operations versus EHS staff on safety processes clearly identified Employee HR assistance available for health care and wellness related needs JSA (% utilized) with goals and follow up Fitness for duty (% Completed) Presence of community affairs for engagement with facility neighbors Sponsored health screenings and wellness promotions Excellence x 1.5 Sustainability Stewardship (Water utilization, renewable energy, recycling, etc.) Employee assistance programs offered gym discounts, activity promotions, etc. Proactive communication of upcoming process safety events with community (eg. Flaring with unit startup) Fatigue Management Program for shift / work scheduling EHS professional certifications earned (eg. CSP) Support work-life balance programs Organizational Health Support Tables
Company Involvement Three industry partners Three industry partners in 2021 semester Those in organization who might complete survey Process Safety Lead Safety Lead Operations Manager HR Manager Unit Superintendents Maintenance Manager Engineering Manager Role of Company in Purdue Research Review and comment on OH material Missing metrics of fishbone, support tables Suggest improvements on fishbone, support tables Comment on future application of OH metric tools
Conclusions & Recommendations OH Fishbone Metric and Metric Support Tables provide opportunity to increase performance & continuously improve each element of organizational health through tangible scoring metrics tangible scoring metrics If elements of fishbone and metric support tables are assessed, reviewed, enforced, and audited then a safer and healthier work environment can result Looking for Additional Industry Partners to Pilot Organization Health Metrics Contact Information Elizabeth Rosene: erosene@purdue.edu Professor Ray Mentzer: rmentzer@purdue.edu