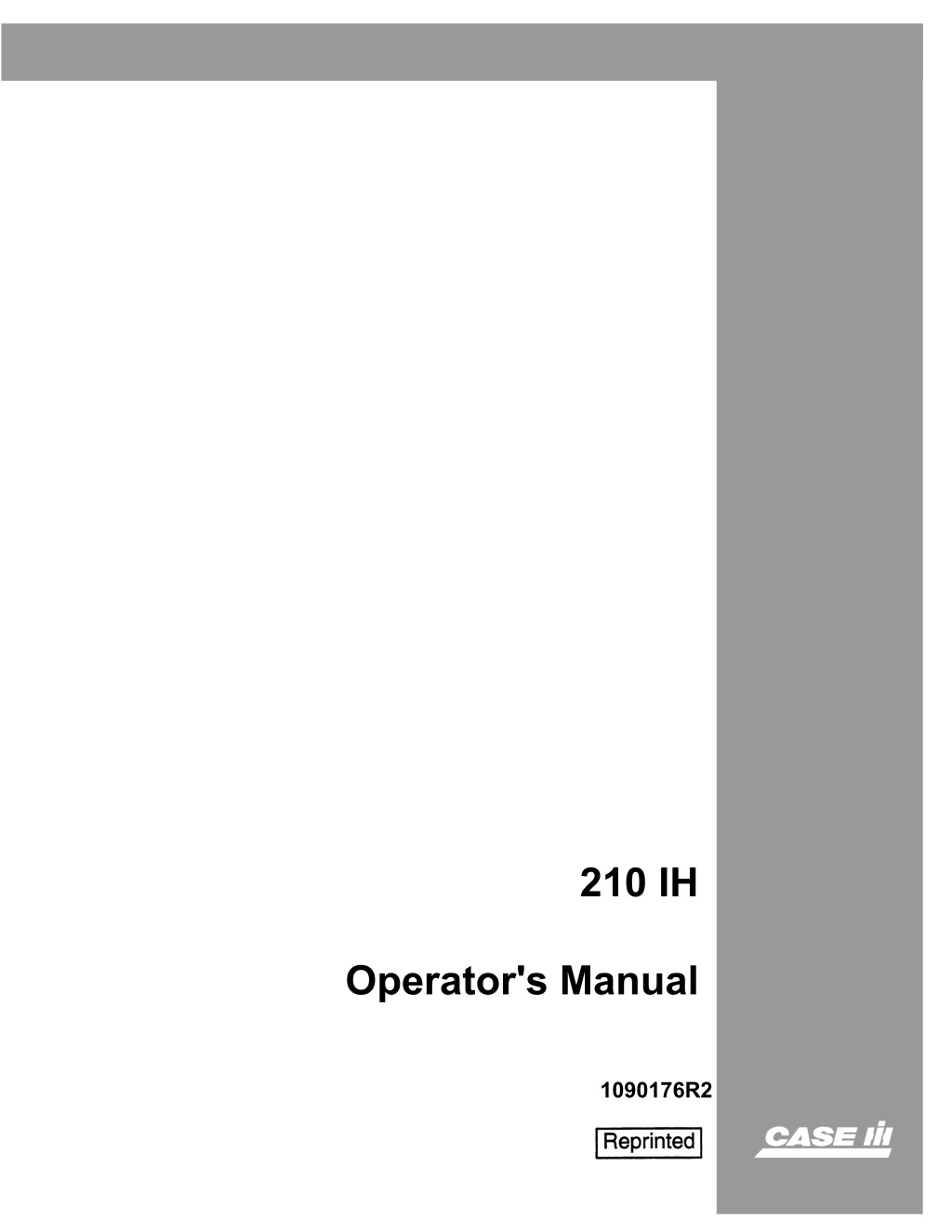
Case IH International 210IH Windrower Operator’s Manual Instant Download (Publication No.1090176R2)
Please open the website below to get the complete manualnn//
Download Presentation

Please find below an Image/Link to download the presentation.
The content on the website is provided AS IS for your information and personal use only. It may not be sold, licensed, or shared on other websites without obtaining consent from the author. Download presentation by click this link. If you encounter any issues during the download, it is possible that the publisher has removed the file from their server.
E N D
Presentation Transcript
210 IH Operator's Manual 1090176R2
it THIS SAFETY ALERT SYMBOL INDICATES IMPORTANT SAFETY MESSAGES IN THIS MANUAL. WHEN YOU SEE THIS SYMBOL, , CAREFULL Y READ THE MESSAGE THAT FOLLOWS AND BE ALERT TO THE POSSIBILITY OF PERSONAL INJURY OR DEA TH. M171B If Safety Decals on this machine use the words Danger, Warning or Caution, which are defined as follows: DANGER: Indicates an immediate hazardous situation which if not avoided, will result in death or serious injury. The color associated with Danger is RED. WARNING: Indicates an potentially hazardous situation which if not avoided, will result in serious injury. The color associated with Warning is ORANGE. CAUTION: Indicates an potentially hazardous situation which if not avoided, may result in minor or moderate injury. It may also be used to alert against unsafe practices. The color associated with Caution is YELLOW. If Safety Decals on this machine are ISO two panel Pictorial, decals are defined as follows: The first panel indicates the nature of the hazard. The second panel indicates the appropriate avoidance of the hazard. Background color is YELLOW. '" it WARNING IMPROPER OPERATION OF THIS MACHINE CAN CAUSE INJURY OR DEATH. BEFORE USING THIS MACHINE, MAKE CERTAIN THAT EVERY OPERATOR: Prohibition symbols such as \.Y X and 8 if used, are RED. Is instructed in safe and proper use of the machine. Reads and understands the Manual(s) pertaining to the machine. Reads and understands ALL Safety Decals on the machine. Clears the area of other persons. Learns and practices safe use of machine controls in a safe, clear area before operating this machine on a job site. It is your responsibility to observe pertinent laws and regulations and follow Case Corporation instructions on machine operation and maintenance. Bur 0-00000 2001 Case Corporation issued November, 1994 CASE and IH are registered trademarks of Case Corporation
https://www.ebooklibonline.com Hello dear friend! Thank you very much for reading. Enter the link into your browser. The full manual is available for immediate download. https://www.ebooklibonline.com
TO THE OWNER Your new International .Harvester Windrower is todays exacting operating requirements. The ease and comfort of op- eration, the ability to match ground requirement, and the effortless intended to lighten your work and shorten your hours on the to meet to engine power and work of the hydraulic are Your local. International Harvester [)ealer is interested in the receive frorn this Windrower. He has factory-trained service men in the latest method of servicing your \Vindrower and L Fl. service parts to a.sslire you of eration. Windrower op- To obtain top Windrower should be inspected depending on its use, periodically, or at least once a year by your International IIarvester Dealer. and assure economical operation, the Before you operate the Windrower, study this manual carefully . It has been prepared to help you operate and maintain your Windrower with utmost efficiency. New copies may be ordered from your dealer at a nominal price. Your dealer has original- equipment parts, which assure proper fit and good performance. When in need of parts, always specify the Windrower and engine serial numbers, including prefix and suffix letters. The Windrower serial number is stamped on a name plate attached to the right rear side of the chassis" A" frame.
INDEX DESCRIPTION P,'\GE lNTRODUCTION. . . . . ...... . 2 GET ACQUAINTED v\1TH THE CONTROLS BEFORE OPERATING . . 3,4 PREPARING YOUR MACHINE FOR WORK .. Apron Drive Belt . .. ... Apron Roller Drive Chain . .. Countershait Drive . . . . .. .. Hay Conditioner Drive Belt ..... Hay Conditioner Roll Drive Chain . Hydraulic Pump Drive .. . ... . . Platform Drive .. .. . Pneumatic Tire Pressure .. Rear Counterweights . . .. Reel Drive - Belt Type .. . . Reel Drive - Roller Chain .. Reel Jackshaft Drive Belt . Variable PropulSion Dri ve Variable Speed Drive .. .. 5-10 9 9 7 10 10 5 5 9 8 8 8 3 8 () OPERATION OF YOUR MACHINE . .. .. Cutting Range . . . . . . Dri ves Guards Attachment . . . .. Equalizing The Hydraulic Reel Lift . Hay Conditioner . ..... .. Roll Height .... .. . Roll Pressure .. .. Uppe r Roll Stop Bolts . .. Windrow Deflector .. ... Knife, Knife Drive and Knife Register .. Pick-Up Reel ... ... ...... .. Platform Apron Adjustment and Alignment . Platform Apron Speed . . Platform Float Adjustment . Platform Float Operation . Platform Gauge Wheels . . Reel Adjustment . . . . Reel Drive Shield Attachment . Reel Speed . ... ... .. .. Seat Adjustment .. . . ... Transporting . . . ... .. Windrow Deflector Rod Attachment . . 11- 19 11 13 14 16,17 17 16 17 17 12 15 13 13 11 11 18 14 18 14 11 H) 18 . CARE OF YOUR MACHINE ... .. .... Assembling The New Countershaft Drive Belt . Assembling The New Variator Drive Belts. Brake Adjustment ... . .. .... . Chains and Sprocket Alignment . . Final Drive Chains and Breathers . Finding Trouble ... .. .. .. . Hydraulic Fluid Strainer .. .. . Knife Removal and Repl.acement . Platform Control Valve . .. .. Preventive Maintenance ...... . Removing The Countershaft Drive Belt . Removing The Variator Drive Belts. Replacing The Platform Drive Belt . Self Aligning Sealed Bearings .. :)'teering and Clutch Linkage .... . Throttle Control Linkage . . . . . . . 20- 30 27 27 25 2:3 2D 20,21 29 30 25 22 27 26,.27 28 23 24,25 25 CARE OF YOUR MACHINE - LUBRICATION 30- 35 SPECIFfCA TrONS .. ... . .. . . ......
2 Years of research, design and development, precision manufacture and hundreds of inspections are your assurance that the 210Windrower will do good work for many seasons. It js up to you, how- ever, to protect your investment by maintaining this windrower's built- in performance. To do this, you must understand exactly how the 210 Windrower works, what can be done with it and how to operate it correctly. How to get the IT IS THEREFORE ESSENTIAL THAT YOU STUDY THE OPERATOR'S MANUAL C!.\REFUL- L Y. Merely a line or two on setting the machine for some rule obtain very crop will not as a results. Most difficulties responsible for aren't serious troubles. They can. be of quickly and easily if you know how to locate and remedy them. work care built into Keep this book handy for quick reference. It will save you time, trouble and money. For ad- ditional information or assistance, see your Inter- national Harvester dealer. your Illustrations are numbered to correspond with the number on which they are located. Therefore, reference is made to IIluzt. lOB, for example, you know that the illustration 10. The letter "B" in Illust. lOB it is the second illustration on that particular page. 210 Windrower Whenever the terms" right" and "left" are used, it must be understood to mean from a posi- tion behind and facing the \vindrower. You will find your new 210 Windrower win streamline your windrowing operation in a number of ways. Your new 210 Windrower has been checked carefully by your 1. H. dealer. He has the entire machine -- made sure that it working order and ready to service. There are, however, a few things which you must do hefore you put your new Windrower to work in the field. You need less help because of its efficient one-man operation. 1. over in good you dependable You s ave time because there is usually little need for slowing clown when the going gets tough. 2. The generous use of sealed-in bearings cuts down lubrication time to a minimum. 3. LUBRICA TE COMPLETELY More crop can be speedily windrowed in case of bad weather at harvest time. 4. You should lubricate the Windrower com- pletely. Use the handy lubrication guides on pages 31 through 35 as a check list. Be sure all lubri- cation fittings are free of paint and any other ob- structions which might keep lubricant from reach- ing the bearings. But don't over-lubricate. Ex- cess grease picks up dirt which may increase wear. The platform design provides the versatility necessary to meet a variety of crop conditions, such as the fonowing: 5. (a) Variable drive speeds for the reel and apron. (b) Belt type or roller chain reel drive. Don't try to lubricate the sealed bearings. These bearings are designed to work without lu- brication throughout their long life. (cl Pick- up reel for 10-1/ 2 ft. machine and bat-type reel for other sizes. (d) Special equipment for varied conditions, such as gauge wheels, windrow deflector rods, and drive shielding for tall or tangled crops. CAUTION: For greater stability when mov- ing the 210 Windrower without a platform, posi- tion the rear caster wheel in the center location.
3 GET ACQUAINTED WITH THE Cerrirols BEFORE OPERATING must. 3A HH5856 Hef. No, L 2. DESCRIPTION Variable control lever control 3. 4. 5. 6. control Brake Clutch Clutch Brake Platform control lever Throttle lever lock lock 7. 8. 9. 10. 11. 12. gauge Ammeter Oil pressure gauge Starter Button Ignition switch Flasher switch 13. 14. 15. 15. 17. 13. and switch Choke Illust. 3B HR5851- 5
4 GET ACQUAINTED WITH THE Controls BEFORE OPERATING STEERING CONTROL LEVERS PLATFORM HYDRAULIC CONTROL PEDAL The steering levers control the turning and the forward and reverse travel of the windrower. The is raised by down on pushing conditioner the bottom down on the the pedal and is lowered of the pedal. The ( ) ~ < , p r ' ' ' M with the platform. With the levers in the forward position, the machine will travel forward in a straight direction. To turn to the right, pull the right steering lever back until the desired turn is obtained. To increase the amount of turn, pull the lever to the rull rear position so the machine will turn on its own axis. The same procedure is used to make a left turn the left steering lever. REEL HYDRAULIC CONTROL PEDAL The reel is raised by pushing down on the bottom of the pedal and lowered by on the top of the podal. down AMMETER For reverse travel, pull back both levers simultan.eotlsly to the rearmost position. Turns in reverse travel are made by moving one lever to the central or forward position, in a manner similar to the forward travel. To stop backward move both levers to the full forward posi.- applying brakes. The ammeter indicates the rate of of the baUery. If it indicates a when the engine is above low idle, investigate cause bnmediately to avoid alternator danHige or battery dischaxge. ENGINE CONTROL PANEL For pos iti ve steering when hills, preload the moderate pressure on the check shut-off valve beneath the gas tank to all control levers, Pull the ignition the foot out, and the choke part way out. V ARIABLE SPEED CONTROL LF;V.ER Press the starter button and reloase as soon the engine starts. If the in a few "''''-'VHU,;'' wait excessive periods as failure of the motor. The variable the speed of t J H ~ rorward increases the speed, puning creases the speed. The rearmost lever drives the wlndrower at its control lever controls does not start try again. Avoid they may cause the lever hack de- of the As soon as the engine starts, adjust the choke to provide a speed and push the choke all the way in the THROTTLE LEVER warms. The throttle lever controls the speed of the engine from low to high idle. Always operate the engine at fun throttle when windrowing. the full CLUTCH PEDAL DO NOT OPERATE TIll:: "VITHOUT A I:ll\TTERY WINDROWEH when depressed, dis en- transmission. The clutch gages the drive of OPERATING SPEED BfLl\KE PEDAL Always operate the machine at fun throttle to maintain the correct speed of the driving mech- anism . At fun throttle, the 2450 RPM with no The brake pedal, when fully depressed stops the forward motion of the windrower. speed is approx- When descending hills, moderate ur",,,,,ure on the brake pedal loads the planetary provides positive steering. If field conditions require frequent move the variahle spee<icontrol leverrear- this reduces ground speed but does not affect the speed of platform drives. DO NOT USE THE THHOTTLE TO EASE THHOUGH ROUGH SPOTS as this adversely affects CLUTCH AND BRAKE PEDAL LOCKS down perform.ance. snd lift the in the locked-down position. until it secures the GOVERNOR PLATFOHM CONTROL LEVEH This lever controls the drive tothe platform, and also to the hay conditioner on machines so Platform and hay conditioner drives are ",engag"''' when the lever is rearward and engaged lever is for'ward. CAUTION: Do not attempt to reset the fin.'V", ,.",Or if correct engine speeds are not obtained; your International Harvester dealer m.ake any necessary adjustments.
5 PREPARING YOUR MACHINE FOR WORK GET ACQUAINTED WITH THE 881t and Chain Drive 11 shtener. But 1)0 Not Adjust With Engine Run,,;", The illustrations on pages 5 to 10 show the belt and chain drives on your machine. plain washer s on each side of the tightener or idler as required. Be sure that tighteners and idlers are in Hne with the drive and driven pulleys (or sprockets) on a particular drive. Faulty alignment results in excessive wear on both drive belt and pulleys (or drive chain and sprockets). Be especially careful when Lining up tighteners or idlers equipped with seaied bearings, as these do not float on the shaft and must be aligned by using Belts stretch as they are used, particularly during run-in. The tighteners are used to main- tain proper belt tension and compensate for the increase in belt length. Always loosen the tight- ener pulley before installing a new belt. Placing a new belt on a drive with the tightener pulley ad- justed tor old or lengthened belt imposes a severe strain on the new belt and pulley shafts IMPORTANT : lllust. 5A must. 5B HR5889 HP5839 HYDRAULIC PUMP DRIVE PLATFORM DRIVE The drive belt is properly ten- lower belt strand can be deflected force at a point as indicated at "Alt in Loosen the mounting bolts as shown to adjust the hydraulic pump sioned when 3/4" with a between the 5A. at IlD" in Illust. drive belt. Move the pump mounting bracket down- war d until the drive belt can be deflected 1/8" with a force of 2 pounds at a poi.nt midway between the pulleys. Tighten bolts at "D". 10 NOTE: The guide bolt support countershaft drive belt is also mounted on bolts at "D". After hydraulic punlp drive belt, it is necessary to the belt guide bolt clear- ance as descr ibed on page 7. for the Loosen the idler bolt at "B" to move the idler until the drive is properly tensioned. Addi- tional adjustment may be made by rnoving the for- ward idler to the upper at "c" .
6 PREPARING YOUR MACHINE FOR WORK VARIABLE SPEED DRIVE Hlust. 8A HR 5979 When properly adjusted, variator belt "E", shown in Illust. SA, can be deflected If 4" with a force of 20 Ibs. , and variator belt "F" shown in Illust. SA, to the transmission pulley can be deflected 1/2" with a force of 20 Ibs. Test the deflection of each belt at a point midway between the pulleys. Startthe engine andmove the variator lever tbrough its full range. The movement of one belt from high to low position between the variator pulley halves should be identical to the movement of the other belt. If belt travel is not equal, disconnect the clevis on the variator control rod shown at "J" in Illuet. Be; rotate the clevis until the belt travel is equalized, then secure it in place with the pin previously removed. To a d ~ u s t the belt tension, loosen bolts as shown at lie I in Illust. SA, on both sides of the variator. Turn variator adjustment bolts shown at "HII in Hlust. 6B equally. until the belts can be deflected as described above. Tightenbolts at "e". IHust. 6e Illust. 8B HR 5919 HR 5971
7 PREPARING YOUR MACHINE FOR WORK COUNTERSHAFT DRIVE - MACHINE LESS HAY CONDITIONER Check the countershaft drive belt tension with the platform lever in the engaged (forward) position. When properly tensioned the belt can be deflected 3/8" with a 5 pound force at a point mid- way between the pulleys as indicated at ilK" in Illust. SA. Adjust the tension with the lever dis- engaged, by loosening bolts at I'Ll' in Illust. to roiatethe idler pulley arm on the lever. The belt guard should clear the P. T. O. and countershaft puUeys by 1/16" with the drive en- gaged. To adjust the guard clearance loosen the stud at "Nil and the bolt at "pH in IUust. SA. SC The belt guide bolt at "R" in must. SA should provide a belt clearance of 1/16" with the drive e n g a ~ e d . The bolt head should clear the belt by 1/8' . The idler pulley guide at "Mil in lllust. SA should be rotated to the maximum forward position. COUNTERSHAFT DRIVE - MACHINE WITH HAY CONDITIONER I11ust. 7A HE 996 must. 7B HR 5902 When the platform control lever is moved forward to the It engaged" position, the lever presses on the spring tension rod on the rockshaft bar to pivot the idler pulley upward, engaging the counter- shaft drive belt and applying belt tension. DRIVE BELT GUIDES The idler pulley guide angle should be ad- justed to provide 1/8" clearance of the belt at the forward edge as shown at "0" in lliust. 7A, with the drive engaged. The countershaft drive belt is properly tensioned when the second hole in the tension r od is visi.ble above the tension spring stop bar on the control lever, as shown at "S1I in lllust. 7A, with the control lever in the engaged position. With the platform control lever engaged, adjust the rear guide bolt at "Wit in IUust. 7B in the slotted mounting to clear the belt by I llS" . The bolt head must extend 1/8" beyond the edge of the belt, To adjust belt tension, move the stud at "Tn (lever disengaged) in the slotted rockshaft bar. Make minor adjustments with the lever engaged by adjusting nuts on each side of stud "Ttl to extend or retract the spring tension rod until the dri.ve belt is properly tensioned. COUNTERSHAFT DRIVE BELT GUARD Check the belt guard clearance with the con- trollever engaged. Provide a clearance of 1/16" between the belt and the guard. Adjust the bolts in- dicated at "An in IUust. 7A to provide the proper clearance at the countershaft pulley and the bolt indicated by "B" in lllust. 7B t o provide the proper clearance at the P . T. O. pulley, IMPORT ANT: The spring tension rod should extend at a 900 angle to the control lever to avoid binding in the stop plate hole, and consequent loss of correct belt tension.
B PREPARING YOUR MACHINE FOR WORK must. 8B H 1715 different hole in the pulley support at '\T" . Secure the outer nut at n Gil and the bolt at II F" . REEL JACKSHAFT DRIVE BELT Loosen the bolt at "c" in Illust. SA. Move the idler pulley until the belt can be deflected 1{ 4" with a 5 pound force at a point midway be- tween the pulleys as indicated at "D". bolt "e". See also Illust. SB. ROLLER CHAIN RgEL DRIVE - Regula.r for IO- IfZ:F't Size, Attachmentior Other Sizes Tighten Set the lower idler sprocket at "K" in Illust. aH in the rear upper hole or one of the four lower holes in the tightener bracket, depending on the position of the reel on the arms. BELT TYPE REEL DRIVE - Regular for 13-1/2, 16-1/2 and 19-1/2 Ft. Sizes Loosen the upper idler sprocket bolt at "L" . Turn the inner nut on the adjusting bolt a.t "M" against the tightener bracket until there us approx- imately 2" of slack between the upper and lower positions of the chain at a point midway between the sprockets, as indicated at "N". Place the lower idler pulley "E" in Illust. SA in the rear upper hole or one of the four lower holes in the tightener bracket, depending on the position of the reel on the arms. Loosen the upper idler pulley bolt at "F". Turn the inner nut on the adjusting bolt at tlG" the ti er bracket until the belt can be 3/8' with a 5 pound force at a ~ o i n t mid- waybetween the pulleys, as indicated at 'H". For additional adjustment, move the upper pulley to a For additional adjustment, move the upper idler sprocket to a different hole in the sp,rocket support at" p!! . Secure the outer nut at 'Ail" and the bolt at ilL".
Suggest: If the above button click is invalid. Please download this document first, and then click the above link to download the complete manual. Thank you so much for reading
9 PREPARING YOUR MACHINE FOR WORK APRON ROLLER DRIVE CHAIN Loosen the bolts at f'W" in Illust. 9A and pull the apron dd ve pulley away from the roller sprocket until the lower strand of chain has approx- imately 3/8t1 of slack at point "A" between the upper and lower positions of the chain. Tighten bolts at "W". REAR COUNTERWEIGHTS rHust. lC HR 5980 All sizes require weight on the caster wheel beam for stability. The 10- 1/2 and IS- 112ft. machines require one bar, the 16-1/2 ft. machine requires three bars, and the 19-1/ 2 ft. machine five bars. If extra stability is needed, an addi- tional bar may be installed by ordering 592 194 R2. VARIABLE PROPULSION DRIVE Propulsion power is transmitted through the variator from the engine to the main clutches by means of heavy duty V-belts. Variation of the belt travel in the compensating variator pulleys determines the ground speed. As the variator is moved through its arc of travel, one belt puns deeper into the pulley, forcing the pulley center section over, which forces the other belt to move outward toward the pulley circumference. Refer to the ground speed chart below. H 4611 Ulust. 9A APRON DRIVE BELT To tension the apron drive belt, loosen either idler pulley bolt "R" or "S", as shov;'ll in must. lB. Move the idler until the belt can be deflected 3/8" with a 5 pound force at a point mid- way between the pulleys as indicated at "TIt in must. lA, and secure the bolt. Ground T ravel Speed Chart in M . P . H. PNEUI'vIATIC TIRE PRESSURE Tires are inflated above the recommended pressure for shipping purposes. Reduce the pres- sure in all tires before operating the machine . The following chart shows the recommended tire pressure. Tire Size I Pressure Left Front 7.60 x 15 (4 Ply Right Front 7. 60 x 15 (4 Ply Rear Caster 5. 90 x 15 (4 Ply) Wheel 30 1bs. 24 lbs. 241bs. " If the machine pulls to the left, decrease the right tire pressure. increase the right tire pressure. If it pulls to the right, :must. lB H 4601
https://www.ebooklibonline.com Hello dear friend! Thank you very much for reading. Enter the link into your browser. The full manual is available for immediate download. https://www.ebooklibonline.com