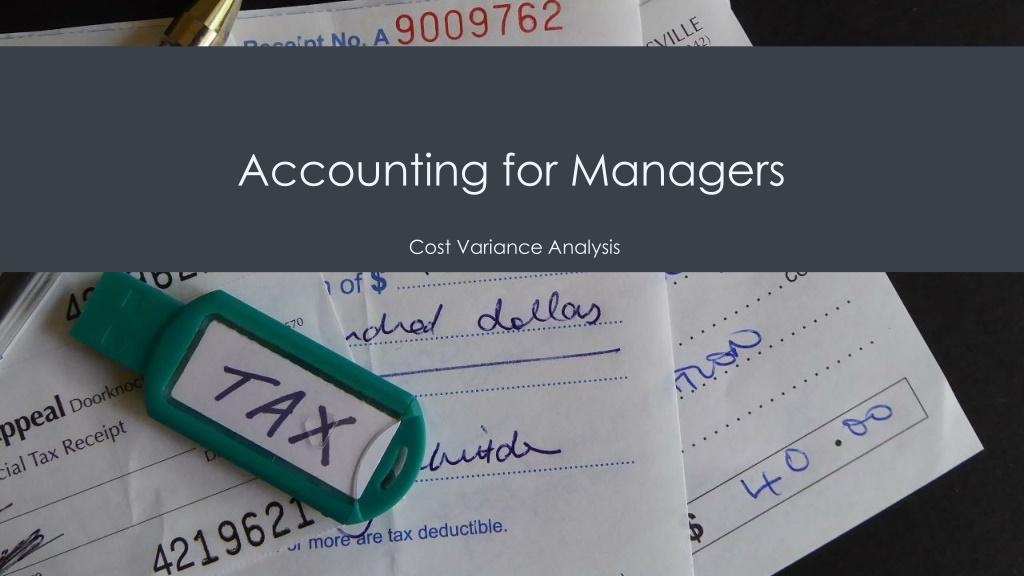
Cost Variance Analysis and Management Insights
"Explore cost variance analysis, favorable vs. unfavorable variances, significant variances, material cost variances, price variance, and quantity variance in accounting management. Learn how to identify, analyze, and address discrepancies in budgeting and expenses for better financial outcomes."
Download Presentation

Please find below an Image/Link to download the presentation.
The content on the website is provided AS IS for your information and personal use only. It may not be sold, licensed, or shared on other websites without obtaining consent from the author. If you encounter any issues during the download, it is possible that the publisher has removed the file from their server.
You are allowed to download the files provided on this website for personal or commercial use, subject to the condition that they are used lawfully. All files are the property of their respective owners.
The content on the website is provided AS IS for your information and personal use only. It may not be sold, licensed, or shared on other websites without obtaining consent from the author.
E N D
Presentation Transcript
Accounting for Managers Cost Variance Analysis
Steps of Cost Variance Analysis Steps of Cost Variance: Calculate the difference between what we spent and what we budgeted to spend Investigate why there is a difference Put the information together and talk to management Put together a plan to get cots more in line with the budget
Favorable vs Unfavorable Variances Favorable variances: generating more revenue than expected or incurring lest costs than expected Unfavorable variances: generating less revenue than expected or incurring more costs than expected
Significant Variance How can you know if a variance is significant? All variances need to be examined, no matter how small to ensure there was not a payroll error. If there was no payroll error, however, small variances are nothing to be concerned about. When looking at a comparison of variances over past years, take note of variances that are much larger than in other years. These variances DO need to be investigated.
Material Cost Variances Factors to consider: Quantity of material that goes into each unit Cost per unit of material
Price Variance What might cause a variance between the standard unit price and the actual price? Quality of product purchased Unavailability of a product Competition for materials What can you do to fix these problems in price variance?
Quantity Variance Material yield variance: when the amount purchased is different from the expected amount used Why might this happen? You buy more because the quality is low and there is waste or production scrap You buy less because the quality is high and there is less waste or production scrap You buy more because there are production issues You buy less because there are production issues
Reducing Material Variances How to get closer to budgeted material quantities: Quality comparison- if the quality of a new product is less than that of an old product a discount could perhaps be obtained Review procedures with staff- allows for greater efficiency Invest in new or better equipment Discuss your findings of the material variance so it doesn t happen again.
Reducing Labor Variances Tips for reducing labor variances: Proper training of staff Keeping the staff happy Ensure that equipment is maintained and properly functioning Ensure that raw materials are of good quality Consistently supervise Have accurate and attainable standards
Variable Manufacturing Overhead Variances
Variable Manufacturing Rate Variances A rate variance may occur if the cost of one of the components of this rate goes up. A difference in the efficiency rate occurs when it takes more hours than budgeted to manufacture the product A rate variance happens when there is a change in the components of the variable hourly rate.
Reducing Variable Manufacturing Overhead Minimizing variable manufacturing overhead: Obtain high quality supplies- can reduce the time needed to produce the product Have well trained employees- and continue the training process! Be a proactive manager
Quick Review Favorable vs. unfavorable variances Types of unfavorable variances: Material cost variances Price variances Quantity variances Labor rate variances Variable manufacturing rate variances How can you as a manager successfully deal with these types of variances?