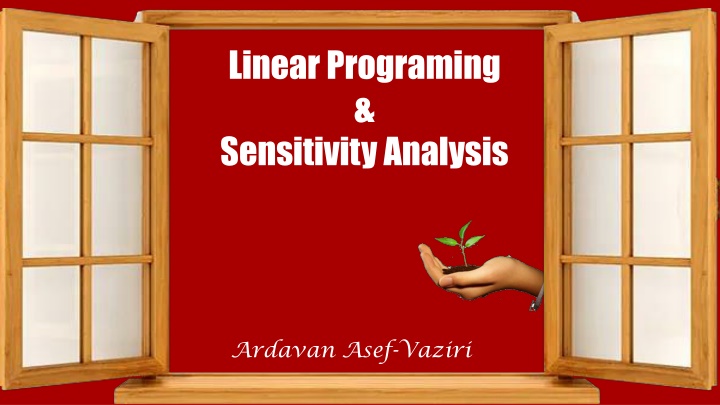
Linear Programing and Cost Analysis Practice
Explore a practice scenario involving linear programming and cost analysis for two products, P and Q. By following a 5-step process, assess production considerations, sales views, standard costing, and activity-based costing to determine the optimal product to produce based on varying cost allocation methods.
Download Presentation

Please find below an Image/Link to download the presentation.
The content on the website is provided AS IS for your information and personal use only. It may not be sold, licensed, or shared on other websites without obtaining consent from the author. If you encounter any issues during the download, it is possible that the publisher has removed the file from their server.
You are allowed to download the files provided on this website for personal or commercial use, subject to the condition that they are used lawfully. All files are the property of their respective owners.
The content on the website is provided AS IS for your information and personal use only. It may not be sold, licensed, or shared on other websites without obtaining consent from the author.
E N D
Presentation Transcript
Linear Programing & Sensitivity Analysis Ardavan Asef-Vaziri
Practice; Follow the 5 Steps Process Two products, P and Q. Weekly demand for P is 100 units & for Q is 50 units. Operating expenses /week: $2000 administrative costs for the manager working as OM/FIN/MKT manager. $4000 non- -administrative costs for the 4 operators working at the work- centers A, B, C, and D. Time available at each work center is 2,400 minutes per week. $90 / unit 100 units / week $100 / unit 50 units / week Q: P: Purchased Part $5 / unit D D 15 min. 5 min. C B C 10 min. 5 min. 15 min. A A B 15 min. 15 min. 10 min. RM1 $20 per unit RM2 $20 per unit RM3 $20 per unit Ardavan Asef-Vaziri 2
Cost World Views Sales View, Cost Accounting View Sales View: Suppose you are the sales manager and you will be paid a 10% commission on the sales Price. What product do you recommend to produce? P: Sales Price = $90 commission /unit = $9 Q: Sales Price = $100 commission /unit = $10 Q Cost Accounting View- Standard Costing. Overhead operating expense - is $6000 per week. Standard cost accounting attempts to absorb all the overhead costs of production into the product cost using a single cost driver. Usually the overheads are directly allocated among the various products in proportion to the cost driver of direct labor cost. The choice of the cost driver depends on the nature of the business. We assume operating expense is allocated in proportion to the potential market (50+100 =150). If we can satisfy all the demand, then overhead is $6000/150 = $40 per unit of product. If the total demand is not satisfied, overhead per unit of product is > $40. Ardavan Asef-Vaziri 3
Standard Costing, Activity Based Costing Cost World View Product Cost-Standard Costing Material Operating Expense Standard Costing Total Cost 85 80 Q Activity Based Costing (ABC). ABC is an alternative generally accepted accounting principle (GAAP). Instead of direct allocation the overhead costs to the products, overheads are allocated to activities, and then activity costs are allocated to the products. In the ABC of our example, administrative cost is allocated based on the time spent on each product. Our manager spends 80% of his time on P ($1600) and 20% on Q ($400). Perhaps because product P is a new product and needs more operations/marketing efforts. These costs are then allocated to the units of products based on the potential number of units produced. $1600/100 = $16 (P) and $400/50 = $8 (Q). P Q 5+20+20 = 45 20+20 = 40 40 40 Ardavan Asef-Vaziri 4
What Product to Produce? Cost World Solution. Non-administrative costs are allocated based on the potential number of units produced. Total Market P (100) and Q(50) $4000 /150 = 26.7 per unit. P Q Material 45 Operating Expense- Admin 16 8 Operating Expense- Non-Admin 26.7 ABC Total Cost 40 26.7 87.7 74.7Q Ardavan Asef-Vaziri 5
Finance View Finance View: Suppose the financial manager prefers the product with higher profit per unit. Lets look into the profit using different approaches Standard Costing P Sales Price $90 Total Costs $85 Gross Income $5 Q $100 $80 $20Q ABC Costing Sales Price Total costs Gross Income P $90 $87. 7 $74. 7 $2.3 Q $100 $25.3Q Marginal Contribution P: Profit Margin = $90 - 45 Profit Margin= $45 Q: Profit Margin = $100-40 Profit Margin= $60 Q Ardavan Asef-Vaziri 6
Facility Layout : Job Shop RM 2 Product P Q A 15 10 B 15 30 C 15 5 D 15 5 A C B D RM1 RM3 Profit Margin 45 60 Product P Product Q PP Ardavan Asef-Vaziri 7
Financial Throughput and Fixed Operating Costs Financial throughput is the rate at which the enterprise generates money. By selling one unit of product we generate P dollars, at the same time we incur V dollars pure variable cost. Pure variable cost is the cost directly related to the production of one additional unit - such as raw material. It does not include fixed costs such as salary, rent, and depreciation. Since we produce and sell Q units per unit of time. The financial throughput is defined as Q(P-V). Fixed Operating Expenses (F) include all costs not directly related to production of one additional unit. That includes costs such as human and capital resources. F = $6,000 per week P1= $90 and V1 = $45 per unit P2= $100 and V2= 40 per unit Incoming $ per unit of product is 90-45 = $45 for product P 100-50 = $60 for product Q. Ardavan Asef-Vaziri 8
Cost World Solution Production View Production View: Minutes of production or profit per minute of production time Q Q Product P Q A 15 10 B 15 30 C 15 5 D 15 5 Minutes Profit Margin Profit/Minute 60 45 0.75 50 60 1.2 For 50 units of Q, need 50 ( ) = min. on B, leaving min. on B, for product P. Each unit of P requires minutes on B. So, we can produce units of P. If we sell units of Q and units of P, we get 50( ) +60( ) = per week. After factoring in operating expense ($6,000), we 1500 30 900 15 900/15 = 60 $5700 $45 $60 LOSE $300! 50 60 Ardavan Asef-Vaziri 9
Cost World Three shortcomings in the cost world: Costs can be reduced at most by what they are. Downsizing is a threat to workforce. Thinks locally; an increase in the cost of an engine of $30 would have decreased the cost of the transmission by $80. The center producing the engine is reluctant to do so. Instead of strengthening the weakest link (improving Throughput in the throughput world), we focus on improving cost efficiency at the current level of performance- that is improving Operating Expenses in the cost world. Chain of 10 links, each with carrying capacity of 100 lbs. except for one with only 50 lbs. For cost reduction, we cut out portions of each strong link; make an efficient chain; every link is carrying exactlysame load of 50. The enterprise is now locked into the current performance level; it now has ten links, any one of which can break. In the future, if improved performance is desired, it will have to work all ten links in the chain If business picks up, it will be harder to recruit employees due to the fear of being fired in the next downsize. Ardavan Asef-Vaziri 10
The 5 Step TOC Focusing Process Step 1: Identify the System s Constraint(s) Step 2: Determine how to Exploit the System s Constraints Step 3: Subordinate Everything Else to that Decision Step 4:Elevate the System s Constraints Step 5: If a Constraint Was Broken in previous Steps, Go to Step 1 Performance of subsystems to be linked to the performance of the total system. The 5-Steps in a continuing Process. Ardavan Asef-Vaziri 11
2. Exploit the Constraint : LP Formulation Decision Variables P : Volume of Product P Q : Volume of Product Q Resource A 15P+ 10Q 2400 Product P Q Capacity A 15 10 B 15 30 C 15 5 D 15 5 Profit Margin Demand 100 50 45 60 2400 2400 2400 2400 Market for P P 100 Resource B 15P+ 30Q 2400 Market for Q Q 50 Resource C 15P+ 5Q 2400 Objective Function Maximize Z = 45P+60Q-6000 Resource D 15P+ 5Q 2400 Nonnegativity P 0, Q 0 Ardavan Asef-Vaziri 12
LP Formulation and Solution Product P Product Q Needed 15 15 15 15 1 Available <= 2400 <= 2400 <= 2400 <= 2400 <= 100 <= 50 Resource A Resource B Resource C Resource D Market P Market Q Contribution Margin Product Mix 10 30 5 5 0 0 0 0 0 0 -6000 1 45 60 Product P Product Q Needed 15 15 15 15 1 Available <= 2400 <= 2400 <= 2400 <= 2400 <= 100 <= 50 Resource A Resource B Resource C Resource D Market P Market Q Contribution Margin Product Mix 10 30 5 5 1800 2400 1650 1650 100 30 300 1 45 100 60 30 Ardavan Asef-Vaziri 13
A Practice on Sensitivity Analysis What is the value of the objective function? Z= 45(100) + 60(?)-6000! Adjustable Cells Final Value 100.00 Reduced Cost Objective Coefficient Allowable Allowable Increase 1E+30 30 Cell $B$10 Product P $C$10 Product Q Name Decrease 0.00 45 60 15 60 0 Constraints Final Value 1800.0 2400.0 1650.0 1650.0 100.0 30.0 Shadow Price Constraint Allowable Allowable R.H. Side Increase 2400 2400 2400 2400 100 50 Cell $D$3 Resource A Needed $D$4 Resource B Needed $D$5 Resource C Needed $D$6 Resource D Needed $D$7 Market P Needed $D$8 Market Q Needed Name Decrease 1E+30 600 1E+30 1E+30 600 900 750 750 40 20 2.0 Shadow prices? 15.0 60 1E+30 2400(Shadow Price A)+ 2400(Shadow Price C)+2400(Shadow Price C) + 2400(Shadow Price D)+100(Shadow Price P) + 50(Shadow Price Q). 2400(0)+ 2400(2)+2400(0) +2400(0)+100(15)+ 50(0). 4800+1500 = 6300 Is the objective function Z = 6300? 6300-6000 = 300 Ardavan Asef-Vaziri 14
A Practice on Sensitivity Analysis How many units of product Q? What is the value of the objective function? Z= 45(100) + 60(?)-6000 = 300. 4500+60X2-6000=300 60X2 = 1800 X2 = 30 Adjustable Cells Final Value 100.00 ????? Reduced Cost Objective Coefficient Allowable Allowable Increase 1E+30 30 Cell $B$10 Product P $C$10 Product Q Name Decrease 0.00 45 60 15 60 0 Constraints Final Value 1800.0 2400.0 1650.0 1650.0 100.0 30.0 Shadow Price Constraint Allowable Allowable R.H. Side Increase 2400 2400 2400 2400 100 50 Cell $D$3 Resource A Needed $D$4 Resource B Needed $D$5 Resource C Needed $D$6 Resource D Needed $D$7 Market P Needed $D$8 Market Q Needed Name Decrease 1E+30 600 1E+30 1E+30 600 900 750 750 40 20 2.0 15.0 60 1E+30 How much additional profit can we make if market for P increases from 110 to 111; by 1 unit. Ardavan Asef-Vaziri 15
3: Subordinate Everything Else to This Decision Keep Resource B running at all times. Resource B can first work on RM2 for products P and Q, during which Resource A would be processing RM3 to feed Resource B to process RM3 for Q. Do not allow starvation of B by purchased material RM2 or by output of Process A. Do not allow blockage of B by D. Minimize the number of switches (Setups) of Process B from RM2 to RM3-Through-A and vice versa. Minimize variability at Process B. Minimize variability at Process A and also in purchasing and arrival of RM2. Do not miss even a single order of Product P. Ardavan Asef-Vaziri 16
Step 4 : Elevate the Constraint(s) The bottleneck has now been exploited Besides Resource B, we have found a market bottleneck. Generate more demand for Product P Buy another Resource B The Marketing Director: A Great Market in Japan ! But the price discount, transportation cost, and other out of country costs adds up to 20% of the domestic sales price. Production costs remains as before. Ardavan Asef-Vaziri 17
Step 4 : Do We Try To Sell In Japan? Processing Times B 15 30 Product A P Q C 15 5 D 15 5 15 10 Product Costs and Profits Selling Price P (domestic) 90 Q (domestic) 100 P (Japan) 72 Q (Japan) 80 Product Manufg. Cost 45 40 45 40 Profit per unit 45 60 27 40 $/Constraint Minute 3 2 1.8 1.33 Ardavan Asef-Vaziri 18
Go To Japan? Product P Product Q Product P 15 10 15 30 15 5 15 5 1 1 45 60 100 30 Product Q Needed 10 30 5 5 Available <= 2400 <= 2400 <= 2400 <= 2400 <= 100 <= 50 Resource A Resource B Resource C Resource D Market P Market Q Contribution Margin 15 15 15 15 1800 2400 1650 1650 100 30 300 27 0 40 0 Ardavan Asef-Vaziri 19
Step 4 : Do We Try To Sell In Japan? We do not go to Japan. Is there something else we can do? Let s buy another machine! Which one? Cost of the machine = $100,000. Cost of operator: $400 per week. What is weekly operating expense now? 2 B $6,400 Ardavan Asef-Vaziri 20
Step 5: Where is the New Constraint? Resource Product P Product Q Product PJ Product QJ Needed Resource A 15 10 Resource B 15 30 Resource C 15 5 Resource D 15 5 Market P 1 Market Q 1 45 60 Available 2400 4800 2400 2400 100 50 15 15 15 15 10 30 5 5 0 0 0 0 0 0 <= <= <= <= <= <= 27 40 -6400 Resource Resource A Resource B Resource C Resource D Market P Market Q Product P Product Q Product PJ Product QJ Needed 15 10 15 15 30 15 15 5 15 15 5 15 1 1 45 60 27 80 50 0 Available 2400 4800 2400 2400 100 50 10 30 5 5 2400 4800 1800 1800 80 50 3000 <= <= <= <= <= <= 40 70 Ardavan Asef-Vaziri 21
Step 5: If a Constraint Was Broken in previous Steps, Go to Step 1 80P, 50Q,0PJ, 70QJ Total Profit = 3000 What is the payback period? 100000/3000 = 33.33 weeks What is the payback period? 100000/(3000-300) = 37.03 weeks The domestic P had the max profit per minute on B. Why we have not satisfied all the domestic demand. Ardavan Asef-Vaziri 22
Lessons Learned Link Performance of each subsystem (Marketing, Finance, Operations, etc) to the performance of the total system. Operating expenses human recourses are fixed costs. Do not treat them as variable costs. Do not assign their wage and salary to the units of products. Decision should promote a growth strategy. Throughput World: Profit Maximization. Limited only by our imaginations. Think globally not locally. There is one or at most few constraint(s) determines limiting a system to achieve its best. Just like the links of a chain, the processes within the enterprise work together to generate profit for the stakeholders. The chain is only as strong as its weakest link. Go and Exploit the Constraint Find the best way to use the constraint and elevate it. Ardavan Asef-Vaziri 23